Tooling shops may need to ditch current CAD software
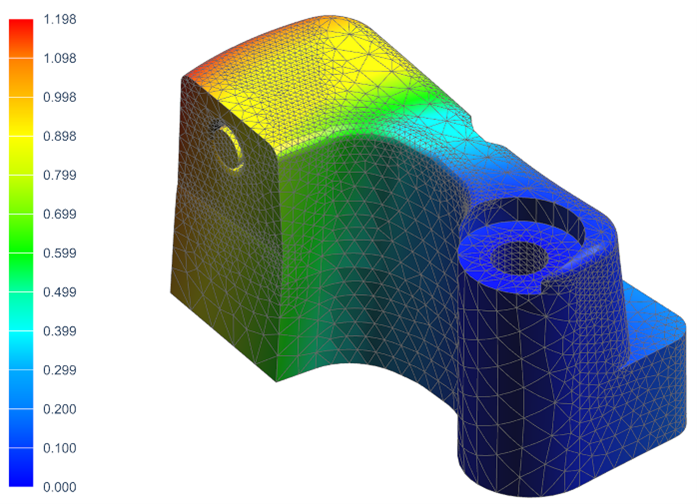
Many North American tooling shops are thriving, while others are going out of business or getting absorbed by larger companies. On the surface, this might look like the natural ebbs and flows of industry. But underneath it lies a series of strategic decisions that have separated the best from the rest. This growing separation exists at every level of a tool’s lifecycle, from quoting to delivery. This article focuses on how tool design and engineering workflows have created a growing gulf between industry leaders and laggards.
Cheap CAD won’t cut it for tooling shops
Today, tooling shops in North America have two basic choices when it comes to CAD solutions: premium software like Siemens NX for Mold Design or Die Design or special niche solutions directed toward SMBs. The latter solutions promise an experience close to premium for less money, and many Tier 2 and 3 suppliers have opted to go this route.
In the short term, it always makes sense to choose a less expensive CAD tool. This is doubly true if a shop’s design team is already familiar and comfortable with that solution. Investing in a more expensive option is a hard sell to both ownership and users, and few managers feel strongly enough about the difference to take that on. Yet the question lingers: why do premium CAD solutions continue to survive and thrive, not only among OEMs and Tier 1s but among Tier 2 and 3 suppliers? Are these other shops financially undisciplined? Don’t they know there are cheaper options out there?
Seeing clearly through the fog
The reason we ask these questions is because lost efficiency isn’t always easy to spot in a design and engineering workflow. Different CAD solutions offer different time-saving commands, hoping that users will miss the forest for the trees. But every lost efficiency is like incurring a debt—the pain might not be felt immediately, but sooner or later, the debt is paid in full… with interest.
For top tooling shops, convenient commands and feature-to-feature comparisons with other CAD tools are pointless. What truly matters is integrating their CAD solutions with their upstream and downstream processes, along with other major digital assets like BOM automation tools and standard parts libraries. Cavalier Tool & Manufacturing is an excellent example of one such company, which looked to Siemens NX for its mold design applications.
“With NX, we could literally generate a mold base in minutes—slides, lifters, hydraulic actions, ejectors pins, standard components, all of it,” Jim Korenev, Cavalier’s head of engineering and manufacturing processes, said. When asked if Cavalier might maintain its industry-leading innovation and time-to-market with a different CAD Solution, Korenev answered, “There’s no way.”
NX applications for tooling design are used by the top OEMs and Tier 1 suppliers for a reason: they bring maximum design efficiency and innovation. The same is true for the top tier 2 and 3 mold shops, but things can become a little murkier at these levels, especially when shops only produce simple tools.
Companies might think they can use cheaper design software because they’re receiving a neutral CAD format from their customers. Or they might think they already have a decent CAD/CAM workflow that’s stitched together with in-house custom connections. The problem lies in thinking that this is a cutting-edge strategy. They don’t realize that they’re losing time and money compared to their competitors because the market hasn’t punished them—yet.
Better collaboration with international teams
While reshoring is a very real trend in North American manufacturing, design and engineering work is moving toward greater international collaboration. Follow-the-sun approaches have companies running design teams through the day in North America and through the night in other parts of the world, more than doubling the speed of their design workflows. With this trend, companies are realizing that their inexpensive CAD solutions don’t have strong user bases in international markets, making efficient collaboration next to impossible. This trend is currently driving down the use of niche CAD solutions that target North American tooling shops, and even Tier 2 and 3 suppliers will eventually need to move to solutions like NX that are more widely used on a global scale.
Customers need more evidence for tool performance
Traditionally, tooling shops have left extra material in their tools to safeguard against structural failure. Customers have accepted this approach because tool failures can be extremely uncommon among their suppliers. However, this trend is quickly changing as a younger generation of managers and buyers demand more scientific evidence for tool performance from their suppliers. They’re not willing to take the design team’s word for it. They want to see FEA simulations of tools to ensure they’ll perform properly under different conditions. On the flip side, they’ll no longer accept the idea that extra material is intentionally being left in tools to buffer away the possibility of failure.
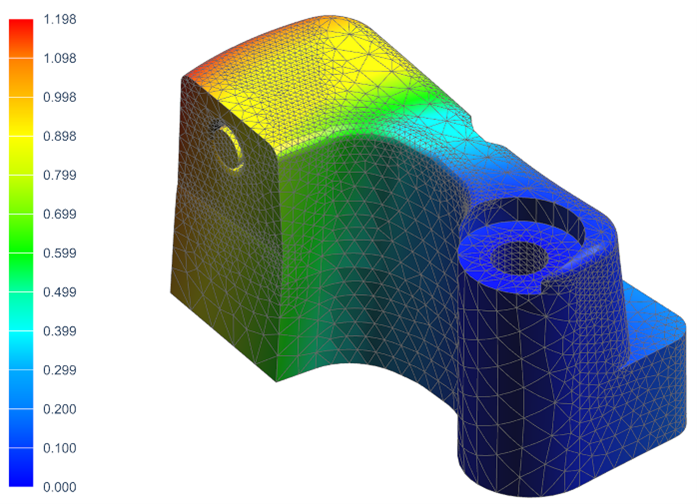
Weight restrictions on tools are becoming a higher priority, and with greater emphasis on lightweighting comes a greater emphasis on simulation to ensure the optimal recipe of design, weight, and strength. Simply put, companies will no longer accept “We’ve been doing this for 40 years” as an explanation for a tool’s weight or strength. They’ll want simulation using best-in-class tools like Simcenter 3D, which is built directly on top of the NX modeling environment for maximum workflow efficiency. There’s no importing or exporting of models for FEA—everything is done in one environment.
Experienced support is a must-have
Once a company makes the decision to invest in NX Tooling applications, there remains one more important consideration: who will they work with to buy and implement the software? Without proper support, companies might experience frustration with these solutions and feel they’re not getting adequate ROI from their investment. Yet this need not be the case.
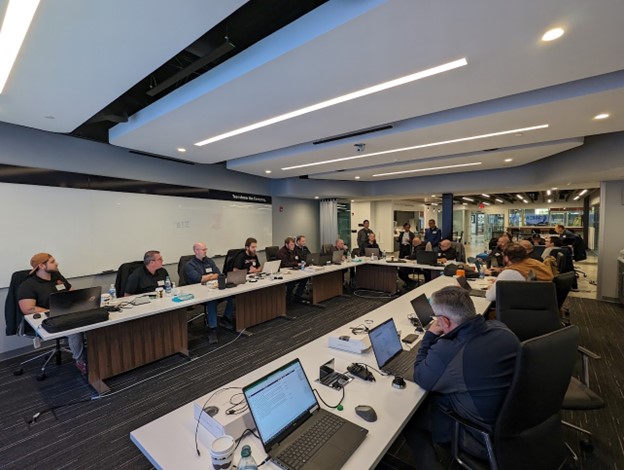
Longterm Tech has been working with top shops in the injection mold, die casting, and stamping die industries for over 20 years. Our engineers have direct industry experience with these tools, from day-to-day CAD work to the long-term development of standard parts libraries and design workflow automation. Our annual NX Tooling Workshop brings together the strongest tooling design and engineering teams in North America to share best practices, learn about new software releases, and provide feedback directly to the NX development team to shape the product’s future direction. There’s no other provider of NX Tooling applications in North America that comes close to Longterm Tech on these solutions, and a quick call with our support team will confirm as much for any interested company.
Reach out today for a free consultation. We’ll be happy to help you create a roadmap for how NX Tooling applications will transform your company.
About the author
Phil Glennie, Ph.D. is the Director of Marketing and Sales at Longterm Technology Services. Over his career, he has worked extensively in the world of enterprise software, including ERP, APS, and PLM solutions. He is dedicated to helping companies of all sizes take their next step forward in Industry 4.0.
About LTS
Longterm Technology Services based in London, Ontario, Canada, and Troy, Michigan, USA, is a recognized Siemens Expert Partner with over twenty years of deep experience helping companies supercharge their products and processes with Siemens Digital Industries Software.