Decrease costly vehicle in-service failures using numerical simulation
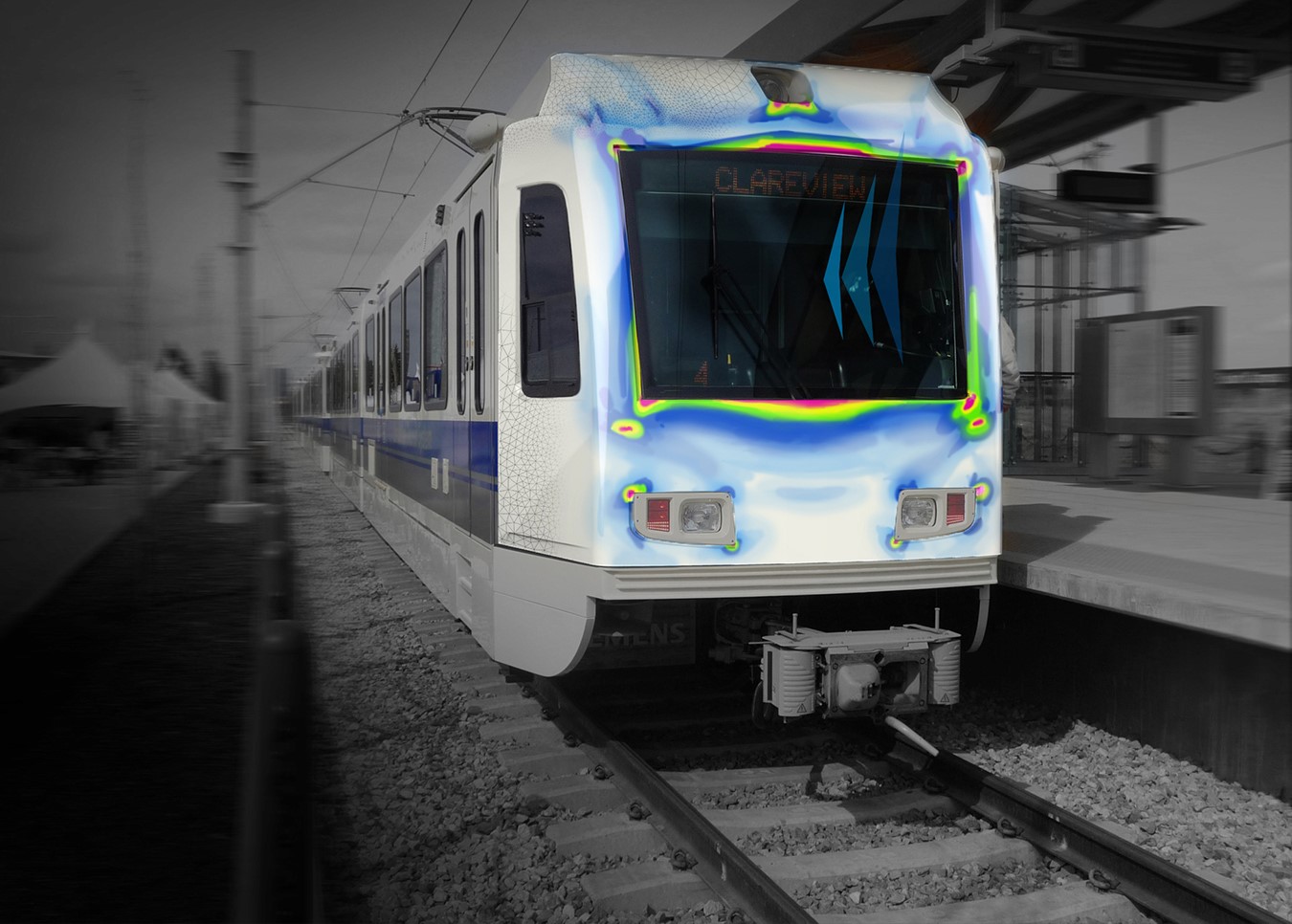
Vehicle fleet operators and manufacturers, such as those in the public transit, heavy machinery, transporter, and commercial delivery sectors are faced with increasing pressure to improve fleet uptime and availability—all while keeping expenditures in check.
Recurring fleet in-service failures and reliability issues significantly affect a carrier’s long-term profitability. Poor-performing vehicles can cause warranty costs at the OEM level and maintenance costs to skyrocket and drastically increase the total cost of ownership (TCO). What’s more, noise, vibration, and harshness (NVH) problems can generate high levels of customer dissatisfaction as well as driver workplace health and safety (WHS) concerns.
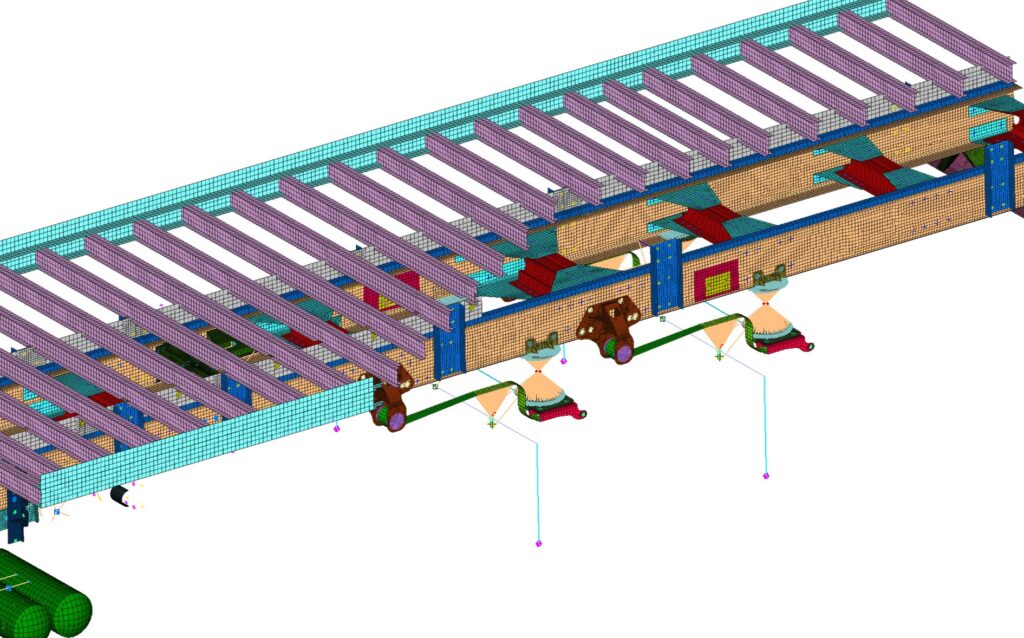
Numerical simulation helps overcome fleet issues and mitigate risk
While in-service fleets are designed to be robust and offer extended service life, they are not immune to defects or significant failures. Apart from improper design, vehicles can be subject to improper use, repeatedly traveling of the same routes, and severe loading environments that can all be culprits to in-service damage or failure.
Fleet owners, operators, and manufacturers need to find the best compromise for low failure rates, safety, performance, and product differentiation. This is where numerical simulations come in.
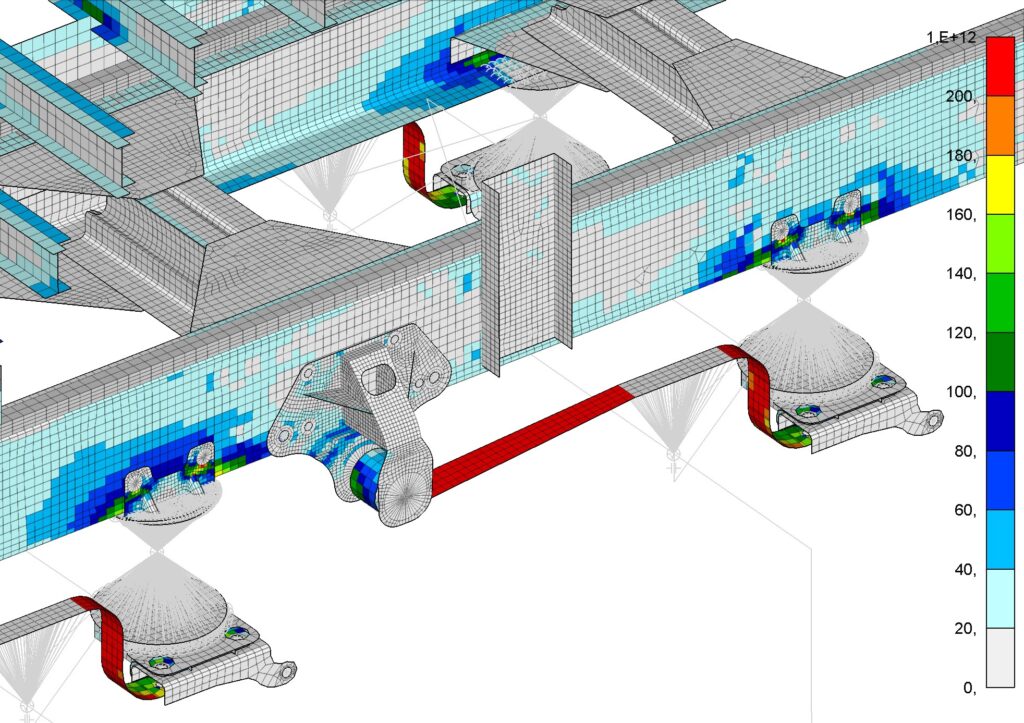
How can numerical simulation help
Numerical simulations can help fleet owners, operators and manufacturers understand, diagnose, and correct recurring problems definitively. When combined with data acquisition (strain, acceleration, temperature, noise, etc.), numerical simulation becomes a powerful solution to leverage experience, understand product loading and operating environment and find a viable solution to in-service issues.
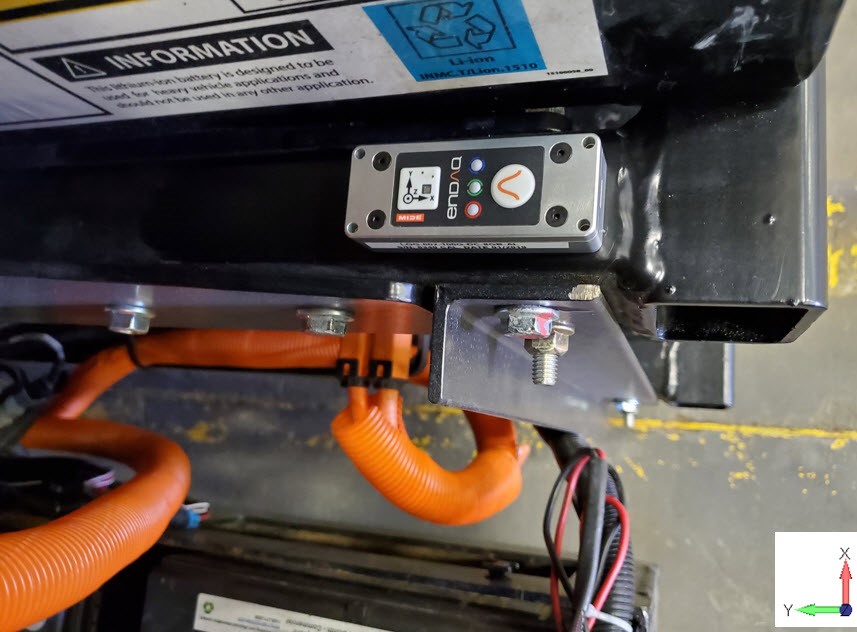
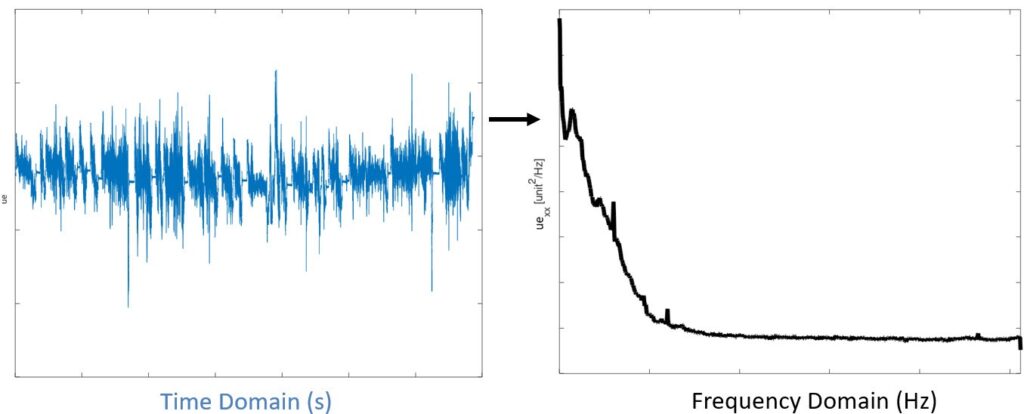
Understanding how vibrations and dynamic loading impact a vehicle
For example, public transit buses can acquire route severity using accelerometers and strain gauges. The loading environment can be applied directly to the finite element model (FEM) to assess durability. Data processing of the acquired routes enables engineers to identify the loading spectrum impacting the vehicle. Typically, maximum and fatigue inertial loadings, vibration, and shock loads are diagnosed. By understanding the damage caused by a specific route or how vibrations and dynamic loading are impacting a vehicle, operators can optimize the durability life of the main structure. Furthermore, premature failure can often be explained by dynamic amplification and dynamic coupling between main mechanical components and substructures. Creaform Engineering leverages the enormous capacity of Siemens Simcenter Nastran to solve complex dynamic problems affecting vehicles and machinery.

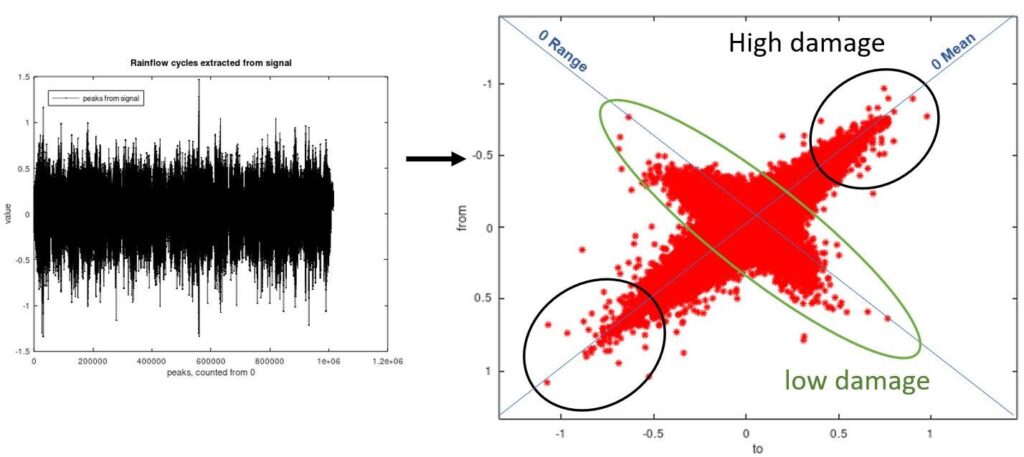
The root cause analyses of in-service failures are essential for the transportation industry. Numerical simulation offers a sophisticated tool for analyzing, correcting, and preventing a myriad of problems that can affect a company’s CAPEX and OPEX. Creaform Engineering is proud to be able to count on Siemens as a valued technology partner.
About Creaform Engineering and the Author
Creaform Engineering is a Siemens Digital Industries Software Technology Partner that offers engineering services to help companies develop products—particularly in the transportation industry. The Creaform team uses a wide range of Siemens products, including Simcenter NX, STAR-CCM+, Femap, and Simcenter Nastran to carry out extensive numerical simulations for fleet operators and manufacturers who are looking to mitigate the costs and customer satisfaction issues associated with in-service failures. For nearly 20 years, Creaform Engineering has been a one-stop-shop for manufacturers’ product development needs.
Pier-Olivier Duval has over 14 years of experience as an FEA expert and team leader at Creaform Engineering, one of the largest numerical simulation consultant teams in Canada. He specializes in numerical simulation with extensive expertise in nonlinear, dynamic, and vibration analysis, modeling of composite materials, and polymers. Pier-Olivier has contributed to significant projects in public transportation, aerospace, and heavy machinery industries.
Comments