SimOfis helps engine valve manufacturer optimize material and costs
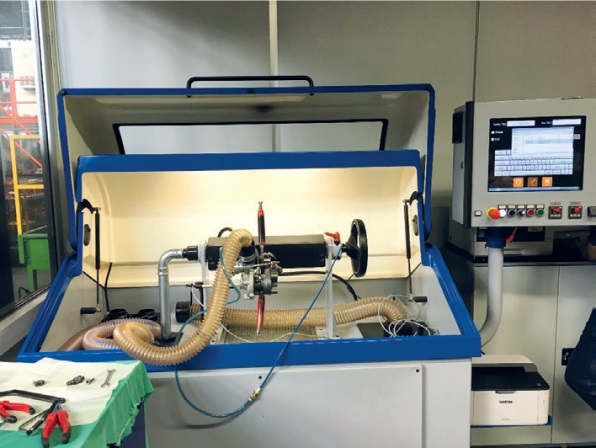
A turbocharger is an important part of a vehicle that determines engine performance. The design process for developing a turbocharger must analyze the flow conditions and heat distribution as well as bearing design and lubrication. Using Simcenter™ FLOEFD™ software, designers can simulate exactly how exhaust gas and air will react within the turbocharger, thus leading to engine efficiency.
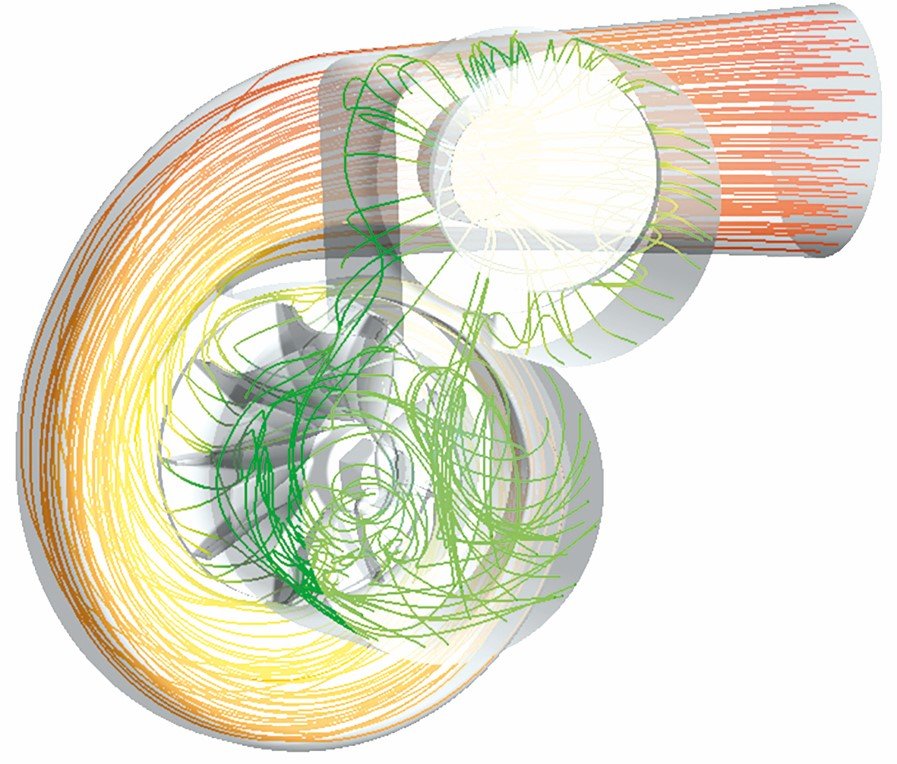
SimOfis is a Siemens Smart Expert partner in Turkey that specializes in Simcenter FLOEFD. It possesses extensive experience in computational fluid dynamics (CFD) for customers in the aerospace and defense, automotive and electronics industries, among others. SimOfis helps customers become familiar with how to use advanced simulation capabilities and rapidly integrate them into their design process.
Supsan, the automotive division of Borusan Group, is the largest manufacturer of engine valves in Turkey and distributes turbochargers, among other products. The company’s goal was to develop and manufacture new and innovative turbochargers to enhance the fluid dynamics. SimOfis worked with researchers and engineers at Supsan using a test rig to measure the flow rate and pressure. With the help of Simcenter FLOEFD, which is a part of Xcelerator™ portfolio, the comprehensive and integrated portfolio of software and services from Siemens Digital Industries Software, they were able to simulate the fluid dynamics virtually and the results of the physical test were compared to the simulation.
Using Simcenter FLOEFD for turbocharger testing
Twelve loading conditions ran in total using the rig: six each for the compressor side and the turbine side. For the turbine side, the wastegate was kept open for three cases and closed for the remaining three. Researchers measured rotational speed, inlet mass flow rate and outlet pressure. Then the open and closed wastegate test results were compared to the Simcenter FLOEFD results, with the maximum deviation of 9.4 percent.
Next, further simulations in Simcenter FLOEFD were performed on hot turbine gases and oil flow. Temperature distribution as well as different impeller materials with their effects on the shaft temperature distribution were analyzed and investigated. After that, the thermal expansion and the clearance for the operating conditions were calculated.
Based on the results of multiple tests, the appropriate material was selected. Not only was the material optimal for the design and function, but it also optimized costs.
“We started our new designs and performed all the turbocharger simulations, obtained the thermal distributions and found material substitution opportunities,” says Mert Alpaya, Technology and Strategy Development Unit Manager at Supsan Automotive Components. ‘’We achieved this with Simcenter FLOEFD.”
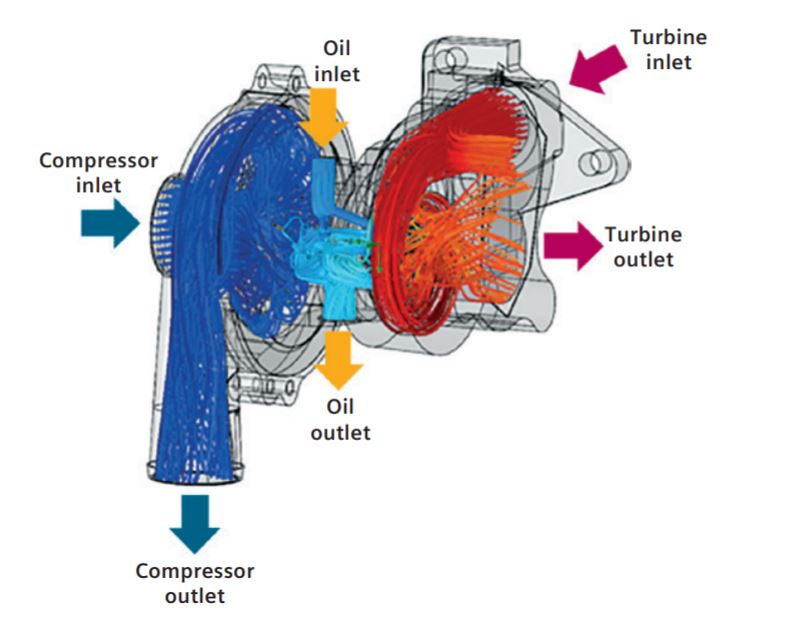
Applying front-loading CFD to the design process
The technique of incorporating CFD simulation early in the design process is called front-loading CFD and helps design engineers examine trends and dismiss less desirable design options. With Simcenter FLOEFD, SimOfis developed a comprehensive digital twin to help customers optimize product designs, this methodology can be integrated into computer-aided design (CAD) tools and reduce overall simulation time by as much as 75 percent and enhance productivity by up to 40x. As a result, users can optimize product performance and reliability and reduce, and sometimes even eliminate, the cost and time associated with building physical prototypes and testing.
SimOfis has considerable experience producing models and simulations, which is proven by its simulation results that closely match those produced by the more expensive and iterative design, prototype and test cycle. The simulation results enable the customer to more quickly and thoroughly investigate multiple tests and designs to optimize the product design and cost.
Leveraging SimOfis’ CFD expertise
A typical SimOfis engagement starts with assessing the customer’s design process, spending a day with its engineering team and teaching the customer how to apply Simcenter FLOEFD to easily incorporate CFD simulation into a CAD design. SimOfis’ mission is to educate customers and provide them with services so they can apply the technology to their design challenges. To facilitate early success, SimOfis has found it is essential to establish a customer’s confidence in using simulation and provide expert support when it’s needed. Ultimately, SimOfis helps customers use Simcenter FLOEFD to realize the business benefits of front-loading CFD.
To learn more about Simcenter FLOEFD and the value of front-loading CFD, take a look at one of Simofis’ on-demand webinars: Frontloading Electronics Cooling Simulation with CAD-Embedded CFD
SimOfis is a Siemens Smart Expert partner in Turkey with a specialization in Simcenter FLOEFD with vast expertise in computational fluid dynamics. Salih Bilgiç is a CFD Application Engineer and Çağrı Bostancı is a Sales Manager at SimOfis.
Siemens Digital Industries Software Contributors: James Gregory, Director, Global Channels Business Development responsible for global partner coverage and capacity, and Mollie Gladden and Maggie Korte, market research Co-Ops studying Marketing at the University of Cincinnati.