Thermal analysis: a crucial part of any PCB design flow
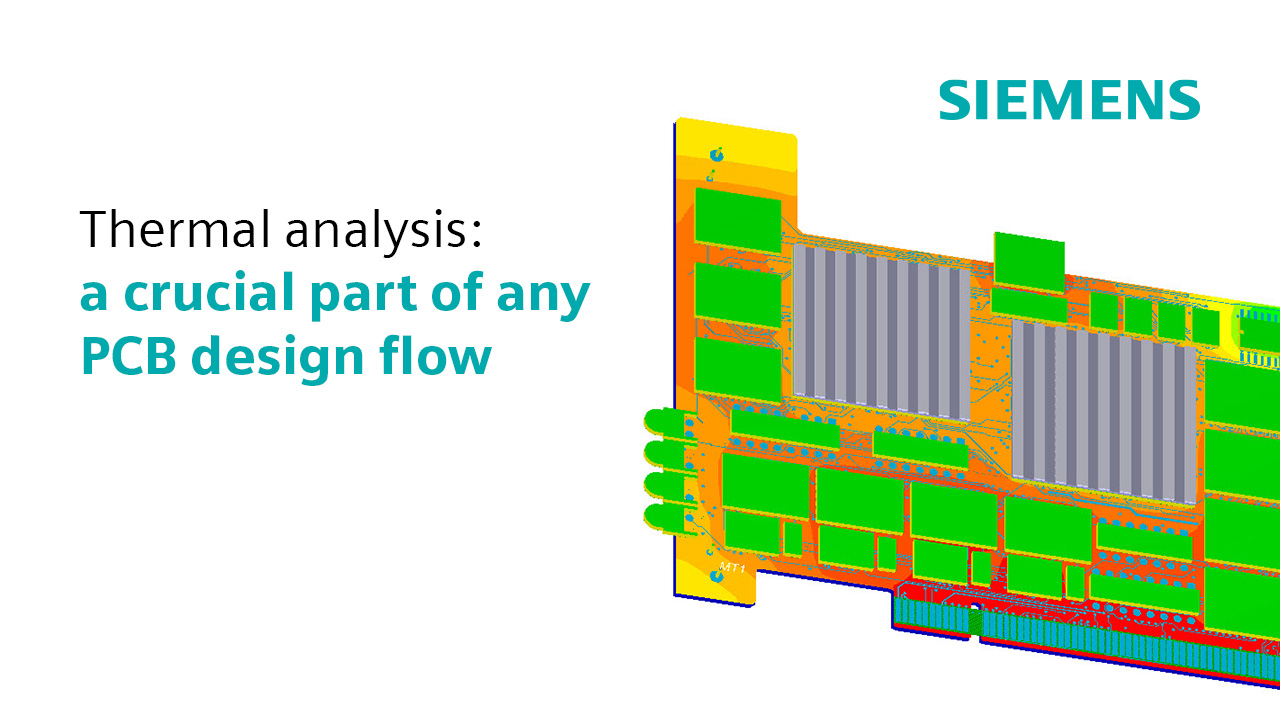
Thermal analysis stands out as a pivotal tool for ensuring the reliability, performance, and longevity of electronic systems. Often overshadowed by other analyses or relegated to conservative approximations, thermal analysis is experiencing a renaissance, compelled by the evolving technological demands of today’s products.
Traditional approaches to thermal analysis
Engineers often rely on manual strategies to address thermal concerns, employing rules of thumb or excessive cooling measures just to be safe. These approaches, while offering some semblance of control, lacked the sophistication needed to handle modern board complexities. Placing components at safe distances or relying on pyramid models to estimate thermal thresholds were common practices but could mask underlying issues.
The landscape of PCB design has undergone a shift, with escalating power requirements, high-density designs, and stringent performance demands becoming the norm. The inadequacy of traditional thermal methodologies to accommodate these demands is becoming increasingly apparent. Placing components farther apart to mitigate thermal issues inadvertently compromises the speed and connectivity between vital components, creating a problem that necessitates a more nuanced approach.
Shifting thermal analysis left in design flows
Today, the narrative surrounding thermal analysis is evolving. Engineers are recognizing the imperative to integrate thermal considerations earlier into the design process, moving away from iterative “shake and bake” HALT chambers with physical prototypes. The realization that conservative approximations and generic cooling strategies no longer suffice has sparked a renewed focus on implementing thermal analysis at earlier stages of design.
Exploring the thermal characteristics of a design can be done as soon as critical components are placed, not necessarily when the design is complete. Thermally relevant information such as fan velocity, if the system has a fan, and heat sinks are considered. Running the simulation of a board within the chassis of the product makes sure that the users get the most realistic results from the simulation run. Several different types of data can be extracted from analyzing the digital prototype. For instance: temperature distribution of the electrical and mechanical components, air velocity within the design, and even data about the temperature change over time can be captured and make it easy to optimize the thermal performance of the end product.
Thermal necessitates multi-discipline collaboration
Thermal analysis’s resurgence isn’t confined to a single domain. Its integration often spans multiple disciplines, fostering collaboration between mechanical engineers and electronics engineers. This cross-disciplinary approach enables a holistic view of thermal performance, where mechanical considerations converge with electronic design methodologies to create robust, efficient, and thermally optimized systems.
The challenges of adoption and iteration
Despite the newfound acknowledgment of its importance, integrating thermal analysis left into design flows poses challenges. It requires a shift in mindset and methodologies, often involving a learning curve for engineers accustomed to conventional approaches. Additionally, the iterative nature of thermal analysis demands sophisticated tools and methods that seamlessly integrate into existing design frameworks.
Tools like Simcenter Flotherm XT, which can shorten electronics thermal design by using a CAD centric electronics thermal analysis software that connects ECAD and MCAD design flows. Co-simulations of power (with HyperLynx) and thermal (with Flotherm) predict voltage drop, high current areas, and resulting temperature changes. The tight integration of these simulators with the design authoring environment greatly simplifies setup, and ensures frequent simulations with maximum accuracy.
The future of thermal analysis in PCB design
By proactively addressing thermal concerns during the initial design stages, engineers can optimize system performance and enhance reliability. Embracing thermal analysis not only safeguards against potential pitfalls but also lays the groundwork for pioneering advancements in electronic systems.
As the PCB design landscape continues to evolve, the shifting left of thermal analysis in your PCB design flow becomes not just a necessity but a cornerstone of PCB design excellence.
For a deeper dive into this topic download our white paper: Overcome thermal issues in the printed circuit board PCB thermal design process.