Three ways to automate wire harness costing
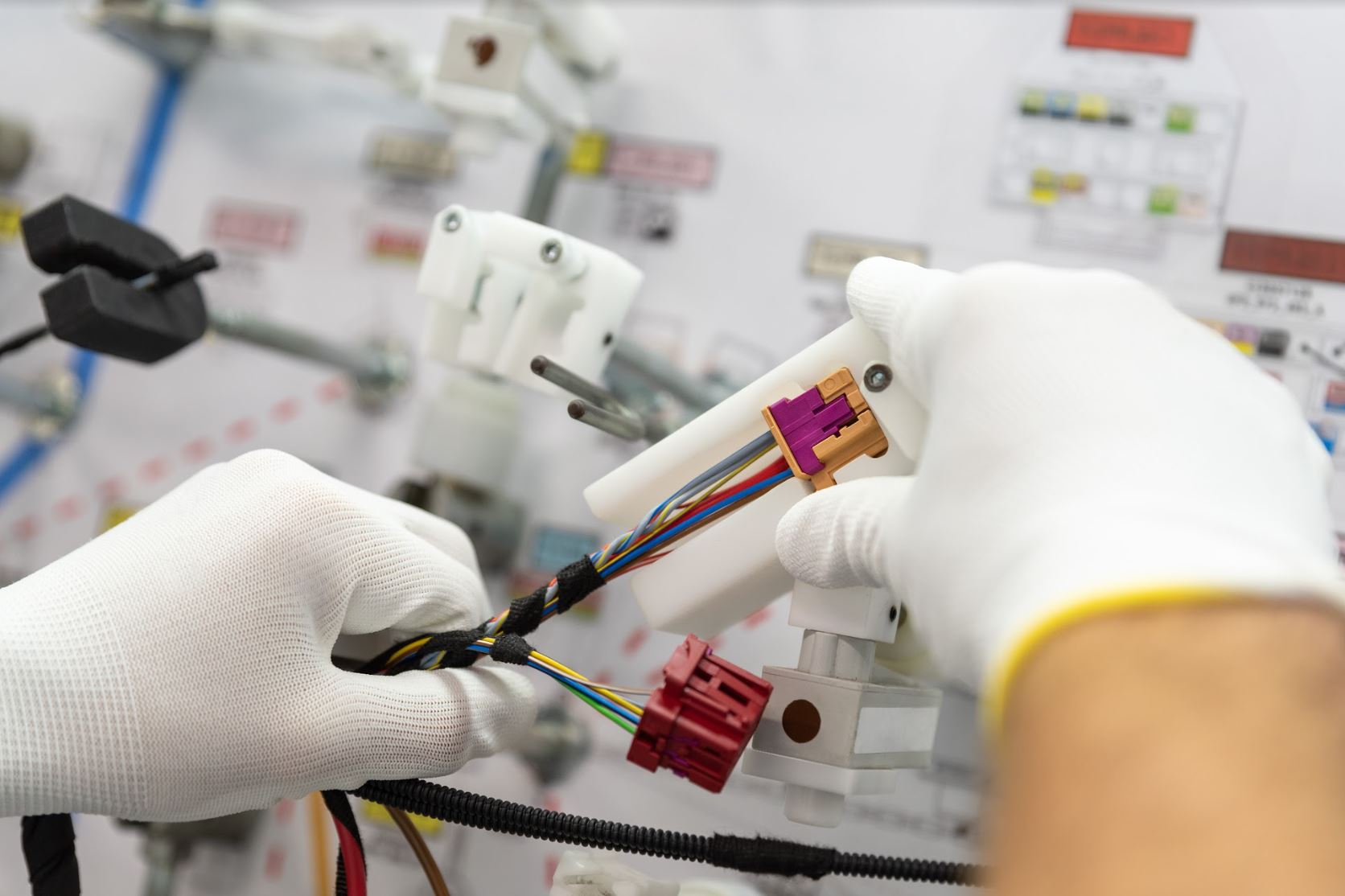
To win in today’s wiring harness industry, manufacturers must be able to quote competitively and produce high-quality products.
Sounds simple, right?
The truth is that a wiring harness contains numerous and diverse individual parts. Wiring harness design and production often involve a blizzard of engineering changes all the way through to manufacturing. Any miscalculation of costs can quickly cut into the bottom line and impact the harness manufacturer’s prospects for commercial success. The pressure to “get it right the first time” is intense, especially in high-volume jobs.
As a result, automating the costing process has become essential. This reality goes for wiring harness manufacturers and suppliers working within tight deadlines and profit margins. But there are multiple automated options available. The task of finding the right fit for your wiring harness costing needs can be daunting. Let’s take a closer look at the three most common technology-based approaches for improving the speed and accuracy of wiring harness costing. (See Figure 1.)
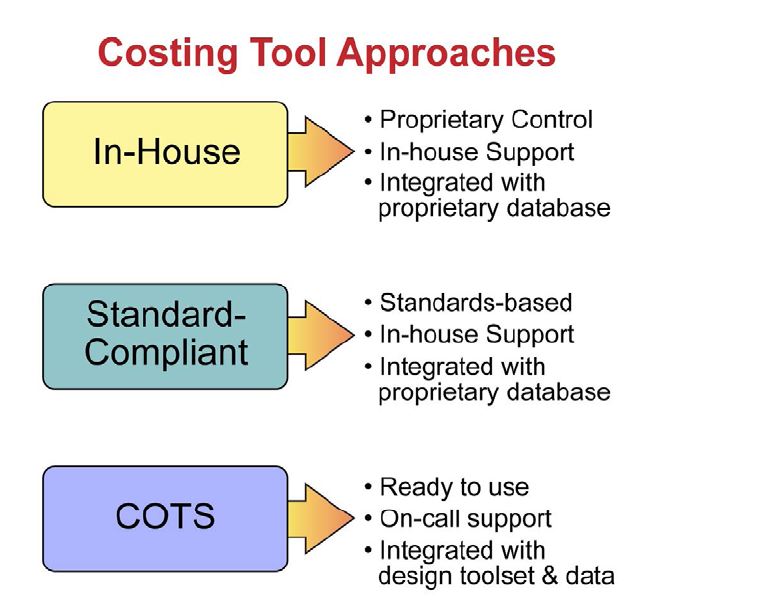
1. In-House solutions
Automated in-house solutions rely on readily-available spreadsheets and are based on one company’s practices. The information technology (IT) team works with internal data sources and adapts data descriptions meant for engineering use. Cost and price elements are added and integrated into a workable whole. The end product is a completely custom solution. Every formula in every spreadsheet cell is deliberately chosen for its role in decision support, customer price quotes or validation. In-house solutions are usually accurate and manage to eliminate some cost estimating uncertainties. However, they also come with high up-front development costs and a heavy ongoing maintenance burden.
2. Standard-Compliant solutions
Standard-Compliant solutions are based on an industry-developed universal standard model for harnesses. (Although they are not themselves “industry standard” because there is no such thing). Solution designs may come from either in-house resources or commercial software developers that incorporate standardized elements. For example, the ProSTEP organization’s AP212 standard using the KBL harness listing format. The drawback of a Standard-Compliant approach is that it creates a maintenance and programming burden for the harness manufacturer’s IT staff. This can lead to a fixation on the mechanics of the XML language and style sheets. In turn, this can create a lack of focus on real cost estimation issues.
3. Commercial Off-The-Shelf (COTS) solutions
COTS solutions are derived from a superset model built from the experiences of many companies. They are fully designed, tested, supported and typically in stock on an actual “shelf.” COTS software from a trusted vendor is the most expedient way to automate harness costing. However, some wiring design and harness manufacturing software vendors omit costing from their COTS products. Others embed the capability and don’t promote it. And, some manufacturing decision-makers become extremely nervous about using COTS solutions. They need to input proprietary labor and material cost rules, which the system must know in order to do its work.
So what is the best approach?
In the long term, the best choice is a comprehensive, flexible solution that recognizes all of the many harness assembly operations, and handles the applicable time and cost standards. A flexible costing system can encompass “what-if” scenarios, labor rate changes and fluctuating prices. The goal is not to “future proof” the costing process, but to fully embrace the policies that are currently in place. For example, determining how many connector cavities exist at a particular harness location, or the number of cavities that contain wire ends. When variables like these are known, it becomes possible to determine the applicable labor standards and fold them into the costing.
Fortunately, today’s COTS solutions, including the Capital Suite from Siemens Digital Industries Software, can automatically model such variables. These digital wiring harness systems derive cost information from normal engineering data, as well as prototype BOMs, architectural studies and similar early-cycle sources. They provide actionable intelligence that was little more than sketchy guesswork just a few years ago. If a design begins to stray from its cost targets, one part of the tool can isolate the cause and another can correct the problem. Now costing professionals have the opportunity to remedy cost overruns early or better yet, prevent them from happening in the first place.
To learn more, download our whitepaper: Fast and accurate wire harness costing.
Like what you just read? Check our our recent series of wiring harness blogs!
- How to improve wiring harness manufacturing efficiency? Let me count the ways
- A tale of two formboards: How to improve merged formboard efficiency
- Building blocks for better wiring harness manufacturing engineering