如鸟群预测迁徙般管理电驱动系统工程
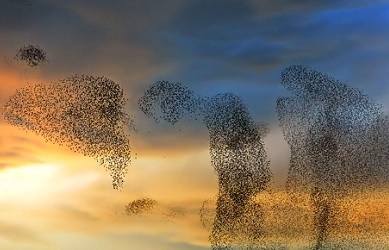
“当我年轻时,电驱动或电动汽车还无迹可寻。汽车广告以速度和马力为卖点。而现在,广告都在讲续航里程和零排放,”Siemens Digital Industries Software 汽车行业解决方案主管史蒂文·多姆 (Steven Dom) 评论道。

电动汽车 (EV) 不仅改变了广告,还改变了工程设计。“负责开发内燃机的工程师团队可能会选择购买或自行设计变速箱,”史蒂文继续说道。“只要它们符合车辆的规格要求就行,决定权在他们手中。这种独立决策对于电动汽车而言并不可行,因为电动汽车的趋势很明显,就是采用集成电驱动单元,将组成驱动单元的电力电子设备、电机和传动系统打包为一个整体。从制造角度来看,制造一个集成单元更加容易,但要正确地制造这个整体,各个不同工程学科之间必须进行持续的对话。对于某些个体和企业来说,这将是一个巨大的挑战。”
应对电驱动系统工程的挑战
西门子专家史蒂文·多姆和电气化产品经理贝努瓦·马格内维尔 (Benoit Magneville) 共同讨论了电驱动系统开发的各个方面,以及企业如何支持工程团队并加强协同。
贝努瓦解释说:“总体目标是设计一种在各种条件下都能高效运行的电驱动系统,但其中存在许多潜在的冲突要求。例如,缩短逆变器和电机之间的距离能够减小整体装配尺寸、降低电缆重量和优化布线;然而,这会带来新的热和机械挑战,因为逆变器的发展越来越受限制。”
与热冷却相关的其他挑战还包括如何满足一系列发热元件的关键需求。为电驱动中的每个组件考虑单独的冷却系统并不是最有效的方法。整合所有组件的冷却系统将简化构造,减少大量管道、泵和热交换器的使用。然而,这会提高工程任务的复杂程度。除此之外,电池和乘客会争夺热管理资源,只有高效的热管理才能为其提供适当的冷却或制冷功能。
此外,在达到电驱动的运行目标和预测乘车人员的声振感知之间还存在着复杂的动态关系。从商业角度来看,乘客舒适度对于制造商而言至关重要,尤其是对于高价值品牌。
解决电力电子设备的设计、系统集成和可靠性问题
开发电驱动电子设备的一个早期阶段是拓扑设计。设计师必须了解效率、成本、容差和电磁干扰 (EMI) 抑制等关键指标才能定义理想的拓扑。设计师可能花费大量工程时间来评估拓扑对车辆的影响,然后根据这些结果进行优化。但是,如果在该过程结束时才发现热影响,这些工作就可能会付诸东流。理想情况下,热设计和仿真应与拓扑设计和评估完全同步。
半导体技术的选择也很重要。但是,如果您不知道如何识别半导体的特性并比较可用的选项,就无法做出更好的决策。“能否了解结温是关键,因为结温决定了可靠性,”贝努瓦说。“您不能仅仅依靠供应商的性能评级或一组测试结果。”
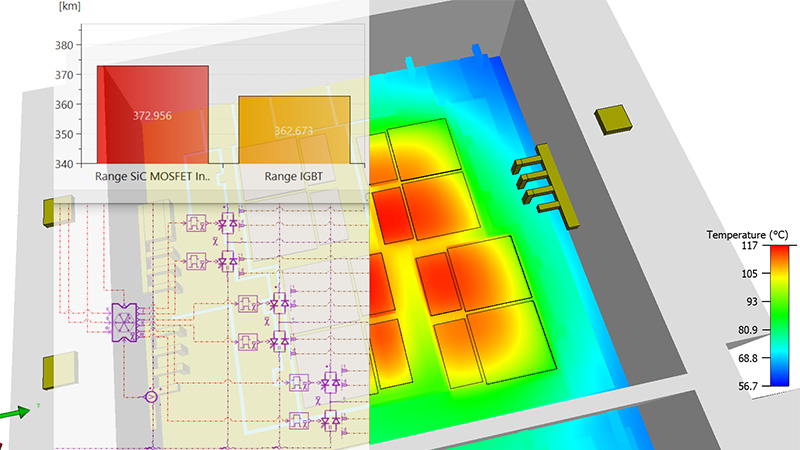
全面准确的电子设计探索涵盖了印刷电路板 (PCB) 和母线设计,需要与机械 CAD 以及电磁、热和结构分析等领域的集成。对此,解决方法是在单一环境中进行开发,使所有工程师都能轻松访问其他学科领域,并且专家可以彼此互动。
ATZ International 网络研讨会将介绍如何构建集设计、仿真和测试于一体的 Simcenter 工作流程来优化电力电子设备,并以可靠、紧凑的封装提供所需的功率密度,从而确保 EMI/EMC 合规性和性能。
如果您想了解更多背景信息,请查阅此博文 - 逆变器:电动汽车的心脏。
从早期的电机选型到性能验证
电机的可靠性是一项基本要求,其使用寿命必须超过车辆保修期和车辆使用寿命。热设计是提高使用寿命和性能的一项主要方法。
“成功始终始于设计,”贝努瓦指出。“电机的要求是从电动汽车的性能目标逐级分解而来。要快速准确地获得电机选型和配置,理想方法是在架构阶段根据电磁效率、热和声振性能快速评估多种设计类型和拓扑。”
Simcenter 产品组合连通了所有这些领域,能够评估电机尺寸和设计对整车的影响。在初始阶段,设计只是一组运行要求。对此,Simcenter 提供了广泛的电机模板库和 200 多种材料。这样就有可能确定全新的电机架构,从而实现目标并生成理想的热冷却系统。只需将任何虚拟模型导出到 Simcenter Amesim,即可对其进行测试和验证。
尽可能提高电驱动传动系统的效率
从运行角度来看,挑战在于如何尽量提高传动系统效率并同时减轻重量,将其与驱动系统的其余部分组装在一起而不超出装配限制。其中的关键是评估齿轮接触应力、轴承力和轴的灵活性,以便准确预测变速箱中齿轮旋转造成的噪声和振动。同样,这意味着需要在设计时考虑多种属性,包括耐用性和润滑油供给。
制造商希望制造更轻的车辆,并可能考虑使用新型材料,但这些材料并不总能得到充分验证,会带来特定的挑战。
预算是另一项挑战因素。单个齿轮的原型制作成本可能高达 200,000 美元。因此,企业需要彻底评估性能,并在进行资本投资之前及时解决任何失故障或弱点。
面向电驱动系统、电磁、热、机械和声学工程师的生态系统
制造商为赢得出色的统计数据和更好的评价而互相竞争。能否满足客户需求是他们获得商业成功的关键,而电驱动的特性可以为此做出重大贡献。制造商必须清楚了解整个车辆中各种组件和系统的影响。
要降低车辆成本和缩短开发时间,一种行之有效的方法是为企业提供单一协同工作环境,以同步推进工程设计、分析和测试的各个方面。Simcenter 产品组合能够连通所有这些领域,使循环中每个阶段的输出既可以用作下一阶段的输入,也可以用作之前步骤的反馈,并最终在整车级别提供验证。
鸟群能够迅速调整方向,不是因为它们跟随领头鸟,而是因为它们能够预判下一步的行动。这正是灵活协同生态系统的优势。它可以帮助企业统一行动。
“任何企业的内部变化都可能令人生畏,增加仿真的使用必须能提高保真度和信心,”史蒂文·多姆说。“必须正确建立新的工作流程,因为它对整个企业具有深远的影响。”
本次网络研讨会将指导您如何应对潜在挑战,并重点介绍从子系统设计到车辆集成等领域的某些客户的成功案例。
有关电驱动的更多信息
电力电子:
电动机:
- 点播式在线研讨会:基于驾驶周期的电机设计和优化
- 案例分析:吉凯恩汽车利用多维仿真减少电动汽车的上市时间和原型迭代周期
传动系统:
- 白皮书:使用多体仿真提高变速箱工程设计的生产效率
- 案例分析:现代汽车公司减少了传动系统中的齿轮啸叫