Digital twin and the emerging challenges for silicon suppliers
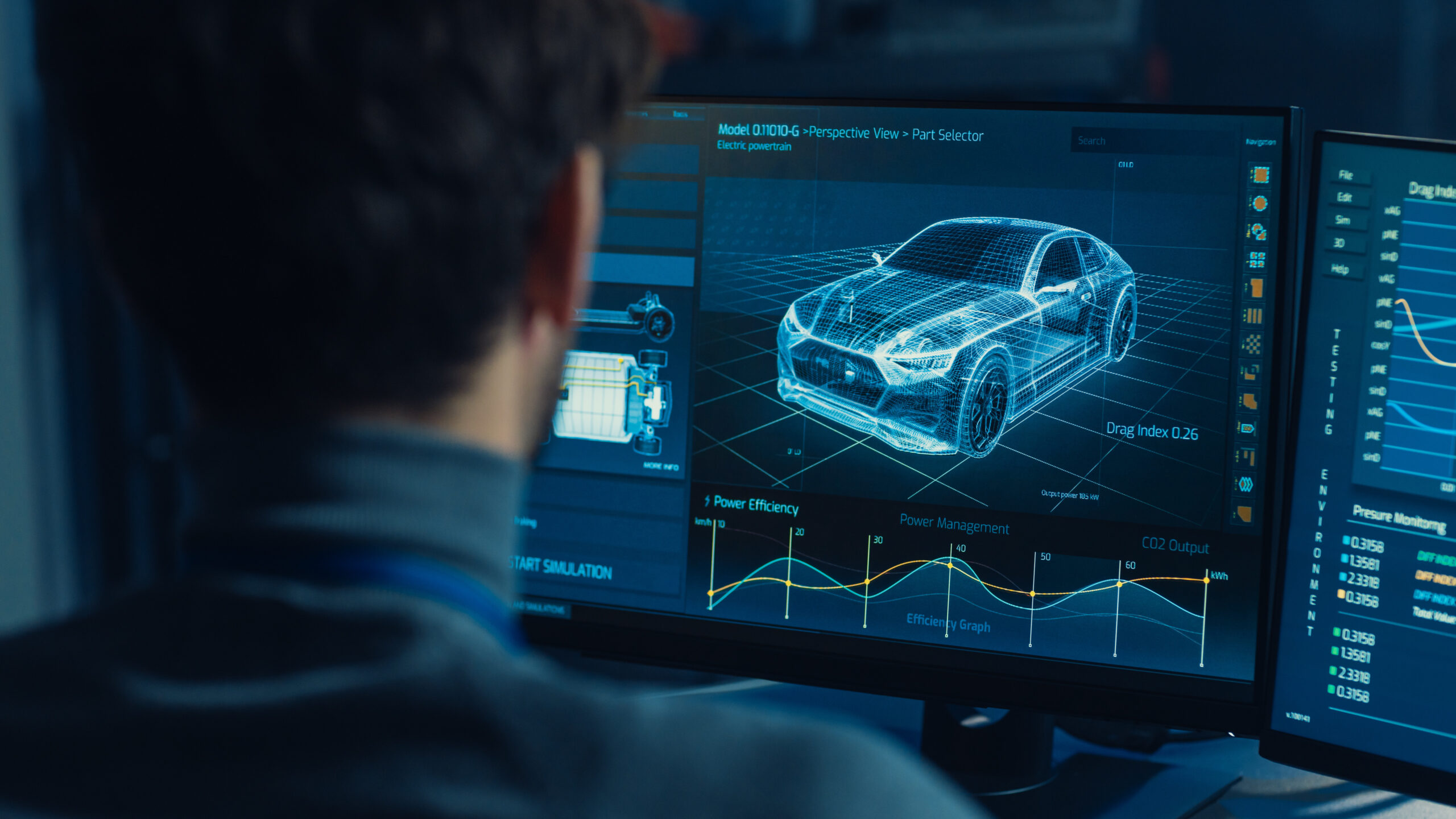
Introduction
The word digital twin is used frequently throughout the automotive ecosystem but putting a clean definition on the exact implementation of a digital twin is quite challenging. One can argue that industry experts, practitioners, and even design automation vendors are directionally aligned, but they may deviate in the details. In Digital Twin Demystified, Will Hastings did a nice job articulating a digital twin as “a digital representation of an asset, product, or process that mirrors the behavior of its real-world counterpart.” But as Mr. Hastings also points out, this definition lacks the substance required for meaningful discussion. How do boil down from the the high level and abstract to specifics defining what a digital twin is in the context of suppliers. In other words:
How do digital twin concepts apply to automotive suppliers (IP or Silicon) and are there emerging challenges that suppliers must recognize?
Before diving into that, let’s set a foundation by defining a digital twin. At Siemens, our definition of a modern digital twin is more comprehensive than traditional viewpoints. In a nutshell, our belief is that there exists only one dynamic digital twin of a product, and that digital twin represents the product as it traverses the numerous design phases and models of physical behavior across the entire development lifecycle.
Key digital twin characteristics include:
- A highly accurate virtual representation of the physical product
- A virtual model acted upon across the lifecycle to simulate, predict, and optimize the product
- A virtual model that takes on multiple representations throughout the development lifecycle
- A virtual model that evolves and needs to be managed throughout the lifecycle
- A closed-loop lifecycle enabling bi-directional connectivity and feedback between the physical and virtual worlds
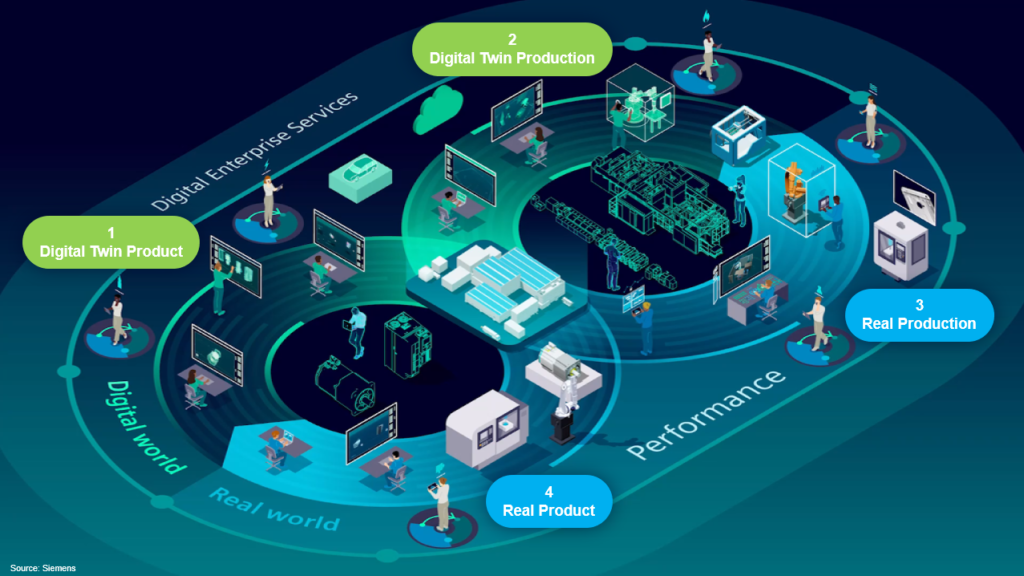
Digital twin for semiconductor suppliers
With those concepts in mind, your first impression may be “Yep, we have been doing that for decades!” That perception isn’t far from the truth. The complexities and cost of failure (i.e., silicon bugs resulting in multiple tapeouts) are simply too high to forego thorough design and verification in a virtual environment.
Unfortunately, new challenges have emerged, and semiconductor providers must re-evaluate their development processes, methodologies, and tools to meet those challenges.
Emerging challenges for semiconductor suppliers
Systems integrators and car manufacturers have recognized that the road to full autonomy requires a digital twin that virtually models systems and connects the virtual and physical worlds. This shift in thinking has new implications and challenges for semiconductor suppliers including:
New Implication | Conceptual Overview |
The creation and delivery of models | Creation and delivery of models supporting systems and vehicle level testing activities. This includes varying levels of model fidelity. |
Tighter coupling of verification technologies among integrators and suppliers | Delivering mixed-fidelity V&V environments allowing for collaboration within and across the supply chain. |
Feedback of real-world data | Feedback of lifecycle data to provide additional insights and support reactive and predictive verification activities. |
Evolution to a virtually vertically integrated company | Interlayer and Intralayer data management and traceability of lifecycle data. Interlayer includes all data management within the context of the product lifecycle. Intralayer includes data exchange between suppliers and integrators |
Want to learn more?
Each of these topics deserves a deeper dive, and therefore, a white paper has been created to provide another level of detail on each implication.
Conclusion
As the automotive industry evolves, so must the semiconductor suppliers that propel it. Disruption to the traditional supply chain model and a path to full autonomy have real implications in how suppliers build and deliver silicon. Companies who start the migration to a modern digital twin paradigm will be well positioned to tackle tomorrow’s challenges today.
Fortunately, the journey to a modern digital twin is not an all or nothing decision. Companies can realize the value of a digital transformation in a piecemeal approach with minor incremental investment. Siemens Digital Industries Software provides a comprehensive suite of solutions to help companies succeed as they move forward on the road to tomorrow’s electronics-centric vehicles.