Sustainability and the digital twin energy resource impact – Summary
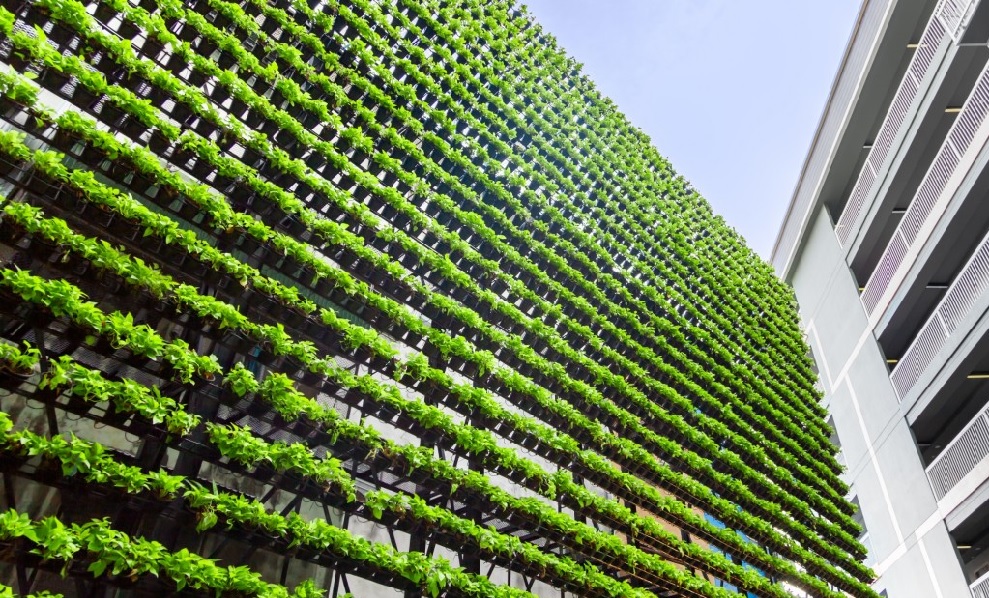
In the previous episode of our podcast series, we focused on sustainability and a holistic viewpoint, describing the key trends driving sustainability. In this fourth episode, we continue our sustainability discussion, looking at the impact of energy resources and focusing on machine operation’s significance in driving overall sustainability for our planet.
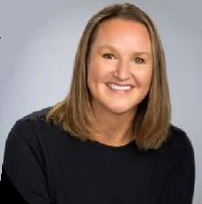
We again welcome our special guests, Eryn Devola and Rahul Garg. Eryn is Head of Sustainability at Siemens Digital Industries Software and a mechanical engineer by training and has spent the last 20-plus years working in the industry. Rahul Garg is VP of Industrial Machinery and SMB Business Program at Siemens Digital Industries Software, and his background is in electrical computer engineering, being instrumental in the design and development of software and other activities for the last 20 to 30 years.
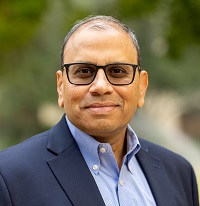
Focusing on machine operations and sustainability, we study its impact on factories and machines. A compelling statistic shows that even a one percent reduction in the industrial carbon footprint of production could mean 70 million tons of less CO2 annually – a startling impact.
And we can better manage this impact by getting OT/IT convergence to control and predict what’s occurring on the production floor and orchestrate that energy use of equipment to optimize it based on the minimization of startups and shutdowns. We want to ensure we don’t have a line going down for material problems, getting the best conversion of those resources.
So, in durable products, it’s using that intelligence we’re collecting by running the machinery, understanding, and identifying the user and energy profiles, and optimizing them. This is a direct path to drive sustainability through industrial machinery.
Additionally, the whole recyclability of waste has a significant impact when thinking about resources used in machine function production, cooling the machine, and cooling the parts. All these items have a significant impact on the overall sustainability of how the production is running.
A part of this is that we use 1.7 of the Earth’s natural resources per year. Overall, we need to decrease that by 59 percent to reach the point where the Earth can renew the resources. And the challenge with that is we can’t just look at CO2, which is extraordinarily essential. However, there are other considerations. Water, is one of those resources that falls right behind it.
In observing how we recapture items that we waste, heat is a massive waste in some places where we generate much heat, and we need a way to turn that heat into energy to reuse it for another purpose. These scenarios are the circularity models, where industrial machinery can play a significant role in solving problems.
Energy resource efficiency is going to have a significant impact on how we are all affecting the planet. From a design perspective, most companies want to see how to improve the machine’s overall performance. But they also need to know how to change the throughput to maximize the utilization of how the machine is being used. It is a balancing act to maximize it. Plus, it’s also necessary to know how to optimize it for sustainability.
These factors require a digital twin to simulate hundreds of variations, which is critical to help ensure you’re making correct choices for design creation. This process involves the materials chosen to optimize water, energy efficiency, and waste – placing sensors on the machines to deliver optimum data metrics. Additionally, it’s essential to design the machine for end-of-life recycling disassembly.
These are all critical things that must be thought through, and you perform that process by leveraging a comprehensive digital twin and a complete digitalization solution that brings everything together cohesively for more excellent optimization.
It’s a multi-part variable equation that must be solved by leveraging digitalization technologies early in the design process. If 80 percent of the performance and environmental impacts will all be determined during the product design phase, it is essential to ensure and maximize the optimization of the whole process. And to optimize the process, you optimize your performance, which helps optimize the sustainability requirements.
Various technologies can help with this. One is virtual commissioning, which allows you to bring all the capabilities in a virtual format without building or constructing even a single part. The plus side is that if something goes wrong in the virtual world, you can start from scratch again, making it easy to bring in and take advantage of the benefits of a digital twin, leveraging it to reduce time and cost. A digital twin helps test and optimize operations, making production more flexible and predictive.
All this can be done via virtual commissioning and digital twins. It also deciphers the carbon impact. Therefore, it’s more than just optimizing for peak performance but understanding the sustainability and carbon impacts of how a machine will be running.
The environmental impact will be one of the significant shifts in peak machine performance in the future. Several variables need to be solved and optimized for continuous growth. Over time, it will not just be the virtual commissioning but also virtual maintenance and repairing or upgrading the equipment with minimal human interaction. A primary concern of companies is the ability to maintain equipment moving forward.
With sustainability, it is a multi-part equation – from water usage radiations to other sets of variables to be solved. One of the most significant pieces of legislation is the Corporate Sustainability Reporting Directive coming out of the EU for effectivity as a requirement for reporting in fiscal 2025.
This directive will require entities manufacturing or selling in the EU to report 400 different environmental-related KPIs. This pushes legislation, providing the transparency needed to give information into design processes to minimize impacts.
Technology needs to be available for sustainability, and we are approaching the tipping point where people are prioritizing applying that outstanding technology to solve problems. Also, governments are not only writing legislation but also providing incentives in funding to help solve problems. Therefore, we’ve got the motivation, funding, technology, and industry. We also have the momentum and the size to make a big difference.
There is much opportunity for growth. Please join us in our next episode of the sustainability series.
Learn more in the podcast or transcript.
Siemens Digital Industries Software helps organizations of all sizes digitally transform using software, hardware and services from the Siemens Xcelerator business platform. Siemens’ software and the comprehensive digital twin enable companies to optimize their design, engineering and manufacturing processes to turn today’s ideas into the sustainable products of the future. From chips to entire systems, from product to process, across all industries. Siemens Digital Industries Software – Accelerating transformation.