Talking Aerospace Today – The Power of the Digital Twin Ep. #2 – Transcript
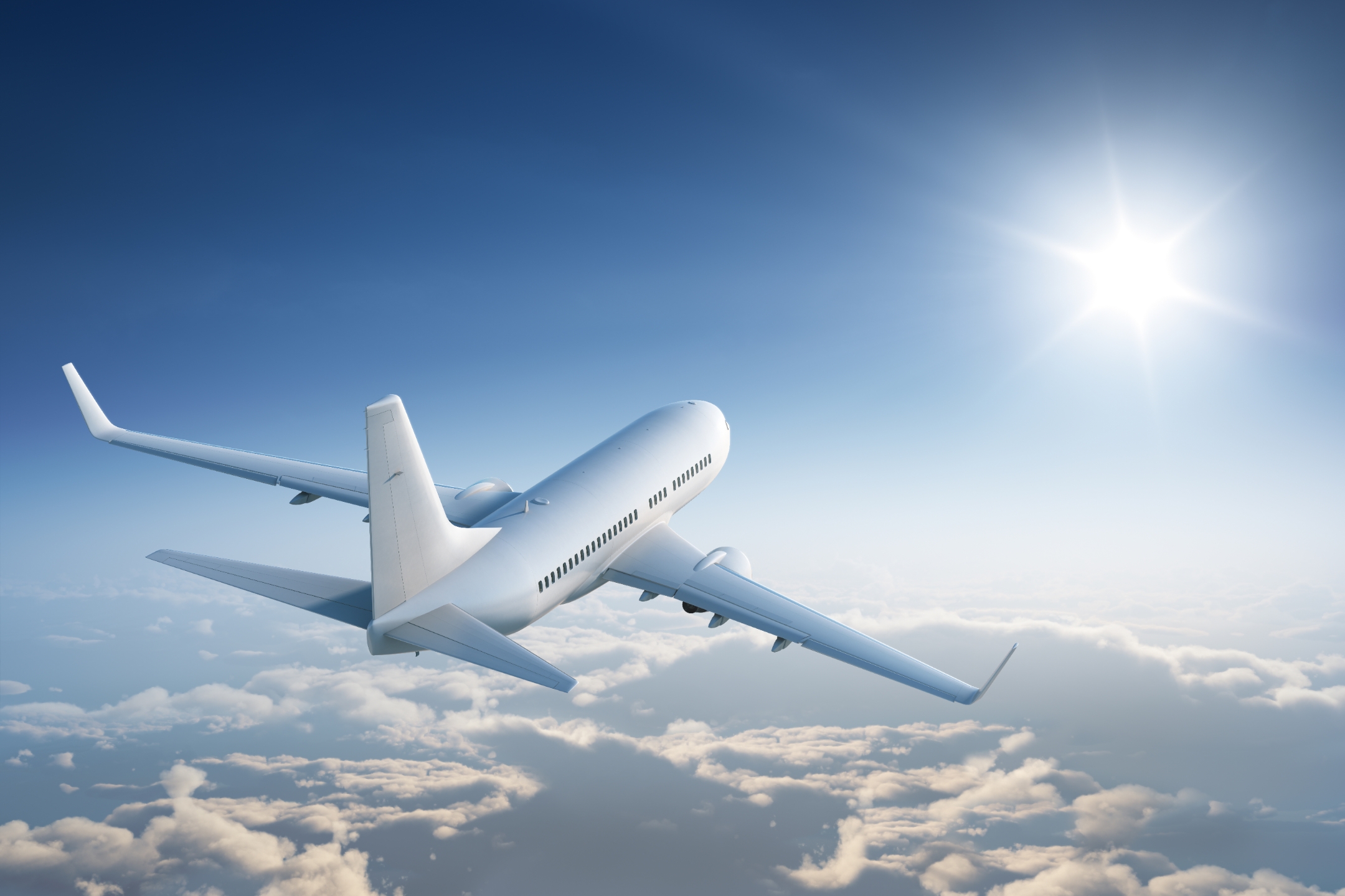
Continuing their conversation from the previous episode of Talking Aerospace Today, Todd Tuthill, Patty Russo, and Dale Tutt discuss how the digital twin can increase integration and interoperability, as well as improve areas such as supply chains and sustainability.
You can listen to the episode here or read the transcript below.
Patty Russo: Hello, and welcome to episode 2 of our new season of Talking Aerospace Today from Siemens Digital Industries Software. I’m Patty Russo, the Global Marketing Manager for Aerospace and Defense. Today we continue our conversation from last episode introducing our new Vice President for Aerospace and Defense, Todd Tuthill, and his insight into the industry. Todd joins me today along with Dale Tutt, our Vice President of Global Industries– Dale is Todd’s predecessor as Vice President Aerospace and Defense Industry here at Siemens.
Patty Russo: So, Todd, last episode we talked about digital transformation, workforce issues, and benefits of the digital twin. You talked about the importance of culture and organizational change as key considerations as companies consider the digital transformation process. I’d like to start with a followup to build on that conversation. My first question today is related to customers who have not yet adopted the digital twin or a digital transformation in their organizations. Some of them potentially are in this analysis-paralysis phase, so they choose to do nothing because it’s so overwhelming. And Dale, you’ve talked about the fact that customers do benefit from the digital twin. One of the areas that we talked about at a recent conference about the digital twin was related to trust. Can either or both of you comment on the benefit of the digital twin and the benefit of trusting the digital twin?
Dale Tutt: I go back to a story that I had when I was a little bit earlier in my career. We had been developing new simulations and we were having great success. They were actually pilot-in-the-loop simulations. So they were digital twins but with hardware and did a lot of desktop simulation, and we transferred to hardware and pilot-in-the-loop. And we came back and the pilots came to the conclusion that we probably needed to change something. And I remember my VP asking us at the time, “Should we delay our program? Are you that confident in what you’re doing?” And we’re like, “Oh, well, we’re not sure yet. This is still our first time.” But as a company, we took some mitigation measures to make sure that we could have something in place. And it turns out, when the airplane started flying, it did exactly what had been doing in our simulation work. Because we had then built that foundation that we had validated it to one aircraft program, then we’d actually had worked it and used it to make decisions and drive decisions. In this case, we did mitigations on the second program, then the third program came along and it was a different airplane, a completely different airplane. And when our pilots came back and said, “We think we have an issue with the flight control system,” we went ahead and the company just decided to change it. So, over time, they had developed confidence in the results that we’re getting not just in how we’re using the technology, but the processes that we’re using to validate and keep configuration control of our simulations, our models—that digital twin in that case—and then how we were evaluating and keeping it up to date really gave the company a lot of confidence in the work that we were doing that they were able to then use that to drive decisions going forward on future programs.
Patty Russo: Todd, do you have anything to add to the idea of why is it so beneficial if companies in the industry start to trust the digital twin?
Todd Tuthill: I think one of the conversations I would have with some of my staff is we’re designing control systems. I would say where’s the truth? In other words, we’re going to build physical hardware, we’ve done the simulation, we’ve done the performance, but where is the truth? And we’d have this great discussion. And of course, I’m talking to a mechanical designer, the mechanical designer is trying to say, “Well, the truth is we cut the metal and we move the actuators back and forth.” And whatever they do, that’s truth. And I’d say, “Well, that’s difficult, because I’ve got a customer that’s given us requirements to validate this over thousands of hours of life over all kinds of conditions.” And we’re only going to test eight or 10 of these, we’re not going to test these for the entire complete life, we’re not going to put it through every single possible condition, we’re not going to build all of the combinations in terms of tolerances for this whole control system. How are we going to do that? And the reality is what we do is that we create a model, the model helps us learn about the physical thing we’re going to build, we build the physical thing, and then we validate that model. And then we take the model virtually through all of those situations, through all the parts of the envelope, and that’s where we really gain the confidence that the system has delivered and will perform the way it’s going to perform. That’s where we start to trust that our design works. And as I see in my career over the industry, what I see is we do more and more virtual tests, and less and less physical tests. We’re not to the place yet where we don’t need any physical test. I have hopes that in my lifetime, in my career, we’ll get to some of that where we can do prototypes virtually and not have to build them and do all that learning from a model. I think that’s a goal I have to promote. But I think it’s that’s the trust; it’s how much can you do virtually and trust it virtually as validated or compared to the physical.
Patty Russo: Those are both great examples. So, learning and seeking the truth, so to speak. And Dale, in your case, seeing the benefits play out from using the digital twin, all leading to the idea of having confidence in gaining that trust. Another area that increasingly takes the attention of the aerospace industry and aerospace customers of ours is interoperability and integration. How can the digital twin help with those areas within their organizations and disciplines?
Todd Tuthill: I talked earlier about building up this idea of the journey of going into digital twin and starting with just maybe a mechanical design and starting with the electrical design. And I think, fundamentally in that journey, you start in pieces. But eventually, you want to put the pieces together, whether in simulation. Again, you want to do that, you want to learn from the building and integration of all those pieces before you have to go do that physically. The digital twin is this area and this opportunity to learn, to make mistakes, and to optimize before you do things for real. And that’s certainly one the areas when I think of integration of all the pieces it takes to put together a subsystem for an aircraft or spacecraft, and then to put the spacecraft together itself. I can’t imagine back in the days when I’ll call the real engineers, I think of the Apollo program early on when they didn’t have any of these tools, and I look at what they had to do. And it’s just astounding and incredible to me, the kinds of integrations that they had to do to make a rocket fly, and they just didn’t have the kind of tools we have. And wow, the benefits we have from digital twin today.
Dale Tutt: But they did have slide rules. But no, I have to agree, the interoperability is key — the ability to be able to move data. I always just wanted my engineers actually working on solving problems, not managing data and managing paperwork. So, I think as we get with more interoperability and with higher levels of integration, you are able to move your teams away from that. Whether it’s your engineers or technicians, they’re focusing on solving the challenges, not on managing data.
Patty Russo: I’ll dive a little deeper into the idea and the topic of digital twin. Can the digital twin help customers and help companies in our industry address supply chain issues? And if so, how?
Todd Tuthill: Certainly, if I look at the supply chain, let’s look at a simple scenario I might have in supply chain. I’ve designed this circuit cart, and circuit cart has a multitude of different components on it, and I’d like to know what are the components I have in stock, where are those relative to long lead items, which of the companies I’m working with are likely to have problems. I like to be able to integrate that data and understand that so I can predict supply chain problems before I have them met. That’s thing one. And then I’m going to find some supply chain problems. So then I want to be able to quickly do a redesign to design the part that I can no longer buy anymore, I want to design that part out. And I’d sure like to do all of that in a digital world, to not have to do things physically, to figure out how to update that design so that by the time, the parts I have on stock are no longer in place, I already have a design ready to go to mitigate that problem.
Dale Tutt: When I think about the supply chain and the challenges that you have in a supply chain, it’s just understanding the expanse or the extent of your supply chain and how do you model it. I think all the years that I’ve been in the business, we just knew that we were going to have a part show up on our dock one day, and we might have insight into when it was actually gonna get shipped, but we may not know how it’s actually going to get there. As I think about our global supply chains now and how do we model it more effectively, maybe this is where tools, if you could almost think about your digital twin of your supply chain of the business processes, even the routings. So if you have a shipment from China to your company, what route are the ships going to take to get there? Are they going to go through the Suez Canal? Are they going to be on a train that’s going through a massive snowstorm in the Midwest of the US? And you’re going to have a delay. How do you start predicting these delays and be more proactive than just “Oh, the parts didn’t show up. Now, let’s start looking for it.” So, I think nowadays with industrial metaverse and bringing that forward and bringing this concept of a digital twin of your supply chain, you can start to think about where your parts are actually flowing in from and applying digital logistics to be able to actually bring those solutions forward and have much more insight into your supply chain and what’s available than what is available several years ago. So, the digital transformation has really given a lot of visibility, transparency, this connectedness between the OEM and all of their suppliers, and maybe their suppliers, and have a lot more insight so that you can start to be predicting and forecasting disruptions and reacting weeks earlier before you find out the part didn’t show up because there was a ship that got stuck on the Suez Canal.
Patty Russo: We’ve been talking about the digital twin, I’m going to continue on that path and ask a question around the digital twin and sustainability. Can and if so how does a digital twin support our customer’s sustainability goals?
Todd Tuthill: It’s a great question, Patty. I know an issue that’s on top of the mind for a lot of our customers, how best can they implement sustainability in their designs? It’s a goal that all of them have. And when I think about sustainability from a customer perspective, I think about the two central key things that they need: they need to be really, really innovative, and they need to be able to pay for and afford what they’re doing. So, if we think from the innovation standpoint and from the idea of these radical new things the customers need to do, it starts from a fundamental idea of the front-end concept development in systems engineering, and this idea of where do I go, what parameters do I need to set relative to just the fundamental requirements, the fundamental architecture that it’s going to take to meet these new ideas in terms of greener vehicles, in terms of lighter vehicles, in terms of more efficient vehicles. It’s not simply a matter of just going out and designing a wing, that needs to be done in the context of the overall vehicle and the overall requirements and goal because while in some cases, maybe a lighter wing may make sense; in the context of the overall vehicle from a system standpoint, maybe it doesn’t because maybe the lighter wing is not going to be something that is going to last for the lifetime of the aircraft, as well as looking at new kinds of sustainable requirements in terms of materials, the lifecycle and where those materials go after the vehicles research its end of life. It’s a whole new set of requirements that in aerospace, we haven’t always been as concerned with as we need to be from a sustainability standpoint. And then the idea of cost of doing it as efficiently and as optimized as we talked about, we keep talking about this idea of learning and optimization. But that’s kind of the key fundamental part of a digital twin; the thing that it allows us to do is to learn and to optimize digitally before we have to go build it physically. And those are just a couple of the ways. We could talk about sustainability and operations in the new buildings that are building and all those kinds of things but I don’t know if we want to go there today. But just lots and lots of ways that digital twins and that digital transformation and digital threads can benefit our customers from all the really difficult work they have to do relative to sustainability.
Patty Russo: So we started out by talking about organizational change. And it seems like the answer is the digital twin can potentially help with that, and helps move companies and helps them change how they need to work for what’s needed for the future. Do you want to add any other comments to that?
Todd Tuthill: Well, I’ll add it maybe from the perspective of the engineers designing all these great new products. And from there, I think one of our goals at Siemens is to really make life better for our customers and our engineers. When I was back in functional leadership, I used to look at and try to understand how the engineers that work for me spent their day. They spent a lot of their time looking for information, moving data, doing things manually; things that they didn’t go to school to learn; things that really don’t bring a lot of job satisfaction. Engineers want to be creative, they want to think of new things, they want to do analysis and make high-level decisions; they don’t want to move data and move information. And this whole idea of digital transformation of moving from a document-based way of working to a digital way of working, and this idea of really high-level simulation and integration really creates a working environment for those engineers that is far better than this idea of just moving data around all day.
Patty Russo: You’ve used an analogy to describe what you just talked about. Would you like to share that? Because I think it’s a great foundation for my next question. And the analogy has to do with boats.
Todd Tuthill: Patty you know me well. We’ve only known each other for a few months but you’ve already heard some of my stories. I like to talk about islands. And I think in a lot of companies, a lot of the systems and the tools they have because some companies will say, “Hey, we’ve done digital transformation. I’m doing these things digitally.” And we talk about it as a journey. I think the first step in the journey is to go from doing things manually in documents to doing things digitally. But the next step, as Dale talked about earlier, is the connection. And what I’ve seen in companies I’ve worked for and other companies that I’ve worked with is that all of these systems are islands of data. The engineers – it getsfrom island to island on the backs of engineers and rowboats, and those rowboats are called Microsoft Excel. That’s the way a lot of the industry works. And certainly, another one of our goals in Siemens is to help customers integrate all of their data and all of their systems to provide the digital backbone where the single source of truth resides and where data can be much more easily shared. Because as I talked about before, in making the engineers life better, who wants to copy data to and from Excel or in or out of their email box? And how many of us just today have said, “Where’s that file?” And we go diving into the inbox. Digital transformation is intended to really help solve those problems so that we don’t live on islands — our digital systems are islands of data connected by Microsoft Excel.
Dale Tutt: I love that and I love that analogy; the view of all these digital islands connected by rowboats is a good visual. We talk about digital transformation is going to change the future of work for engineers, for technicians, and for people that are servicing aircraft across the board. And it’s going to be really moving from– we’ve always talked about paperless, but it became digital paper. And now how do we make that digital paper actually go away and help to automate some of those processes, as Todd says, to provide that connectivity so that our technicians and our engineers are actually working on what we need them to be working on, solving complex engineering problems or building products faster in a more innovative way and higher quality. So that’s when we start to talk about where digital transformation is really going to start changing the way people work; that’s the opportunity for us. So, it’ll be a nice change for a lot of people, and it has been a nice change for a lot of people.
Patty Russo: Over the years that I’ve been involved with Siemens, I’ve heard some of the same messages. And over the years, the incremental changes have been dramatic for those customers who have implemented some of the solutions that we’ve talked about. And the digital twin kind of seems to be the launch point to take us to the next level, which is accelerated digital transformation. I understand that there are some customers that are making some progress with digital transformation. I’m sure our audience would love to know what are some of the lessons learned from those customers that we have been working with that are making that leap from the digital islands and Excel rowboats.
Todd Tuthill: I’d say the ultimate goal is to see real value in change, in how they bring products to market. We want them to be able to bring products to market faster, we want them to be able to bring products to market for much less cost, and bring real value to their customer, as well as creating a real environment that their employees want to work in. It’s not one thing, it’s a combination of things, and digital transformation can help you in all those areas. We talked earlier about people, processes, and tools. One of the things I’ve learned and that I’ve seen other customers learn is that it takes all three. And when you think about a transformation, you’re going to transform all three. If you look at digital transformation, I think one of of the things you don’t want to do is just implement your current processes that are paper-based or are not digitally based in a digital transformation. Think about the real advantages and things that computers do better than people. And think about all the ways that you can find benefit from computers and transform your processes, then transform your tools. And don’t forget about the people and the whole organizational change management aspect of that and transform all of them along the way. And then as you do that, also look for incremental value. You’re always looking at the horizon at the place you want to get to. Don’t focus just on the horizon, focus also on incremental value and the ways that you can improve your daily working environment, your time to market, the things you can learn from digital transformation. Find those incremental values, and that really brings a sense of accomplishment to the team and will energize your company and really continue to have people on board with “This is the way we want to go with digital transformation.”
Patty Russo: So, what I’m taking away from this great conversation is there are trends that continue in our industry, the digital twin can add tremendous value to our customers, and goal of accelerating digital transformation in organizations is a process that can take a little bit of time, but value can be achieved in short increments. Is there anything else that we want to wrap up with, Todd, before we close out our session for today?
Todd Tuthill: Well, I’ll just go back to, again, thank you to Dale for passing the baton to you and me and for this opportunity. I’m really looking forward to the opportunity in the future to talk about aerospace. And thank you to everyone who’s listening in. I’m really looking forward to the journey that we’re going to be on together, talking about aerospace, talking about digital transformation, and all the topics around that. And thank you to you, Patty, too, as well for really moderating and asking some really interesting questions today.
Patty Russo: Well, that wraps it up for us today. Dale, thank you. Todd, thank you. And we look forward to talking to you on our next Talking Aerospace Today podcast.
Siemens Digital Industries Software helps organizations of all sizes digitally transform using software, hardware and services from the Siemens Xcelerator business platform. Siemens’ software and the comprehensive digital twin enable companies to optimize their design, engineering and manufacturing processes to turn today’s ideas into the sustainable products of the future. From chips to entire systems, from product to process, across all industries, Siemens Digital Industries Software is where today meets tomorrow.