Meet customer’s expectations with smart manufacturing and digitalization
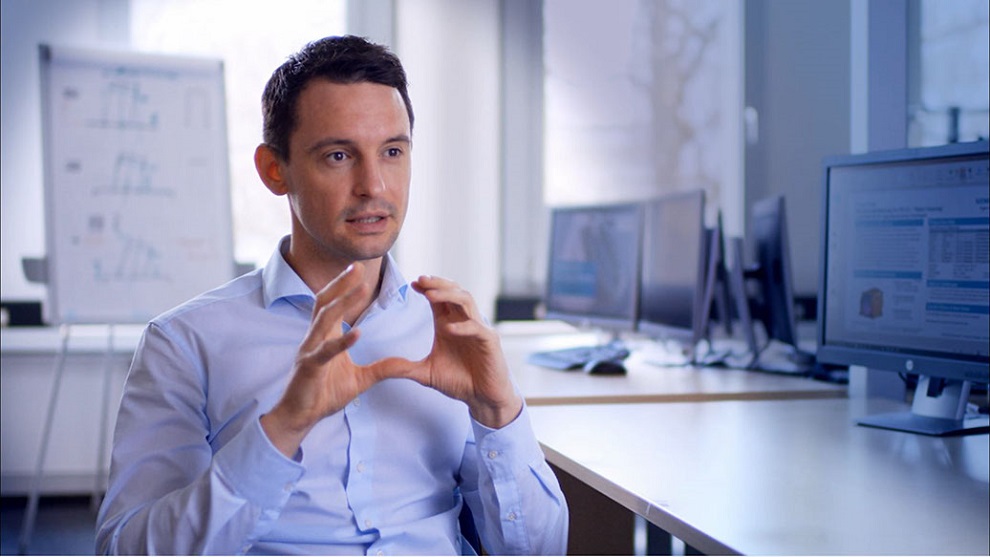
There are significant challenges in the industrial machinery and manufacturing industry. Smart manufacturing systems enable companies to overcome these challenges, including product complexity and sustainability.
A broad spectrum of companies provides the equipment that goes into larger manufacturing companies and greater manufacturing organizations. General Motors and Lockheed Martin are good examples of how equipment that goes into the factory shop floor is near the building of the parts and assembling equipment or products. However, complexity issues are causing end customers to demand customization for their specific shop floor needs, ensuring that products be built from those machines quickly. In addition, supply chain and critical labor shortages only further complicate all companies.
Therefore, it’s necessary to meet customer needs using less energy and resources and ensure that equipment performs optimally.
Listen to the Smart Manufacturing Overview podcast.
Some of these issues predated COVID, as companies needed to leverage innovative technologies like digitalization to bring their design manufacturing processes to the next level. However, the pandemic exponentially increased this process, with companies needing to drive digitalization into their businesses. Additionally, it was necessary to build machines to become smarter, enabling end customers to implement smart manufacturing.
Having smart factories helps lead equipment manufacturers to create and build smart machines. In turn, digitalization is crucial to helping companies to do things differently and succeed in a highly competitive market.
Digitalization requires some essential capabilities:
OT and IT convergence focus on how end customers will use technology, equipment, machines or products while considering how the process of closed-loop manufacturing and execution is delivered, including speed of delivery. It also finds closed-loop quality, ensuring that the products and the parts are right the first time.
Factory and operations are becoming more holistic, along with the OT and IT convergence concept. This convergence is essential to drive the production and operational efficiencies that companies need. For example, OT (Operation Technology capabilities) allows a company to monitor the operations on the factory floor. And IT also manages the business operations and business systems. So, the whole concept of OT and IT convergence enables real-time process capabilities that monitor what’s occurring on the shop floor and the business impact.
In parallel, the shop floor can react expeditiously to requirements from the business systems. So, because customer orders are dynamic, they require more flexibility in manufacturing operations to drive customization. It is promoted through a business operating system to ensure production shop floor systems can react to changing demands quickly and flexibly. This aspect is the primary value that OT/IT convergence provides for extreme flexibility and visibility to drive necessary changes.
Listen to the OT/IT Convergence podcast.
Closed-loop manufacturing allows a company to move to the next level of detail and provide better controls throughout the manufacturing operations to maximize production throughput. All companies must establish how to yield maximum benefits from the assets used in the factory. The complete closed-loop manufacturing process ensures customer orders are coming in as scheduled, tracked correctly, and billed to the correct designs and engineering systems created for them.
When orders go through the execution process after the orders are fulfilled and products delivered, there is the ability to provide feedback on the order and engineering systems. Issues can occur during the manufacturing process that may have or have not been captured or thought about in the engineering systems. Therefore, having a closed-loop manufacturing execution system provides the ability to bring diverse organizations in a company together for easier continuous monitoring.
Listen to the closed-loop manufacturing podcast.
Closed-loop quality and the manufacturing process cannot exist without each other. It is essential to ensure that what gets manufactured has the correct quality while confirming that the products and parts are delivered on time and to the correct specifications. By integrating quality and manufacturing, a company or factory takes advantage of digitalization by taking the quality process to the next level. The goal of closed-loop quality is to optimize the manufacturing process by identifying and correcting nonconformance early, thus minimizing scrap and rework to improve the overall product to market.
Manufacturers desire to accomplish these goals by accounting for quality in phases. This requires writing a plan for quality up front, examining all requirements for quality before building anything, checking against well-defined capabilities, and determining and defining where the failures could exist.
Companies implementing a closed-loop quality process achieve a median product compliance rate of 99 percent, with the majority performing between 97 and 100 percent. Conversely, organizations without this capability have significantly more variability in performance, with the majority performing between 90 and 98 percent.
Listen to the closed-loop quality podcast.
Sustainability in manufacturing includes several contributing factors, including gasoline, vehicle movements, passenger cars, and trucks. Also, there are other contributing factors to energy consumption via factories. These are the engines of the world producing goods to run the engines because you need energy to get energy. One must rely on fossil fuel or other mechanisms to drive the factory’s electricity requirements.
Therefore, these are huge contributors to the environment. When you think about a five percent reduction change in the electrical power requirements of a motor – this is typically the equipment that’s “running the factory” – it equates to a considerable impact. As a result, sustainability and factory manufacturing machines have a strong relationship and a strong potential for a significant impact on what kind of an effect it has on the planet.
Listen to the sustainability podcast.
Siemens Xcelerator, the comprehensive and integrated portfolio of software and services from Siemens Digital Industries Software, helps companies of all sizes create and leverage a comprehensive digital twin that provides organizations with new insights, opportunities, and levels of automation to drive innovation.
For more information on Siemens Digital Industries Software products and services, visit siemens.com/software or follow us on LinkedIn, Twitter, Facebook and Instagram. Siemens Digital Industries Software – where today meets tomorrow.