The advantages of a multi-disciplinary design in industrial machinery
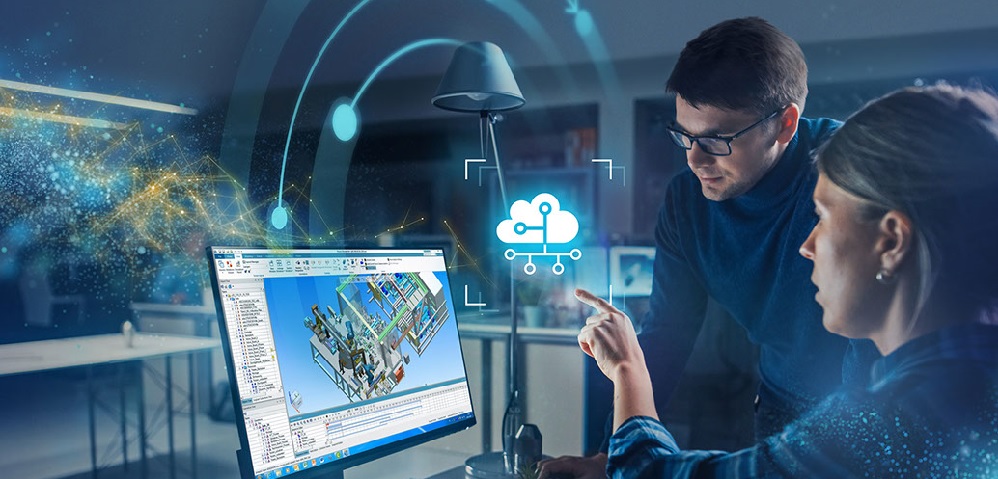
Current machines are highly sophisticated mechanical geniuses; however, electrical power has been a part of motors, rotary equipment, and camshaft gears in the last two decades.
Digital Engineering 247 magazine highlights an article with Rahul Garg, VP of Industrial Machinery and the SMB Program for Siemens Digital Industries Software, discussing the complexity of the machine-building process.
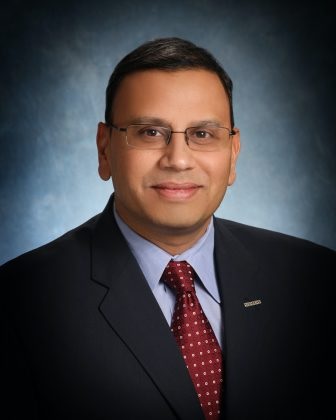
Learn more in the article.
Engineering disciplines must work collectively to ensure a design is completed on time and be cost-effectively manufactured and commissioned. As a result, manufacturers are leveraging a multi-disciplinary design approach to assess engineering design and manufacturing machine-building complexities for improved efficiency.
Using a multi-disciplinary design approach
A multi-disciplinary design approach combines all capabilities and skillsets to advance machine engineering into a collaborative environment, paying dividends in machine design output quality with all areas working collaboratively. Machinery companies are aggressively condensing timelines to deliver complex machinery to market. In turn, there is a significant effort to provide simulation into the design process, including a multi-discipline domain, finite element analysis, computational fluid dynamics, vibration and harshness.
Companies are trending toward a collaborative approach in the current landscape, but it’s essential not to forget conventional processes without migration. For instance, when new technologies are adopted, machinery and automation companies must not consume them all at once because it’s unsustainable culturally. However, we are witnessing companies adopting these innovations most effectively.
Additionally, virtual machine simulation and commissioning provides another significant benefit of adopting a multi-disciplinary approach to machine design. This technology helps to validate the software code in the virtual world before physically operating on the factory floor. Consequently, simulating the code running on a virtual twin of the machine generates considerable dividends in time and resources.
In this modern domain, the software is driving the machines. Therefore, when you simulate the code running on a virtual twin of the machine, it generates considerable dividends in time and resources.
“Validations of the PLC software are in a managed environment using virtual commissioning, with an entire modular product development strategy. So, machine builders can perform the simulation upfront and link the software to the modules,” says Rahul Garg of Siemens.
Machinery companies are striving to compress timelines to push sophisticated machinery to market. There is a significant effort to provide simulation into the design process, integrating a multi-discipline domain, finite element analysis, computational fluid dynamics, vibration, and harshness.
Siemens’ software solutions
Siemens’ Xcelerator portfolio helps companies of all sizes create and leverage digital twins that provide organizations with new insights, opportunities, and automation levels to drive innovation.
For more information on Siemens Digital Industries Software products and services, visit siemens.com/software or follow us on LinkedIn, Twitter, Facebook and Instagram.
Siemens Digital Industries Software – where today meets tomorrow.
Related links:
AME podcast01
AME podcast02
AME podcast03
AME podcast04
About the author:
Rahul Garg is Vice President of Industrial Machinery and the SMB Program for Siemens Digital Industries Software. He and his team are responsible for identifying and delivering strategic initiatives and developing solutions for the industry, working closely with industry-leading customers and providing thought leadership on new, emerging issues facing the machinery industry. Rahul’s experience and insights are derived from a 25-year career of delivering software-based solutions for product engineering and manufacturing innovation for the global manufacturing industry. He has held leadership positions in multiple areas, including research and development, program management, sales and P&L management, having focused exclusively on the industrial machinery and heavy equipment industry since 2007. Rahul holds a master’s degree in Computer Science from Wayne State University, with a concentration in Operations Management and Strategic Marketing, as well as a Bachelor of Computer Engineering degree in Computer Engineering from Bombay University.