+25 to 35% intralogistics improvement: Eye-opening simulation and analysis of manual vs. automated intralogistics and ASRS integration through Plant Simulation
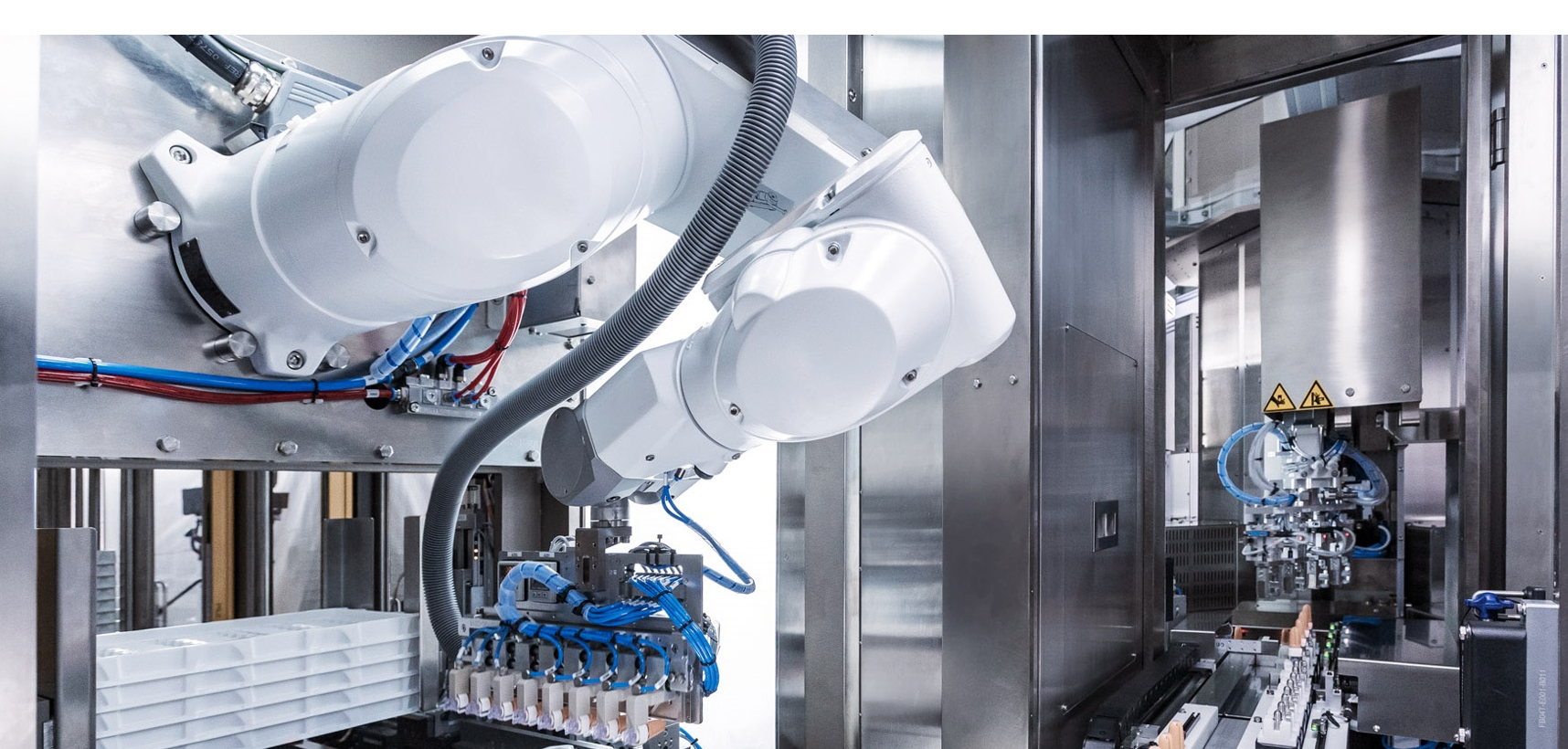
Exploring automation in autoinjector manufacturing: A comparative analysis for medical device production
SHL Medical; Lu Yi-Chi and Luigi Fumagalli
Medical device manufacturing processes have undergone significant transformations, particularly in the realm of automation. At the 2024 Plant Simulation User Conference, we delve into a comparative analysis of manual versus automated intralogistics and automated storage and retrieval system (ASRS) integration through Plant Simulation, shedding light on the transformative journey within autoinjector manufacturing.
Brief introduction to SHL Medical
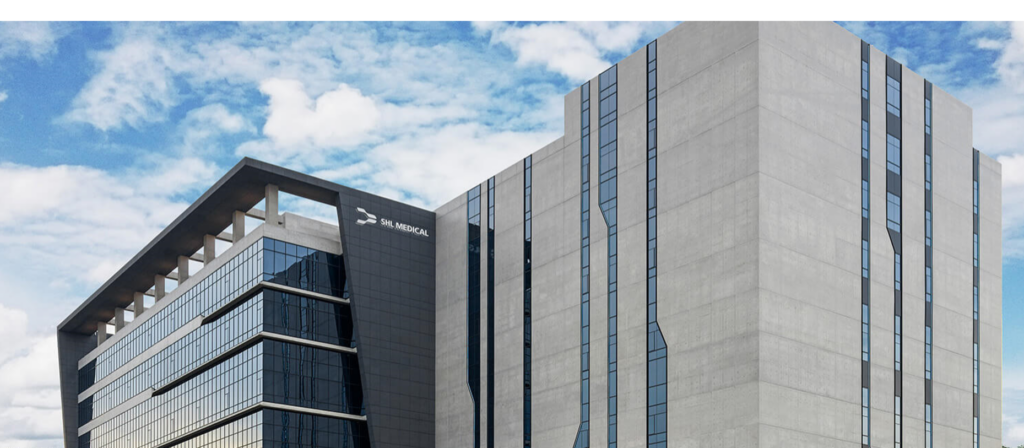
Founded with a noble ambition to improve the lives of patients reliant on self-injection solutions, SHL Medical pioneers advancements that foster patient independence and elevate their healthcare experience. Through partnerships with leading pharmaceutical and biotech companies, we deliver high-quality products and reliable platforms, empowering millions of patients annually and catalyzing positive change within the medical device and healthcare ecosystem.
What we do
At SHL Medical, we specialize in the design, development, and manufacturing of self-injection solutions, offering a comprehensive suite of services from design to build and contract manufacturing. Our portfolio includes autoinjectors, pen injectors, and innovative specialty delivery systems tailored for large-volume and high-viscosity formulations.
![]() | ![]() |
Yi-Chi Lu is a Senior Process Engineer at SHL Medical, leading efforts in production strategies and estimations for the US site factory. Ms. Lu specializes in machine capacity assessments and manufacturing process optimization. With a background in data science, process operations, and manufacturing process improvement, she previously served as a graduate research assistant, focusing on predictive modeling and data analysis. Ms. Lu holds a Master’s degree in Transportation and Highway Engineering from the University of Maryland (MD, US). | Luigi Fumagalli is a Senior Simulation Engineer at SHL Medical, leading the development of SHL’s factory simulation capabilities. He supports the company’s global expansion and factory optimization strategies with advanced plant models, manufacturing processes, and operations simulations. Prior to joining SHL Medical, Luigi accrued 5 years of experience as a Lead Manufacturing Specialist in the Aerospace sector. In this role, he focused on optimizing processes through the development of discrete event simulation models and process digitalization. Luigi holds a master’s degree in aerospace engineering from the Polytechnic University of Turin (Italy). |
Background and objective
The transition from manual processes to automation in medical device autoinjector manufacturing presents a paradigm shift with profound operational implications. Our study, utilizing Tecnomatix Plant Simulation, aims to showcase the enhancements in production efficiency, inventory control, and overall process integration achieved through automation in medical device manufacturing. With a focus on optimized operational strategy, our objective is to provide a comparative analysis and actionable insights into integrating automation to enhance operational performance across key areas in medical device production.
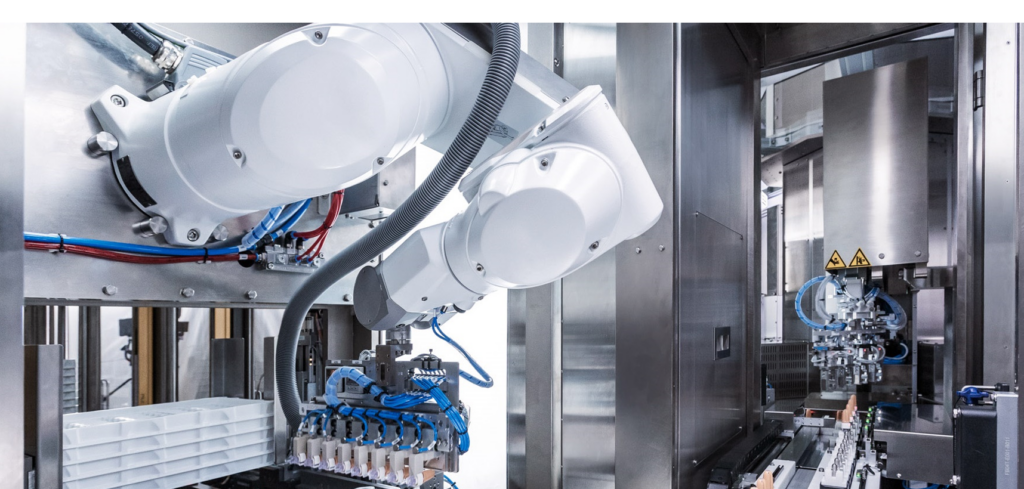
Addressing complexity challenges with Plant Simulation
Navigating the complexities of automation implementation necessitates overcoming several challenges. From data dependency and supplier collaboration to integration trials, each hurdle poses unique obstacles. However, Tecnomatix Plant Simulation emerges as a potent solution, enabling data adaptation, guiding suppliers with precise requirements, and minimizing costly trial-and-error processes.
Simulation model development
Central to our analysis is the development of a robust simulation model that encapsulates production data, layout design, operation flow, and intralogistics strategy. By meticulously crafting a virtual representation of manufacturing operations, we gain invaluable insights into the dynamics of manual and automated production stages.
Analysis of results
Our analysis delves into two key aspects: operation evaluation and performance comparison. By meticulously evaluating requirements, testing solutions, and implementing optimization adjustments, we unveil the tangible benefits of automation. From significant headcount savings to enhanced operation efficiency and intralogistics improvements, the data underscores the transformative impact of automation in autoinjector manufacturing.
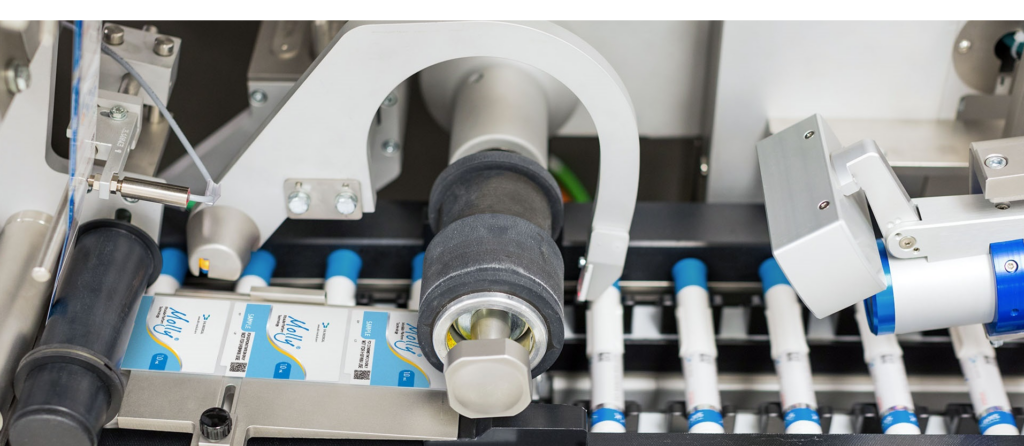
Analysis of results: Performance comparison
This segment delves into a comparative analysis between the manual and automated production stages, emphasizing the transformative changes achieved through automation and subsequent optimization adjustments. Utilizing plant simulation software as a powerful tool, the data presented below holds significance for the transition to automated systems, aiding in strategic decision-making and investment.
Benefits
- -60% headcount saving: Automation drastically reduces the need for manual handling and supervision, resulting in a substantial decrease in labor costs.
- 15 to -25% inventory level decrease: Automated systems facilitate more precise inventory control, leading to a notable reduction in excess stock and storage space requirements.
- +25% operation efficiency: Enhanced automation fosters swift material movements and efficient management, thereby enhancing overall stability and throughput.
- +25 to 35% intralogistics improvement: Optimized automated workflows streamline material handling processes, mitigating delays and boosting productivity. Furthermore, the automated storage and retrieval system (ASRS) effectively utilizes limited space, maximizing storage efficiency.
Conclusion
As we navigate the ever-evolving landscape of medical technology, automation emerges as a catalyst for innovation and efficiency. Through meticulous analysis and strategic insights, SHL Medical continues to spearhead transformative initiatives that redefine the boundaries of possibility within autoinjector manufacturing. Join us in shaping the future of healthcare delivery, one innovation at a time.
Learn more about SHL Medical:
shl-medical.com/about-shl/
shl-medical.com/products-services/drug-delivery-solutions/
shl-medical.com/sustainability/
Trademark notice
The SHL Medical logo, Molly, Madie, and Maggie wordmarks and logos are registered and/or non-registered trademarks of SHL Medical AG or its affiliates, in various jurisdictions. Other product names, logos, and brands are property of their respective owners. Use of these names, logos, and brands does not imply endorsement. This presentation contains copyrighted images and graphics of SHL Medical AG. All rights reserved.
On June 6th 2024 at the 2024 Plant Simulation User Conference, taking place at the Infinity hotel in Munich, Germany, we will delve deeper into this topic. This event, taking place right after Realize LIVE Europe, is an ideal opportunity for attendees to learn from industry experts, network with peers and explore the latest advancements in Plant Simulation software. They will experience presentations like what’s new in Plant Simulation 2404 and engaging discussions that might transform their approach to material flow simulation.
Other lectures at the 2024 Plant Simulation User Conference are for example:
User-friendly modeling and simulation of manual production lines
Empowering sustainability: Decarbonization strategies in construction process management with the integration and benefits of Plant Simulation
Driving Sustainable Transformation: BSH’s Journey Towards CO2 Reduction in Enamelling
AI and Digital Twin technology are transforming manufacturing by providing real-time guidance to workers through smartwatches