Model-based quality and the digital thread
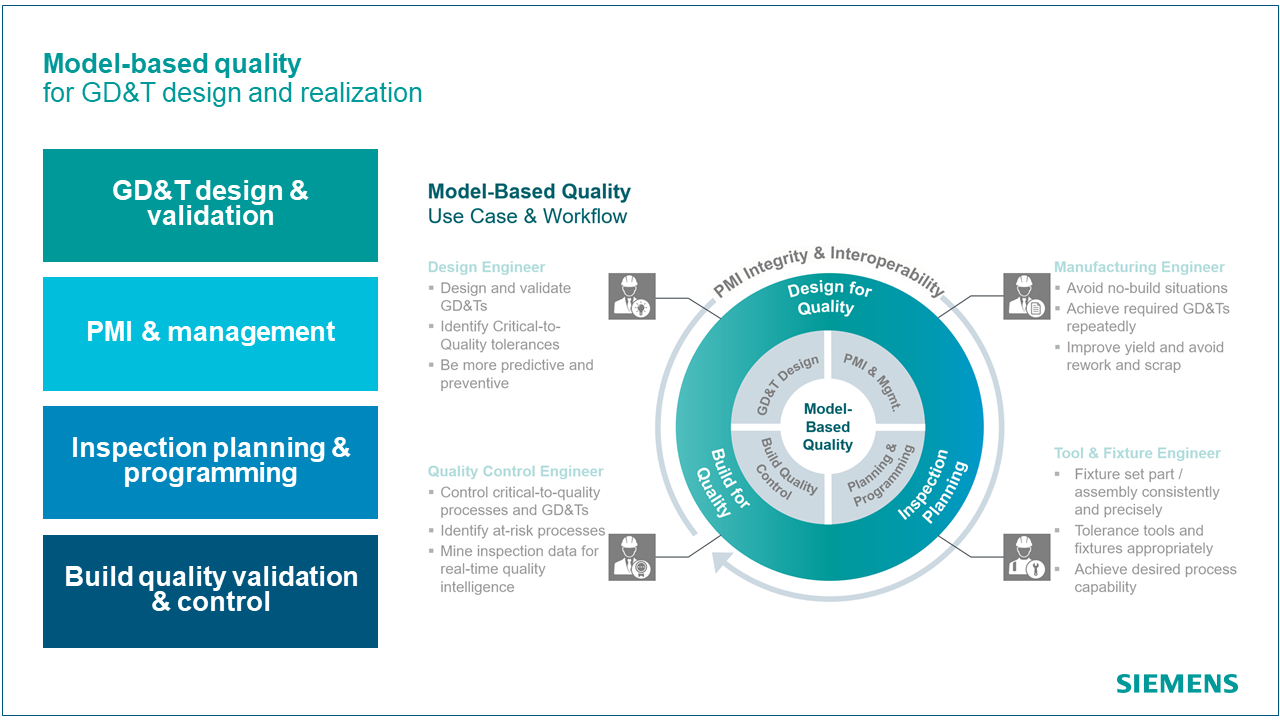
This is the fourth in a series of blogs where we discuss the requirement for detailed manufacturing engineering and operations orchestration in industry today and the potential benefits that can be realized by utilizing digital manufacturing solutions.
—–
Production excellence is achieved with a digital thread connecting product engineering through product production all the way to product utilization and performance. The continuity of this digital thread is key to manufacturing success, helping to relieve the pressures of today and establishing the required foundation for tomorrow.
As discussed in the previous blogs in the series, digital manufacturing underpins the union of manufacturing engineering and manufacturing operations and is the basis for digital continuity between innovative product designs and best-in-class performance.
Key to continuity of the digital thread from design to manufacturing, and overall production capability and performance, is manufacturing quality. Manufacturing quality starts up front in product engineering with the appropriate use of geometric dimensioning and tolerancing (GD&T), and product and manufacturing information (PMI), supporting the process of inspection planning and programming, all the way to build quality validation and control.
Model-based quality
Model-Based Quality, or MBQ, is a connected product portfolio from Siemens for GD&T design and realization. MBQ can help manufacturers digitalize their dimensional management practices and achieve profitable quality. We will use a simple example to demonstrate the complete process of GD&T design, optimization, and inspection programming using digital manufacturing tools to show a true end-to-end offering for MBQ.
The case for MBQ
Let’s start with two real world stories.
First, in 2016, after introducing a new smart phone, a major mobile device manufacturer had to recall 96% of the 3 million phones sold in the first three months. They lost over $6 billion in this process. The root cause, according to a four month long investigation, was “irregular sized batteries”. The speculation was that the phone itself did not leave room for the battery to expand, which led to a short circuit.
Second, a major car manufacturer had to recall over 9 million automobiles in 2009 and 2010 for fatal crashes due to “sticky pedals”. They lost over $2 billion in this process. The technical fix to this problem was to insert a shim with a thickness similar to a Canadian dollar coin behind one of the teeth components to reduce the excess friction that caused the issue.
Both stories have to do with a problem called manufacturing variation, also known as dimensional variation due to manufacturing. It is the deviation between the physical part or assembly and its digital design. Manufacturing variation can directly impact a product’s quality in its function, assembly process, and appearance, often causing scrap, rework, production delays, and warranty costs.
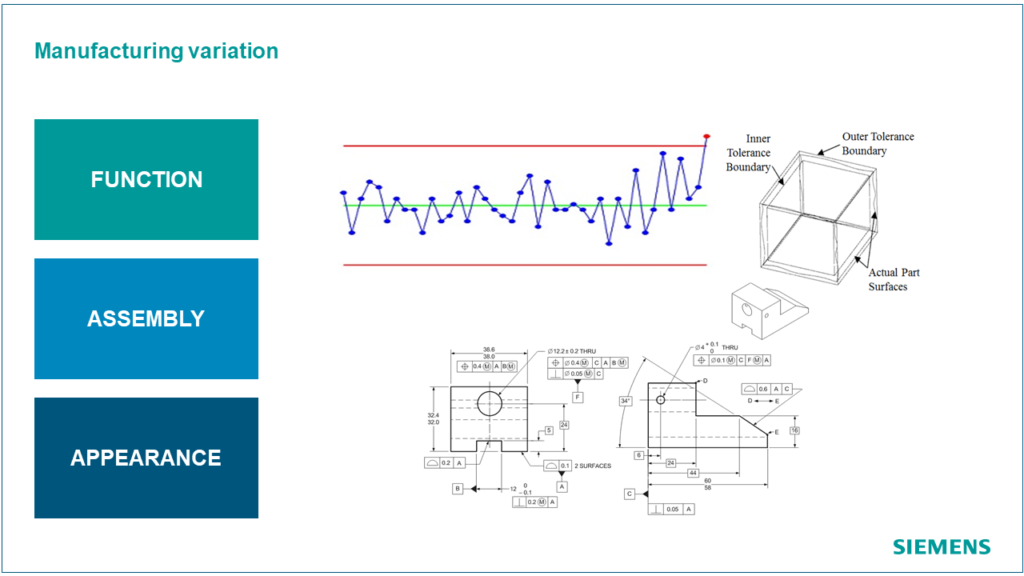
The engineering and manufacturing disciplines within an organization use GD&T to explicitly describe nominal geometry that is theoretically perfect, with allowable variations or tolerances.
Although GD&T can accurately communicate product and process requirements, use of GD&T requires some level of discipline to assure proper interpretation. Perhaps the first instance of this discipline came about during the industrial revolution over 250 years ago when Eli Whitney developed a way to communicate dimensional requirements when he invented the cotton gin and interchangeable musket components. This has evolved over time to become what is known today as dimensional management.
Dimensional management is a quality engineering discipline for GD&T design and realization, by way of optimized part tolerance design, robust assembly process planning, and controlled manufacturing variation. It spans the entire quality lifecycle, with defined processes and deliverables, to arrive at a fine balance between the cost of good quality and the cost of poor quality.
We simplify the definition of a quality lifecycle by starting with advanced product quality planning (APQP), followed by design for quality, inspection planning, build for quality, and customer quality assurance.
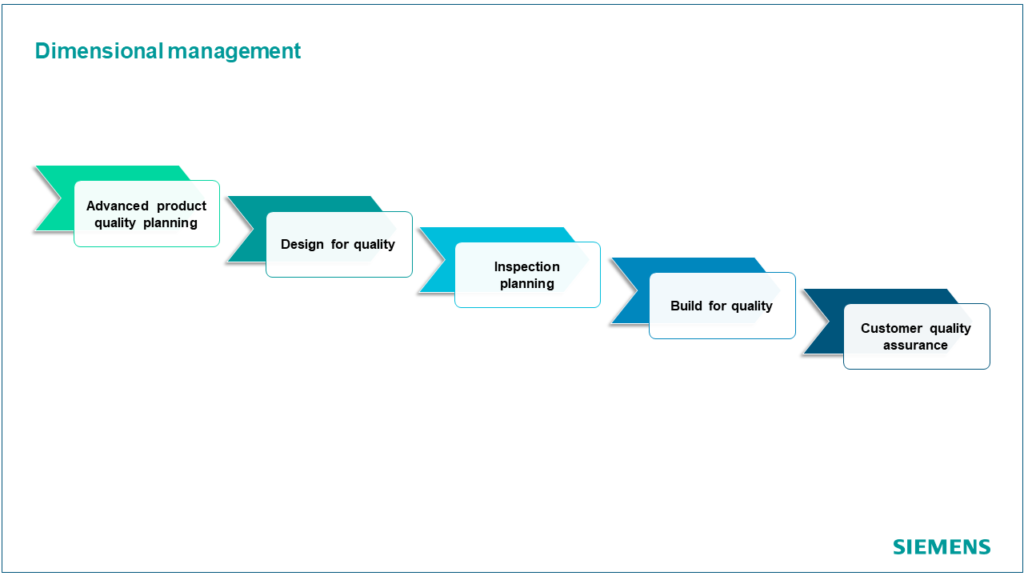
MBQ plays a significant role in this lifecycle and is the solution for digitalizing dimensional management. It is a bridge that connects design-intent and data-driven activities to deliver shop-floor quality. MBQ has multiple stakeholders including design engineers, manufacturing engineers, tooling engineers, and quality control engineers.
The MBQ workflow covers the entire design to manufacturing and inspection process, focused on 4 use cases: GD&T design and validation, PMI and management, inspection planning and programming, and build quality validation and control.
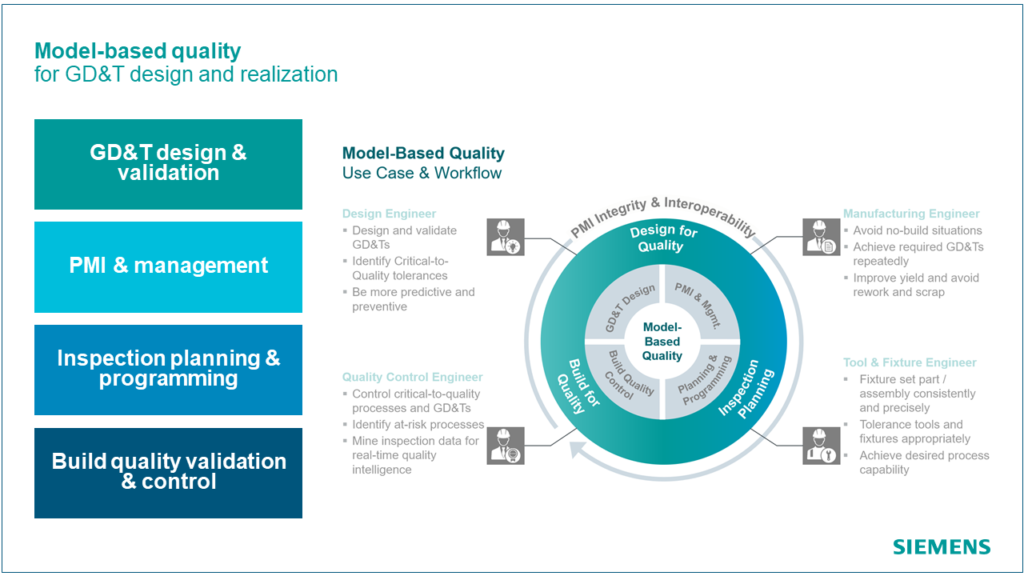
A comprehensive model-based quality solution provides a set of digital manufacturing tools for upgrading your quality processes to a dimensional management 4.0 methodology, in support of these use cases.
How MBQ works
Model-based quality first starts with the virtual product as a 3D model or a 2D drawing. Then, using digital manufacturing software and simulation, parts are virtually fabricated according to their GD&T design, assembled per their real assembly processes, and virtually produced and inspected to verify and validate part and assembly GD&Ts, identifying critical-to-quality PMIs to limit manufacturing and inspection asset costs during real production.

This is a highly iterative process between design specification and engineering verification, until the product design, including geometry and PMI, is ready for release.
Once the design is released, all downstream activities become sequential and straight forward:
- PMIs are extracted into the PLM system for lifecycle management and manufacturing and inspection planning using PMI management.
- CMM quality inspection programs are generated directly from the master model and simulated for optimization.
- Production is executed where parts are cut, fabricated, and inspected running CNC and CMM programs and assembly operations previously created from the master model.
- Measurement data of real products is collected from the shop-floor to provide real-time quality reporting, analytics and dashboarding using dimensional planning and validation tools.
The design-intent master model including CAD and PMI flows from design to downstream processes and back from as-built quality data. The difference between the two is the manufacturing variation that MBQ tackles.
Now is the time for MBQ
The truth is that many companies are already doing some level of the four use cases of model-based quality, but often in a disconnected way. With the proper MBQ solution, there is no disconnect – it breaks down the walls between the stakeholders, enables cross-value-stream communication and collaboration, and closes the quality loop. In addition, a data-managed environment connects and enriches the quality digital thread of PMI from design to realization and beyond.
Model-based quality is a complete end-to-end solution from design to manufacturing and inspection using a single software; it is effectively driven by PMI interoperability and integrity, and its deployment is scalable with a plug and play approach on the PLM digital backbone.
The bottom line? Model-based quality digitalizes dimensional management for GD&T design and validation and helps manufacturers achieve profitable quality.
—–
Blogs in this series have focused on the key values of digital manufacturing and how they can be achieved, covering topics like closed-loop manufacturing for discrete manufacturing industries and closed-loop formulation for process manufacturing industries, model-based manufacturing and model-based quality. Subsequent blogs will address topics such as the holistic digital twin and the factory of tomorrow.
—–
> You might also like these blog posts by Zvi Feuer on manufacturing and emerging technologies for 2021 and beyond.
> Learn more about our Digital Manufacturing solutions for dimensional and build quality
> You can try our Digital Manufacturing software for free.