Manufacturing 2021 – Perspectives on the Year Ahead
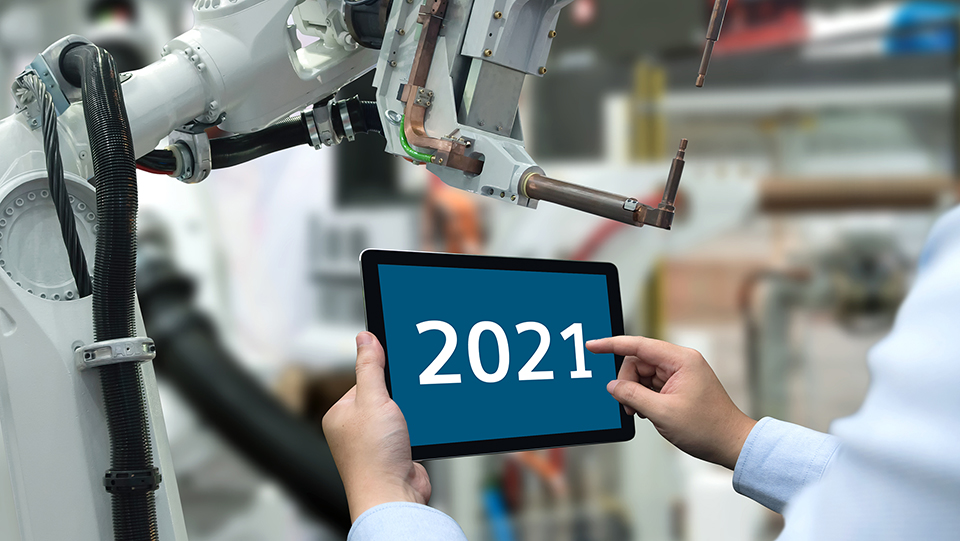
Zvi Feuer is senior vice president of Digital Manufacturing Software Solutions for Siemens Digital Industries Software. Digital Manufacturing Software develops software products to deliver world-class solutions for Manufacturing (Part & Assembly) planning, simulation, and validation and Operations (MES, Scheduling, Quality and automation).
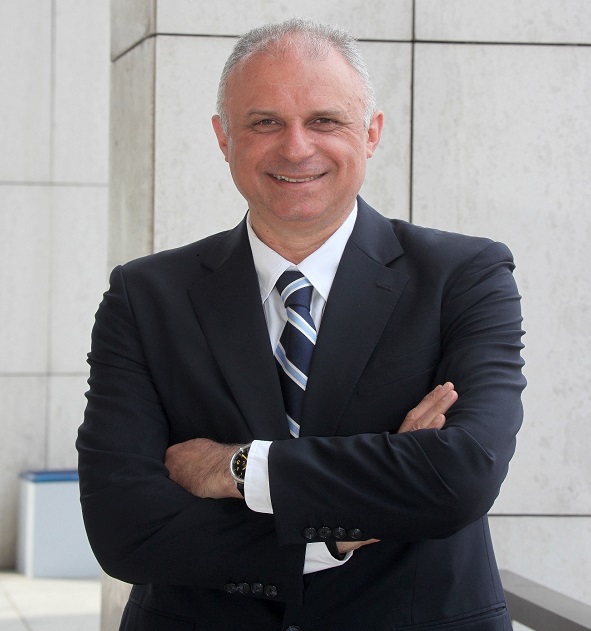
2020: A reminder of the importance of good manufacturing.
The month of December is always a traditional time to look back at the successes and challenges we faced throughout the year and a time to look to the future. This December is no different in that respect, but our view will be dominated by the stresses brought on by the COVID-19 pandemic and the lasting effects that it will have on our society.
It was a year of unique challenges in terms of health and the economy. However, there were some positive surprises as well. In 2020, the world saw, with renewed interest, just how important the manufacturing sector is. Makers in diverse industries from automotive to spirits quickly, and quite effectively, turned their manufacturing production processes from their traditional products to ventilators, personal protective equipment, sanitizers, and other much needed medical products. It is a testament to the people who work in manufacturing and the processes and skills that they have developed through the years.
When you have a good manufacturing infrastructure and you have the know how to produce high quality cars, refrigerators, or air conditioning, it is possible to shift production to products as different as ventilators and produce them in high volumes, with good quality, and at high speed. Manufacturing is something you learn; it takes time to master. If you lose it, you can lose it for many years, but if you have sustainable processes, supported by the right infrastructure and people, you gain the flexibility to effectively switch from one product to another when called upon to do so.
Getting back to work in 2021
I have been quite impressed by how quickly manufacturing is recovering. Many of the industrial countries are back to work, manufacturing high quality products while executing in a new normal. Companies are starting to leverage digitalization more and more across their business to support their operations. They are monitoring and managing processes remotely, as much as possible. Remote teams are collaborating on engineering content with people working from home or outside of the company networks. We are seeing remote expert assistance on the shop floor, people working in capsules with designated shifts and minimal overlap, and social distancing within the factory – all to ensure that we can get back to work as safely and effectively as possible.
With a vaccine on the horizon and a willingness to “embrace the new normal” there is reason for optimism for recovery, but how long that recovery takes depends on the industry and a manufacturer’s dependence on outsourcing, supply chain dynamics, and low-cost manufacturing sources and whether they have full digital transparency and traceability.
Some companies that were more reliant on Chinese manufacturing faced problems for the first few months when China was shut down. They are reconsidering their supply chains and thinking about investing more in manufacturing either in house or with suppliers closer to home. Others are still very dependent on low-cost manufacturing. This may come at a cost; when you are too reliant on low-cost manufacturing, you are not only losing the capabilities required to manufacture, but also your intellectual property. Look at what happened with the semiconductor markets in America, for example. They were the best in the world in producing chips, but today the whole semiconductor industry has been shipped out to China and Southeast Asia. This is not only a semiconductor issue. It will be interesting to see how other industries who are reliant on low-cost manufacturing react to the changing landscape in coming years.
In the automobile industry, we are seeing a slow down on traditional big investments as manufacturers take a wait and see position. They are looking at investments that are smart, easy to deploy, and deliver a fast return on investment. Many are also looking more at electric and autonomous vehicles and identifying the technologies and infrastructure needed to produce them at mass scale for sustainable growth.
In other industries like electronics, food and beverage, and cosmetics demand is high. Pharmaceutical and medical device companies are also investing heavily due to a demand for COVID medicines, treatments, and vaccines.
The key for all of these industries will be to find ways to make profitable products with good quality, while keeping their workers safe and productive. You have to ask questions like, “Can we manage operations and expenses in a stable way? Where are the opportunities to improve this stability? How can we embrace remote tools and digitalization to help us be more effective, stable, and safe?”
Digitalization is Critical
While we see digitalization concepts emerging more frequently, I recently read a report that only 5% of the manufacturing sector has really fully embarked on the road to digitalization. In the bigger companies, you will hear a lot about Industry 4.0 and digitalization. In smaller companies there is less discussion, but faster adoption. Digitalization is still far away from being fully deployed across the board, but the companies that are moving in this direction are seeing results. Digitalization is especially vital today when you need to maintain the safety of your employees.
You need to be able to monitor the behavior of employees on the shop floor to ensure safety and effectiveness. To do this, you need the ability to schedule work in a better way, so that you don’t mix between different employee groups. You want to avoid situations where one employee is affected by COVID the whole team is shut down to quarantine.
Digitalization offers companies the ability to evaluate different aspects of production flow, production in detail assembly processes, remotely manage manufacturing processes, even do virtual commissioning. It enables remote analysis to inspect whether we can insert a new machine on an existing shop floor or can we divert or change the routings. All of these things can become much easier and much smarter if you have a digitalization process.
Digitalization of the entire end-to-end manufacturing process can produce tremendous benefits for both the manufacturer and the customer. One example is in the eyeglass industry. An eyeglass company here in Israel has turned to digitalization to produce high quality, customer-specific glasses while significantly reducing the time it takes to get the order to the customer. When a customer comes into the shop to have their eyes tested, the measuring device captures that data digitality. Optometrists are provided with an app that they can use to download data from the measuring machine, attach their own notes, and scan the frame selected by the customer. If they send all of this to factory before 10am, then by 5pm the glasses can be back at the shop waiting for the customer. This process previously took 3 to 4 weeks. Digitalization brings advantages to everyone, even if you are a small shop, even if you are a startup, even in an industry that no one would imagine.
The Digital Twins
The digital twin concept provides the foundation for companies to build their digitalization strategies. A digital twin is used to model any physical product or process in order to predict performance. Using multi-physics simulation, data analytics, and machine learning capabilities, digital twins demonstrate the impact of design changes, usage scenarios, environmental conditions and other variables to reduce development time and improve the quality of the finished product or process.
At Siemens, our combined Manufacturing Engineering (MFE) and Manufacturing Operations (MOM) portfolios support the growth and long-term maintenance of several comprehensive digital twins. These include:
- A digital twin of a product represents the way the product was designed, including design elements such as mechanical, electronics, software, automation, control and wire-harness. Here it is critical to ensure that we have a smooth and easy connection to all product data.
- A digital twin of a Digital Manufacturing process represents the required processes, software solutions and assembly plan to produce and assemble the major components of a specific product.
- A digital twin of a production system/line or a production facility represents the bill of equipment and the requested layout needed to build a specific product end-to-end. In today’s world of individualization, where it is common to support a lot size of one, this production system is flexible, easy configurable and can automatically be reconfigured in the future.
- A digital twin of production in operation represents the technical package and the production management of components, subassemblies, assembly of a full-size product, quality and genealogy in action on the shop floor.
- A digital twin of a product in action represents the practice of offering products as a service. In any industry, it is becoming more and more common for the OEMs not to sell the product, but to offer it as a service. In this case, together with MindSphere and our partners, we can provide software solutions to support the service and maintenance of end products and/or production systems and their key assets.
A New Year, New Opportunities
As we put 2020 behind us and embark on a new year, we know the world has changed. 2021 will present its own challenges, but with each of those challenges will come opportunities. Embrace new ways of working. Find ways to enhance your manufacturing processes. Take care of your best resource – your people. We look forward to a new year and wish all of you a happy and productive 2021.
Comments