Thermal Design: Whose job is it anyway?
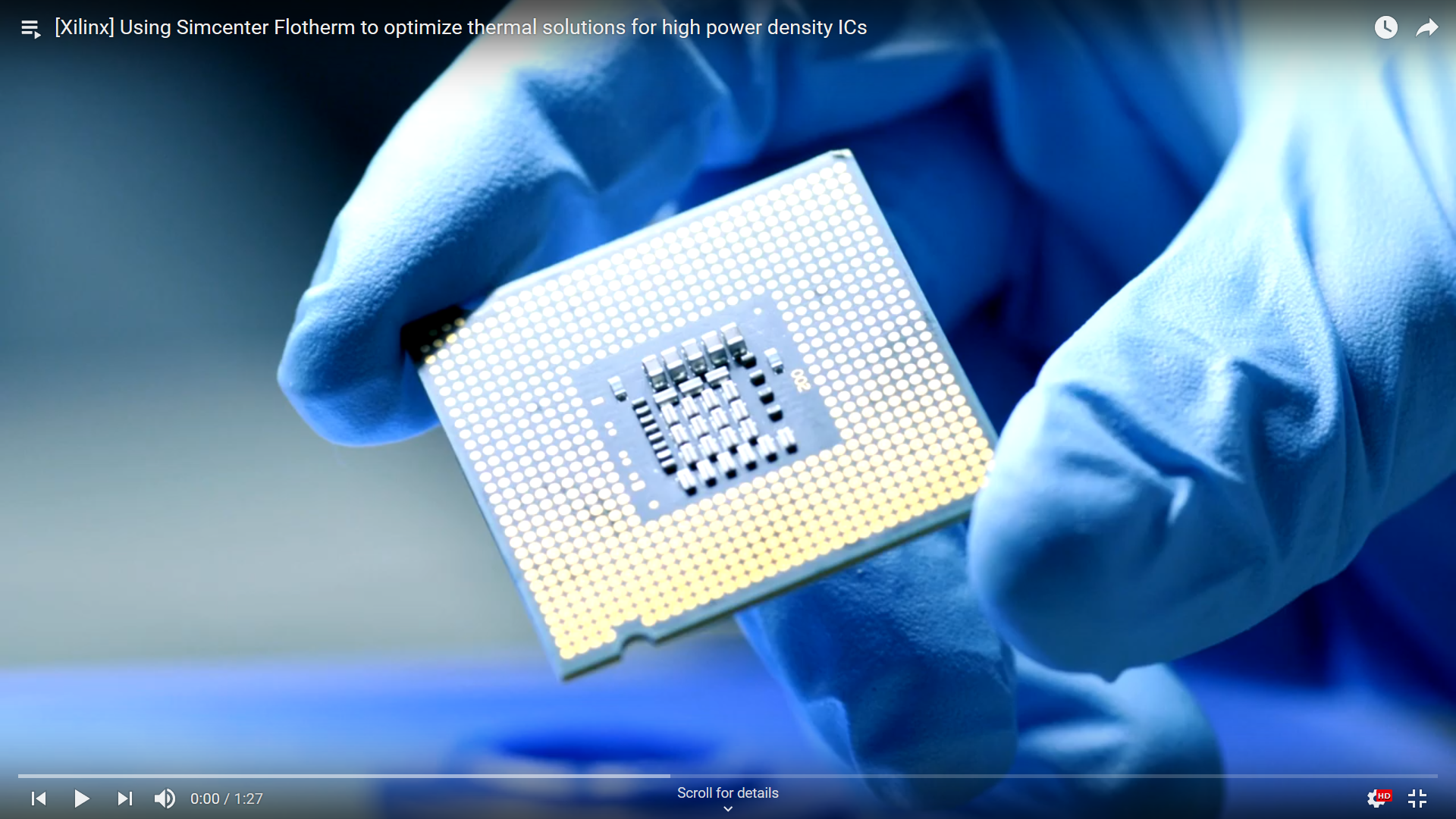
For a first blog on all things electronics cooling I thought I’d pose the question.
If there’s time at the start of a conference presentation, or a talk I’m giving on electronics cooling I like to poll the audience.
“Who thinks that thermal is an electrical problem that should be solved as part of the electrical design?”
The show of hands depends on the audience demographic, but with a mixture of mechanical and electrical engineers typically a bit less than half put their hands up.
There are a great many things electrical engineers can do to help with thermal challenges. The choice of package for a given IC is often not within their control, but the board layout, local copper distribution, and thermal vias certainly are. Circuit design can also influence power dissipation.
I then ask:
“Who thinks that thermal is a mechanical issue that should be solved as part of the mechanical design?”
Again, about half are likely to put their hands up.
Fair enough. Mechanical engineers are responsible for the integrity of the product as a whole, which includes the enclosure needed for mechanical robustness, EMI and EMC. The enclosure can be fully sealed, with fins to act as an external heatsink, or have openings and optionally fans to help drive cooling air through the internals. Mechanical engineers have a big role to play in electronics cooling.
The last question I ask is:
“Who thinks it’s a trick question?”
A few tentative hands go up.
It is a trick question because both of the above answers are correct, not in isolation, but in combination with other disciplines. As power densities continue to rise, design for steady-state operation at maximum power is often not viable. Where it is, a lighter, thinner cheaper product can be achieved by designing for specific use cases, with software-based control strategies can be introduced to cut power if temperature gets close to a critical limit.
Xilinx driving Digitalization of 5G, Accelerating Data Center Processing, Powering IoT, & Autonomous Vehicles.
Xilinx use Simcenter Flotherm to create DELPHI compact thermal models of their parts, which they make available for download from their website, helping their customers to develop the most advanced communication products. Watch Brian Philofsky, principal product marketing engineer for power and thermal at Xilinx Inc. explain how the latest digital electronics incorporated into products across a range of industries is driving the need for ever higher fidelity thermal design practices in this one minute video:
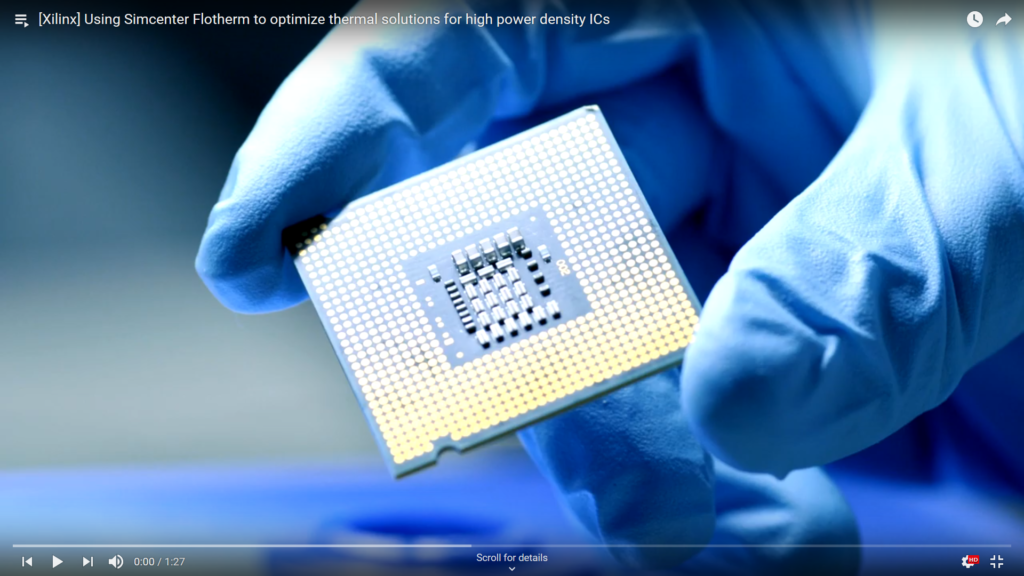
Xilinx provide an application note on “Mechanical and Thermal Design Guidelines for Lidless Flip-Chip Packages” and run thermal workshops using Simcenter Flotherm at their Xilinx Developer Forums.