Realistic shock replication: Simcenter Testlab 2306 Shock & MIMO Shock Control
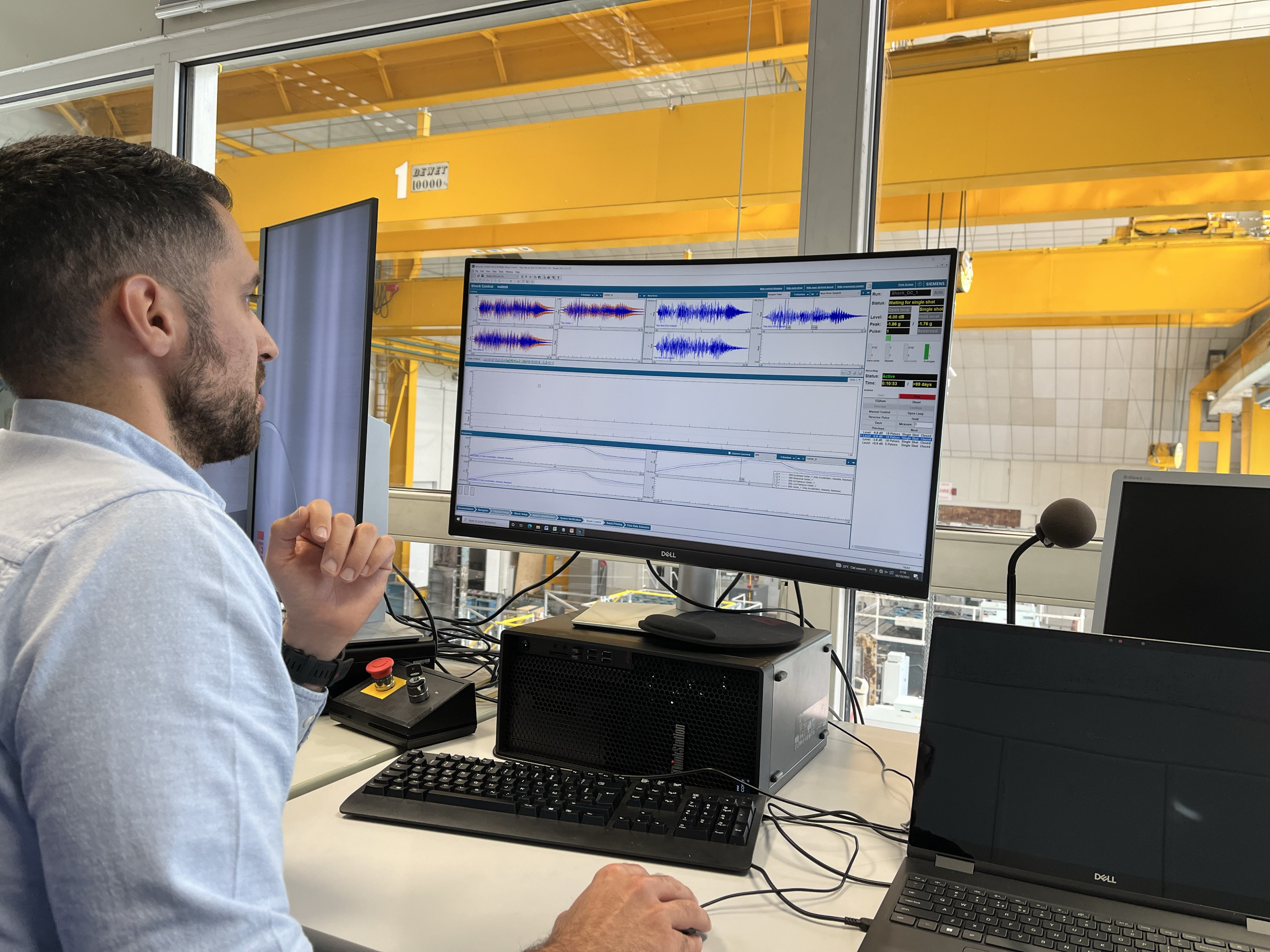
The energy sector is currently experiencing a period of strong uncertainty, with a decrease in demand for carbon-based fossil fuels. Green alternatives are emerging, and large investments are funneled toward the sector of renewable energy and nuclear power.
This evolving landscape drives radical changes in design concepts, materials, and processes that serve the larger scopes of increased efficiency and reduced costs. However, the main question that haunts the mind of the design specialists responsible for the new concepts is still the same: will my innovative system properly function in-service, surviving harsh and potentially damaging dynamic environments?
Testing gives the ultimate answer.
Shock events, such as earthquakes, drops, blast or crashes, are among the most severe dynamic environments that critical electronic components and systems need to withstand during their lifetime.
State-of-the-art solutions for dynamic environmental testing can be adopted to replicate dynamic vibrations and shock environments accurately and realistically.
The new Simcenter Testlab Dynamic Environmental Testing 2306 release leaps beyond the state-of-the-art, introducing innovative capabilities, unique functionalities and enhanced performances for setting up and ultimately run Shock & MIMO Shock control tests on shakers, starting from specifications defined as Shock Response Spectra (SRS).
SRS was born to describe seismic events
Maurice Anthony Biot (a graduate of the Catholic University of Leuven, Belgium) describes the SRS in his Ph.D. thesis (see fig. 2) from the California Institute of Technology. This is widely recognized as the first published reference to the SRS.

Figure 1 – Biot’s PhD dissertation cover page.
The SRS was initially developed by Biot to quantify and understand earthquake vibrations. It quickly became very popular in the seismic community because of its simplicity and representativeness of a seismic event. It was immediately extended to represent almost all types of shock events for several reasons, mainly because it ensures that the effects of a shock test are repeatable, and it allows defining general frequency-domain specifications and margins that can be considered for standardization. These are fundamental needs, especially for cases where measured data are not available or the designed device has multiple scopes, meaning that it needs to withstand multiple potential missions. Today, besides seismic events, the SRS is adopted for qualification of devices to different “impulsive” environments, for example
- Functional shocks
- Transportation shocks
- Crash hazard shocks
- Pyrotechnic shocks
- Blasts
All these categories (and more) fall in dedicated sections of the Mil-STD 810H, a primary reference for shock testing, under different methods (e.g. the 516.8 or the 517.3).
Depending on the specific application, other standards can be consulted for procedures and guidelines, for example, the generic standard on SRS analysis
- ISO-STD 18431– Mechanical Vibrations and shocks – Signal processing. Part 4 – Shock Response Spectrum analysis.
or the ones that are tailored to guide the test engineers through seismic qualification
- IEEE/IEC-60980: Nuclear Facilities – Electrical Equipment Important to Safety – Qualifications
- NF EN 60068-2-57 (France) – “Méthode par accélérogramme et sinusoides modulées”.
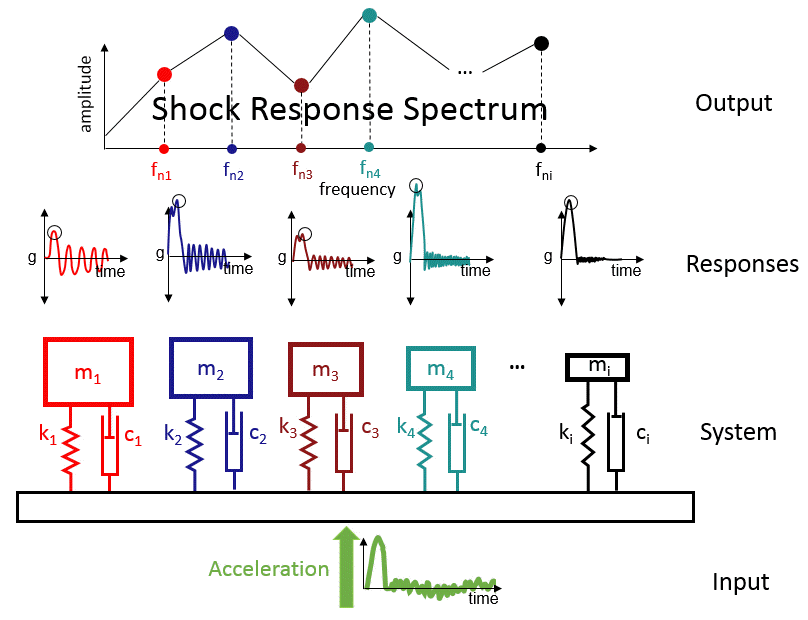
Figure 2 – the SRS model.
Simcenter Testlab release 2306 provides some new key features that enhance the capabilities of users that need to perform SRS Shock testing on shakers in the most realistic way. The enhancements in Siemens Simcenter Testlab 2306 Shock & MIMO Shock Control have the main goal of increasing the user control over the safety of the test article, the safety of the excitation hardware, and obviously the representativeness of the replicated environment.
New control modes for improved controllability, improved workflow, and on-line fine-tuning
There is no better way to control a time transient event than to directly use a time domain control algorithm! In Siemens Simcenter Testlab Shock & MIMO Shock Control release 2306 this is available as an alternative to the legacy frequency-domain “Inverse Model” control. And when a perfect drive is already recorded and available on disk, it is also possible to simply replay it using the new “Replay” mode.

Figure 3 – Multiple control modes are available in Shock & MIMO Shock Control, Simcenter Testlab Dynamic Environmental Testing release 2306.
All environmental test engineers love an automatic process that converges towards the desired reference spectra, but what they love even more is the possibility to intervene manually in case a specific situation requires it! A good example is the case where an extra over-testing margin may be requested once the iterative process is completed. Undergoing extra iterations until convergence to a new upscaled reference is certainly possible, but with the price of subjecting the article to potentially unnecessary cycles.
In Siemens Simcenter Testlab Shock & MIMO Shock Control release 2306 the test engineer can fine-tune the drives during iterative control or replay easily and safely with the new Online Interaction Manual Control.

Figure 4 – Fine tune manually your drives and add margin to the SRS response thanks to the new Manual Control online interaction. Available in Simcenter Testlab Shock & MIMO Shock Control as of the release 2306.
No under-testing at all costs!
In order to avoid the potential risk of unexpected failure in-service, a safety critical aspect is to avoid under-testing at all costs. In Siemens Simcenter Testlab Shock & MIMO Shock Control this can be done by defining an Undertesting Avoidance Factor (UAF) per frequency line during the Time Synthesis.
The UAF does not simply scale the generated shock component in safety-critical frequency band of interest. It is fully included in the generation of the desired shock events and taken into account in the refinement of the synthesis.
Figure 5 – Do you need to converge to an SRS with some under-testing margin in specific frequency bands? As of Simcenter Testlab 2306 you can use the new Undertesting Avoidance Factor in the shock synthesis.
Optimizing the shaker stroke and the shaker residual displacement and velocity
Next to the safety of the device under test, it is critical to protect the often-expensive excitation hardware as well. Simcenter Testlab Shock & MIMO Shock Control release 2306 provides the new component type “Damped sine – Envelope” that guarantees a zero displacement and velocity at the end of the shock and minimizes the shaker stroke.
From single-axis to multi-axis shock testing
Have a look at figure 6. This figure reports 30s from the time recordings of an earthquake in El-Centro (California), EW: East-West, NS: North-South and UD: Up-Down, together with the natural cross-correlation that exists between the pairs of events.
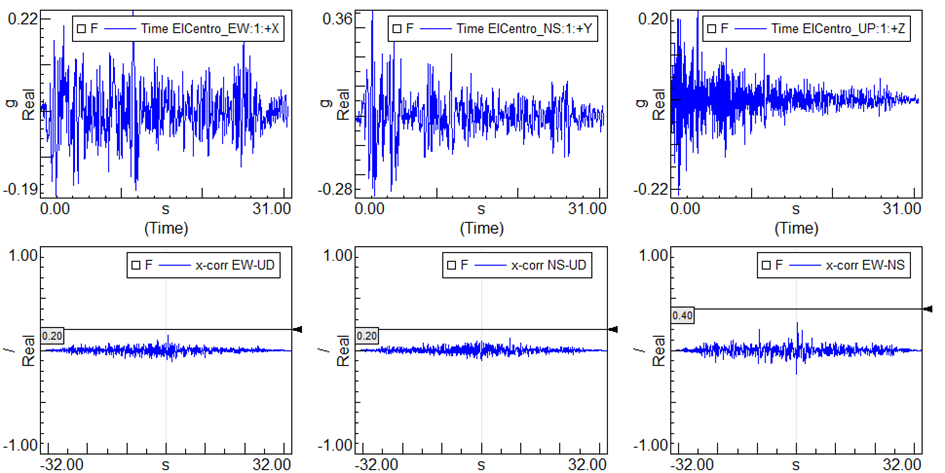
Figure 6 – 30s-segment from an earthquake recorded in El-Centro California
The most representative replication of this specific earthquake would require exactly the three recorded events to be replicated simultaneously, which would automatically return the cross-correlation that naturally exists between the waveforms. Clearly, this cannot be generalized to cover all the possible seismic events and, as explained earlier, SRS is used instead to define test specifications. This example highlights important aspects that may be overlooked when searching for the optimal solution for shock control:
- The possibility, if needed, to replicate available recorded shocks is extremely valuable.
- A simultaneous multi-axis (three-axis) control would allow for the most representative test.
- In theory there are (more than!) infinite shocks that can be synthetized from the multiple SRS specifications. A synthesis procedure that guides the user in obtaining a set of shocks that fulfills a specified decorrelation is certainly an extra step towards a more realistic replication.
Simcenter Testlab Shock & MIMO Shock control fulfills all these needs in the latest Simcenter Testlab release 2306 and helps the user throughout the entire workflow, from setup to reporting. With maximum efficiency. The new release not only features a new safe and reliable full MIMO control algorithm starting from SRS specifications (Figure 7), but it also helps the user in defining a multi-axis shock set starting from multiple SRS. The software now guides the user in finding an optimal set of shocks that fulfills a specific max cross-correlation requirement and maximum SRS error (Figure 8). All within just few clicks.
Figure 7 – Shock & MIMO Shock Control reference SRS and shock synthesis. Acceleration waveforms and normalized cross-correlation can be evaluated in the Time synthesis tab.
Figure 8 – Need for a set of shocks with a specified maximum de-correlation? You don’t need to spend time in endless iterations outside your shock control solution. The new Simcenter Testlab Shock & MIMO Shock Control features an automated optimized decorrelation tool that will help you!
Of course, not every user has a multi-axis shaking table available…..No problem. This process can be also seen as an enhancement of the shock synthesis for single-axis shock control. Synthetizing your shock from a multi-axis SRS specification and adopting it for a single-axis test can be done in just few steps with Simcenter Testlab Shock & MIMO Shock Control!
Now it’s time to show some results! Figure 9 and 10 shows the result of a synthesis carried out within Simcenter Shock & MIMO Shock Control starting from a set of measured reference SRS derived from the waveforms of Figure 5. From the figure, it is possible to see how the software can replicate accurately and reliably, not only the requested SRS within the specified tolerances but also the shape of the measured shocks and the cross-correlation that naturally exists between each pair!
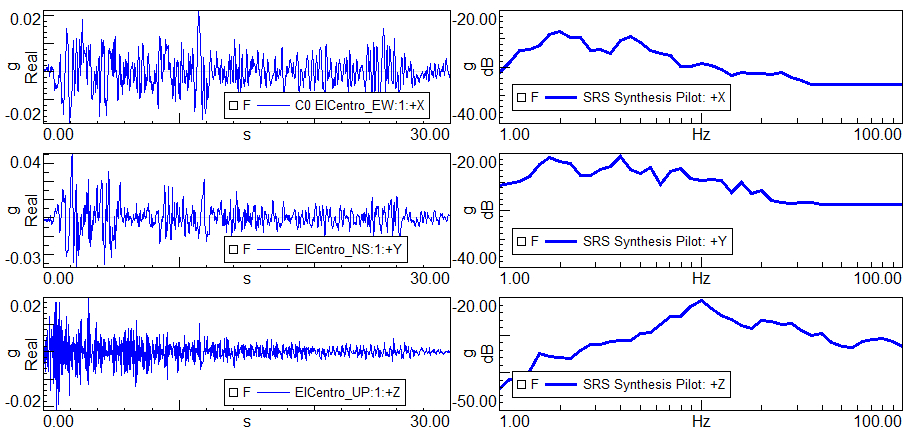
Figure 9 – Multi-axis shock synthesis from SRS
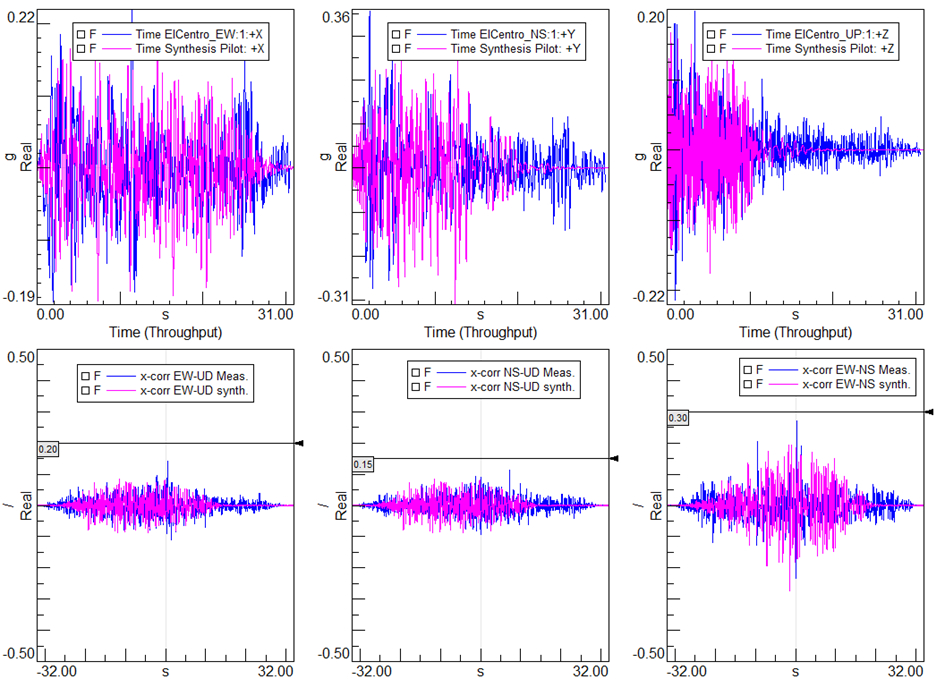
Figure 10 -(top) comparison between measured seismic shocks and synthetized shocks starting from SRS and between measured and synthetized cross-correlation (bottom)
Want to know more?
- Webpage – Vibration control testing
- Video – MIL-STD-810H Method 516.8
- Article Shock Response Spectrum (SRS)
- Video – Shock Response Spectrum
- Blog – Simcenter Testlab 2306