The significance of systems simulation in aerospace problem-solving and breakthrough achievements

As the evolution of aircraft designs continues, aerospace engineers face an ongoing challenge to discover more efficient methods of powering and cooling down onboard systems. To address this challenge, leveraging cutting-edge systems simulation in aerospace emerges as the most effective approach to model and explore innovative solutions.
Among the various onboard systems, the Environmental Control System (ECS) stands out as one of the largest consumers of secondary power in modern civil transport aircraft. To substantially reduce fuel consumption in the ECS, an Engine-Mounted Cabin Compression System (EMC2S) presents a promising solution.
As ultra-modern jets and other high-performance airborne systems continue to advance, engineers face challenges in operating their onboard electronics. The increasing electrification of aircraft has led to these systems generating a significant amount of heat, which can negatively impact the efficiency and reliability of electronic components if not properly regulated. Traditional cooling techniques like air cooling are inadequate for these advanced electronics due to their compact design and high heat dissipation. To address this issue, engineers have developed an Airborne Liquid Cooling System (ALCS) as an efficient, reliable, and lightweight cooling solution
By utilizing systems simulation in aerospace, engineers can assess the benefits of these innovative technologies and evaluate their potential performance when integrated into an aircraft. Only through comparing results and gaining a better understanding of their capabilities, engineers can make well-informed decisions regarding their implementation.
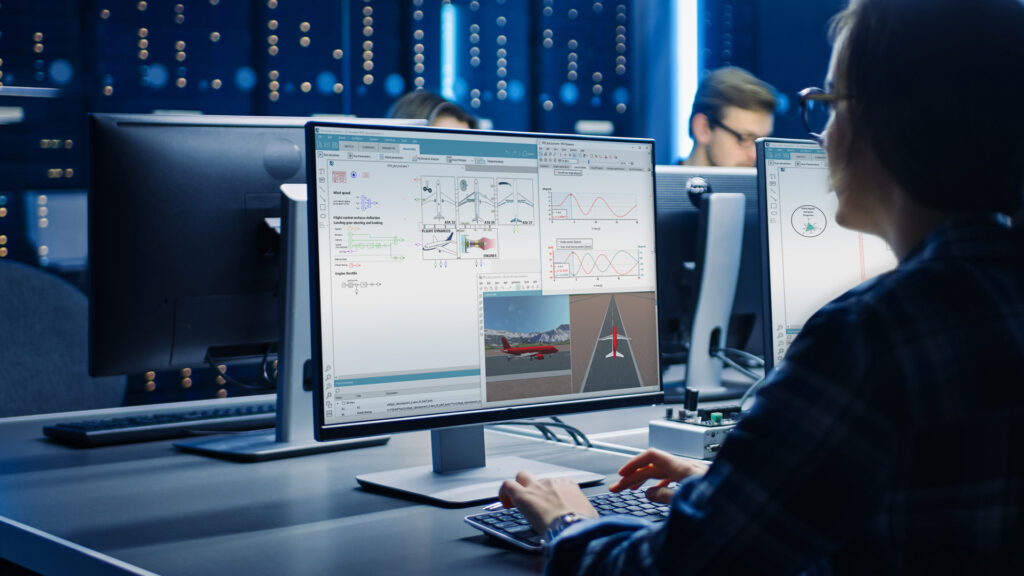
Case study #1: Potential benefits of the Engine-Mounted Cabin Compression System
An unprecedented analysis presented at the ASME Turbo Expo 2023: Turbomachinery Technical Conference and Exposition highlights the potential benefits of the Engine-Mounted Cabin Compression System. As part of the analysis, the researchers modeled the integration of an EMC2S with the engine, airframe, and environmental control system (ECS) of a single-aisle short-to-medium range aircraft thanks to systems simulation capabilities.
The key advantage of the EMC2S is that it uses a dedicated mechanically-driven centrifugal compressor, rather than bleeding high-pressure air directly from the engines. This allows the compressor speed to be controlled independently, optimizing its efficiency.
The analysis was carried out using Simcenter systems simulation, which seamlessly integrated the EMC2S with the engine, airframe, and ECS components. This comprehensive and integrated modeling approach enabled the researchers to evaluate the performance of EMC2S across a typical flight profile, demonstrating how systems simulation in aerospace aids engineers in exploring innovative solutions, ensuring robustness and reliability, streamlining performance comparison, and effectively addressing aerospace problems to achieve breakthroughs in analysis.
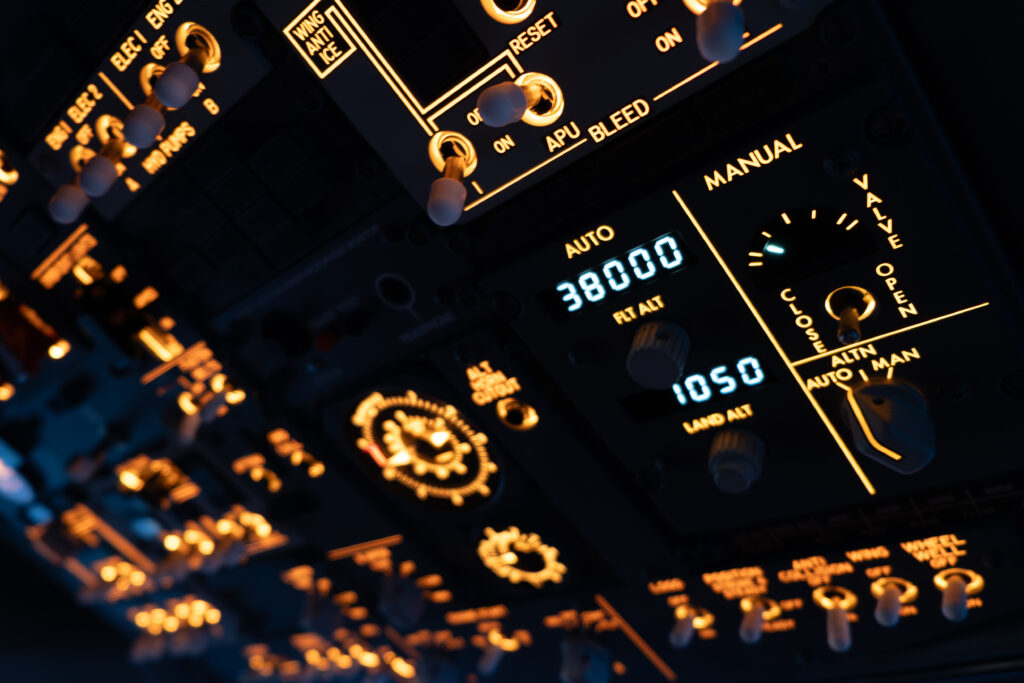
Ensuring robustness and reliability through systems simulation in aerospace
When it comes to exploring the potential of innovative solutions like the EMC2S technology, the researchers also conducted extensive analysis to investigate the behavior of the system in various off-nominal scenarios, such as extreme temperature conditions or component failures, making systems simulation in aerospace the ideal approach for such investigations.
Understanding how the EMC2S performs in these situations is critical to ensure its robustness and reliability in real-world applications. For this scenario, a mechatronic systems simulation platform allows design engineers to virtually assess and optimize the systems’ performance. This can enhance overall systems engineering productivity throughout the entire research and development process, from the initial stages to the final performance validation and controls calibration. This comprehensive approach will ensure that the EMC2S is thoroughly evaluated and optimized, leading to increased efficiency and effectiveness in the engineering processes involved.
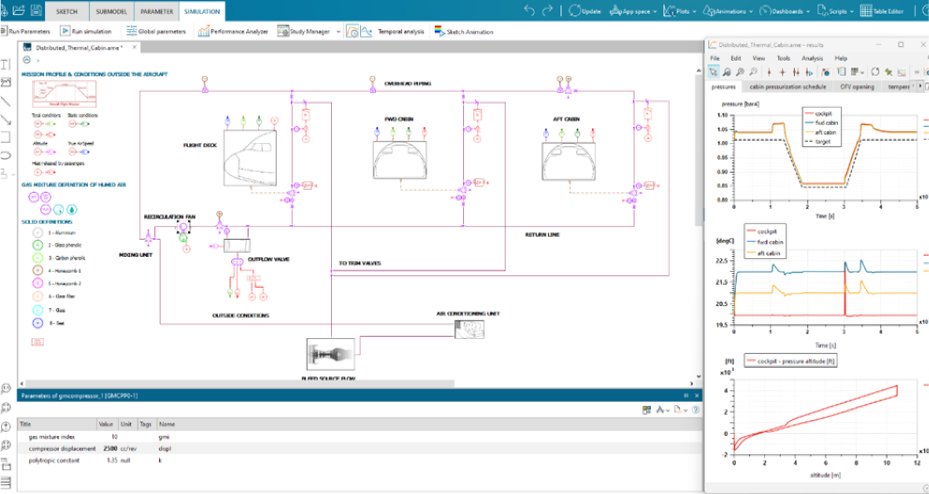
and the cockpit
Streamlining performance while integrating innovative technology
When researchers aim to assess the performance of the EMC2S against a conventional two-port bleed pneumatic system, they require a streamlined platform for systems simulation in aerospace. This platform encompasses a diverse array of capabilities and tools, facilitating efficient analysis and evaluation of the system’s behavior in comparison to other modeled systems. With access to such a platform, researchers can save valuable time and effort, ultimately enhancing reliability and significance.
Case study#2: Potential benefits of the Airborne Liquid Cooling System
The second case discussed in this blog focuses on the vital aspect of cooling. The foundation of this case is the research paper titled ”Modeling Simulation and Temperature Control on Thermal Characteristics of Airborne Liquid Cooling System”
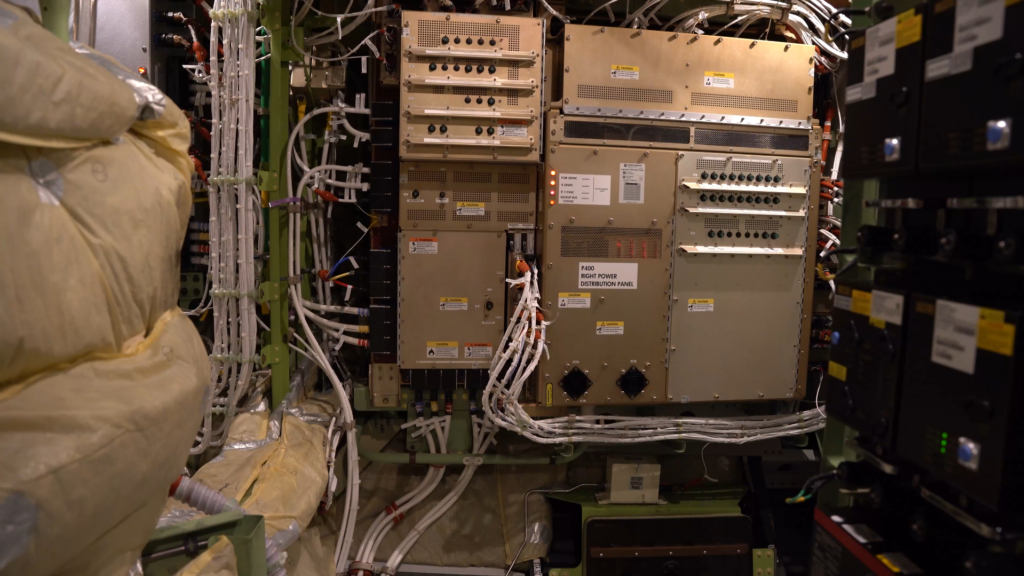
The paper investigates the thermal properties of a liquid cooling system specifically designed for aircraft electronic equipment. By employing model simulation, the study examines these properties under different temperature conditions. Notably, it establishes a numerical calculation model for assessing heat transfer in the system’s main components and constructs simulation models of these components using Simcenter systems simulation software.
Modeling and Analysis of Thermal Characteristics
The researchers utilized systems simulation in aerospace to study and model the thermal characteristics of essential components in an airborne liquid cooling system. By focusing on components like the liquid storage tank, gear pump, heat exchanger, cold plate, and pipelines, they gained valuable insights into their thermal behavior. Incorporating factors such as convection, radiation, pressure drops, and fluid properties, the researchers developed mathematical models to accurately represent heat transfer. This enabled a comprehensive understanding of how these components functioned thermally.
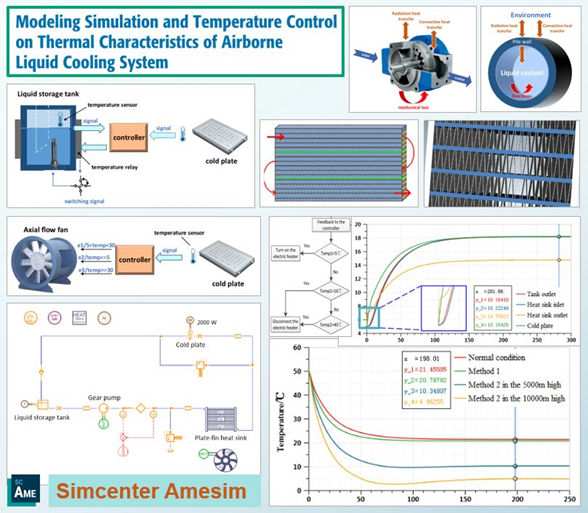
Validation and Optimization of Temperature Control Methods
To assess the system’s dynamic thermal performance under various operating conditions, the researchers built a simulation model of the entire liquid cooling system using Simcenter systems simulation multidisciplinary software. Through simulations, they obtained temperature profiles of key components, such as the cold plate, across a wide range of temperature conditions. This validation process ensured that the system could effectively maintain the desired temperature range of 5-25°C for the cold plate.
Furthermore, the researchers compared different temperature control methods using systems simulation in aerospace. They explored strategies like using an electric heater at low temperatures and increasing fan speed or opening a ram air port at high temperatures. Through these simulations, the researchers quantified the effectiveness of each control strategy. This valuable information can aid in optimizing the engineering design of airborne liquid cooling systems, enhancing their overall performance and reliability.
Addressing aerospace problems and achieving breakthroughs
The utilization of aerospace-specific solutions like Simcenter systems simulation can lead to significant breakthroughs in analysis.
When it comes to EMC2S systems simulation in aerospace can help address result in various positive outcomes, such as reduced block fuel consumption and improved performance metrics, considering thermal management is a key metric to ensure the viability of your design. The specific conclusions may vary depending on the engine and aircraft’s characteristics but the vital role of systems simulation in aerospace remains unchanged.
On the other hand, the use of systems simulation in aerospace connected with the study of airborne liquid cooling systems has proven to be a powerful tool for engineers and researchers. By comprehensively modeling and analyzing the thermal characteristics of the components, valuable insights are gained to support the engineering design and optimization of these systems. The ability to validate temperature control strategy through simulations provides a practical approach to enhance the performance and efficiency of such systems.
As the aerospace industry continues to seek ways to reduce emissions and operating costs, innovative solutions like the engine-mounted compression system or supplemental cooling systems may play a key role in the future of aircraft environmental control. Addressing these challenges through solutions that drive digital transformation in aerospace will empower engineers as they move forward.
The significance of the Environmental Control System (ECS) as a major consumer of secondary power underscores the importance of advancements in ECS simulation capabilities. Stay tuned for the upcoming 2504 release of Simcenter Systems Simulation, where groundbreaking advancements in ECS simulation capabilities are set to revolutionize the aerospace industry.