Sustainable aviation: adding hydrogen propulsion to jet engine designs
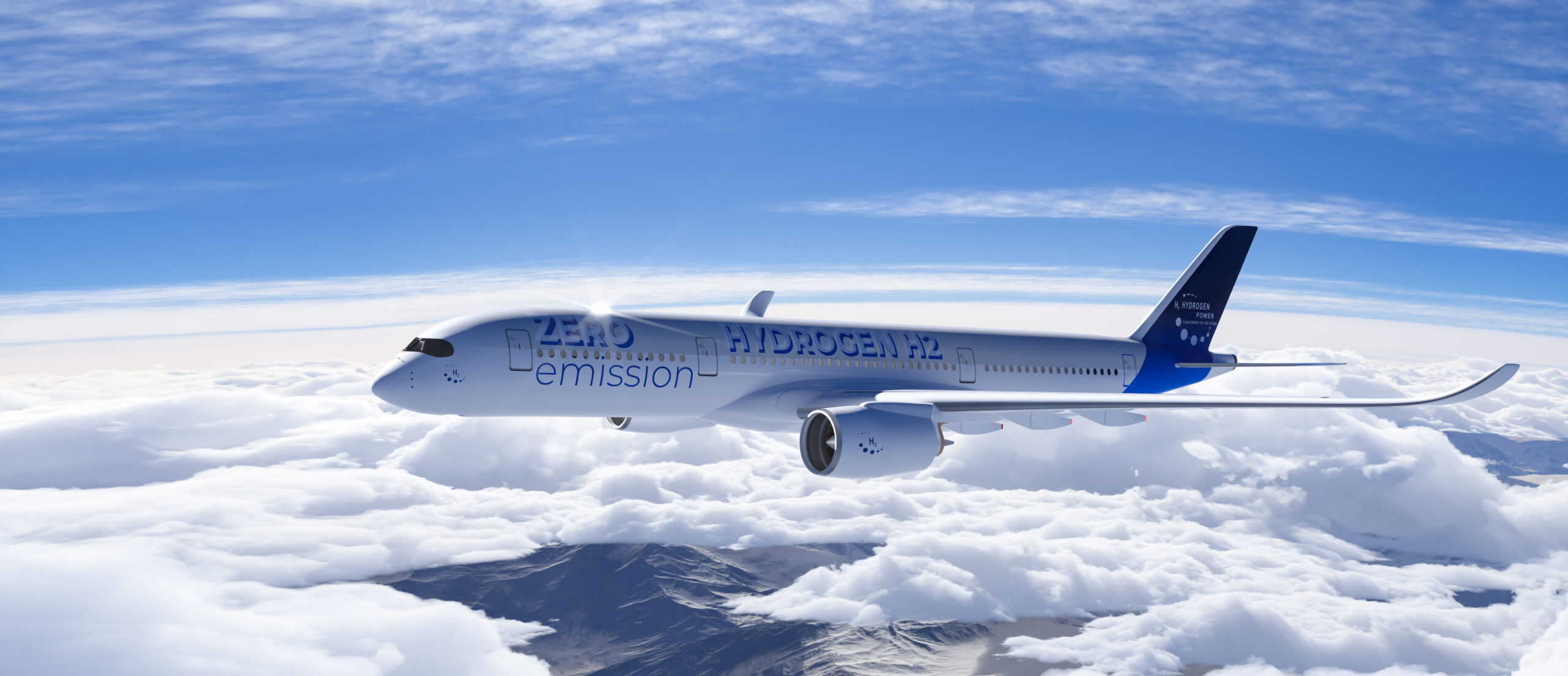
Aviation is committed to reaching net zero by 2050. Analysts believe this target is achievable and airlines are developing ways to realize this goal. While truly carbon neutral air travel is only possible with battery-powered aircraft and hydrogen fuel cells, the most promising way for airlines to reduce their emissions is by improving the fuel efficiency of their fleets and moving to sustainable aviation fuels (SAF) such as biofuel or hydrogen. Hydrogen-powered aviation offers the fastest route to Net Zero and green hydrogen is the most sustainable option because it is produced without generating CO2.
Companies are therefore evaluating hydrogen-powered propulsion but designing jet engines is complicated and introducing hydrogen adds more complexity for several reasons.
Hydrogen burns with a flame speed that is ten times faster than with kerosene so there is a risk of flashbacks that would destroy the combustor. This means that hydrogen-powered jet engines need new mixing and injection techniques.
Hydrogen combustion does not create CO2 but there are other emissions: nitrogen oxide gases, or NOx, which contribute to atmospheric pollution, acid rain and smog. The design of the engine must minimize these.
The increased heat in the jet presents challenges. Hydrogen-powered jet engines need new flame positions and thermo-acoustics and this will affect the service life of the engines.
Hydrogen combustion creates higher thermal loads so designers need to develop new cooling techniques for hydrogen-powered engines.
B&B AGEMA, specialists in dry no NOx hydrogen combustion technologies, are working on simulations for a revolutionary transitional jet engine that can use two fuels: kerosene or hydrogen. This would allow airlines to introduce hydrogen as fuel and reduce their CO2 and NOx emissions without replacing entire fleets of planes. The design uses a combined burner that runs on hydrogen or kerosene so it is more challenging to design than a combustor that only uses one fuel. B&B AGEMA’s design objectives are to create an aero engine that can:
- Burn hydrogen and kerosene
- Switch flexibly between both fuels without modification in the combustion
- Achieve low NOx
- Reduce CO2 and NOx and pollutants
- Provide a transition technology to hydrogen-powered flight
The design must also integrate with the engines and the other systems within the aircraft.
Fundamentals of hydrogen combustion with MicroMix
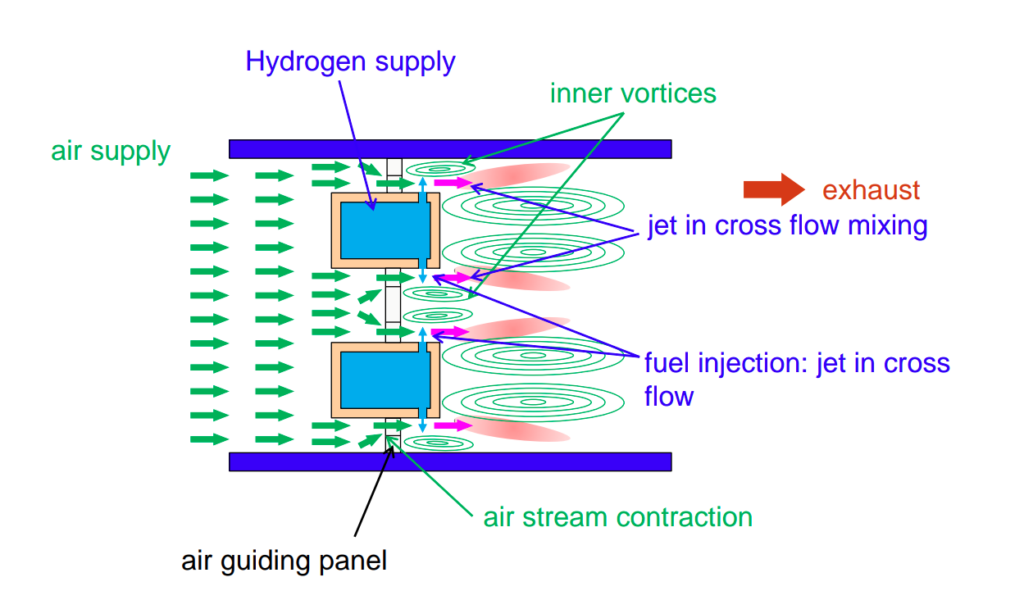
Key to B&B AGEMA’s design is their MicroMix (MMx) combustor. The MicroMix combustor can be integrated into a conventional kerosene combustor so that the engine can burn kerosene or 100% hydrogen. This revolutionary design meets the two objectives of managing the temperatures and the emissions in hydrogen combustion. It has already won an energy efficiency award in Germany.
MicroMix is a dry low NOx solution which doesn’t require steam or water or a catalytic NOx reduction for cooling. This is significant because it makes a difference to the cost of building the engine and the commercial attractiveness of the design.
MMx works on the principle of mixing hydrogen with air using a jet in cross flow (JICF) principle. Air is drawn in through single air gates with the fuel injection behind and hydrogen is injected vertically into the cross flow. The design moves the air through two recirculation zones to stabilize the flames and uses fast mixing to achieve small flames and low emissions of NOx.
Bearing in mind the risks of flashbacks, the micro-flames need a very precise design and geometric tuning in order to be safe.
Because hydrogen burns at higher temperatures than kerosene the secondary air flows within the combustor are critical to prevent the ingestion of hot gases, so modelling these air flows was a crucial part of the design.
B&B AGEMA wanted to integrate MicroMix with conventional kerosene combustion engines that use the TAPS (Twin Annular Premixing Swirl-up) concept but they did not know if the jet would need a rich air/fuel mix or a relatively weak mix.
The designers needed to optimize the design and performance of the gas turbines in order to minimize the fuel consumption of the engine.
Simulations of four designs
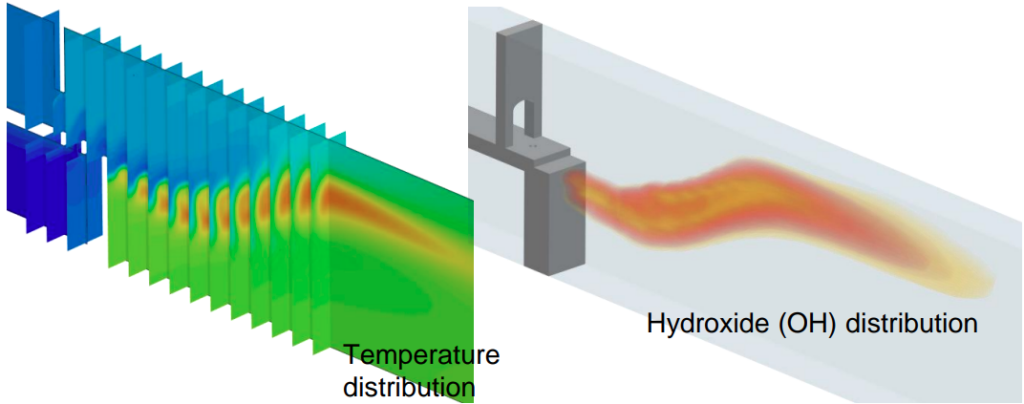
B&B AGEMA used simulations to model the design, understand the level of emissions it would produce and find out if it would be stable in operation. They modelled several configurations for the airgate and the air inlets.
- A model using MicroMix with hydrogen combustion technology and a radially-staged combustor. Here MicroMix replaces the main burner. The researchers needed to understand the requirements, advantages and disadvantages of this approach.
- A model where MicroMix is added to a kerosene reverse flow combustor. With this model, the designers wanted to find out if there would be sufficient air for the engine to function because air is also needed for cooling, and burning kerosene creates hot gases that can cause “coking”.
- A design with a liquid jet cross-flow injection. This allowed the maximum space within the combustion chamber but the principle of the diffusion flame might not be viable, and this approach would require an atomization process.
- A design using the TAPS principle with a central pilot flame. This model uses a central pilot flame with an integrated MicroMix ring and a radial swirl of the burner. Kerosene is injected as with TAPS. This is a proven technology that is scalable to different combustor sizes and allows plenty of air for hydrogen combustion, but it was difficult to predict the effect of the swirl on the MicroMix.
Concept design and simulation for a hydrogen-propelled jet engine
B&B AGEMA’s researchers used Simcenter from Siemens Digital Industries Software to study the phenomena associated with hydrogen combustion and compute the fuel consumption and the performance of the engine under different conditions.
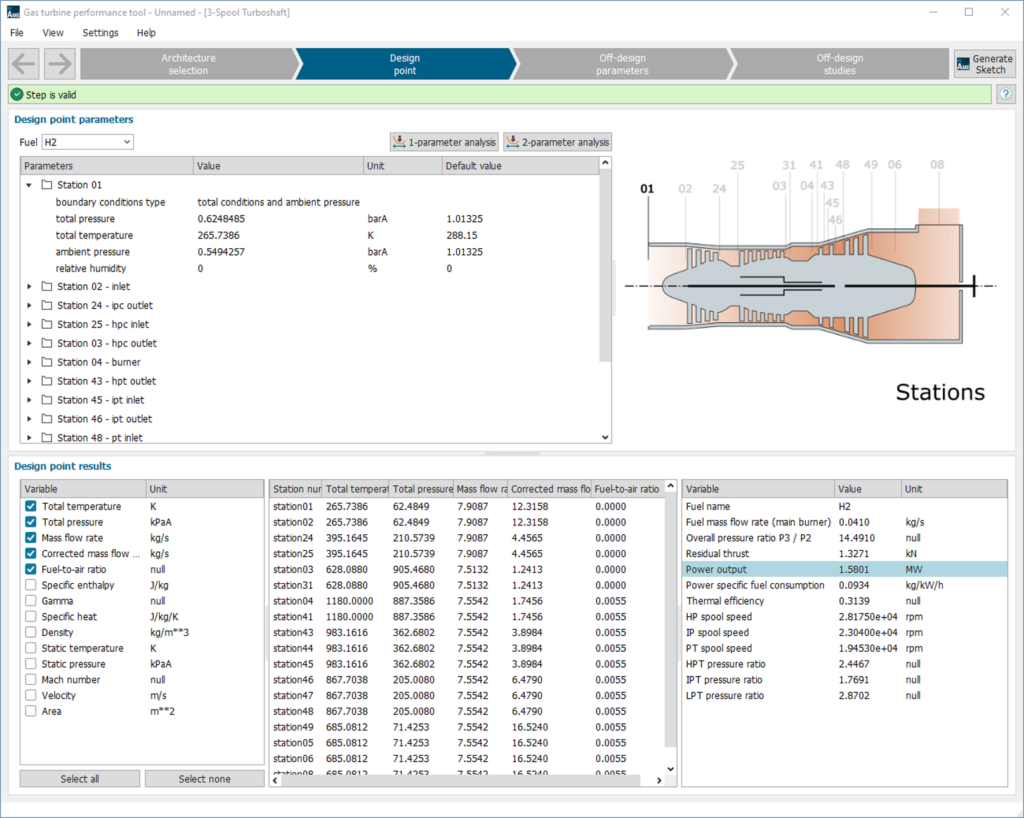
They simulated the periodic sector model of the combustor using LES and the more state-of-the-art RANS simulations. Engine manufacturers can use the gas turbine performance tools in Amesim to work on the engine configuration parameters and automatically generate transient models of the thermo-dynamics. These can be integrated with the system and its controls.
B&B AGEMA designed the model in sections and this work led to a design for a complete virtual integrated engine.
They learned a lot from the multi-component gas model and their model of NOx emissions and conjugate heat transfer. The models soon showed precise predictions of the flame temperatures, emissions, efficiency and stability of the MicroMix combustion.
It is worth noting that the new GPU capabilities in Simcenter made the solver 45% faster, 37% cheaper and brought an energy saving of 60%.
Want to learn more?
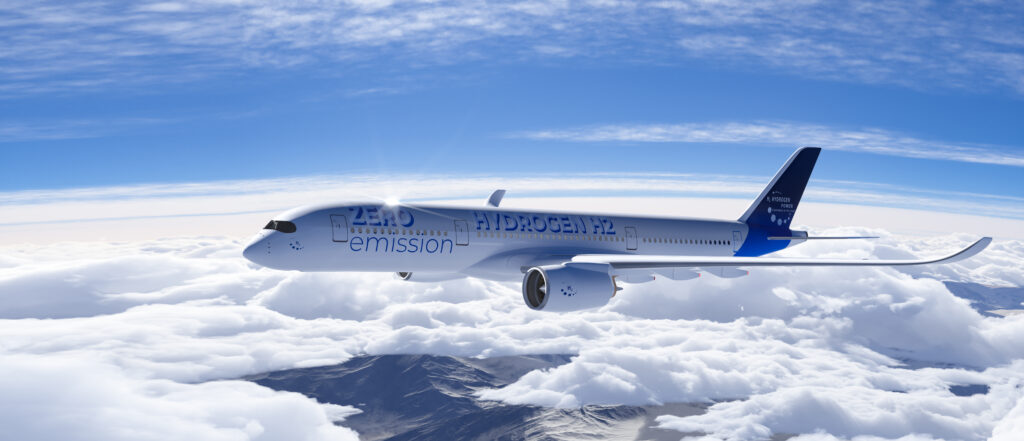
Webinar
Using simulation to revolutionize hydrogen-powered aircraft design