Spurious peaks begone! A unique method to smooth measured FRFs for Frequency-based Substructuring
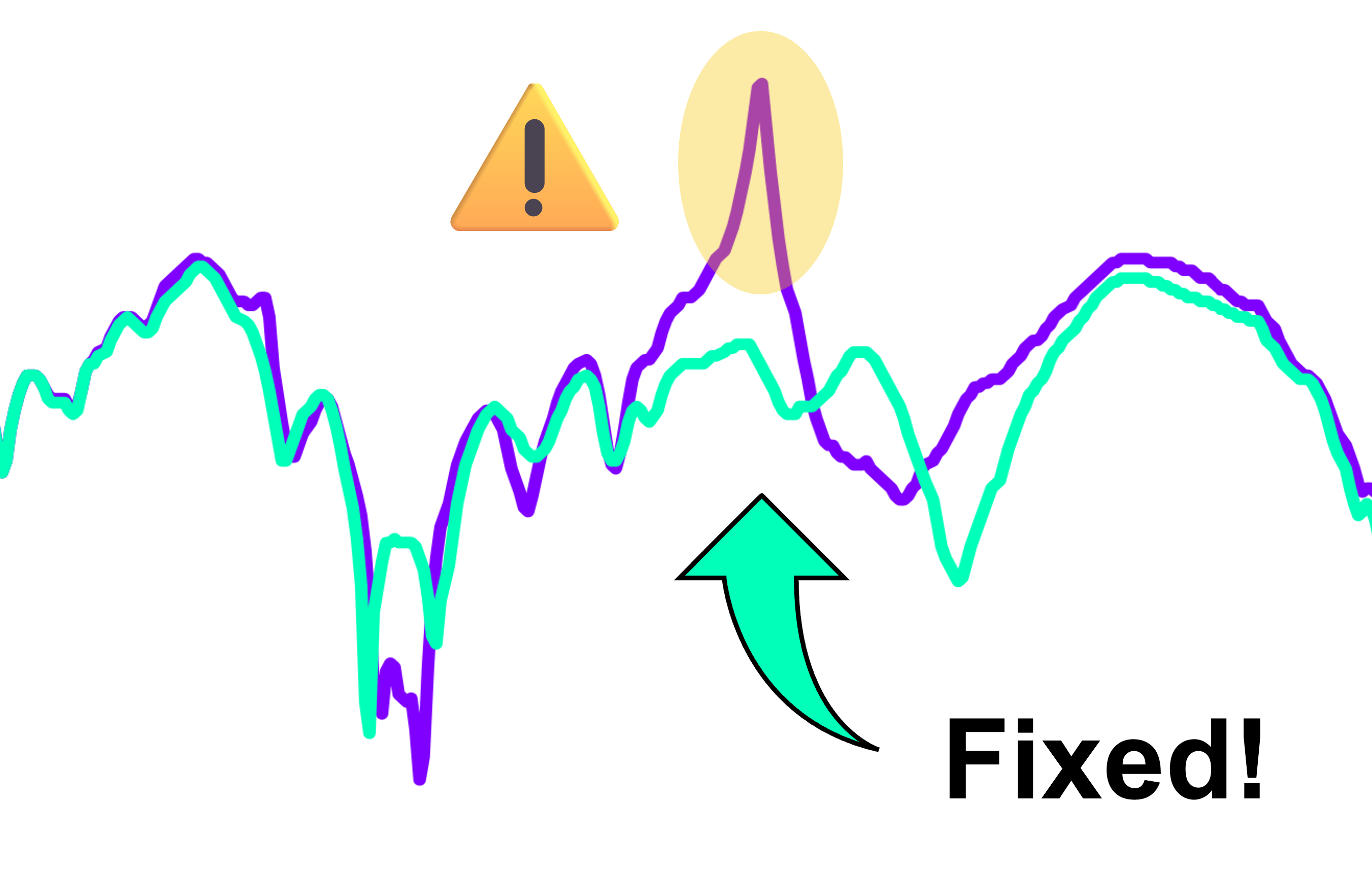
Have you heard of Frequency-based Substructuring (FBS)? This is one of a family of dynamic substructuring techniques used to analyze complex system behavior by dividing the problem into smaller, more manageable parts. FBS has long been a popular method in the CAE community to efficiently couple component Finite Element models using only Frequency Response Functions (FRFs) at their connection interfaces and predict the NVH performance of the virtual assembly.
Recently, a new trend in FBS has emerged. With physical prototypes becoming increasingly scarce in today’s NVH engineering landscape, test and CAE engineers are being driven to work closer together to exploit synergies between the physical and virtual worlds. As a result, NVH development processes are increasingly relying on hybrid virtual prototypes which combine data from physical and virtual components alike. This allows more of the component integration and design optimization work to be digitalized, saving both development time and cost.
From measurement inaccuracies to spurious peaks
Introducing test-based component FRFs in FBS introduces new challenges however. Unlike in CAE, the world of physical testing is full noise and inaccuracies which contaminate the measured data and therefore also the virtual assembly prediction results. This fact cannot be avoided, as even experienced NVH test engineers will produce results with some degree of human error.
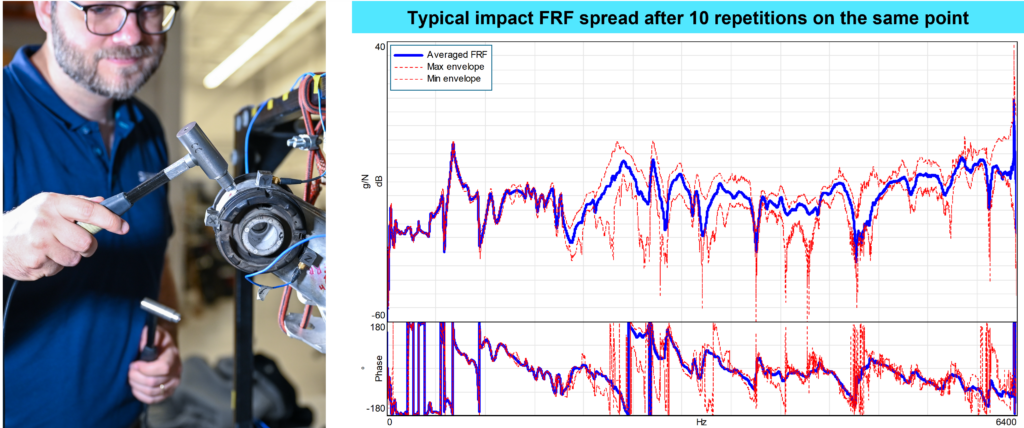
A particular point of attention are the “spurious peaks” which appear when the FRF inversion step in FBS amplifies inconsistencies near anti-resonances, especially in lightly-damped structures with sharp resonances. Such non-physical peaks strongly pollute the virtual assembly prediction results and should be avoided at all costs!
Consider the following example where we have used FBS to virtually assemble a wiper motor to a trimmed vehicle body. The wiper motor was suspended in free-free and its impedance FRFs were measured using impact testing and then transformed to its center of gravity using Virtual Point Transformation (VPT). A similar measurement was performed on the trimmed vehicle body to obtain its impedance FRFs and Noise Transfer Functions (NTFs) towards the target microphones in the cabin. When we directly apply FBS to this measurement data, the resulting assembly NTFs are distorted by a strong spurious peak.
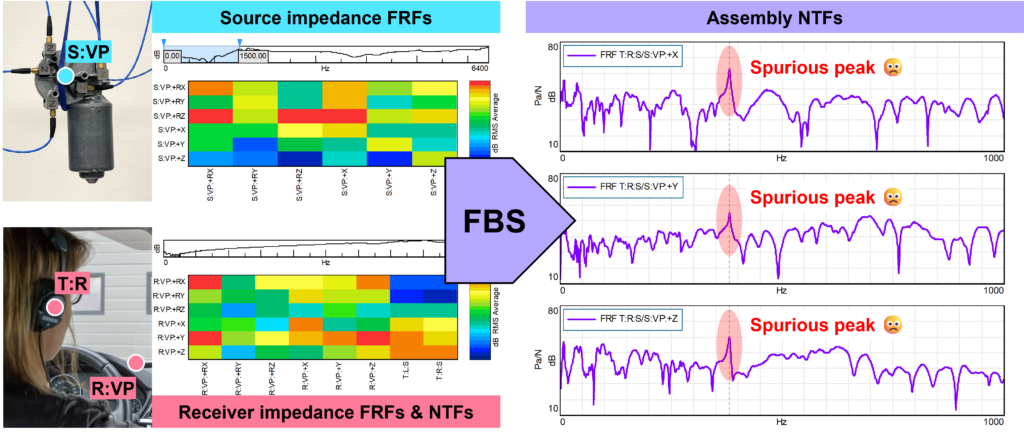
Why did this happen? The fundamental reason is that each individual impact is performed at a slightly different position and angle, resulting in impedance FRF matrices which are not perfectly reciprocal. This effect is particularly problematic in the lightly-damped wiper motor, where an inconsistent anti-resonance frequency manifests as the spurious peak seen earlier.
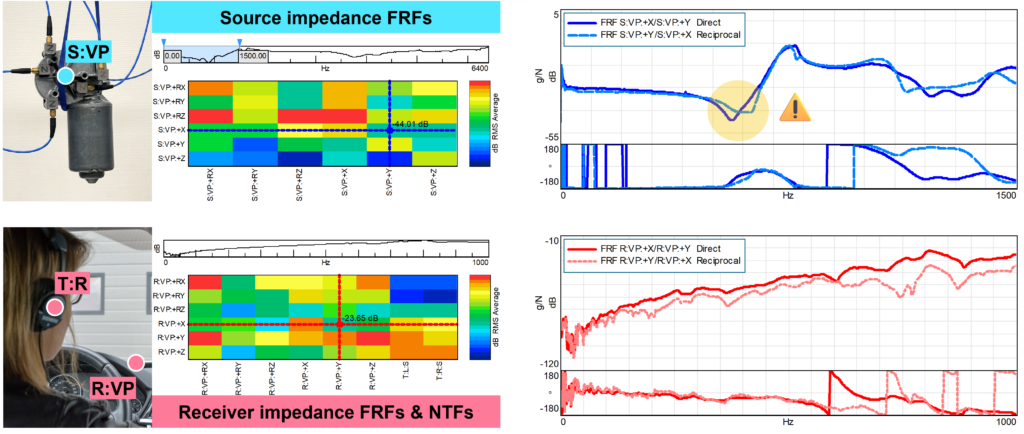
No more spurious peaks with Simcenter Testlab
Luckily, Simcenter Testlab offers a quick and elegant solution to this problem, drawing from our long-time expertise in Modal Analysis: Maximum Likelihood Estimation of a Modal Model (MLMM)! This unique algorithm automatically fits a modal model to an FRF dataset using a constrained optimization approach.
How does MLMM eliminate spurious peaks in FBS? Essentially, we can use it to quickly find the optimal reciprocal modal model for the measured FRF data and then re-synthesize the FRFs using that modal model. The result is a set of component FRFs which are guaranteed to be perfectly reciprocal and free of noise to boot!
I can hear you thinking: “doesn’t Modal Analysis require a significant time investment from an experienced engineer?”. With Simcenter Testlab Modal Analysis, this is no longer the case. After loading your measured impedance FRFs, you can use our PolyMAX curve-fitting algorithm to calculate a clean stabilization diagram which rejects noise and makes it easy to select the physical modes of the structure. Even so, Automatic Modal Parameter Selection (AMPS) will happily do the work for you to make it even easier.
Now for the best part: whether you are an expert or not, you don’t have to worry about making a perfect selection in the stabilization diagram! MLMM will take the initial guess provided by AMPS (or you) and iteratively optimizes it until it converges on the modal model with the best possible fit of the measured FRFs. Additionally, we can set certain constraints on the modal model during the optimization process, such as enforcing reciprocity to avoid spurious peaks in FBS. This whole process can be completed in just a few minutes and delivers extremely consistent results between novice users and experts alike.
Let’s revisit our wiper motor example. We have used MLMM to automatically find the reciprocal modal model that optimally fits the measured impedance FRFs. Using that modal model, we can now synthesize a new set of impedance FRFs which are perfectly reciprocal and free of noise.
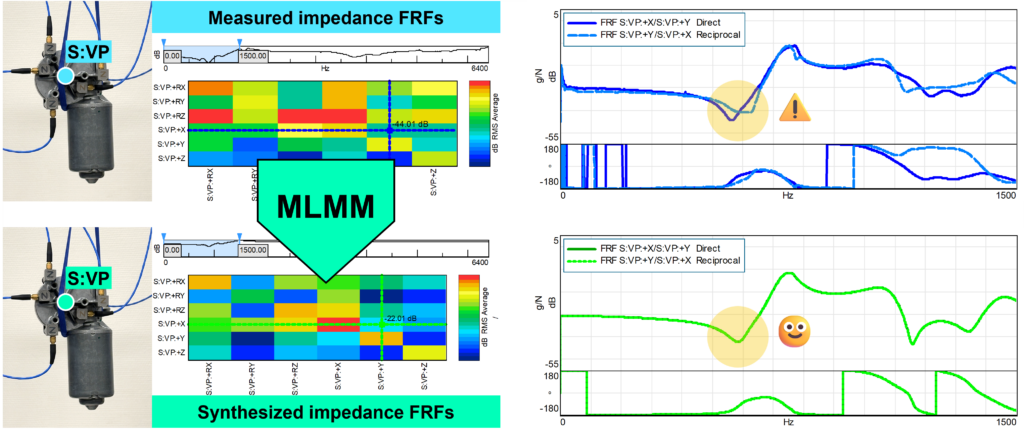
The result? Introducing the synthesized FRFs in FBS eliminates the spurious peaks completely!
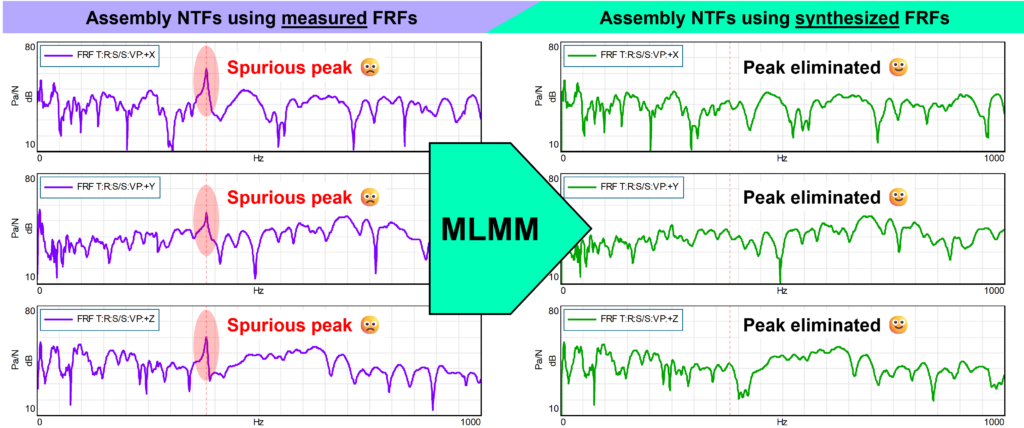
Maximize the accuracy of your hybrid virtual prototypes
Test-based component FRFs are vital to the digitalization of NVH development processes through hybrid virtual prototyping. However, special attention is needed to prepare such data for virtual assembly techniques like FBS, due to inherent inaccuracies in the world of physical testing.
Simcenter Testlab Modal Analysis and its unique MLMM algorithm provide a quick and elegant solution to re-synthesize measured FRFs with perfect reciprocity and zero noise, guaranteeing highly accurate hybrid virtual prototype prediction results.
Has this article left you curious about the technology and process behind predicting NVH performance using virtual prototypes? Watch our free on-demand webinars on Component-based Transfer Path Analysis (C-TPA) and Virtual Prototype Assembly (VPA) to learn more.