Simcenter Tire 2212 enables driver in the loop
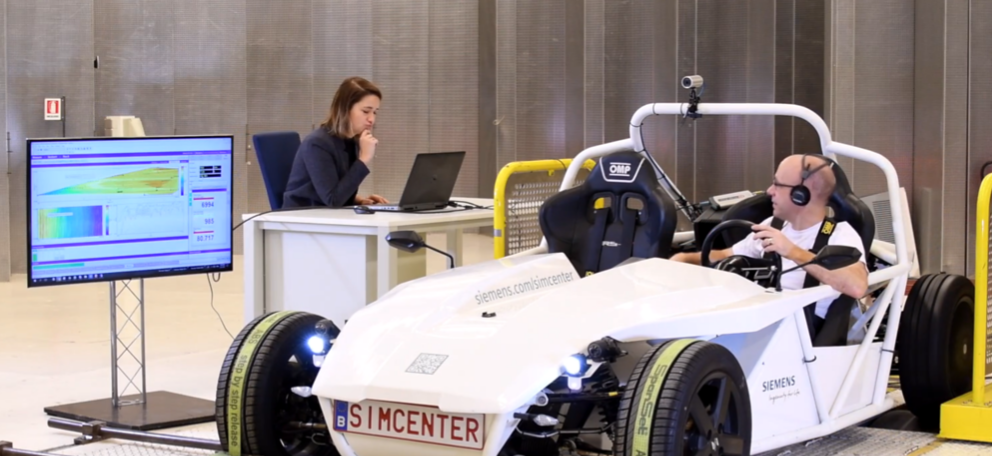
Enabling the virtualization of vehicle development through driver in the loop simulations
Accelerating vehicle development through virtual engineering
In recent years, the automotive industry has embraced – and accelerated – a transition from physical to virtual prototyping. As an industry, there is a huge desire to design products virtually, via computer-aided engineering (CAE), and thus significantly reduce the number of physical prototypes created throughout the design process. Achieving such a goal significantly reduces lead times and costs – hence, automotive OEMs can bring products to market faster and cheaper.
Most recently, CAE technology has become sufficiently advanced that companies can run vehicle simulations by pairing a driving simulator with a professional driver (i.e., a Driver in the loop, or DiL, setup). This in turn means that, for the first time, OEMs can obtain subjective feedback from tests performed entirely on the virtual proving ground.
Such an achievement is not an accident. In general, there are many phenomena that a professional driver can ‘feel’ but cannot be measured (or at least metricized). Traditionally, this has always forced engineers to rely on the same professional drivers testing physical prototypes on a track, after which they can provide their subjective feedback. However, today, with the help of Simcenter Tire, this process can be conducted virtually, and the vital subjective feedback provided by drivers can be given extremely early in the vehicle development process, overcoming the barrier of physical prototypes being required. This process has been shown in blogs posted by BMW and Continental.
Simcenter Tire: an enabler for subjective feedback
To enable DiL feedback loops in the virtual development process, there are two requirements: a high-fidelity model, and a model which solves quickly enough to run in a real-time simulation. However, these things naturally run contrary to one another: more detail often requires more computation time. To achieve the optimal balance for an end user’s application, our tire model – MF-Tyre/MF-Swift – is made up of several modules:
Module | Primary application |
MF-Tyre | Handling |
Turn slip | Parking/low-speed maneuvers |
Rigid Ring | Higher frequency (⪅100 Hz) dynamics |
Enveloping | Obstacles and/or rough roads |
Temperature and Velocity | Thermal modeling |
As a driver, to achieve the most realistic feeling possible, you would ideally enable all the above modules. And to maximize your fidelity, the enveloping module is vital for ride comfort and durability analyses.
Enveloping: a complex road contact model
Our enveloping module accounts for both rough roads and obstacles on a road surface. It works by first recognizing that, when driving over an obstacle (and/or a rough surface), two things occur in the contact patch: 1) the contact patch is lengthened; and 2) the tire ‘swallows’ obstacles. Both effects lead to the ‘enveloping’ phenomenon of tires.
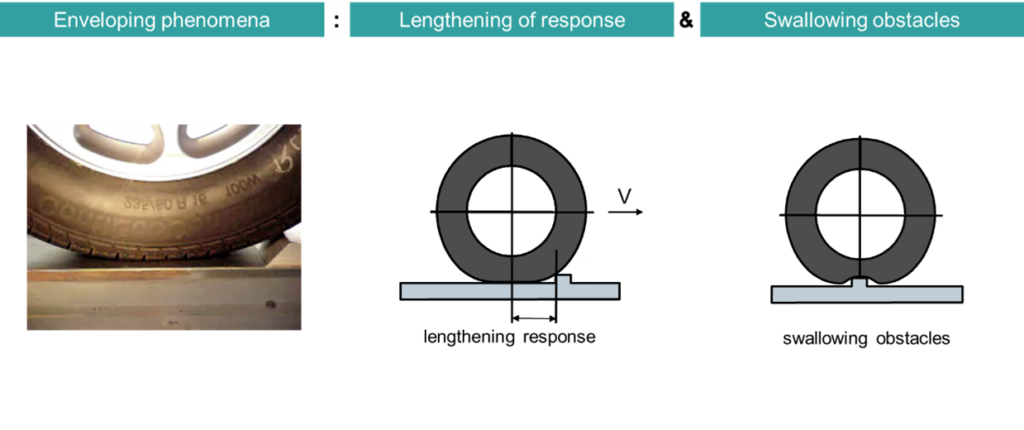
The enveloping effects combined can be viewed as the tire acting as filtering mechanism, from the perspective of the wheel center. This filtering occurs because it takes time (and distance) for the tire’s contact patch to fully drive over obstacles. In addition, the rubber effectively acts as a swallowing mechanism to the obstacle. So, from the perspective of wheel axle, obstacles are not so sharp:
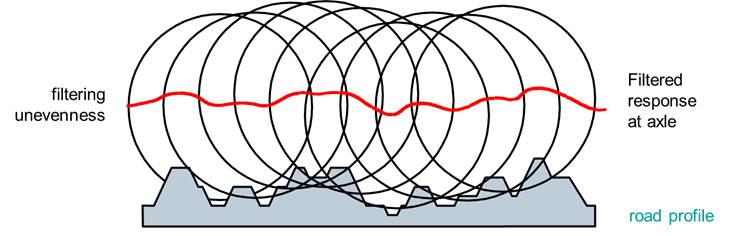
To account for this effect, the Simcenter Tire MF-Swift enveloping module uses a special road filter to determine the effective road surface at the wheel center. Then, that effective road surface is used as the input to the MF-Swift model. The filter works through using rigid elliptical cams. These are positioned at the front and rear edges of the contact patch and are free to move vertically as they encounter obstacles. For maximum accuracy, more cams can be utilized, and are inserted along the length/width of the contact patch. Of course, there is a trade off in computational efficiency.
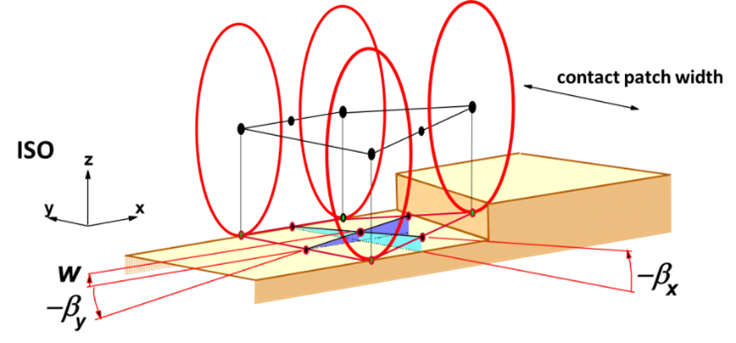
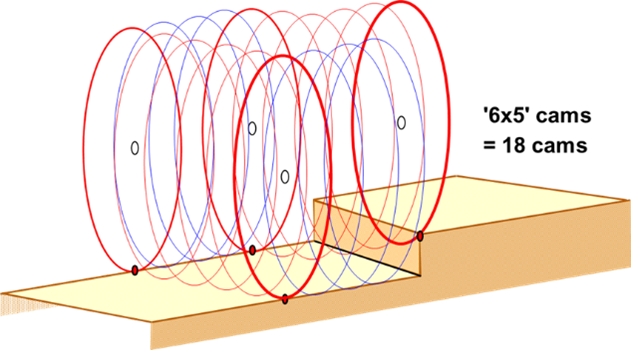
Thus, compared to the other modules within MF-Tyre/MF-Swift, enveloping is different in that it makes many road contact calls – especially when one uses a larger number of cams. Naturally, this increases the computation time, and therefore enveloping can be very computationally hungry. To enable maximum fidelity for DiL (and HiL) setups, we have therefore increased the computational performance of the enveloping module. We have done so by updating the way in which the road data exchange algorithm works. In the Simcenter 3D 2212 release, this has led to up to a 45% overall performance improvement.
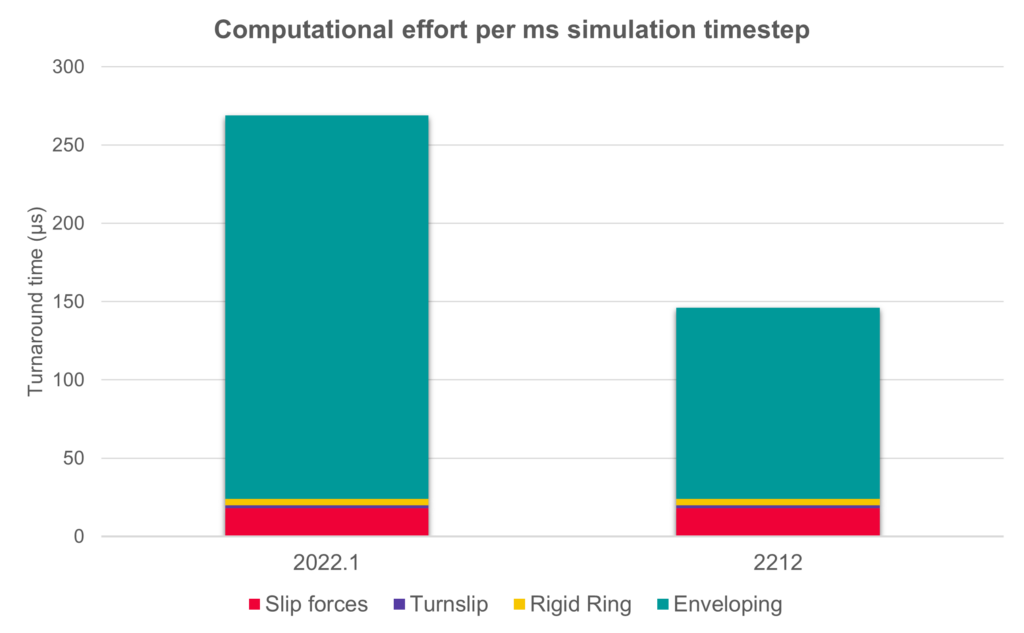
In the above figure, the computation time for one tire in the Simcenter Tire 2212 release is reduced to 150 µs per ms. For four tires, this would equate to ~0.6 ms, and thus allowing real-time capability and, with it, DiL-type setups are achievable.
Summary
The automotive industry is rapidly accelerating on its journey towards relying on virtual design loops for the development of new vehicles. An increasingly important part of that process is in the use of driving simulators, especially for the subjective sign-off of tire and/or vehicle characteristics. To truly enable the virtual development of vehicles, end users require high fidelity, real-time-capable tire models.
To support this process, in the Simcenter 3D 2212 release, we have updated our MF-Swift enveloping module to be much faster, ultimately leading to up to a 45% reduction in the overall solving time for our tire model. This then truly enables the use of DiL rigs, and with it has the potential to drastically speed up vehicle development by providing professional drivers ‘virtual’ access to the prototype vehicle and/or tires incredibly early in the process. The benefits also apply to Hardware-in-the-Loop (HiL) rigs, and even regular “desktop” (or “offline”) simulations.