Simcenter 3D 2020.1: What’s New?
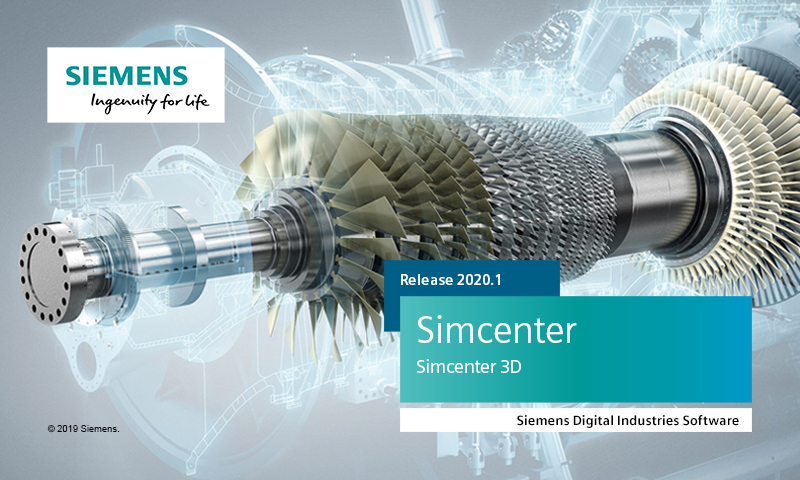
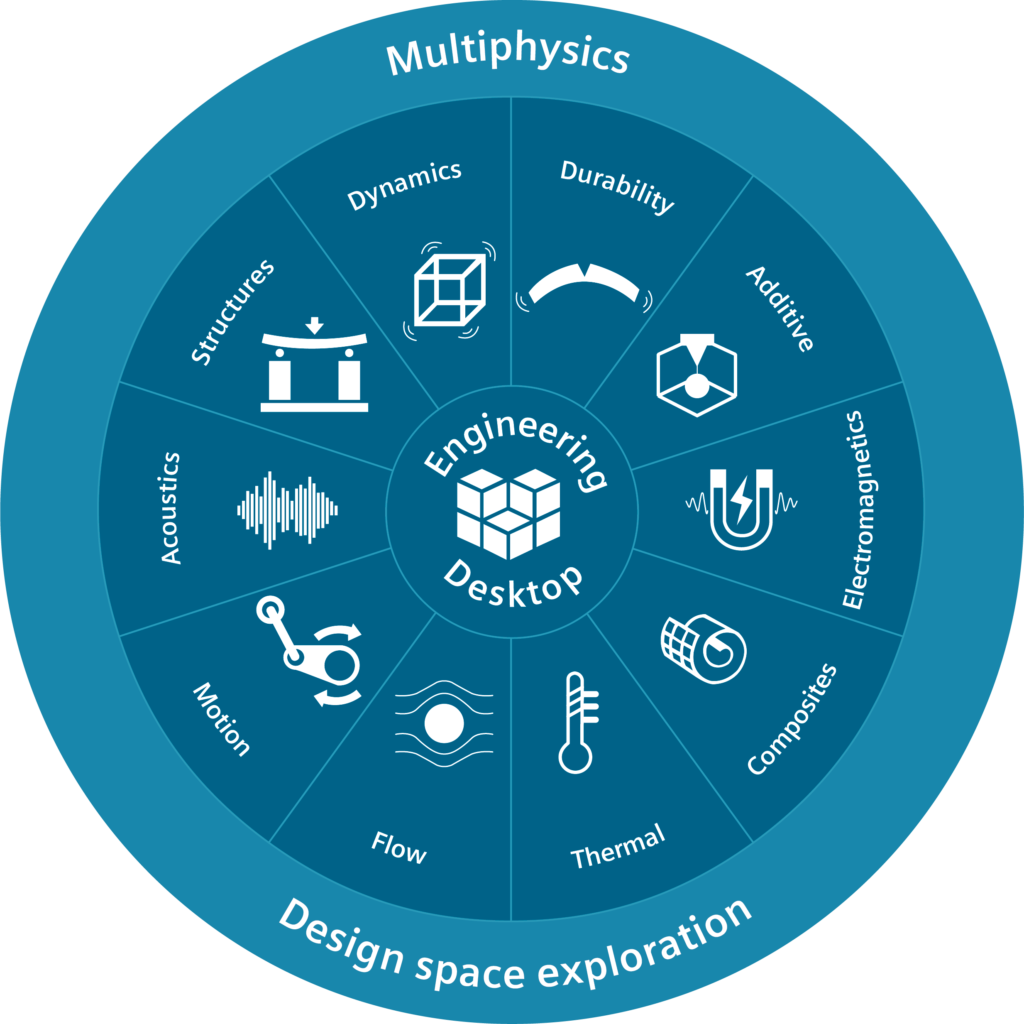
Meeting complex engineering challenges
Product engineering teams need a unified, shared platform for all simulation disciplines, with leading-edge analysis tools that are easy-to-use, incorporate more productive workflows and produce consistent results. As such, we are proud to introduce the latest release of Simcenter 3D, and our investments in Simcenter 3D 2020.1 are aimed at meeting complex engineering challenges.
Enhancements in this release are focused on these four differentiating strengths of Simcenter 3D:
MULTIDISCIPLINE INTEGRATION
Perform more simulation types from a common, integrated environment
Simcenter 3D delivers multi-discipline simulation all from within a centralized engineering desktop, and Simcenter’s 3D simulation solvers help you to predict real-world performance for a large variety of physics domains. With this release, we’re deepening the types of analyses that can be achieved in a number of these domains:
Extended rotor dynamics solution
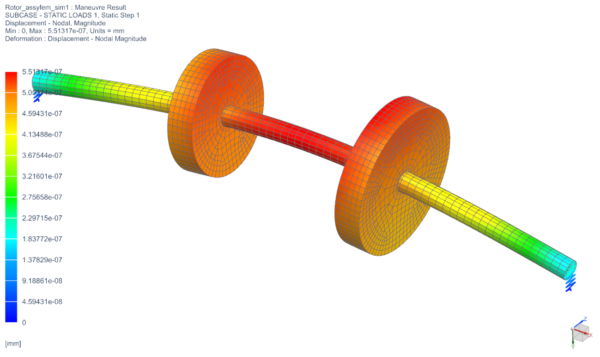
Understanding of the critical speeds in rotating machinery is important for engineers to avoid potential catastrophic failures. In previous versions, Simcenter 3D’s rotor dynamics simulation was restricted to linear analysis, but in this release, we have extended the solution to cover nonlinear connection elements. This means rotor dynamics analysis in Simcenter 3D allows you to minimize rotational unbalance and unnecessary external forces in applications such as aircraft engines, gas turbines, automotive engines, industrial equipment, and even electronics – like in the case of computer disk drives that spin at high rates.
Aeroelasticity flutter analysis
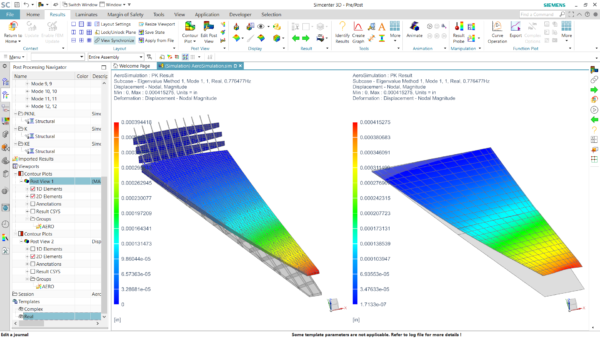
Flutter is an unstable oscillation caused by interaction of aerodynamic forces and is a very dangerous condition for aircraft because it can lead to destruction. With this release, Simcenter 3D now has the ability to perform aeroelastic flutter analysis through the Simcenter Nastran solver. With Simcenter 3D, you define the aerodynamic model as well as aerodynamic and flutter analysis parameters like the mach numbers and altitudes. On top of that, The International Standard Atmosphere (ISA) definition has been integrated to help easily define these parameters. Finally, As with all models created using Simcenter 3D, your analysis model is associative to the design geometry and will update automatically with any geometry change so you can rapidly see how geometry changes impact results.
Ray acoustics
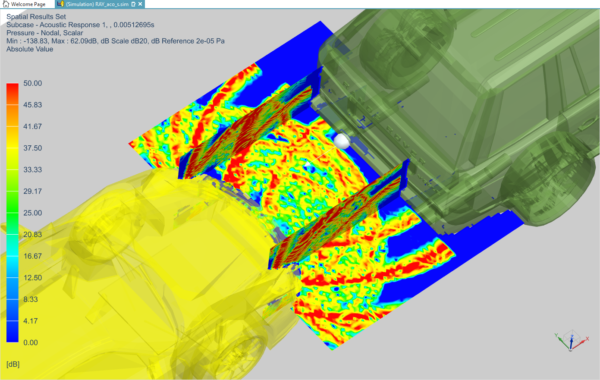
Boundary element and finite element method based simulations are very well suited for low and mid-frequency simulations, but their model sizes become very large very quickly when increasing the computation frequency. This makes these higher frequencies difficult to compute even with good hardware. Simcenter 3D’s new ray acoustics solution treats high frequency sound behavior as if it were a ray of light. This means you can simulate sound propagation by tracing beams of sound shooting from a monopole source and reflecting when striking surfaces. Simcenter 3D Ray Acoustics lets you simulate very large geometries and higher frequencies for applications like exterior ramp noise or interior cabin noise for aircraft, or for automotive parking sensor pulse simulations.
Two-way fluid-structure interaction (FSI)
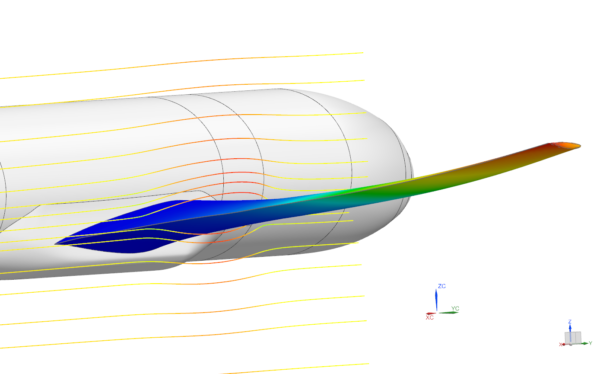
In the past, performing structural analyses in conjunction with flow simulations was a disjointed process and only supported one-way coupling. Now in this Simcenter 3D release, you can streamline this complex multiphysics analysis by setting up a single solution with both structural and flow physics and launch a two-way coupled solution all from an integrated environment. An example application would be air flow over a wing which causes a lift pressure that deforms the wing which then changes the flow field around the wing. It is also possible to include thermal effects in the multiphysics environment so one could simulate coupling of thermal, flow, and structural physics without user intervention.
FASTER CAE PROCESSES
Spend less time modeling, and more time on engineering
Faster CAE processes are another hallmark of Simcenter 3D. Simcenter 3D’s unique simulation environment helps you achieve much faster CAE processes than what can be achieved with traditional CAE tools, and this release expands our ability to help engineers spend less time modeling and more time on actual engineering.
Design space exploration for aerostructures
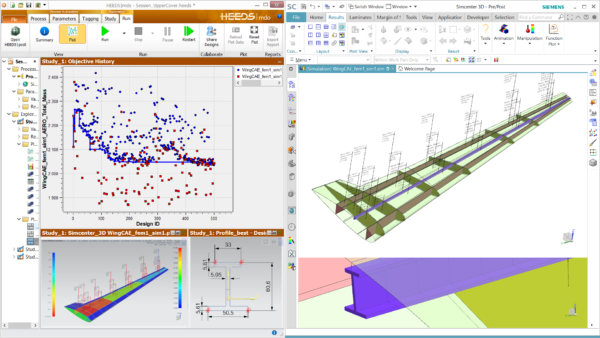
In this release, we have added the ability to use Simcenter 3D Design Space Exploration with Simcenter 3D Margin of Safety. Thanks to both its parametric engine and its strong link to CAD, Simcenter 3D provides unique capabilities for design space exploration. This lets you automate and simulate multiple design variants so you can quickly understand how design parameters impact margin of safety performance so you can make the right data-based trade-off decisions.
NVH composer
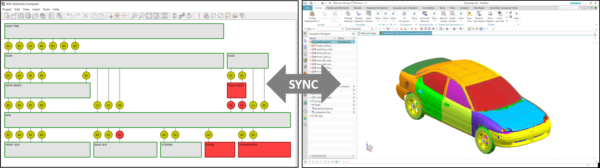
Previously, assembling and verifying a full vehicle model for noise, vibration and harshness (NVH) was an error-prone process that took weeks. Now with the new NVH composer in Simcenter 3D, you get a simplified interface to interactively define the full vehicle assembly layout as a 2D network diagram, including all typical automotive full vehicle connections. Once the full vehicle assembly layout is defined and verified, the NVH composer automates the creation of a ready-to-run full vehicle FE model – reducing human error.
Motion parameter tables
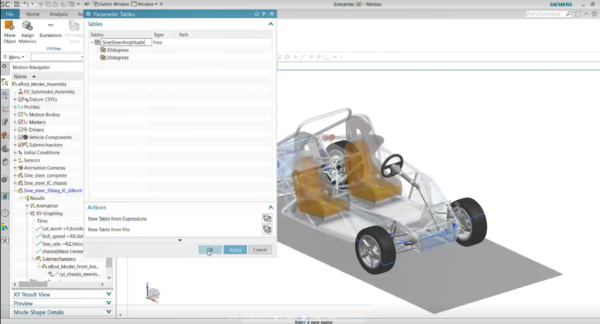
Now you can easily parameterize motion models through configurations of expressions. You can create sets of model parameters with different values that change depending on each configuration. This speeds the model setup process by letting you simply cycle through configurations without retyping in parameters so that you can quickly evaluate the effects of any changes to the model design.
TIED TO THE DIGITAL THREAD
Connecting simulation to your development process
Simcenter 3D has always had seamless, out-of-the-box integration with data management to help keep simulation in sync with the latest design variations. But simulation also needs strong ties to the physical testing group. In this release, we have invested in deepening Simcenter 3D’s test/analysis correlation capabilities which helps increase confidence that your simulations are accurately predicting real-world results.
Test/analysis correlation
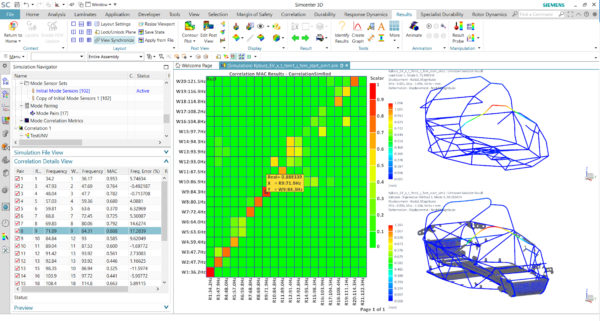
We have added new capabilities in the area of test/analysis correlation for pre-test planning. This means you can use analysis models to help test engineers determine the best locations where they should add sensors an exciters to the physical test model.
Load identification from test
Determining operating forces at connection or attachment location is very important for analysis, such as for transfer path analysis (TPA). Test teams can capture these forces through their measurements. The test team can then share the measurement data with the analysis team, and Simcenter 3D can compute loads to be used for NVH analyses from thephysical test measurements, which helps ensure you’re using the right loading data.
OPEN AND SCALABLE
A pre/post for all of your solvers
Simcenter 3D is not a closed environment, and you can gain the benefits of faster CAE processes and multidiscipline modeling by using Simcenter 3D in connection with other popular CAE solvers you might use.
Abaqus cyclic symmetry
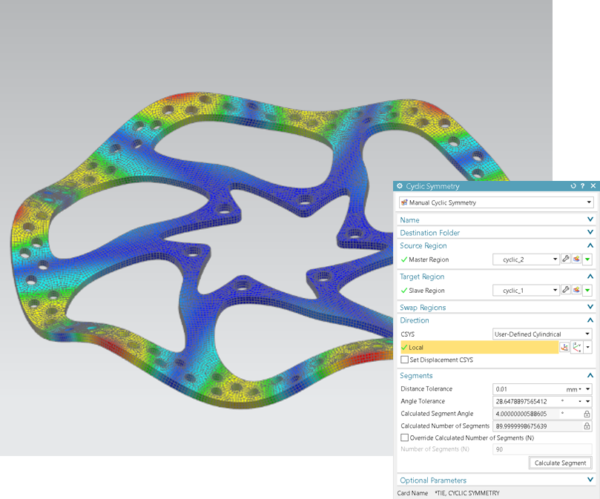
Cyclic symmetry simulation is often used for efficient structural modeling of rotating systems such as for blades and disks in turbine engine systems, and this capability has been supported for the Simcenter Nastran solver for some time. In this release, Simcenter 3D now also extends support for cyclic symmetry to the Abaqus solver environment. In addition to easily being able to set up the cyclic boundary conditions in the pre-processing steps, it is possible to post-process an Abaqus ODB file to plot contour and animation results for the single sector or any number of the sectors.
Comments
Comments are closed.