Accurate and robust CFD for rotary positive displacement machines: TwinMesh™ meets Simcenter STAR-CCM+

A global success story – Robustness and broad applicability of rotary positive displacement machines
Rotary positive displacement machines are indispensable for various industrial processes due to their robustness and ability to handle highly viscous, abrasive or corrosive fluids and maintain constant flow rates. They can operate under varying pressure conditions, ensuring efficient and reliable operations, and are most efficient when handling lower heads at high flow rates.
- Screw pumps can transport very high viscosity fluids, such as crude oil, slurries or paper pulp, and are for example deployed in the chemical, petrochemical and process industry. In the area of food and beverage, dairy products, syrups, juices, and other food ingredients need to be pumped while ensuring sanitary conditions. The smooth, continuous flow predestines them also for pharmaceuticals, supporting transfer and dosing of medical compounds and solutions.
- Gear pumps are typically deployed in lubrication systems, for fuel injection or hydraulic applications.
- Screw compressors can be used in the process industry to compress various gases, e.g. pressurized air, but also hydrogen or carbon dioxide.
- Scroll compressors are frequently applied for refrigeration and cooling units, ensuring steady and quiet operation when compressing and pumping refrigerants.
- Scroll or screw type expanders play an important role in the context of organic Rankine cycles, e.g. in geothermal applications, heat pumps, or waste heat recovery systems, but also for pressure reduction processes – like in natural gas distribution networks – or for compressed air energy storages.
- Lobe blowers are comparatively cheap, reliable devices for moving air and gases in many industrial applications, e.g. as vacuum pumps or in drying or extraction systems.
The range of applications is obviously vast, and while the examples provided here are not exhaustive, they certainly offer a glimpse into the numerous possibilities and the importance and impact of these devices.
Pumps under pressure – the challenges of efficient rotary machine design
Energy conservation is becoming increasingly important for society and industry. National and international regulations demand higher efficiency across nearly every sector, and companies are trying to reduce their environmental footprint. It is thus worthwhile to reduce energy consumption also for industrial machinery.
For rotary positive displacement machines, optimization can be especially challenging: They must handle varying conditions and feature extremely complex geometry. Characterized by complicated, 3-dimensional shapes, they are transporting fluids through the movement of rotating volume chambers. Narrow gaps between the chambers formed by the rotors or between rotors and stationary parts, such as housings, cannot be avoided and are causing leakage flow and losses, leading to efficiency decreases.
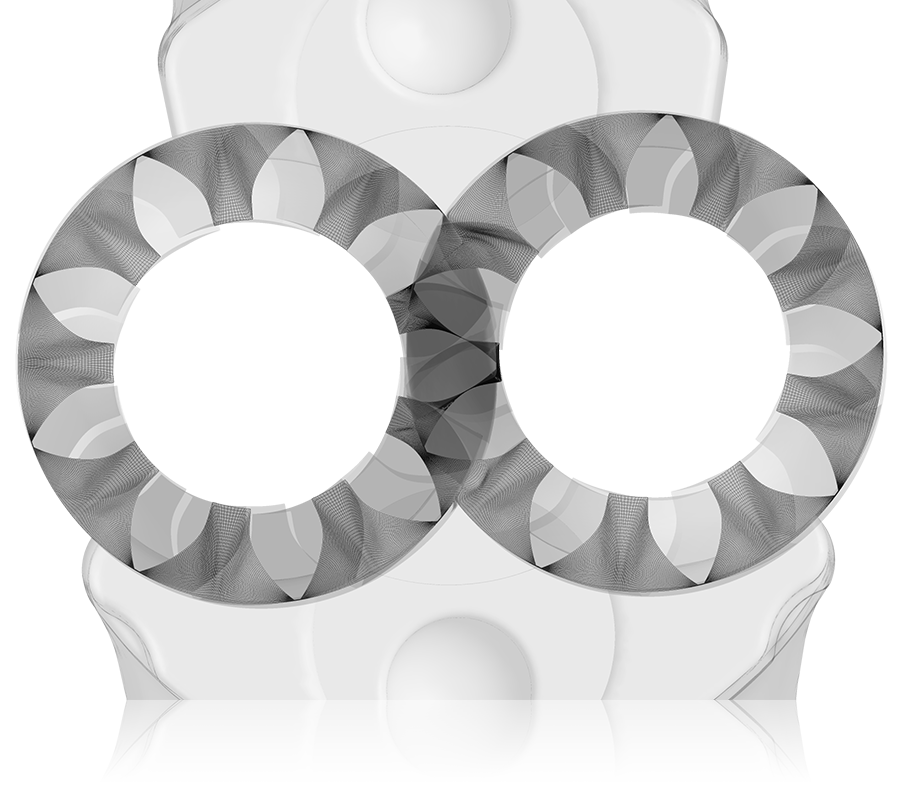
Improving the design can be challenging due to the difficulty in gaining insight into the flow field. After all, it is very complicated or even impossible to measure detailed fluid behavior directly in closed cavities, as measurement probes either cannot be put in place or would affect and distort the flow significantly.
Model physical complexity of rotary positive displacement machines with high fidelity CFD
But there is a smart way out: Computational Fluid Dynamics (CFD) simulation can overcome this issue and provide detailed insights into flow variables like velocity fields, temperatures or pressure distributions. The flow through gaps can be analyzed in detail. A lot of understanding can be gained about the liquid and gas flow and complex physical effects.
Flow and fluid phenomena such as turbulence, boundary layers, compressibility, or complex, rheological material properties, cavitation, as well as the free surface of additional liquids for sealing, cooling or lubrication (where required) are crucial for the operation of rotary displacement machines.
As a multiphysics CFD software, Simcenter STAR-CCM+ provides the required modelling capabilities to accurately simulate these machines with all the typical relevant effects. For instance, the representation of free surface flow or radial clearance cavitation can be achieved using multi-phase flow and cavitation models. The simulation of wetted surfaces is facilitated through the utilization of wall film models. The inclusion of time integration enables the simulation of transient movement, just to mention a few capabilities.
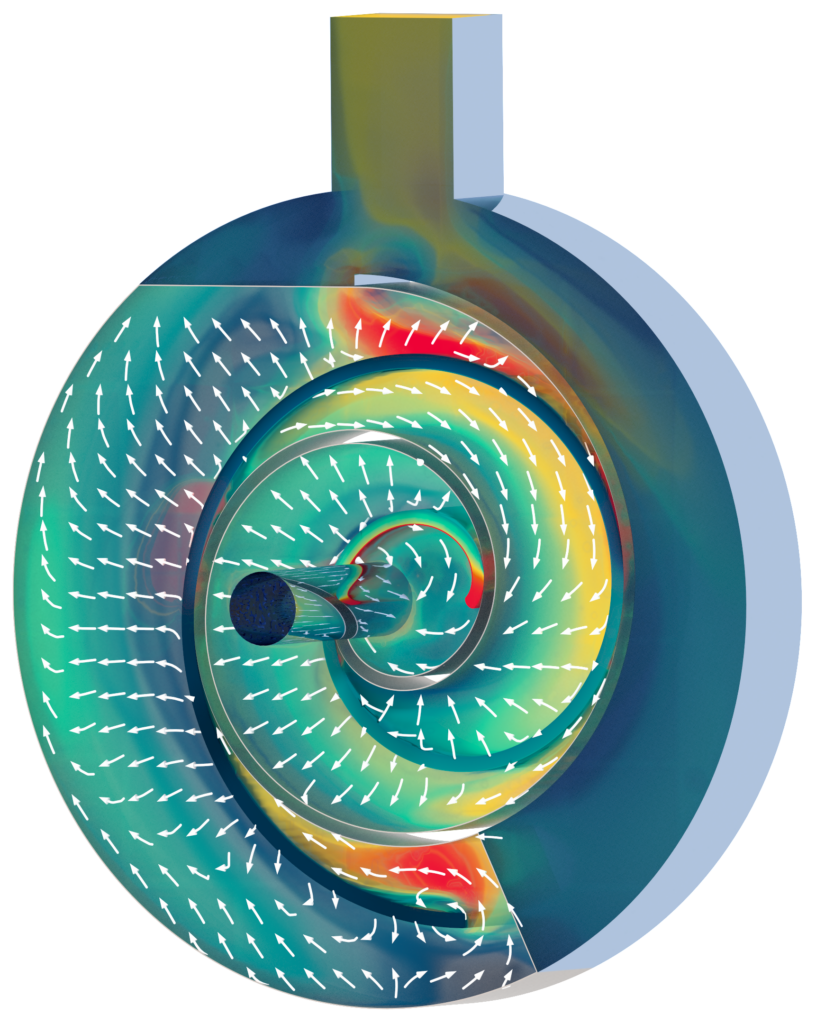
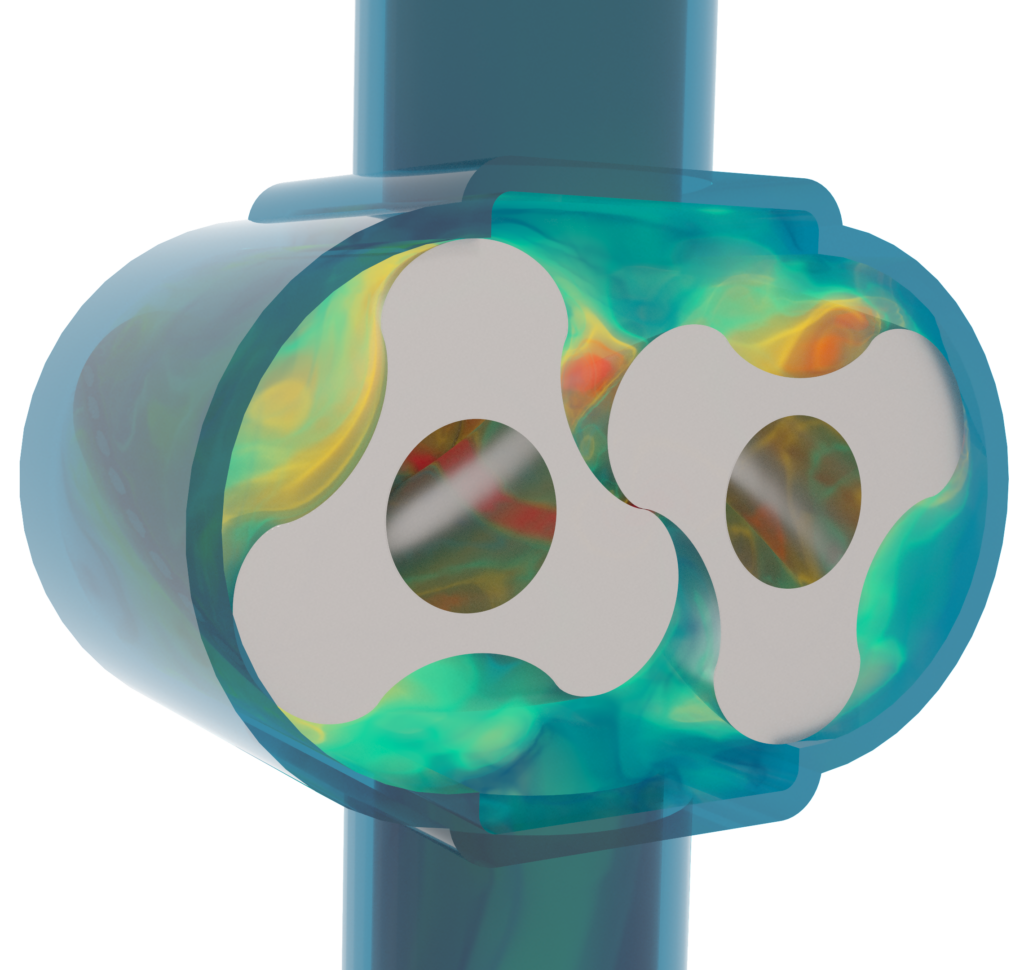
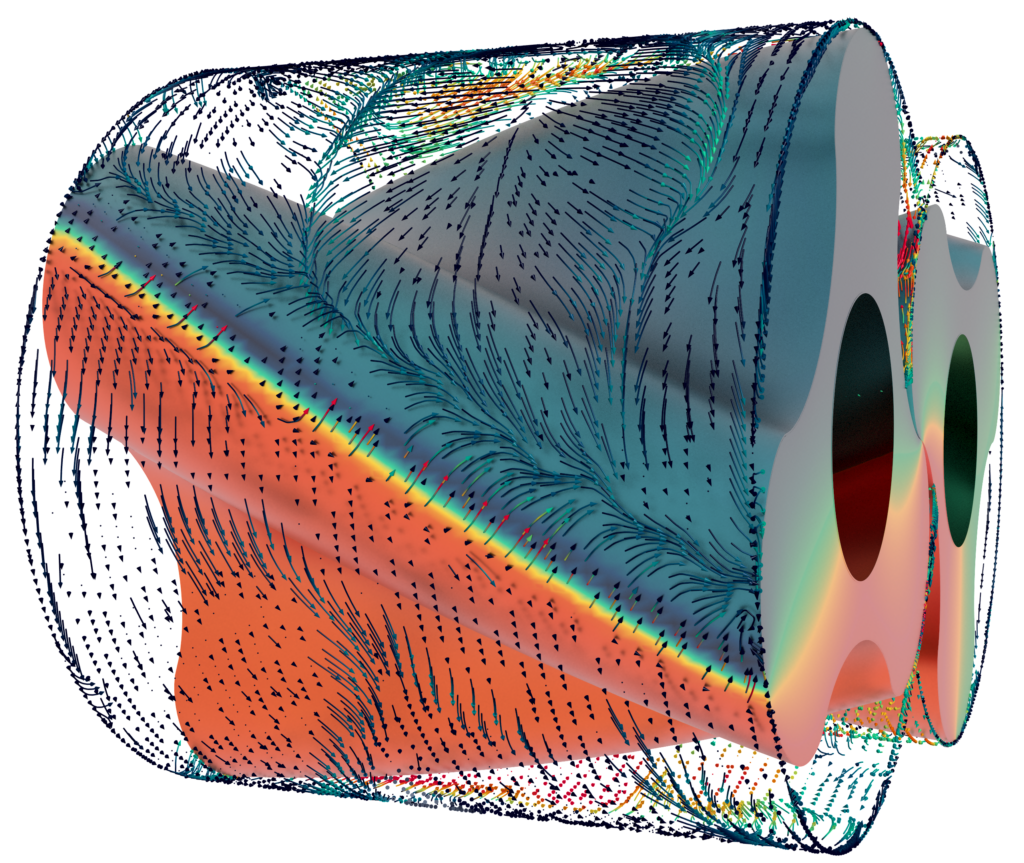
The challenge of high quality CFD simulation meshes for rotary positive displacement machines
And while Simcenter STAR-CCM+ offers all the high-fidelity capabilities to enable engineers to model the physical complexity of rotary positive displacement machines, this alone is not sufficient. The success of numerical simulation significantly depends on the quality of the fluid domain discretization – simulation engineers refer to this as “meshing”. The number of cells should be minimized as far as possible, to avoid excessive computation times, while the cells must not be distorted or feature extreme aspect ratios. And for rotary positive displacement machines this is a very delicate challenge:
Rotary positive displacement machines obviously contain moving parts. So any CFD method must consider this movement. On top those machines are usually characterized by very small clearance gaps that need to be adequately resolved to capture the underlying physics. And discretizing ever changing small volumes is not a walk in the park. The choice of the meshing scheme is therefore crucial for accurately simulating these machines, while ensuring efficiency and process reliability.
The most widely used, proven and tested meshing schemes for simulating moving or rotating geometry parts in CFD can have shortcomings when applied to rotary positive displacement machines.
Overset meshes are used to discretize a computational domain with different meshes overlapping each other. To represent movement, the mesh is updated regularly during the runtime of the simulation. Another approach is to use mesh morphing and remeshing. Here, the mesh topology changes according to the moving geometry. Remeshing is triggered whenever the mesh quality drops below user-defined mesh quality criteria.
While being valuable for several applications, the methods described above can lead to a high mesh count when small details – like gaps – need to be resolved, especially as they are usually based on tetrahedral or polyhedral meshes. Changing meshes will always exhibit a certain degree of mass non-conservation due to the interpolation. The meshing settings need to be controlled carefully to ensure that the model preparation and numerical simulation process are stable and robust – resulting in effort for the CFD practitioner.
In terms of accuracy and simulation time, structured meshing with hexahedral elements is ideal for simulating rotary positive displacement machines. Nonetheless, building such meshes manually is not a practical alternative as it can be extremely time consuming – the mesh generation could take days or longer, depending on the user’s experience.
This is where TwinMesh™ comes into play: CFX Berlin Software GmbH has developed a method to overcome all the challenges offering an automated meshing solution tailored to rotary positive displacement machines.
Go faster: Automated meshing workflow with TwinMesh™
The preprocessing software TwinMesh™ by CFX Berlin Software GmbH allows to automatically mesh the time-varying flow volumes in the working chambers of rotating positive displacement machines. TwinMesh™ generates meshes for the chambers and gaps for each rotational position and performs a mesh quality check. The meshes are block-structured and hexahedral which helps to limit the total number of grid cells while at the same time sufficient resolution of boundary layers and gap clearance can be realized. In combination with a consistent mesh topology for each rotational position – i.e. node numbers and connectivity stay the same – the overall simulation time can be kept reasonably brief.
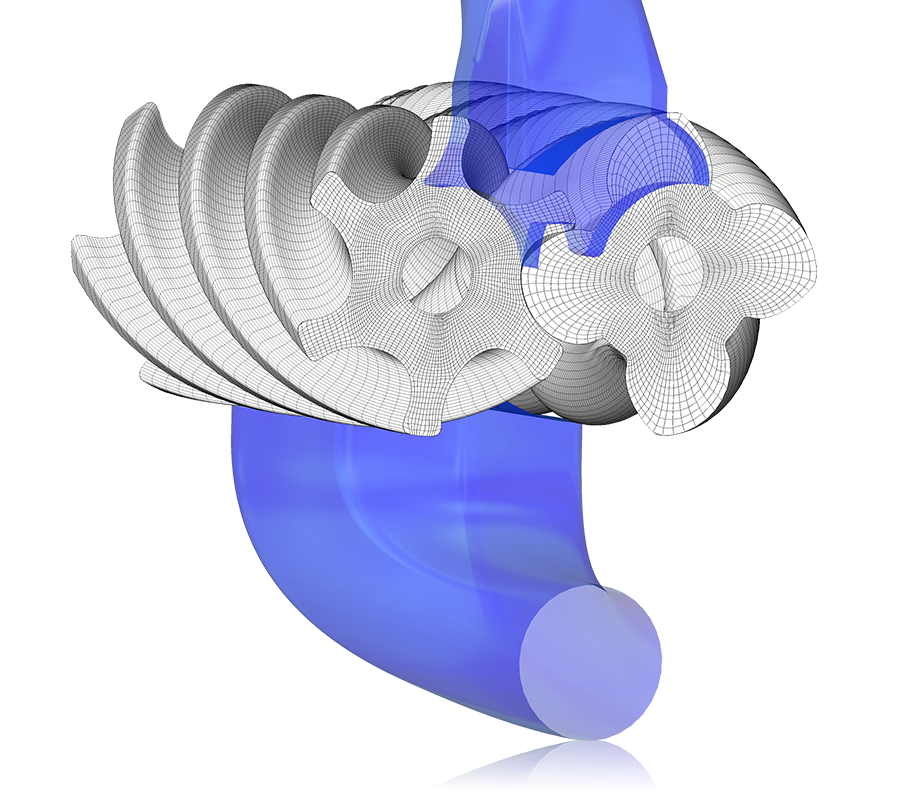
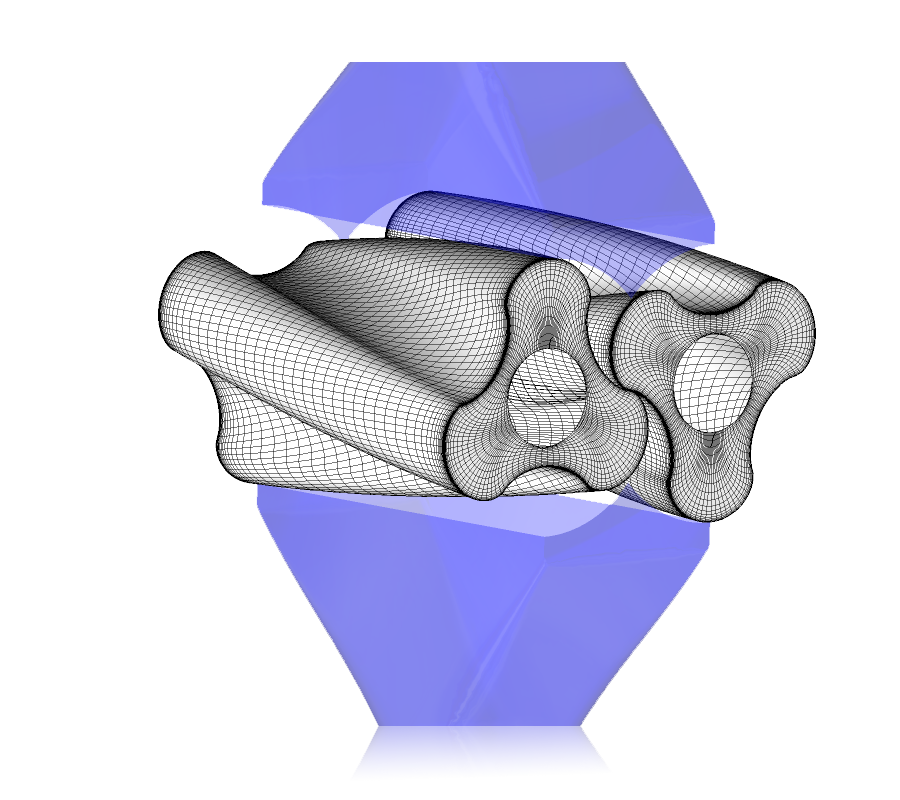
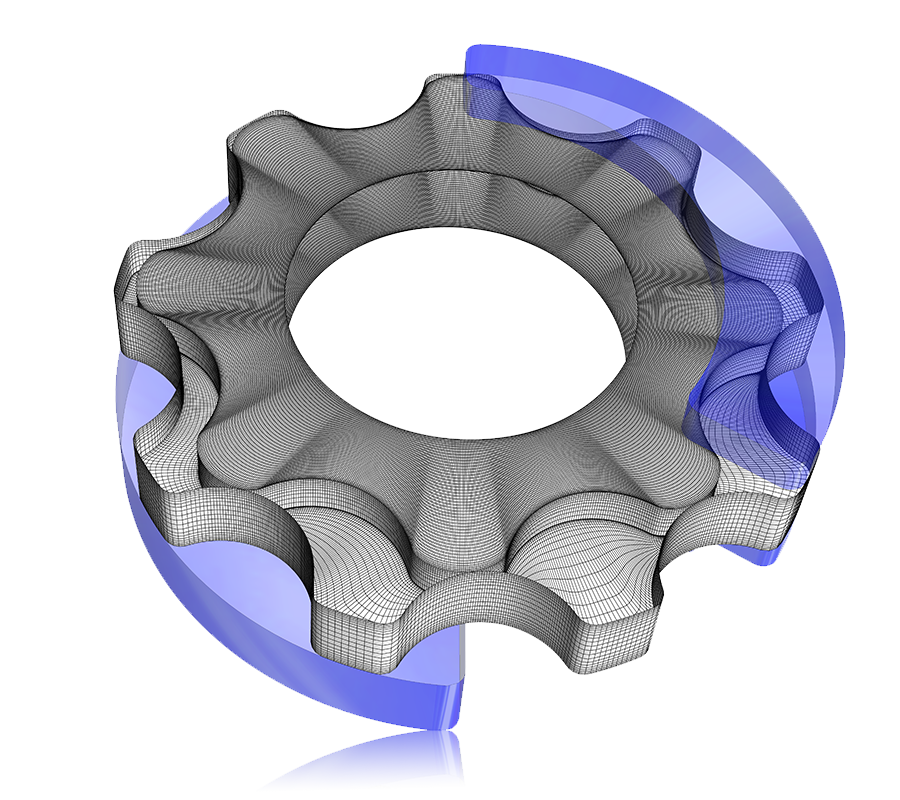
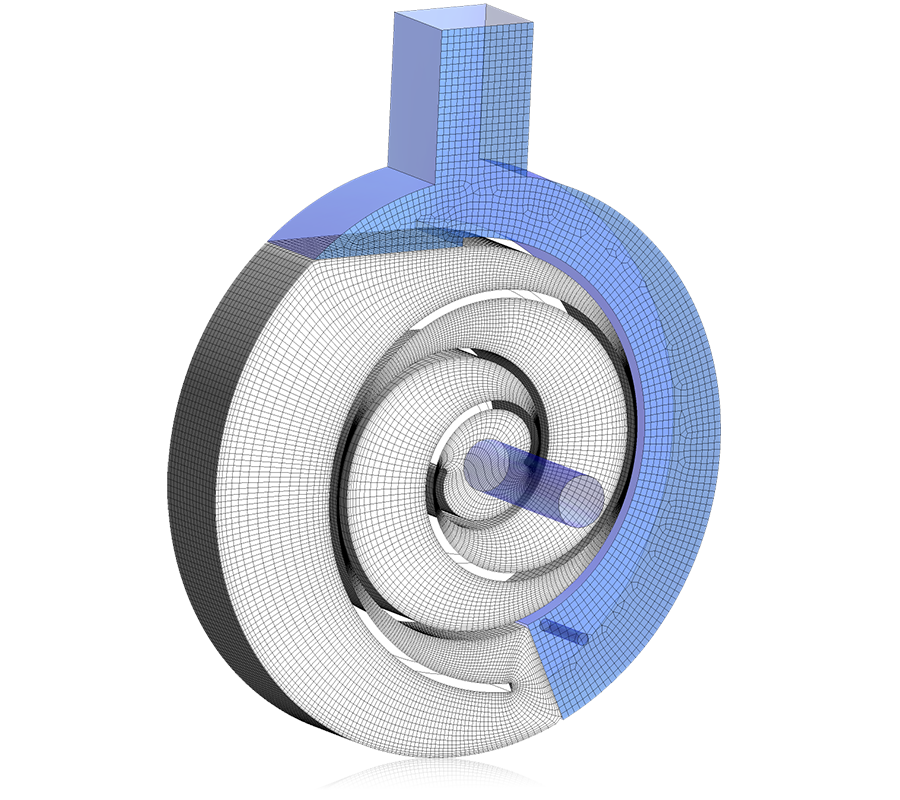
And so with high fidelity CFD modeling capabilities and a robust high quality meshing technology, all the elements you need to develop innovative rotary positive displacement machines are on the table. There is only one revolution missing: combine the two.
Stay Integrated with TwinMesh™ and Simcenter STAR-CCM+
Together Siemens and CFX Berlin Software GmbH developed a seamless workflow to leverage TwinMesh™ in combination with Simcenter STAR-CCM+. This allows you to take advantage of the benefits of modern 3D CFD for many different types of rotary positive displacement machines.
High-quality meshes, with defined quality in terms of distortion and aspect ratio, are exported as a set of files together with all the required setup information, so that the simulation can be directly started in Simcenter STAR-CCM+. This automated procedure ensures process reliability during product development and helps to accelerate the design process significantly.
With 3D simulation providing detailed insights into the internal flow properties, new ways for innovative design and rotary positive displacement machines performance enhancement are opened up.
Enterprises, small to medium-sized businesses as well as research institutions can achieve faster development cycles, create innovative designs, improve energy efficiency, and meet stringent industry requirements, thus gaining competitive edge in the market. With this the next revolution of rotary positive displacement machines has only just begun.