Perfecting the mechanical behavior of seats at Faurecia for the Cockpit of the Future
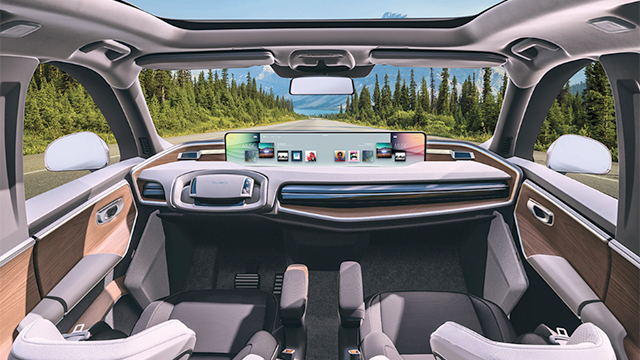
At Faurecia, delivering innovative automotive solutions is at the heart of everything the company does. This includes the products delivered to customers, as well as the tools and methodologies used by internal teams.
At Faurecia Automotive Seating Business Group, engineers are responsible for designing and producing automotive seats and mechanisms. They are the authority for the reliability and engineering of these systems, and they support generics, acquisitions, and application projects.
Within this group are simulation engineers who meticulously analyze nd perfect the mechanical behavior of seats. These engineers work with the design teams to provide innovative solutions to ensure the user experience of these seats is exactly what their original equipment manufacturer (OEM) is looking for.
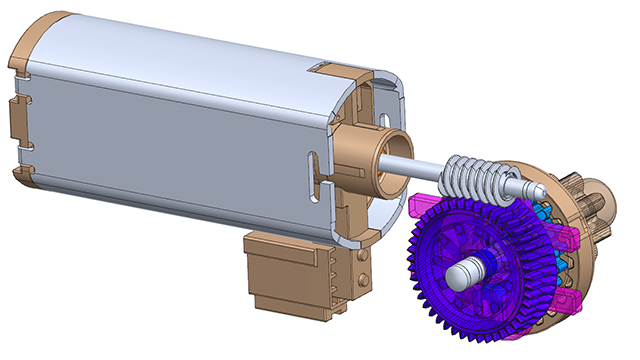
Understanding the mechanical behavior of seats
In order to fully support the design team, engineers need to fully understand the complete mechanical behavior of seats. This includes vibration, loads, tolerances, and contact interferences during motion and defects, to name but a few.
Additionally, engineers need to understand the behavior of seat mechanisms, including mechatronics components, in order to optimize design solutions. Compounding the challenge, manufacturing tolerances and slight variations in the final produced parts can have a significant impact on the forces a mechanism needs for movement. Therefore, it is critical for the engineering team to understand this range.
The importance of perfecting the mechanical behavior of seats
When autonomous electric cars become the norm, seat motion will get even more interesting. Drivers and passengers won’t need to look forward at the road. As a result, car seats will need to have the ability to rotate or move into more lounge-like configurations.
In addition to these new motion challenges, reducing vibrations and the acoustics felt by passengers in their seats will become even more critical since cars will be quieter and smoother without an internal combustion engine (ICE). As part of Faurecia’s “Cockpit of the Future,” reducing vibration and sound in seats will also become more important.
Faurecia’s goal is to measure and quantify vibration, as it can have a detrimental effect on the driving experience. In the past, engineers used to solve these issues with physical testing and experimentation with expensive prototypes. But Faurecia has found a better way.
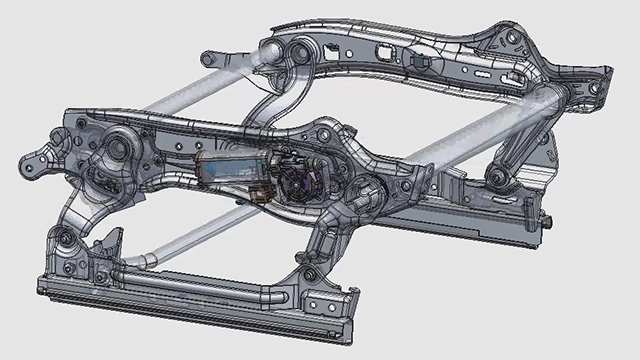
Simulation as a solution
Faurecia has been using Simcenter 3D Motion software and its predecessor, LMS Virtual.Lab™ Motion software, since 2007. “Simcenter 3D Motion makes it possible for us to understand how a production defect will affect a mechanism’s operation and helps us find innovative solutions to give to our design team,” states Mohamed Ben-Tkaya, functional simulation expert at Faurecia. “It allows us to perform end-to-end analysis of the complete functional behavior of automotive seat systems (frames and mechanisms), taking into account all interactions between parts (assembly forces, components flexibility, joints, and contacts).”
Streamlining the CAD workflow
Another advantage of using Simcenter 3D is that it is easy to parameterize CAD dimensions to quickly run multiple simulations. Engineers can import CAD geometry from any source into Simcenter 3D using the JT™ data format translator. The software allows the user to easily update the geometry to cascade into the simulation model.
Once the geometry is in Simcenter 3D, Faurecia simulation engineers are able to parameterize the geometry and perform numerical design-of-experiment (DOE) analyses for minimum and maximum tolerances when a seat is in motion. This gives them a full understanding of the design tolerance impacts on the functional performance of the seat system.
“One of the key benefits of using Simcenter 3D is the CAD associativity that allows us to quickly change our models,” says Ben-Tkaya. “During the design phase, we have a lot of iterations – sometimes the design team will come in every day with new solutions. Constructing a model is a complex and time-consuming process (for example, a recliner model can contain more than 300 contacts), so the ability to automatically update our models with multiple iterations is one of the reasons we chose Simcenter.”
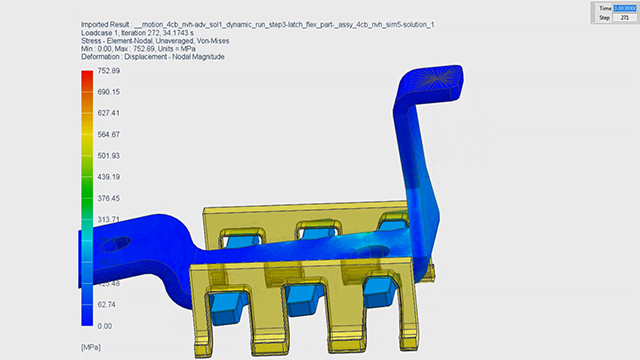
Reducing the time and cost of experimental testing for the mechanical behavior of seats
“Using simulation allows us to test several different designs before going into product testing,” says Benjamin Blanchard, validation leader at Faurecia. “This saves us a lot of money and reduces the experimental tests.”
Using Simcenter 3D has allowed the team to deliver higher-quality components in time to customers by enabling them to rapidly design and analyze multiple solutions before a physical prototype is ever built. The strong associativity with CAD allows updates to be made quickly and easily. As a result, they can streamline the delivery of innovations amongst teams and to customers.
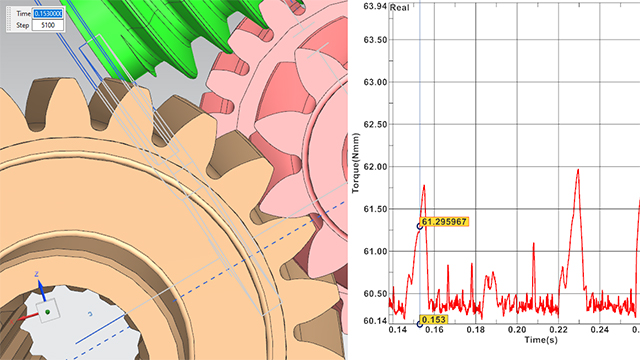
Breadth of solutions
Although Simcenter 3D is being heavily used in the design of seat mechanisms, Faurecia is also taking advantage of the breadth of solutions offered by Siemens to maximize their simulation investment. Using NX™ Open software, Faurecia is working to customize and automate certain processes in order to reduce the amount of time spent on simulation. One example is defining 3D analytical contacts between parts. This process takes about 10 minutes when performed manually. However, using NX Open, the team has been able to reduce this process to one minute. Additionally, preparing a seat model takes one month using the current process. But the team is working on reducing this to one week with Simcenter 3D, a 75 percent reduction.
Another Siemens solution the team is exploring is HEEDS™ software, a design space exploration software package. The team hopes to accelerate innovation by using HEEDS in conjunction with Simcenter 3D.
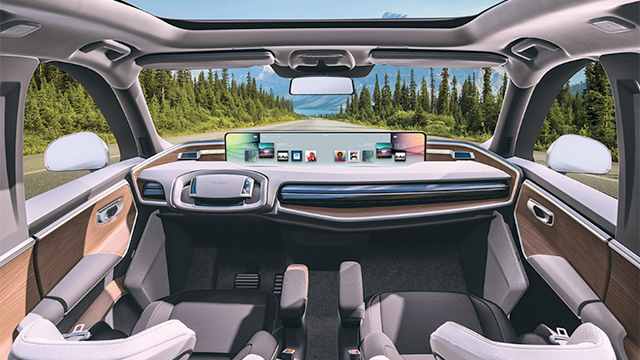
Going forward
Faurecia expects vibration and acoustics to become ever more important characteristics in the Cockpit of the Future. As a result, its simulation methodology team is exploring the integration of additional Simcenter 3D acoustics and vibration capabilities. Engineers are currently using experimental, physical testing methods to measure vibration and acoustics. In addition to being time-consuming and expensive, measurements for vibration and acoustics tend to be much more subjective based on user perceptions. Therefore Ben-Tkaya wants to use simulation to help Faurecia determine more objective, quantifiable criteria for the future. “Our goal is to expand the use of Simcenter 3D at Faurecia targeting systematic use of functional simulation in the design process for any new products, such as recliner, tracks, etc.,” he says. “Key for success for this strategy is extensive use of NX Open automation scripts.”