PCMs: it’s all about phase shifts and thermal gains
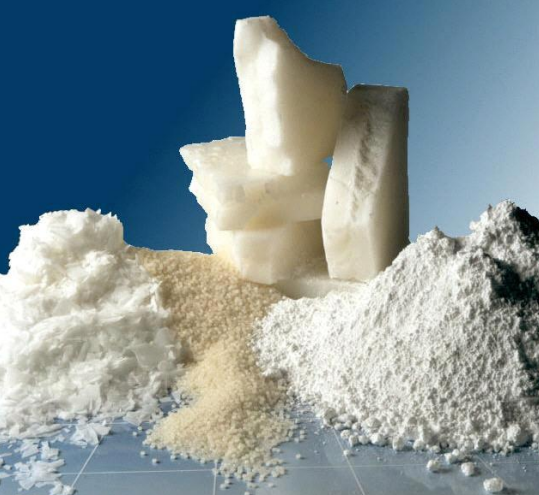
Phase-change materials (PCMs) are substances that have the remarkable ability to absorb, store, and release large amounts of thermal energy during their phase transitions, such as melting and freezing. These unique thermal storage properties have made PCMs increasingly valuable in a wide range of industries and applications, from building insulation to battery thermal management.
One area where PCMs have shown great promise is in the design and optimization of heat exchangers. By incorporating phase-changing materials into heat exchanger systems, engineers can create more efficient, responsive, and versatile thermal management solutions. This is particularly important in industries like HVAC and automotive, where the ability to effectively capture, store, and release thermal energy can lead to significant improvements in energy efficiency and system performance.
In this blog, we will explore the use of phase-change materials in heat exchangers, examining how system simulation can help unlock the full potential of these innovative thermal storage solutions.
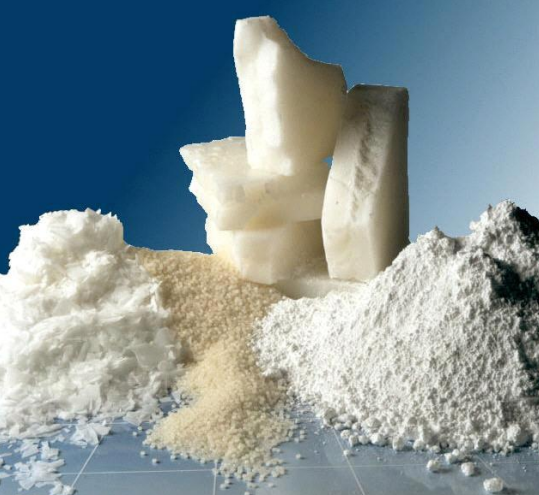
How do PCMs work?
Phase-change materials are substances that can absorb or release heat when they change phases, such as from solid to liquid or liquid to gas. This property makes them useful for storing and releasing thermal energy.
Here’s how they work:
- Melting: When a phase-change material gets warmer, it reaches a certain temperature where it starts to change state (like melting from solid to liquid). At this point, the PCM takes in a lot of heat without getting much hotter. This heat helps break the bonds between the particles in the solid, turning it into a liquid.
- Storing energy: After the PCM fully becomes a liquid, it can keep this hidden heat for a long time, giving a reliable and efficient way to store thermal energy.
- Freezing: When the PCM starts to cool down, it goes back to its solid state. This time, it releases the stored heat into the surroundings. This process also happens at a nearly constant temperature.
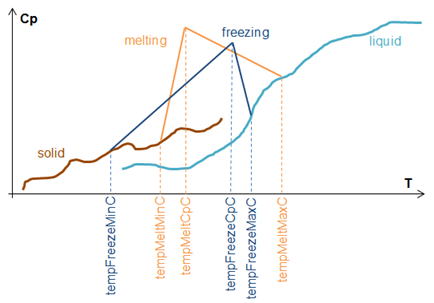
This technology is being explored intensively in the mobility industry (automotive and aerospace) and in the residential HVAC industry.
Recent trends in PCMs
There a 3 major trends among phase-change materials which are development of advanced materials, microencapsulation and integration with new energy systems.
Innovative materials include:
- Organic PCMs made of paraffins and fatty acids, known for their high latent heat storage capacity and chemical stability. Recent advancements focus on enhancing their thermal conductivity and reducing supercooling.
- Inorganic PCMs where salt hydrates and metallic alloys are being developed for their high thermal conductivity and volumetric latent heat storage. Innovations aim to mitigate issues like phase segregation and corrosion.
- Composite PCMs that combine organic and inorganic materials to leverage the benefits of both. For example, incorporating nanoparticles to enhance thermal conductivity without compromising storage capacity.
The microencapsulation of phase-change materials in micro or nano-sized shells prevents leakage and improve thermal cycling stability. This trend is particularly prominent in building materials, textiles, and electronics cooling.
Finally, phase-change materials are increasingly used in conjunction with solar thermal systems, wind energy, Batteries and other renewable sources to provide efficient thermal energy storage solutions. This integration helps in balancing heat supply and demand, enhancing the overall efficiency of renewable energy systems.
Role of simulation in engineering PCMs
Simulation tools play a crucial role in the design, optimization, and application of phase-change materials. in particular it enables to quickly and relatively inexpensively explore the technical possibilities offered by these materials. Here’s how:
- Thermal Performance Analysis:
- Simulation software allows engineers to model the thermal behavior of phase-change materials in various applications. For instance, in a heat exchanger, simulations can predict how different PCM layers affect temperature stabilization and heat transfer efficiency.
- Optimization of Material Properties:
- By simulating different compositions and configurations, engineers can optimize the thermal conductivity, latent heat capacity, and phase transition temperatures of PCMs. This helps in selecting the right material for specific applications.
- Design of PCM-Integrated Systems:
- Simulations help in designing systems that integrate PCMs, such as building envelopes, electronic cooling systems, and thermal energy storage units. Engineers can evaluate the impact of PCM thickness, encapsulation methods, and placement within the system.
- Performance Under Dynamic Conditions:
- Real-world applications often involve dynamic thermal loads. Simulation tools can model these conditions to ensure that phase-change materials perform effectively under varying operational scenarios. This includes transient analysis to study how PCMs respond to changes in temperature over time.
- Cost and Efficiency Analysis:
- By simulating different design alternatives, engineers can perform cost-benefit analyses to determine the most efficient and cost-effective PCM solutions. This includes evaluating the trade-offs between thermal performance and material costs.
Case study: Impact of phase-change material PCM on a heat exchanger
In this case study, we explore the impact of incorporating phase-change materials into a heat exchanger system. The primary objective is to control the temperature of air on the warm side of a wall cooled by a refrigerant fluid. This example demonstrates the significant differences in thermal performance between a traditional aluminum wall and a PCM-enhanced wall.
System description and corresponding Simcenter Amesim model
The system under consideration consists of a wall with two configurations:
- Traditional Wall: A full aluminum wall discretized into three layers.
- PCM-Enhanced Wall: Two layers of aluminum with a layer of PCM (Rubitherm RT-9HC) sandwiched between them.
The refrigerant fluid is defined with two operational phases:
- In motion: The refrigerant temperature is set to -20°C with a heat transfer coefficient of 3500 W/m²/K.
- Stationary: The refrigerant temperature is at ambient conditions (20°C) with a heat transfer coefficient of 100 W/m²/K.
The wall temperature is initially considered at -10°C.
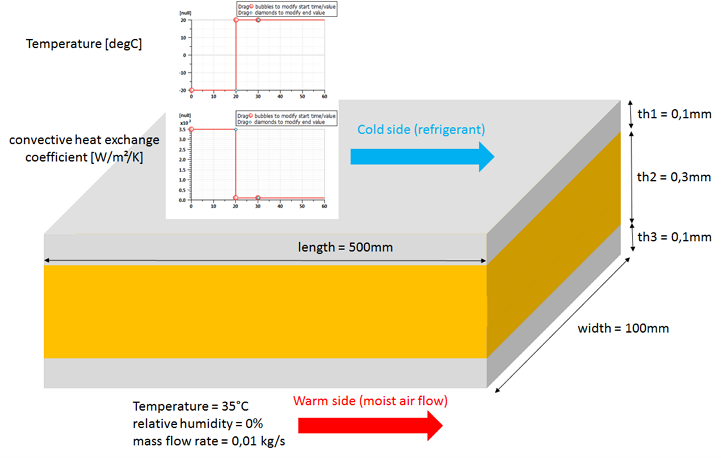
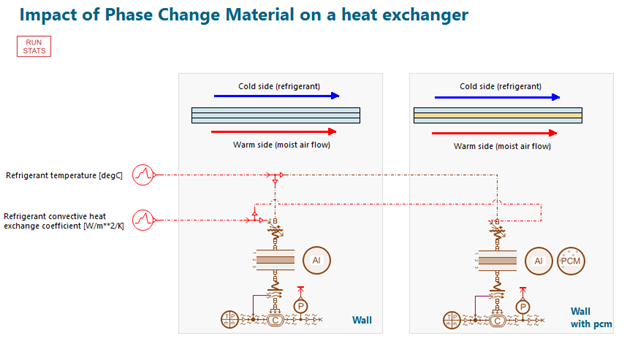
Simulation results and analysis
The simulation is run for 60 seconds and the refrigerant fluid is in motion during the first 20s, then it is stopped for the last 40s of the simulation. The aim of this simulation is to assess the impact of the phase-change material on the outlet air temperature evolution. The following figure shows the superposition of temperatures in the heat exchanger middle layer and in the heat exchanger air outlet with and without PCM. The impact of the phase-change material is clearly visible as the temperature increase of the moist air flow starts later when the refrigeration fluid is stopped.
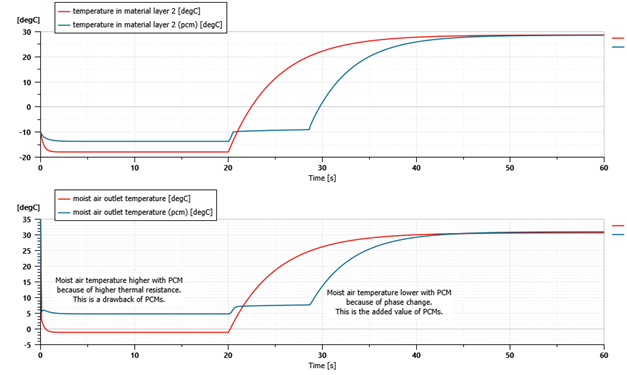
Indeed, when the refrigerant is considered in motion (from 0 to 20s), with a classic wall, the temperature of the wall is stabilized to a homogeneous value of -18°C and the moist air temperature is cooled to -1°C (red curves). With a phase-change material wall, each layer of the wall stabilizes to a different temperature, varying from -18°C to -9°C. This is due to the lower thermal conductivity of the PCM (0.2 W/m/K compared to 200W/m/K for pure aluminum) which translates into a higher wall thermal resistance.
When the refrigerant is stationary (from 20 to 60s), the wall heats up. The phase change is clearly visible with the PCM layer where the temperature reaches a stage where it is almost stationary (blue curves). This is the main interest of this technology: the moist air remains cool as long as 8.5s after the refrigerant fluid motion is stopped. Without phase-change material, the moist air temperature increases much faster.
Impact of phase-change material thickness
Further simulations were conducted to analyze the influence of PCM layer thickness on thermal performance.
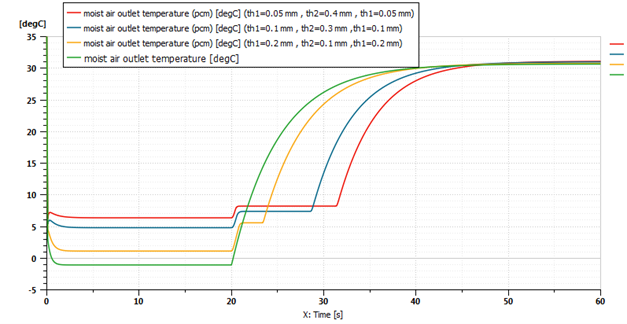
An increase of the PCM material lowers the performance of the heat exchange when the refrigerant is in motion (from 0 to 20s) because of the increased thermal resistance. On the other hand, thanks to the increased thermal capacity, the stage duration at which the temperature is stationary (from 20 to 30s) lasts longer when the refrigerant loop is stopped. The right thickness is therefore a matter of compromise between the heat exchange efficiency and the transient behavior of the heat exchange.
Example of application to electric vehicles
Lithium-ion capacitors (LiC) are considered as one option for high power vehicle applications due to their high power capability. However, thermal runaway associated with the LiC systems due to high-current solicitation can result in a considerable reduction of battery performance and life cycle. The purpose of a thermal management system (TMS) is to maintain the energy storage system at an optimum target temperature to ensure an optimal performance and life cycle tradeoff. In Karimi et al. Passive cooling based battery thermal management using phase change materials for electric vehicles (2020), a passive TMS using PCM is developed. In this regard, the passive TMS is designed, and the performance of the system is analyzed and validated utilizing Simcenter Amesim. The following figure represents the comparative study evaluating the performance of the TMS system. We can observe that adding Aluminum mesh grid foil (Al-foil) to the PCM successfully decreases the temperature in the module.
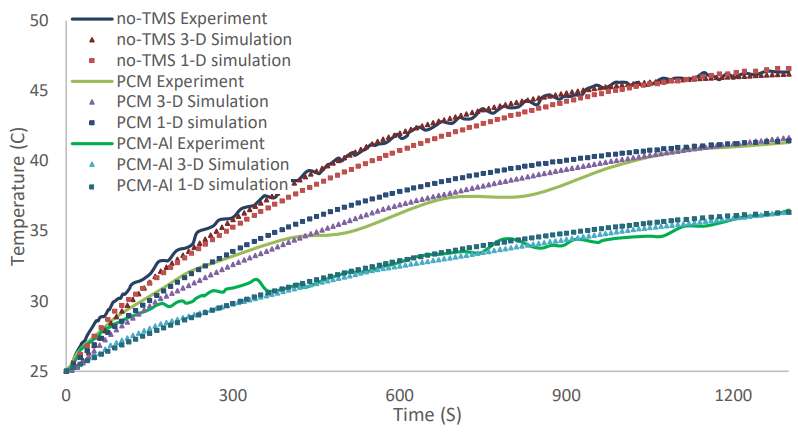
Conclusion
These case studies highlight the advantages of using PCMs:
- Enhanced Thermal Resistance: PCMs provide better thermal resistance, leading to more stable temperature control.
- Prolonged Cooling Effect: The ability of PCMs to maintain lower temperatures for extended periods after the cold flow stops is a significant benefit, especially in applications requiring consistent thermal management.
By leveraging Simcenter Amesim, engineers can design and optimize PCM-based systems more efficiently, ensuring they meet the specific thermal requirements of their applications.
Learn more about Simcenter Amesim
Simcenter Amesim is the leading integrated, scalable system simulation platform, allowing system simulation engineers to virtually assess and optimize the performance of mechatronic systems.