Optimizing NVH testing for SUVs at SsangYong Motor
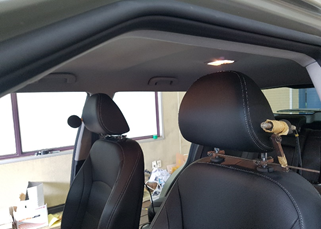
SsangYong is a South Korean automaker that accepts only the best performance and design for its world-renowned SUVs. The company is committed to maintaining an excellent driving experience for its customers by optimizing NVH.
Overcoming today’s SUV engineering challenges
Torsional vibrations are one of the main sources of noise and vibration in a vehicle. The torsional parts of a vehicle include all components that rotate, such as shafts or couplings. When these vibrations get too high, they cause the entire vehicle to vibrate and make more noise. The larger engines in trucks and SUVs exacerbate this problem.
As vehicles have evolved, so too has consumer preference. Consumers nowadays prefer quieter, smoother rides. This provides a more comfortable experience for the driver and passengers and it reduces the environmental noise created by cars.
In addition to NVH, many automakers struggle with the prototyping phase during the product development lifecycle. It is difficult to objectively define and measure data points, particularly when it comes to noise.
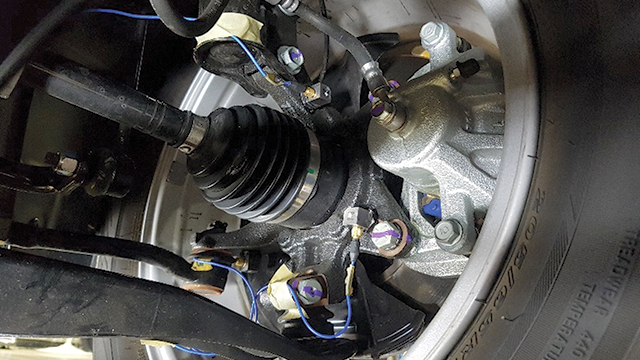
Finding the right NVH testing partner
SsangYong partnered with Siemens Digital Industries Software’s Simcenter Engineering team to identify and mitigate torsional vibrations in its new electric SUV.
“We needed a partner who would not only help us reduce the amount of noise and vibration in our vehicles, but also someone who would work with us to implement a process to measure and reduce noise. Simcenter Engineering was a perfect fit,” said Jaeyong Seo, principal research engineer at SsangYong.
Optimizing the NVH testing process
The Simcenter Engineering team immediately realized the physical testing process at SsangYong could be optimized. The team developed a strategy to support SsangYong in its overall implementation process, including the correct steps to take to validate and measure the changes they were making to the vehicle.
“The test results could be used to identify where the torsional vibrations were coming from,” said Seo. “Using the test data, we could analyze the torsional behavior of several components, including powertrain and the internal combustion engine.”
Building the models
After the physical testing process was defined, the Simcenter Engineering team helped SsangYong build and validate simulation models of relevant driveline components to be used in combination with the test data. With the developed models, SsangYong could easily complement and enhance their testing activities to gain more insight into the torsional vibration behavior of the full vehicle. This allowed SsangYong to easily understand which component modifications could help mitigate the noise issues, with the advantage of an easy interaction back to the design team.
“The Simcenter Engineering team not only build the models, but showed us how to do it ourselves,” added Seo. “I can now understand the torsional behavior of driveline components, such as inertia and stiffness, and how these will affect the full system behavior. Siemens helped me build the powertrain model perfectly.”
The simulation results for individual components correlated well with physical testing results, so the team moved into the next phase – building a full model of the SUV that SsangYong wanted to analyze.
SsangYong’s primary goal was to perform specific measurements on vibrations from the driveline and connect that to the feeling a driver or passenger would have in the vehicle. “We wanted to objectively measure and quantify which part was causing trouble and fix it,” said Seo. “This was another advantage of partnering with Simcenter Engineering.”
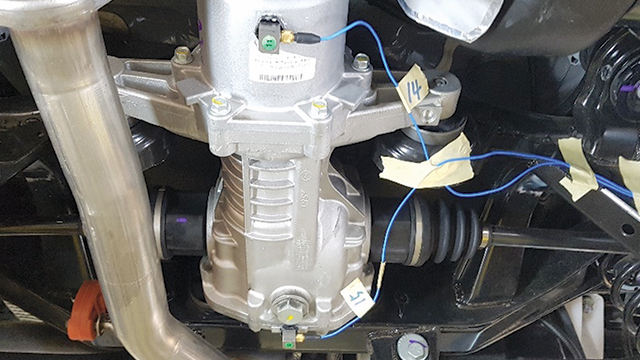
Rethinking the workflow
Simcenter Engineering also specializes in introducing methodology into the engineering workflow. This addresses issues such as where the problem is coming from and what additional technologies can be added both in the troubleshooting and in the design phases. This helps engineers better understand which part is causing the issue and needs to be fixed.
The Simcenter Engineering team worked with SsangYong to optimize the testing setup and reduce troubleshooting costs. Then they demonstrated how, using simulation, they could evaluate in detail which components were causing issues and how to update the design to solve them.
“Siemens made all of our models easy to use. They were very precise and helped us gather the vehicle data we needed in order to reduce vibrations,” said Seo. “The correlation of the simulation models with test data matched almost perfectly. Now that we have solved the issue of torsional vibration, we can move our vehicle into mass production.”
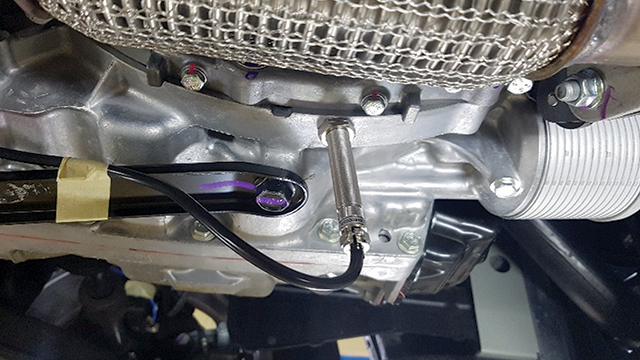
Making changes today for a better tomorrow
The project with Siemens provided SsangYong with a blueprint for future products. Now that the models have been created, the team will save time and costs developing the next generation of vehicles and be better equipped to address the issue of torsional vibrations.
In addition to improving NVH, SsangYong has also realized savings in vehicle weight. “Our work with the Simcenter Engineering team gives us the tools to reduce the weight and material needed to make an internal combustion engine,” said Seo. “We anticipate this will save us money and time on future projects.
“The knowledge we gained from working with the Simcenter Engineering team has been invaluable. Being able to optimize our vehicle with this project will have a positive effect on future projects, as we no longer need to build our entire process and models from scratch. We estimate that working with Siemens on this project will help us save over $200,000 on production of this vehicle.”

You may also enjoy these blog posts related to automotive NVH testing:
- MAB in engineering: A Hyundai Motor Company case study
- Excellence in electric vehicle NVH at Karma Automotive
- Is vehicle virtual prototyping possible? Predict your car’s NVH performance
- The 4 trends you should not miss in NVH engineering
To get in touch with Simcenter Engineering, email us at engineeringservices.sisw@siemens.com.