MCAM achieves hybrid additive manufacturing strategy for new medical device mold
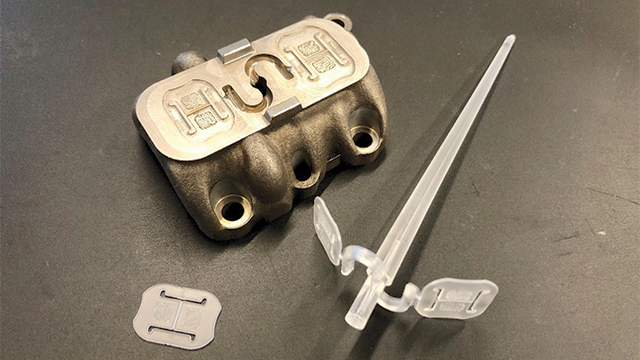
Medical device validation
In the medical device industry, validating a single new part can take up to three years. The extensive validation process often causes massive delays in products’ time-to-market, which can jeopardize a new product launch.
To address this issue, the industry is exploring additive manufacturing and high-end plastics to replace traditional manufacturing methods and materials. This approach allows companies to produce more parts at a faster pace and offers significant end-user benefits.
Plastics in medical devices
Compared to traditional materials such as metals, plastics are lighter and more affordable. Their material properties, including flexibility, transparency and barrier properties, make them ideal for many medical uses. In addition, plastics take significantly less time to produce. By using injection molding, companies can produce million of parts per year using multicavity tools. These tools are also extremely cost effective compared to other material and manufacturing techniques.
Finally, plastics offer much more design freedom than metals. They give engineers extremely high levels of precision and reproducibility. This makes them ideal for an industry that relies on absolute precision.
However, for making prototypes for validation, the precision required by the medical device industry makes plastic additive manufacturing a challenge. Due to technological shortcomings, plastic additive manufacturing technology as of 2020 is unable to support mid- to high-end plastic printing such as polyamides, polyacetal plastics and polyether ether ketone (PEEK) at the required precision level.
The promise of additive manufacturing
The team at Mitsubishi Chemicals Advanced Materials Plastics (MCAM) received a task to develop a new medical device for a client. Due to the limitations posed by current 3D plastic printing techniques, MCAM decided to 3D print a metal mold rather than print the plastic parts for the device itself.
Using this strategy, the team could balance the high precision required for the new part with the unique properties high end engineering plastic materials offer. At the same time, they could take advantage of the speed of injection molding.
Once this course was agreed upon, the only remaining issues for MCAM were the lead time to manufacture a new mold and the number of iterations the mold would need before any validation or testing could be set up.
“The time it takes to develop a mold is dependent on the complexity of the part, but for the mold we wanted to create, production time could take anywhere from 8 to 16 weeks,” says Kristof Declerck, project development engineer, MCAM. “On top of that, we typically go through two-to-three iterations per mold, and each iteration takes two-to-four weeks in addition to the 8 to 16-week development time required. This creates too much delay in the design validation stage for our customer.”
A hybrid approach
Driven by its customer’s needs, MCAM needed a solution to reduce the time for the mold prototyping stage. The mold would come out too rough using traditional metal 3D printing solutions with no post-finishing techniques. As a result, conventional post-finishing would be required, which would not sufficiently reduce the production time.
MCAM found a solution that addressed all the issues with traditional metal 3D printing in hybrid additive manufacturing. The team partnered with the Matsuura Machinery Corporation and invested in a LUMEX-Avance 25 hybrid metal 3D printing machine. This revolutionary new method of additive manufacturing combines 3D metal printing and finishing into one step. This reduces the lead time to produce mold inserts by up to 55 percent compared to conventional machining.
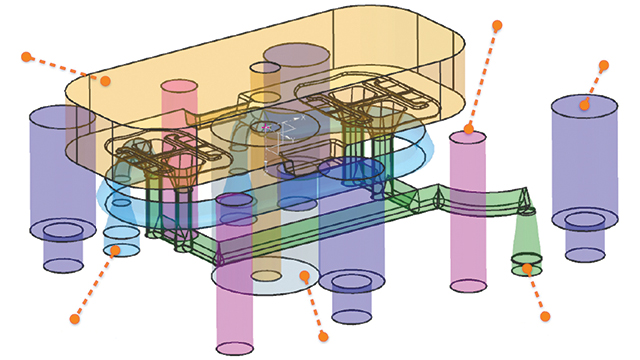
Smart design for additive manufacturing
Now that MCAM had found a printer to suit its needs, the next step was to reduce the build time. They realized the best way to achieve this would be to rethink the way they designed the mold inserts. The design added too much weight to the model, which increased the LUMEX-Avance 25’s build time. After experimenting with lattice-filled solids, MCAM discovered the benefits of topologic designs. This approach meant starting the design not from a block of material to be subtracted from, but from what the part required. This included parameters such as load, pressure, cooling and fixations.
MCAM partnered with cards PLM Solutions to take advantage of the NX™ topology optimization for designers software. By defining boundaries, requirements and constraints on the plastic part’s 3D model, the software calculated the force lines and defined where material would be required.
“Using this approach, we achieved a topologically optimized design,” says Declerck. “We were able to use only the exact amount of material that was absolutely necessary, which gave the strength needed for the application.”
Using the capabilities within NX topology optimization for designers, the MCAM team reduced material weight by 60 percent compared to traditional subtractive design. Additionally, this material savings offered MCAM and its customer significant benefits by further reducing the lead time from design to real injection molded prototype parts.
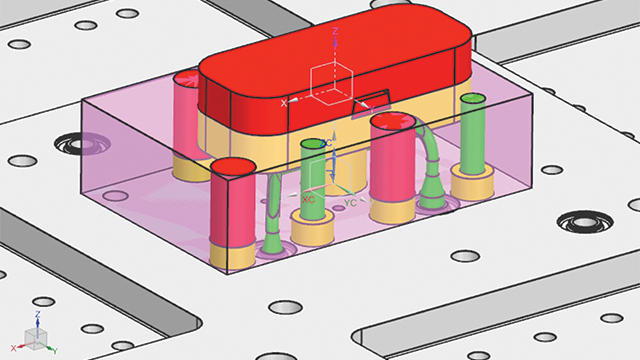
Validating the topologic design with simulation
To ensure the new design met its requirements, MCAM contacted the Simcenter™ Engineering software team at Siemens. The team needed to answer many questions before sending the mold to production. This included questions such as what would happen to the part under certain forces and pressures, whether it could hold such forces (such as internal stresses), and what type of deformation should be expected. If deformation was too high, cracking or openings could result and plastic could escape, which would ruin the entire part.
To validate the topologic design, the team built a detailed finite element analysis (FEA) model in Simcenter 3D software. Then, they used the linear analysis functionality of the Simcenter NASTRAN® solver to accurately calculate the structural performance. Using the Simcenter 3D postprocessing capabilities, the team compared simulated stress and deformation responses against their requirements. After that, the design was signed-off for production.
“Our partnership with the Simcenter Engineering team gave us the confidence we needed to build a first prototype on the LUMEX-Avance 25,” says Declerck.
Using NX topology optimization for designers and validating the detailed design with Simcenter NASTRAN, MCAM cut out unnecessary sections. As a result, they greatly reduced the amount of material used and the weight of the mold. “The new, optimized design took only 10 hours to produce, a significant time savings compared to the 20 to 24 hours required with the subtractive design method,” says Declerck.
“Furthermore, the structural behavior observed on the manufactured prototype corresponded well with the structural response predicted by the FEA simulation model. This verification step was important to establish confidence in the virtual sign-off procedure.”
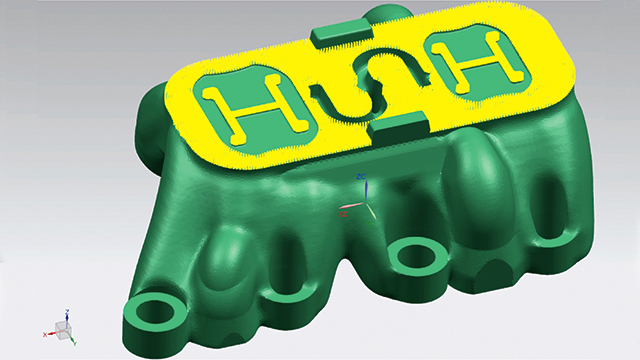
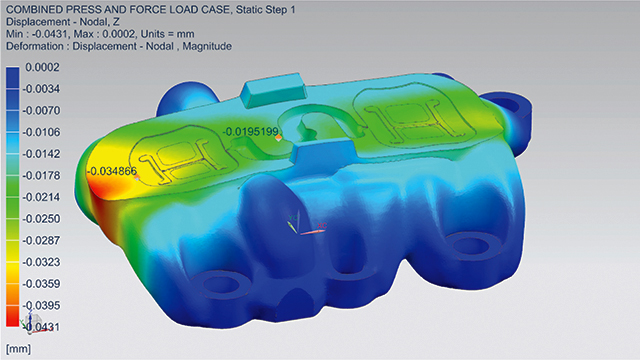
A new approach: The hybrid additive manufacturing strategy
Successfully completing this project gives the MCAM team confidence using this new approach. “We plan to use this approach in future projects using Siemens products for designing and validating complex mold systems,” says Declerck. “We are excited to work with the Simcenter Engineering team on future projects for validation.”
Medical device companies routinely use simulation to design and predict the performance of medical devices. However, MCAM’s approach demonstrates that the value of simulation extends further, including the design and production of the tooling for building the devices.
“It was critical at the start of this project that we gain complete confidence in the design before printing. When poor or incorrect designs are sent to the printer, it becomes very costly and time-consuming. Working with Matsuura Machinery, cards PLM Solutions and Siemens Digital Industries Software helped us prove that we can change the design of a mold and actually improve the product.”
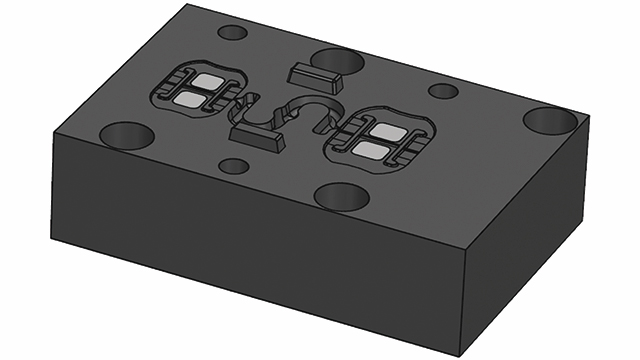
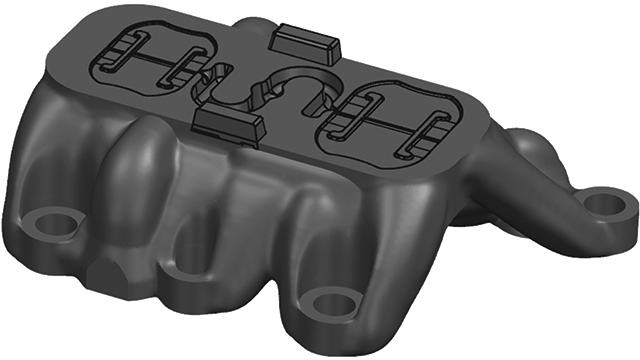
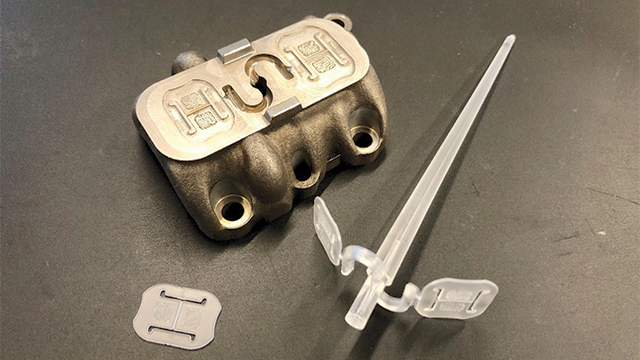
To get in touch with Simcenter Engineering, email us at engineeringservices.sisw@siemens.com.