MBST: the marriage of Test and Simulation – part 1
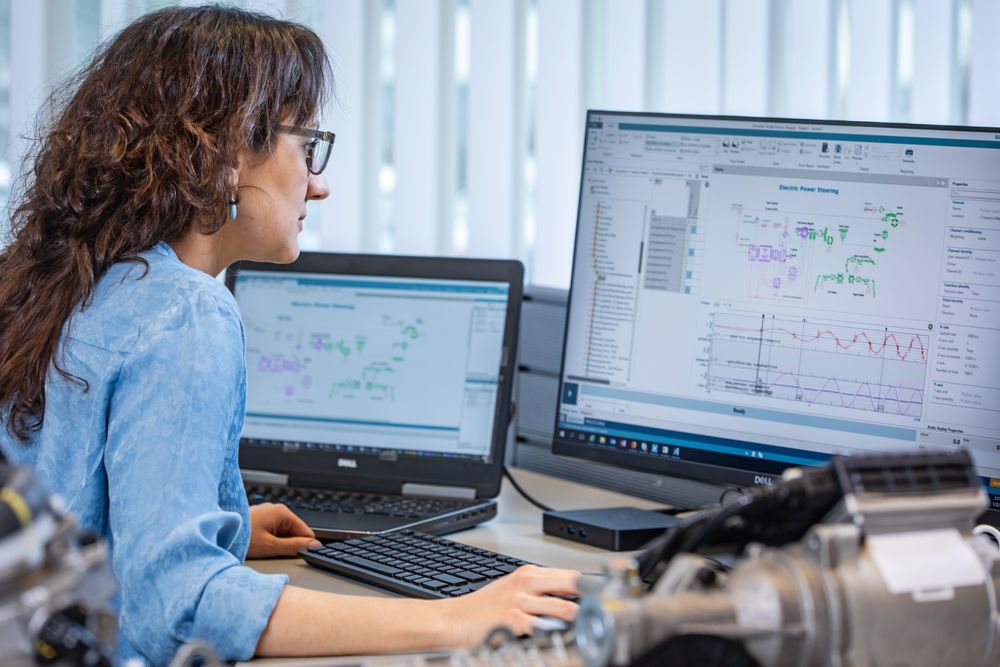
I had a very interesting conversation with a friend. He wanted to buy a car and he was quite sure about which one he wanted to purchase,… right up until the moment he realized that they offered an incredible number of variants and options to choose from.
“Did you know that you can define different engines, suspensions, and other options for the same type of vehicle? You can configure your dream car just by picking from a catalog!” Although his comment was perhaps a bit exaggerated, he had a valid point to make.
By comparing the complexity of a vehicle from nowadays to the ones from some years ago, we can say that the level of complexity in vehicle variants has increased by a lot. Take, for example, the number of new driveline architectures that have to be integrated in vehicles due to electrification and hybridization, and the additional boundary conditions that need to be taken into account due to the new regulations on energy efficiency and safety.
So many variants!
In this context, everyone will surely agree that repeatedly creating and testing the physical prototypes of a vehicle is an incredibly ineffective way for manufacturers to solve system design problems.
It is problematic for many reasons: a physical prototype is expensive, and having multiple vehicle variants physically tested and optimized is simply not a viable option; and on top of that, any modification made to the vehicle at that stage is going to be too costly!
How can they, then, overcome these problems?
The answer, believe it or not, is simple: intelligently combining test and simulation early on.
How easy would it be if we were able to evaluate system designs before having to build the prototype? Imagine evaluating vehicle performance already, even at this early stage!
Merging Test and Simulation would make it possible to identify defects or define better designs at an early stage. There would be a consistent cost and time reduction, and the overall quality of the product would certainly improve.
The good news is that this can be achieved by means of Model Based System Testing, or MBST for short.
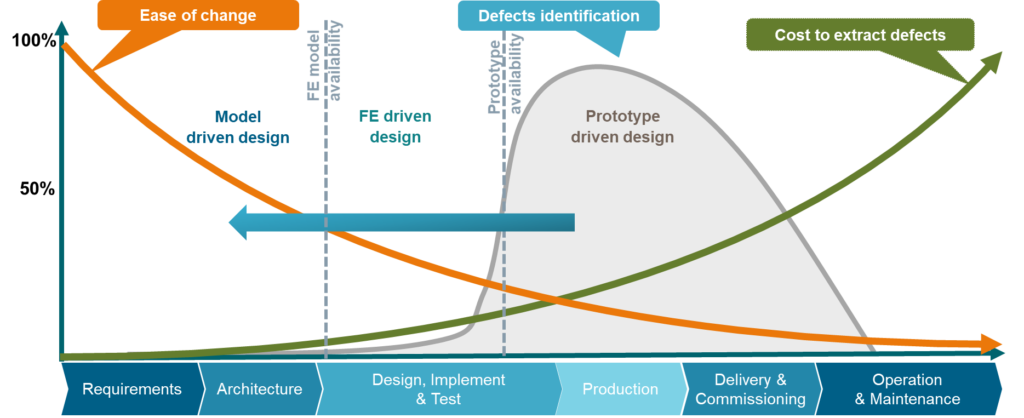
So Model-Based System Testing, huh?
Well, this is all possible thanks to MBST, yes.
It is a framework of engineering solutions made to enable and optimally balance the combined use of test and simulation throughout the product development cycle. MBST allows performing attribute engineering on virtual models, on virtual-physical systems and on physical prototypes.
From these solutions, three main categories can be established when combining test and simulation:
- Test for Simulation: test data is essentially used to build, validate, improve and drive simulation models.
- Test with Simulation: the physical and virtual worlds interact intimately to complement each other in multiple scenarios, such as system-in-the-loop (XiL).
- Simulation for Test: simulation models are used to expand test capabilities, improve and confirm test data. They can also be used as a pretest (virtual testing) to know the expected signals or levels.
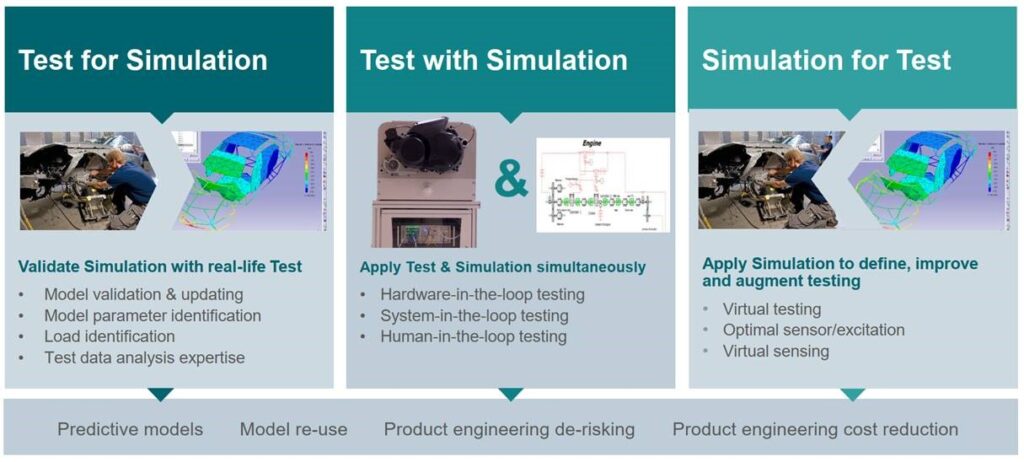
In this blog series, we are going to explore 3 different cases, one for each pillar. We’ll leave part 2 and part 3 for the upcoming blogs.
Let’s first start with the first one.
Test for Simulation
How can we use real-life test data for simulation purposes? This can be done in different ways: using test data as inputs to the digital twins, for validation or for further engineering analysis.
Let’s explain it with an application example. Have you ever heard about Vehicle Energy Management (VEM)?
Well, we all want to have an eco-friendly vehicle,… but only if it doesn’t impact the pleasure of driving. The main question is, then, how we can optimize the energy efficiency of a vehicle without affecting other performances, such as noise and drivability. Being able to assess the impact of system architecture choices on both energy consumption and performance early in the design is a key factor.
While the overall energy consumption in a vehicle is easy to compute, knowing how this energy flows inside the vehicle components is a challenge: multi-physics must be considered, and the models should take this into account. Thanks to those multi-physics models, we are able to access quantities that are difficult or impossible to measure directly on a bench.
Vehicle Energy Management usually starts with a top-bottom approach: from the global energy in the full vehicle, to the energy distributed at components level. Models are created using simulation solutions such as Simcenter Amesim (for the modeling and analysis of multi-domain systems) and Simcenter STAR-CCM+ (for Computational Fluid Dynamics – CFD – simulation), used to validate design decisions.
The following step is to evaluate the vehicle’s performance using an integrated test and simulation approach.
However, considering that VEM analysis cannot be done without simulation, the simulation models must be validated with test data to be predictable for VEM analysis.
MBST offers the possibility to execute productive parameter updating, avoiding endless design iterations, making the full process of data validation more efficient.
By using MBST we want to make sure that the phases of a development cycle are shortened, making the model available faster. Of course, we need to rely on a valid testing campaign.
In this specific example, a big variety of sensors are needed for input, such as temperature, current, pressure, torque, rpm, and CAN, just to indicate some. Simcenter SCADAS hardware support s all the different sensors for a full vehicle measurement campaign.
At the same time, the Simcenter Testlab software is used for data acquisition and much more!
To validate your model and identify the unknown parameters, you would have to transfer the test data into the simulation software solution.
However, the complete process described above can become iterative and it can result in a painful and slow process. Without simplifying the process, switching between test data, simulation models, and the multiple software required, the whole campaign can become a tricky mess.
How to avoid endless iterations?
How powerful would it be if we could access and process the simulation data directly in the test software (Simcenter Testlab)?
Well, MBST allows coupling testing and simulation environments to improve the estimation or optimization of the parameters, without involving any data transfer or format conversion.
The Amesim Sketch viewer introduces an easy way of accessing Simcenter Amesim model data within Simcenter Testlab. This allows users to post-process the results of simulated models using the complete set of metrics available in Testlab.
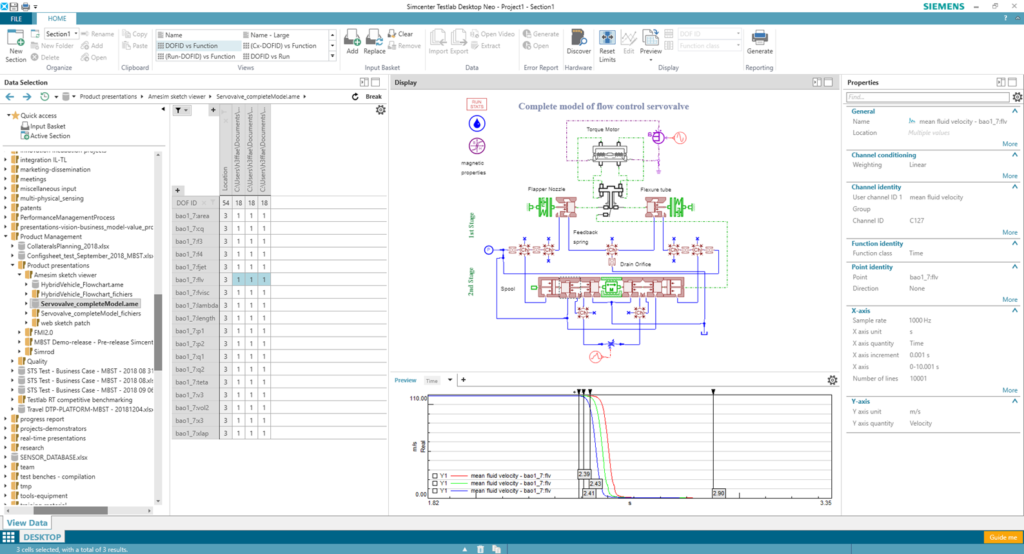
And if this would not be enough, the full Amesim model can be made available as a parametric executable digital twin, thanks to the support of FMI models (called FMUs). This allows the user to execute the model from within Simcenter Testlab and to optimize or update its parameters, until the test and simulation results match.
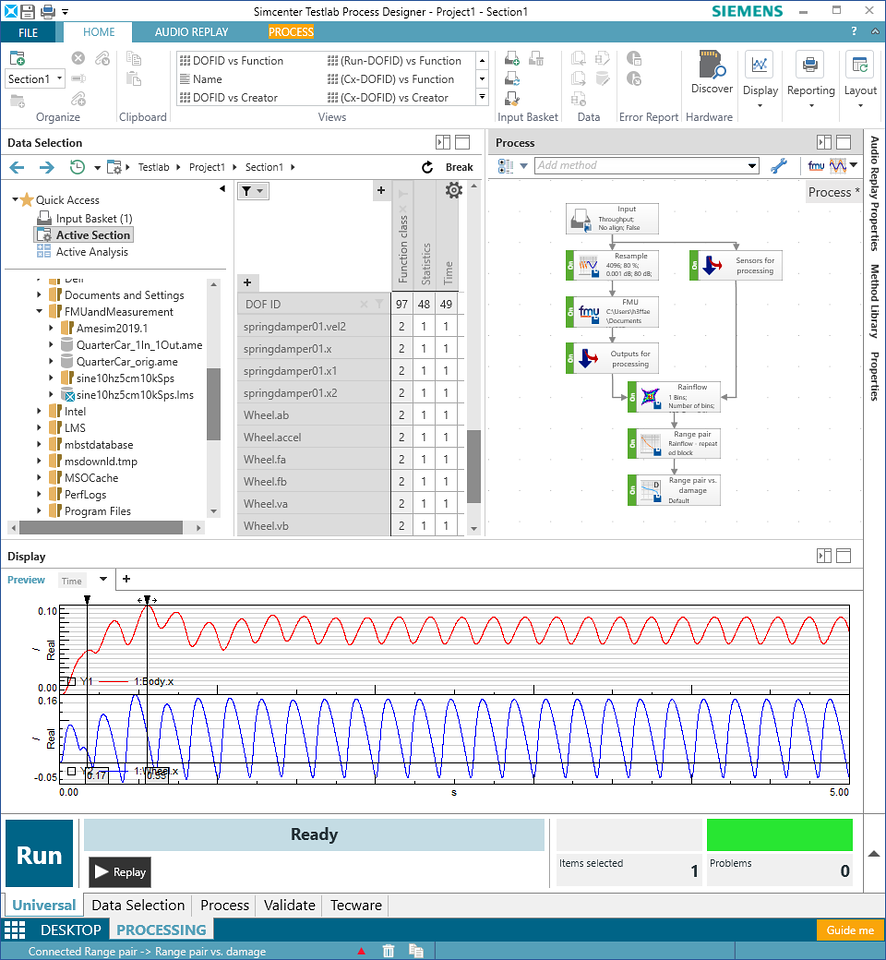
All these points will make the model validation process much more efficient and error-free.
More about MBST, please!
The gains that MBST can bring are clear. The complete process is more efficient and faster, and errors usually made during data transfer or post-processing can be entirely avoided.
We advice to keep an eye out for part 2 and part 3 of this blog series, where we will discuss Simulation for Test and Test with Simulation.
But if you want to know more about MBST right now, then check out the white paper.