Finding the edge in electric transmission design

How a customized simulation workflow can set you apart from the competition
This blog was co-written with Jan Deleener, principal engineer at Siemens Digital Industries Software
Automatic transmissions are a complex feat of engineering. They contain many components – gears, clutches, brakes, torque converter – and are activated by hydraulic systems, making them a very challenging application to build. But manufacturers that spend the time and money to master them can easily stand out above the competition.
However, the advent of electric vehicles has led to much more simplified transmissions. There are no clutches or brakes and no shifting between gears. You just press the accelerator pedal and increase your speed. While this may seem like a good thing, it means that those masters of the previous more complex transmissions risk losing their competitive edge. If it’s much easier for anyone to build, it’s much harder to develop the differences that single them out as a cut above the rest.
Finding these fine margins requires more detailed analysis of every aspect of the electric transmission. Building prototypes of every option would make the design cycle far too long, especially when getting new products to market ahead of the competition is critical. Previously, development time for a new automatic transmission was typically three years. Now, to keep up with the market, manufacturers need to reduce this to under two years. To achieve this, Simcenter Engineering Services created a simulation workflow that scans all the design possibilities, such as the sizing of the gears and their micro geometry, and helps engineers find the optimal configurations early in the development cycle.
Sizing and positioning
Transmission design begins with a set volume that it must fit within. Inside, designers have complete freedom to position and size components such as the shaft and gears. HEEDS generates various configurations that fit the volume constraint before moving to the next step.
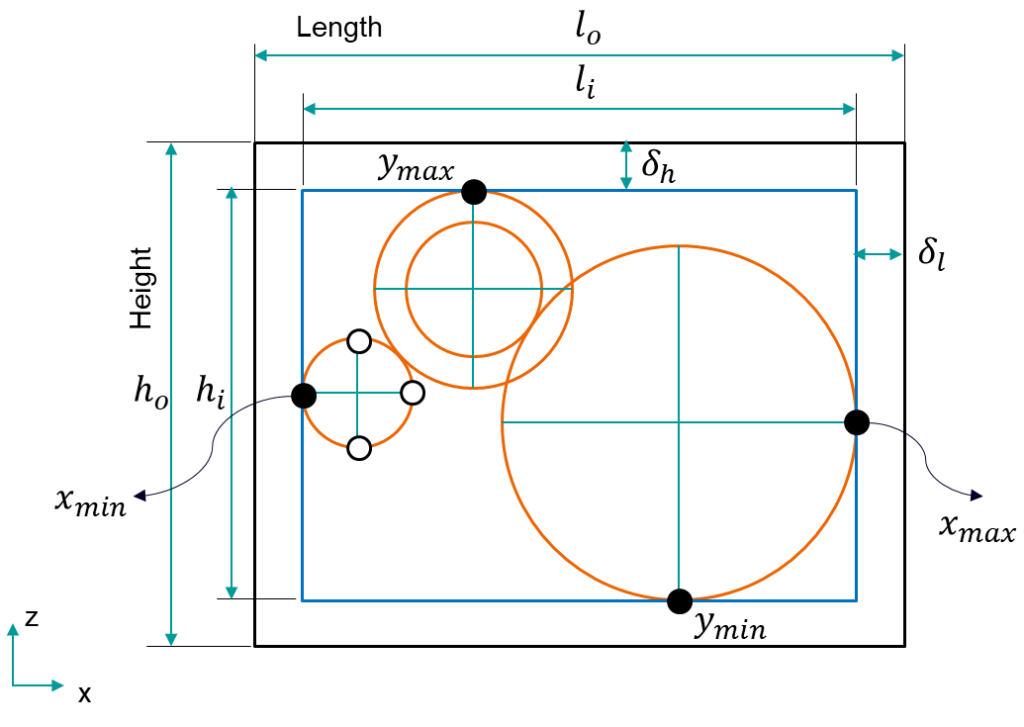
Using Simcenter 3D Motion, engineers build a completely parameterized layout to check interference packaging. This identifies if there will be issues with gears randomly shifting and interfering with the bearing. Unlike most design tools, Simcenter 3D Motion calculates the time domain while still including flexibilities calculated in frequency domain making it easier to incorporate all the physical details.
Reducing weight without misalignment
Reducing weight is important for overall performance and can be done by making shafts flexible instead of stiff. However, this creates more possibility for misalignment which will generate unwanted noise when high torque is applied. Therefore, optimization is vital to minimize this misalignment while allowing flexibility. Engineers use Simcenter Nastran to represent the effect of flexible shafts while HEEDS acts as the master of the workflow, determining the parameters and working with NX Nastran to generate the mesh before the time domain calculation.
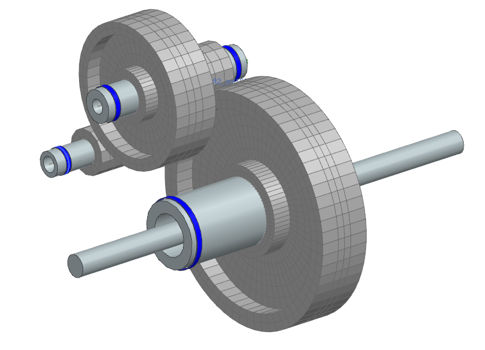
Fine tuning
Simcenter 3D Motion Gear Design Optimization software links Simcenter 3D Motion and HEEDS to fine tune the design, focusing on the microgeometry of the gear teeth to eliminate NVH issues due to misalignment. Reducing the material by just a few microns can make enough of a difference to mitigate noise caused by vibration. Simcenter 3D Motion Gear Design Optimization enables this fine level of detail and completely parameterizes the microgeometry of the gears.
This also helps reduce transmission error caused by variation in the stiffness of the teeth. Forces from Simcenter 3D Motion are extracted in the time domain and automatically applied to a finite element model of the gear to obtain the stress under load – vital to durability.
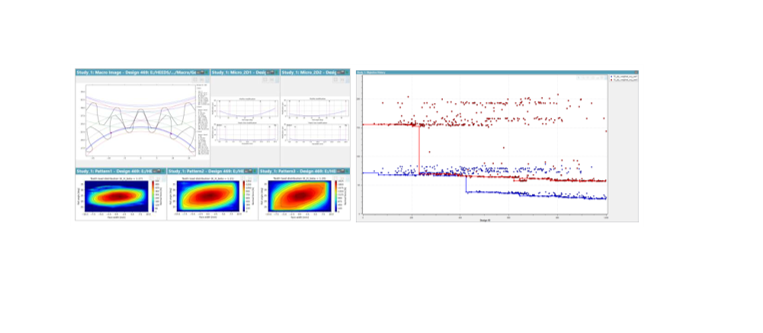
Complete transmission simulation
The complete workflow means that it is not only the gears that are simulated but the full transmission, including detail of the shaft to account for the effect of bending or flexing. The risk of NVH issues is typically determined by the transmission error, but also the bearing forces are evaluated which are typically a better indicator of the total noise generated. As a result, engineers can set a limit for these bearing forces to ensure that these noises do not exceed targets.
While each tool is essential to the workflow, HEEDS is the key that seamlessly links each analysis. With the unique hybrid and adaptive algorithm called SHERPA, significantly fewer model evaluations are required compared to other leading methods. HEEDS allows for easy modification of every geometrical parameter simultaneously to scan a much broader design space.
These solutions are all available as part of the Simcenter portfolio for engineers to create their own workflows that best fit their design processes. However, many customers choose to collaborate with experts from Simcenter Engineering Services to better understand how to get the most value from the tools. This ensures that all the possibilities from the portfolio are explored so that workflows are customized to meet their exact requirements.
To get in touch with Simcenter Engineering Services, email us at engineeringservices.sisw@siemens.com.
Learn more about how to improve NVH performance
Hyundai Mobis uses simulation to enable faster and better transmission design choices. Read more here.