1.2M kilometers. Can you picture the distance?
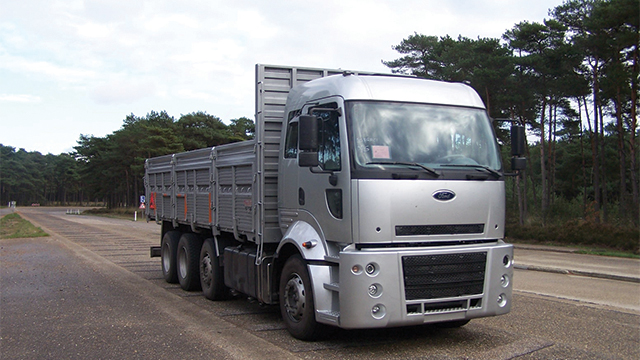
It is already 7 years since I joined the virtual durability engineering team. ‘Virtual’, as we work from diverse geographic locations and all have different backgrounds: industry specialists, technical testing experts, simulation gurus, engineering smart heads, product and industry marketing specialists. Although we all report to different groups within the company, we combine our strengths and efforts for a common interest and goal.
During one of our first meetings, I remember the durability testing automotive specialists buzzing with excitement about an interesting project for a truck manufacturer in Turkey. They had successfully executed extensive field tests for validating the durability performance for a new road truck. Experiences were shared and follow-up plans were made, but somehow this never materialized in public material. Until earlier this year, when our virtual group was reinforced with a new team member coming from Ford Otosan, the same truck manufacturer for which we delivered that outstanding project. And guess what? The company is still following the engineering approach we had set up years ago and deploys our software and hardware tools for their durability programs.
Durability testing automotive manufacturer dreamed of
What was so extraordinary about the project? In a nutshell we performed, together with Ford Otosan, dedicated data collection, applied extensive load data processing techniques and developed an accelerated track sequence and a 4-week accelerated rig test scenario that matched the fatigue damage generated by 1.2 million kilometers (or 720,000 miles) of road driving.
1.200.000 kilometers… can you picture the distance? That is 30 times the circumference of the earth, from pole-to-pole. Or to the moon and back, and yet again to the moon. It is an astronomical amount of kilometers. Just crazy.
It is also ingenious. Instead of doing an actual road test and driving 1,000 kilometers per day for more than 3 years, Simcenter Engineering experts deployed effective durability test scenarios based on actual customer use. This methodology is called customer correlation and maps real customer vehicle usage that considers varying road conditions, multi-cultural driving habits, climate conditions and vehicle loading implications. With an ideal mix of actual measurements and accurate statistics, the correct road loads parameters are determined in order to set accurate durability testing targets for next-generation vehicles.
You can read it all for yourself in the Ford Otosan story. As a sneak preview, this is what Murat Arslan, Vehicle Durability Supervisor of Ford Otosan, says about his cooperation with the Simcenter teams:
“Simcenter Engineering experts developed a target durability test track sequence that accurately replicated the excitation of the actual road and significantly reduced the amount of time that would have been required for road testing.”
Murat Arslan

Left: Proving ground tests to ensure traceability and repeatability. Right: 4-poster durability rig test.“Simcenter durability testing software enabled us to set specific objectives for the load sequences, such as minimizing the time required to perform the tests or achieving the best correlation regardless of the time involved.” Murat Arslan
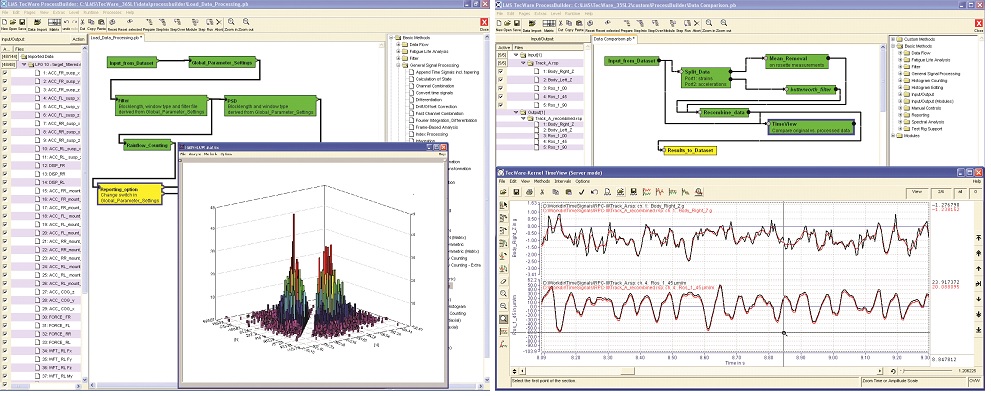
Left: Rainflow counting to classify the applied loads with durability perspective. Right: Enabling automated repetitive tasks.
The combination of test, simulation and engineering services is what differentiates Simcenter solutions. Doing so, we help manufacturers deliver lighter, stronger and more durable designs, while accounting for geographical differences and reduced vehicle weight.
>> Read the compelete case study of Ford Otosan here.