CFD-FEA coupling in Simcenter – lowering pressure and stress
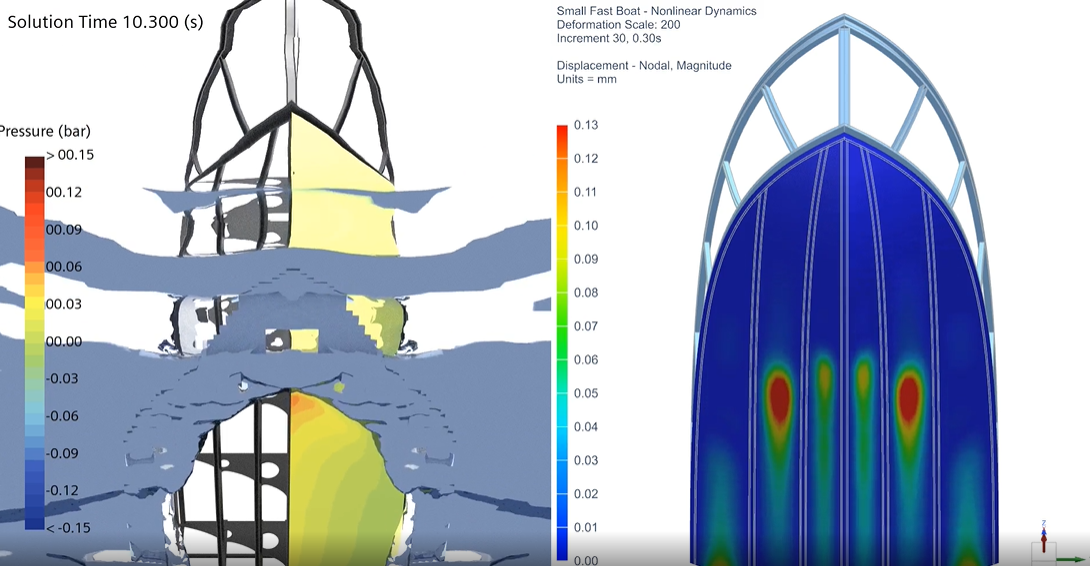
For engineers to collaborate effectively on multidisciplinary applications, being able to transfer results quickly, easily, and reliably from a Computational Fluid Dynamics (CFD) model to a structure mechanics Finite Element (FE) model is crucial. With Simcenter STAR-CCM+ 2206 we introduce a common data format for an efficient transfer of simulation results to Simcenter 3D (CFD-FEA coupling).
Model the complexity of multiphysics applications
Mechanical engineering is an engineering branch that combines engineering physics and mathematics principles with materials science, to design, analyze, manufacture, and maintain mechanical systems. (Source: Wikipedia)
According to the definition above, mechanical engineering is about the design and analysis of mechanical systems. But before it’s even possible to design or analyze any mechanical system, a detailed understanding of the operating conditions and expect service loads is a must.
Example of a recent engineering disaster
Being unable to predict operating conditions and service loads have led to countless engineering disasters. A fairly recent one is the sinking of the MOL Comfort in the Indian Ocean. This event took place on June 17, 2013.
CFD-FEA coupling can help to predict service loads and operating conditions for Multiphysics applications. Continue to read this blog to find out how to use the results of a CFD model to define the service loads of a structure mechanics FE model.
CFD-FEA coupling for a boat hull structure
A boat with an overall length of 5.5m and a total weight of 1600kg (800kg boat only) is driving at 5 m/s through a series of waves with a height of 1m. The objective is to analyze the deflection of the bottom panel of the hull in a practical manner.
CFD-FEA coupling to analyze the deflection in a practical manner
Fluid dynamics and structure mechanics models are often built by different analysts. A process that enables a smooth and efficient CFD-FEA coupling is key.
From a physics perspective, it’s reasonable to assume that the deflection of the panels is small compared to the rigid body motion of the boat. Therefore, we may assume that the deflection of the panels will not have a significant impact on the flow.
In other words, we may assume that the panel deflection is 1-way coupled in the direction fluid to structure. The fluid pressure deflects the panels, but the deflection of the panels doesn’t affect the flow.
Stay integrated with CFD-FEA coupling in the Simcenter environment
Set up your CFD model in Simcenter STAR-CCM+
The first part of the process is to set up the Computational Fluid Dynamics (CFD) model in Simcenter STAR-CCM+. Here we assume that the boat is rigid, and therefore we can model it as a six degree of freedom (6DOF) body. The mass, center of mass, and moments of inertia of the boat are an input for the 6DOF model. And they may be taken from the FE structure model.
Export your simulation results to the Simcenter Data File
While the boat floats through the waves, Simcenter STAR-CCM+ exports the pressure on the bottom panel of the hull is being to a file. Not any file, but a Simcenter Data File with the extension .scd5. The export of simulation results to the Simcenter Data File is a new feature of Simcenter STAR-CCM+ 2206.
Simcenter STAR-CCM+ exports the panel pressure on the native Computational Fluid Dynamics (CFD) mesh and the sampling frequency matches the time step size of the flow solver. Therefore, for the given model, the exported Simcenter Data File may be thought of as a persistent data source with the highest possible fidelity in space and time.
Import the pressure in Simcenter 3D
Next, the CFD engineer hands over the Simcenter Data File to the structure mechanics analysts. This team imports the hull pressure into the Simcenter 3D. After the import, Simcenter 3D stores the pressure within the simulation file as a Table of Fields.
The frame of the boat is assumed to be rigid. Hence, a fix constraint is applied wherever the bottom panel is connected to the frame. The imported fluid pressure is defined as a load and automatically interpolated in space and time. As solver Simcenter Nastran Solution 401 is being used.
An efficient CFD-FEA coupling
The animation below shows the bottom panel of the hull from a diver’s perspective for the duration of about one-third of the wave period.
- In the left part of the animation, we can see the fluid pressure computed with the help of the Simcenter STAR-CCM+ CFD model.
- In the right part, we can see the panel deflection from the Simcenter Nastran 401 model.
Predict service loads and operating conditions
Go faster with efficient data exchange across Simcenter products
The example above demonstrates how a CFD-FEA coupling method can help to predict service loads and operating conditions for Multiphysics applications. Furthermore, it also demonstrates that being able to export simulation results from Simcenter STAR-CCM+ to the Simcenter Data File for a subsequent import into Simcenter 3D is extremely valuable.
Run a productive and efficient workflow
Admittedly, coupling, a Computational Fluid Dynamics (CFD) simulation to a structure mechanics FE simulation through a file is nothing revolutionary. However, the presented workflow has some subtle points to consider:
- The fluid pressure is exported to the Simcenter Data File on the native Computational Fluid Dynamics (CFD) mesh at every time step of the flow solver. The result is a persistent data source of the highest possible fidelity in space and time.
- The Simcenter Data File is imported into Simcenter 3D once. Then the data is being interpolated in space and time onto the Simcenter Nastran 401 model. Therefore, should the structure mechanics analyst want to investigate a different design of the structure (a different frame) there is no need to re-iterate with the flow analyst, not even to re-import the hull pressure.
The two points above may appear subtle, but they are essential for a productive and efficient workflow. The Simcenter Data File is the only component that needs to be exchanged between the flow and the structure analyst. Hence, the required interaction and exchange of simulation results is kept to an absolute minimum.
Additional Simcenter STAR-CCM+ 2206 top features will be revealed soon, keep watching!
In the meantime, check out these latest releases: