Closing the gap between the Digital Twin and physical hardware with system-in-the-loop testing
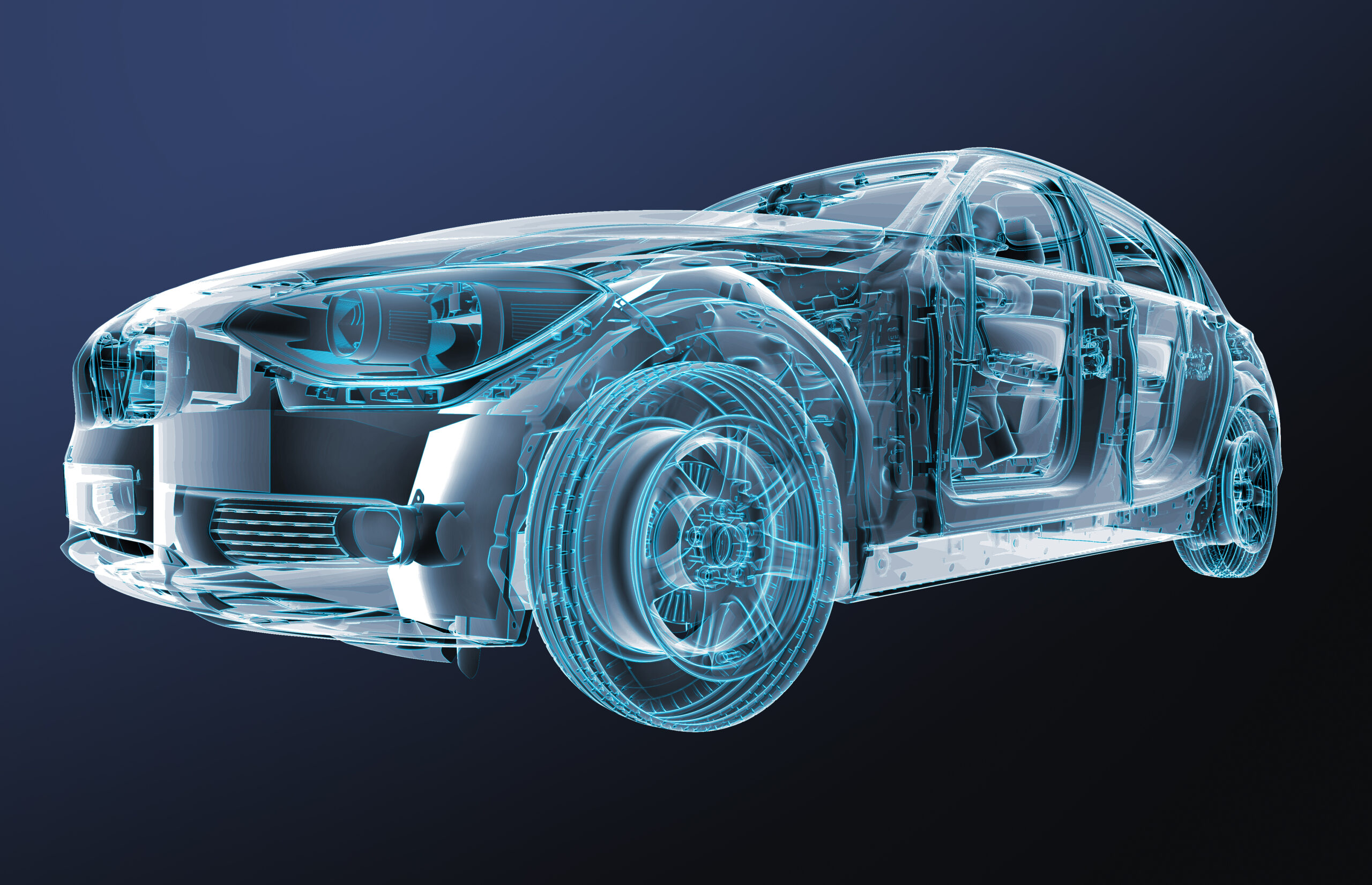
Automotive engineers today are faced with a conundrum: While the complexity of vehicle engineering has exploded, expected time to market has decreased rapidly.
Engineers must account for more factors in vehicle development than ever before:
- Increasing vehicle variants. You’re not building one car, you’re building many versions of the same car (ie different powertrains, etc). This makes the job of a test or integration engineer much more difficult, as more scenarios, environments, and components must be tested in a short amount of time.
- Increasing system integration. As vehicle complexity increases, so too does the amount of systems involved. It is crucial to ensure that all systems work correctly and are integrated.
With the ever-increasing number of variations and complexities, discovering integration issues late in the design stage is costly and negatively impacts time-to-market.
At Simcenter Engineering Services, we believe that a seamless combination of test and simulation is key to addressing these challenges.
The shift to MBD
To avoid late troubleshooting of integration issues, manufacturers are seeking to shift the workload emphasis from test and troubleshooting to system simulation.
Model-Based Development (MBD) pushes the boundaries of vehicle performance evaluation, enabling engineers to address integration issues much earlier in the development process through the use of simulation. Let’s explore MBD more in the graphs below:
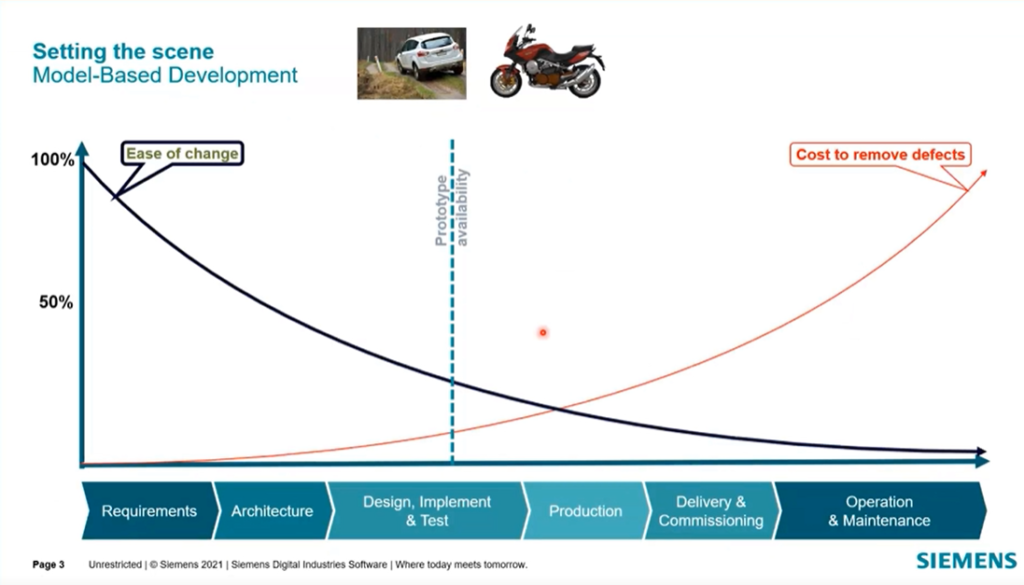
The image above shows a flattened V-cycle from requirements to the final vehicle. Clearly, it is very expensive to make changes late in the V-cycle. If you can identify issues earlier in the cycle when you are still setting up requirements, selecting architecture, etc, it is easier, less costly, and more efficient.
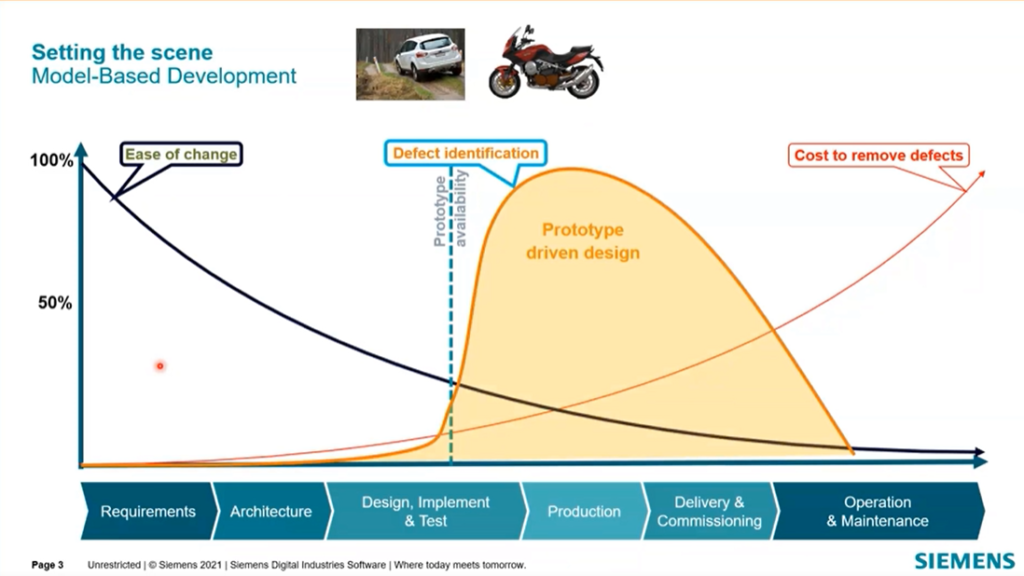
If a company makes a change only when a prototype has become available, the cost increases significantly.
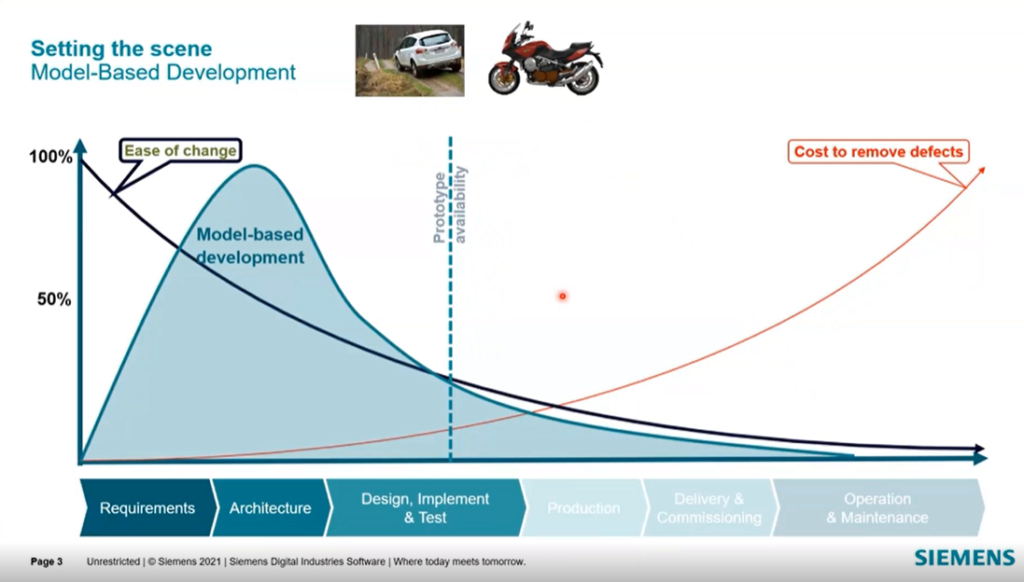
Shifting to the left of the V-cycle through MBD at the full vehicle level resolves most of these issues. However, you can’t do everything with models. There are some parameters, such as friction values for NVH and driveline issues, that are difficult to control before doing a test. It is possible to make predictions using design, but the only way to get the true parameter value is through testing.
In our on-demand webinar “System-in-the-loop testing – a revolution for vehicle integration,” we address the critical question:
How can engineers close the gap between the digital twin and physical hardware?
System-in-the-loop testing – a revolution in vehicle integration
Watch this webinar to learn how Simcenter Engineering Services’ system-in-the-loop testing approach can help you:
- De-risk subsystem integration by combining simulation and test
- Upgrade your test bench to XiL to evaluate variants more efficiently
- Use test data to build, validate, improve and drive simulation models
- Use simulation models to define, validate and complement testing procedures and test data
By connecting product development stages, manufacturers and suppliers will be able to accelerate time to market, master system engineering complexity and boost the vehicle’s performance.
Additional resources: