Is my EV battery going to fail?
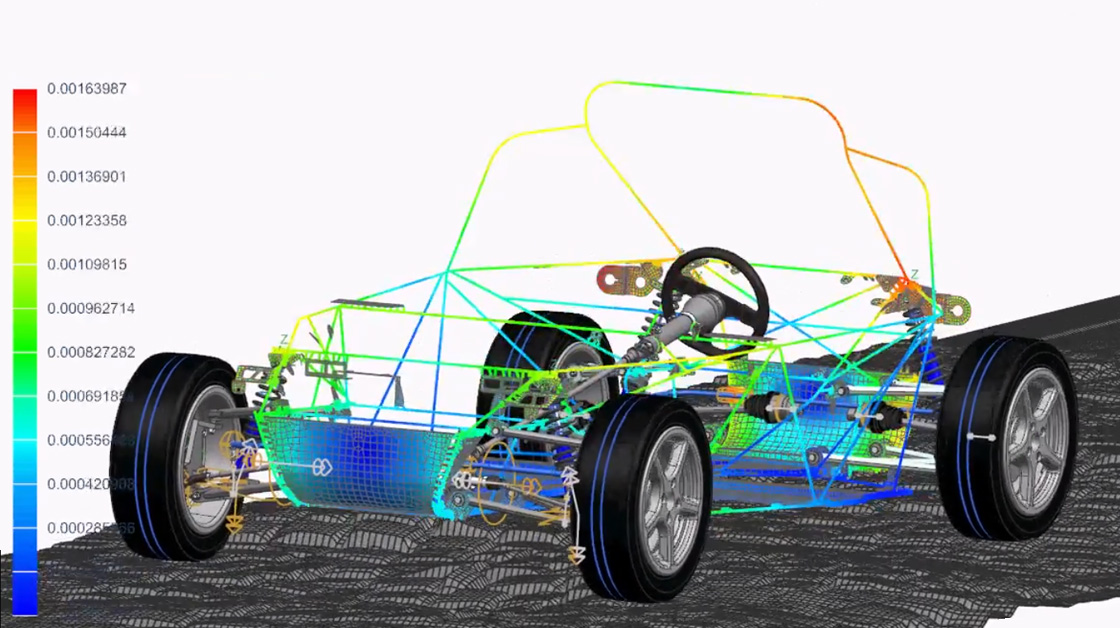
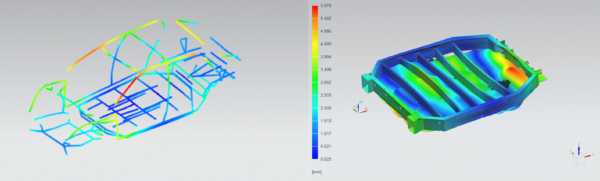
In the context of vehicle electrification, the automotive industry is taking several key steps to ensure the safety and durability of vehicle batteries. Rigorous testing protocols are in place to evaluate battery performance, thermal management and response to abuse conditions like overcharging, short circuits, and crashes. Battery ageing is being looked at intensively, and even more is battery thermal runaway, for very good reasons.
The key to properly managing these requirements is front-loading the design. This means using Digital Twins to predict these effects early on in the design process, thereby minimizing the cost of physical testing and troubleshooting.
But what about structural durability?
Typically bolted below the body, the battery experiences the same loads as the body when the vehicle rolls over potholes, cobblestones and speed bumps. This repetitive loading will lead to accumulated damage in the structure of the battery frame and cause premature failure and high cost if not engineered appropriately.
In another blog post, we discussed battery vibration tests. We introduced a step-by-step approach to determine relevant test scenarios and loading conditions, and avoiding over-testing to control the costs.
But can we do more? Can we apply the same strategy of front-loading battery durability using Digital Twins, allowing us to predict and understand the structure’s behavior early on?
Our simulation expert, Dirk von Werne, investigated this and came up with a process allowing us to do so. This process leverages our testing solutions to identify the proper loading conditions and our know-how in numerical simulation.
Besides front-loading, it allows us to understand the effect of the body to which the battery is attached. Indeed, the battery is reinforcing and interacting with the body structure. As they form an integral structure together, the loads that the battery experiences are much dependent on the stiffness and eigenmodes of the full system. This leads to complex load scenarios and responses during driving, that are not easy to replicate in component testing. The ability to include these effects in simulation allows us to engineer a better battery considering the coupling to the body, and to develop an improved accelerated test scenario for component testing.
Finally, this approach also allows us to minimize the mass of the battery pack without compromising durability. Indeed, the battery is one of the heaviest (and most expensive) components of an electric vehicle.
So, let’s have a look at how we address this engineering challenge and the multiple benefits of this approach!
Duty cycle and loads
As a starting point, you have to define the mission profile that you design your vehicle for. Standards are available to support this, but they only represent a typical usage and might not fit with a specific vehicle under development, a given target market, etc. Therefore, collecting data in relevant test conditions on a relevant vehicle should be considered whenever possible. This can be done, for instance, on a predecessor vehicle. Many scenarios can be considered: how many kilometers one will drive on the highway, in the city, or on a smaller road with cobblestones? What speed ranges to take into account? Which driver profile: comfort driver or sportive driver? All in all, finding the proper loading conditions for a vehicle under development is far from an easy task!
Simcenter Testlab Mission Synthesis is a software that condenses the loading scenarios from years of operation to an equivalent accelerated test cycle. This allows you to understand the “damage potential” in many different conditions and synthesize your “test profile” much better. This can then be used for validation testing and also in a simulation context, where these loads are used as input to the Digital Twin of the structure.

Knowing the stress
In the world of automotive durability, simulation processes are very well established based on decades of vehicle engineering. Using predecessor knuckle forces or actual road surface profiles as an input, you can simulate the vehicle behavior in a multi-body simulation environment, such as Simcenter 3D Motion, deriving stresses and interface forces at the battery attachment.
A Finite Element simulation in Simcenter 3D will assess the damage and life prediction of the battery frame based on the loads at the attachment points, modal stresses to be used in time or frequency domain response analysis, and the superposition of load cases. Damage hotspots will be post-processed and their local data can be analyzed in detail.
Yes, but… the battery is a very complex structure, including special materials, many connections, and some non-linearity. The battery’s structural coupling with the body structure is strong. For those reasons, applying the “classical” approach described above is not straightforward. This is where Simcenter Engineering comes in, with its experience in both testing and simulation.
As Dirk explains, “You need to understand how the structure really behaves when subject to vibration loads. You can expect that a battery has a non-linear behavior, and need to find the best approach to capture it in your Finite Element model. Thanks to our large experience in combining test and simulation, we can support our customers in defining proper assumptions. Modeling guidelines can be defined based on the correlation of the physical battery with the simulation model, and adapting the model until the match is good enough. In the end, you get a Digital Twin that provides a reasonable representation of the actual battery”.
The overall process for battery structural durability assessment is shown below:
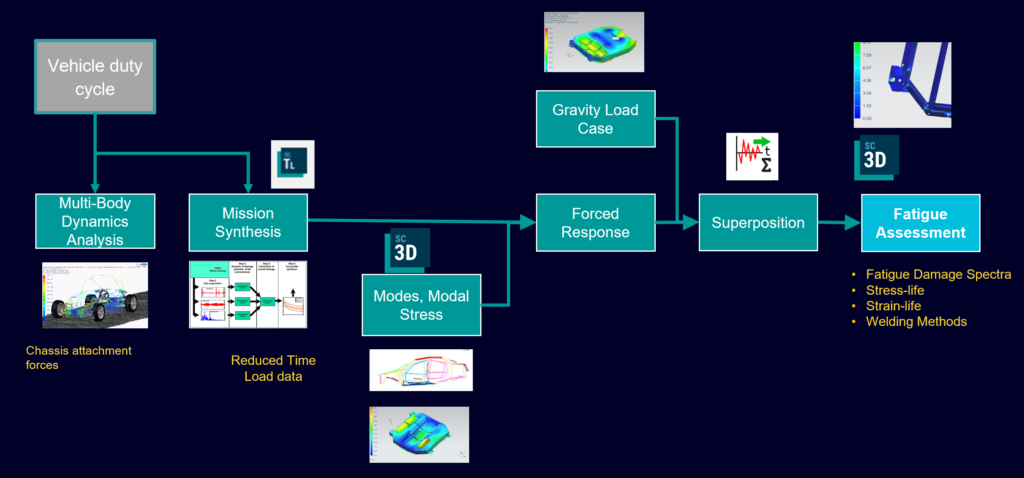
An optimal solution
As mentioned before, there is tremendous pressure in reducing vehicle weight, in order to maximize the range. Numerical optimization enables to do this.
To allow for an optimization, the durability prediction has to be fast enough to be looped in an automatic optimization process. This requires to balance the model size with the accuracy. One way to do this is to represent the Body by means of a reduced representation as a superelement.
The optimization process shown below is driven by HEEDS, part of the Simcenter portfolio. A typical objective of the optimization is to reach the lightest possible battery frame while ensuring good durability performance. Typical optimization parameters include the cross sections and material thickness of the battery frame, as well as the bolt positions of the attachment to the body.
All this becomes possible by parameterizing the CAD geometry in NX and building up automatic meshing, analysis and post-processing. The optimization in HEEDS is enhanced using AI.
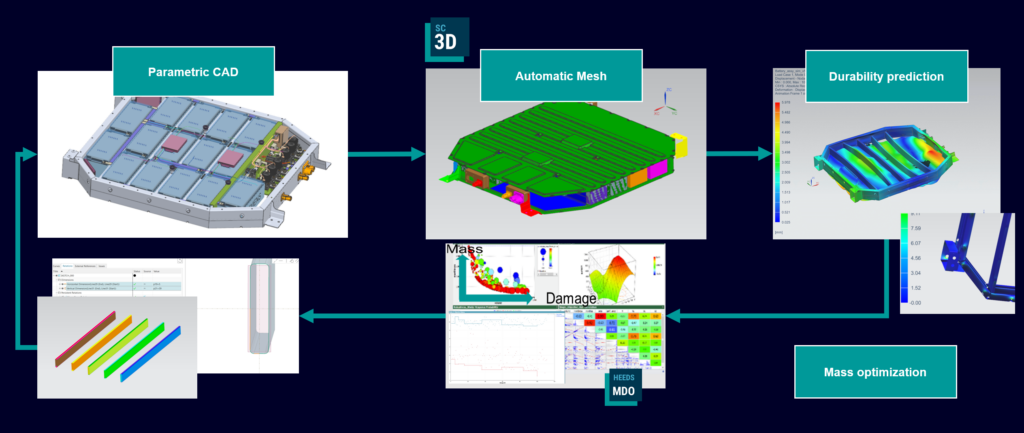
Conclusion
In this blog post, we introduced a process for CAE-based durability analysis of an EV battery.
Durability simulation allows frontloading the mechanical design, optimizing the structure and developing a valid accelerated scenario for component testing.
What’s in it for you?
- Obtain improved design earlier thanks to a CAE-based process
- Avoid conservative approach and reduce mass
- Improve and shorten battery testing
And no, your battery is not going to fail!