Increasing design efficiencies of electronics with Digital Threads
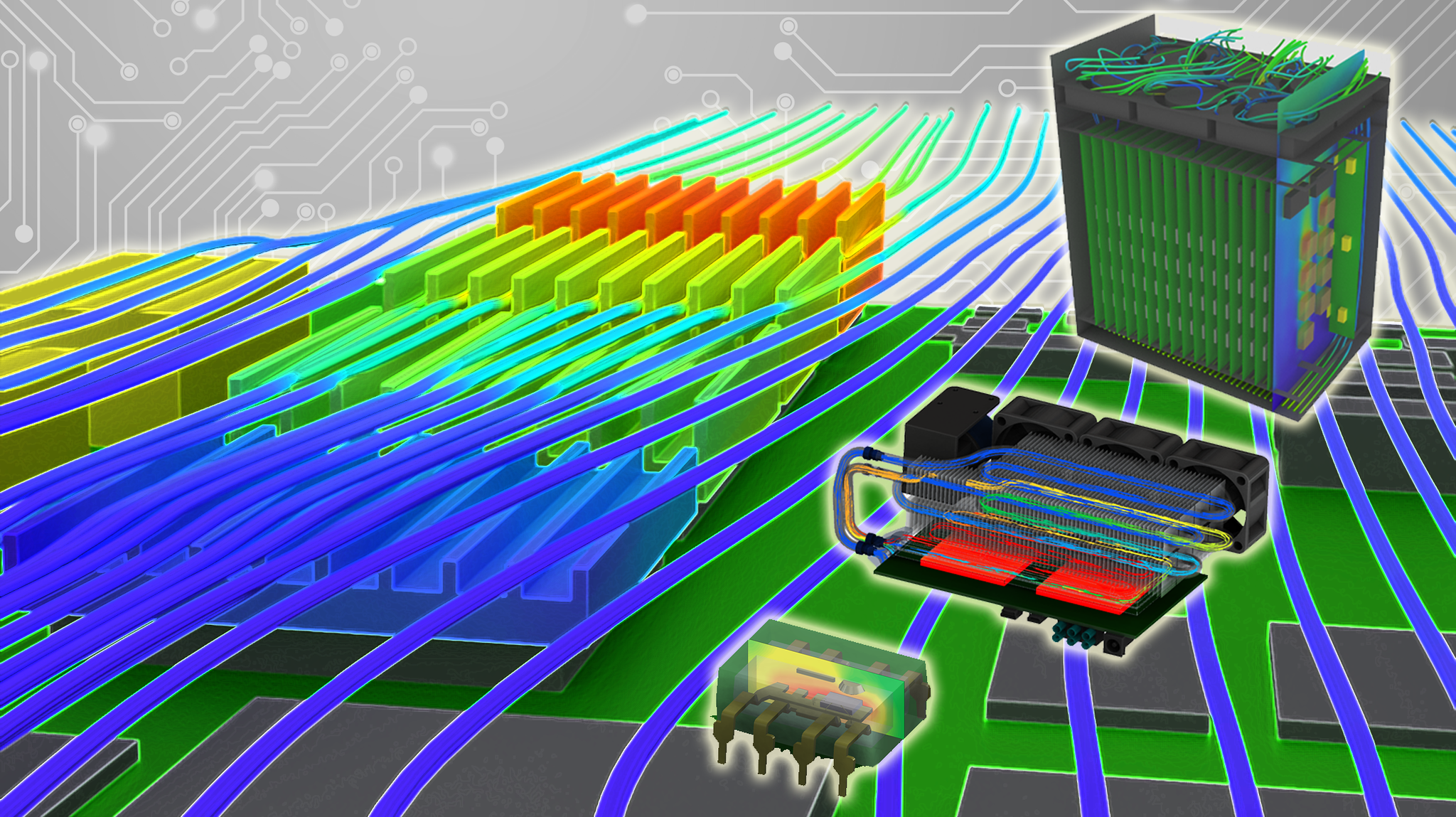
In the fast paced and ever evolving landscape of the electronics and semiconductor industry, small and medium sized businesses (SMBs) face a variety of challenges and opportunities. From navigating complex supply chains to keeping pace with rapid technological advancements, SMBs must continually innovate and adapt to remain competitive. One key strategy that holds immense potential for SMBs is the adoption of a digital thread. The digital thread represents a holistic approach to managing product data and information throughout the lifecycle of any product, from design and development to manufacturing, distribution and beyond.
What is a digital thread?
A digital thread refers to the seamless exchange of digital data throughout the lifecycle of a product or process. At the heart of the digital thread concept lies the seamless flow of data and information across various stages and functions within an organization or across different organizations. For SMBs, where collaboration between design, engineering, manufacturing, and supply chain teams is crucial, a digital thread can offer numerous benefits.
Benefits
Firstly, there would be improved collaboration and communication between different teams and departments by breaking down silos which typically exist in most organizations. Improvements in efficiencies and reduction in errors and delays are possible.
Having a centralized platform for managing product specifications, engineering and CAE design data, and test processes and data, is crucial to ensuring seamless communications between teams, accelerating time to market.
The key enabling technologies supporting the digital thread include product lifecycle management systems (PLM), product data management systems (PDM), mechanical and electronic computer aided design software (MCAD and ECAD), Computer Aided Engineering software (CAE) are some examples. By leveraging these technologies, organizations can improve their ability to innovate, optimize their processes and deliver high quality products and services to their customers.
Siemens Xcelerator
There is a comprehensive suite of software and test hardware within the Siemens Xcelerator portfolio which can accelerate digital transformation and support the creation of a digital thread for the electronics and semiconductor industry.
There are the EDA design tools which help with PCB (Xpedition) and IC (Xpedition Package Designer and Xpedition Substrate Integrator) design. There are also signal and power integrity analyses tools which are used to evaluate and validate designs prior to manufacture. Electromagnetic simulations and rules based electrical design verifications for designers are also available in the Hyperlynx Product Family.
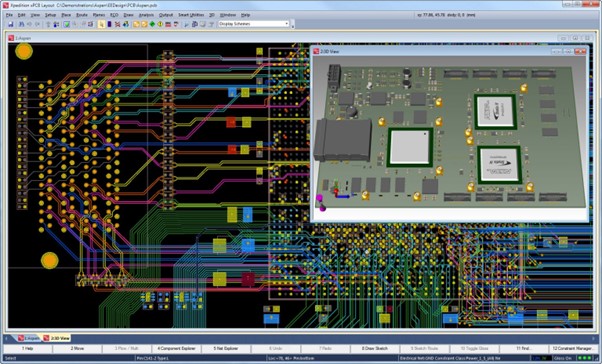
These ECAD designs of PCBs can be seamlessly transferred into NX via the PCB Exchange tool. 2D layouts of the PCBs and ICs are converted into 3D objects. Simcenter 3D, which is an integrated multidisciplinary CAE tool that is built on the NX platform, can also be used to import in the IC and PCB files. The main advantage of using Simcenter 3D is that the ECAD and MCAD data will be combined together in a common CAD and CAE environment.
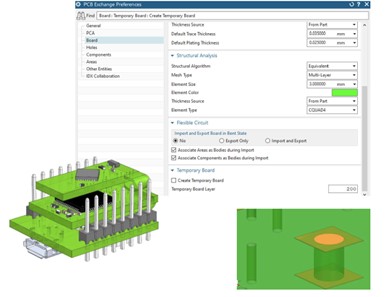
Thermal and Structural Analyses
Thermal management and design have always been an important consideration in the semiconductor and electronics industry. By incorporating thermal management considerations into the digital thread, SMBs can optimize their design and manufacturing processes to address thermal challenges directly, ensuring reliability and performance of their products whilst minimizing the risk of thermal related issues and failures.
Simcenter FLOEFD, the CFD and thermal analysis tool, is fully integrated into NX and Simcenter 3D. This means that the ECAD data can be directly used for thermal analysis directly without having to perform any file conversion. Simcenter FLOEFD can perform a full conjugate heat transfer analysis (conduction, convection and radiation) on the electronics assembly. Temperature hot spots developed within the model can be identified easily. Simulations can also analyze the system under adverse operation conditions such as extreme temperatures, high altitudes with reduced air densities etc. This would be a prove quicker and cheaper than creating physical prototypes and testing them.
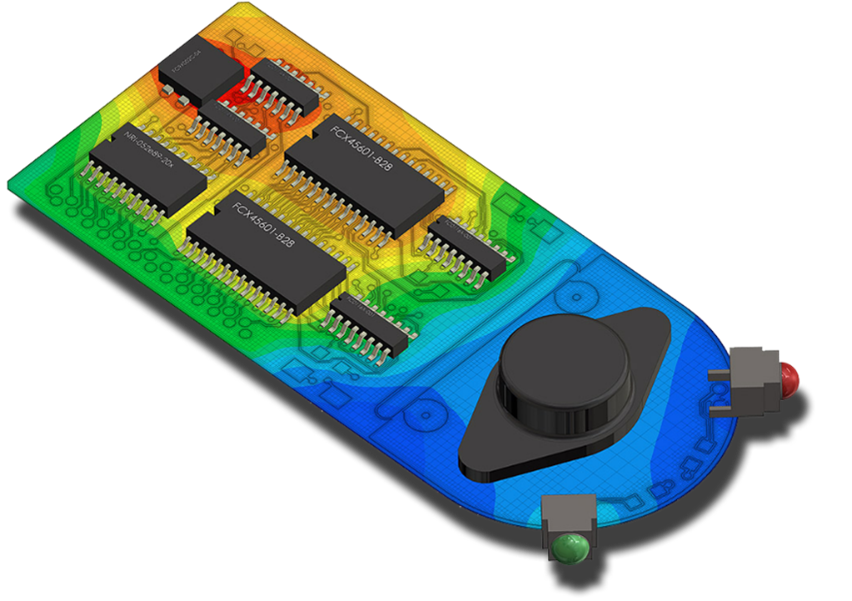
Electro-thermal co-simulations can be performed between HyperLynx and Simcenter FLOEFD to determine the DC or Voltage drop analyses in electrical circuits. Voltage drop analyses are important for the purposes of voltage regulation in electrical circuits, as excessive voltage drop can lead to malfunctions or improper operation of devices connected to the circuit.
Thermo-mechanical analyses are also of importance in electronics design, as it will affect the reliability and lifetime of the product. Simcenter FLOEFD also has the capability to carry out linear stress analyses. A hexa-dominant structural mesh required for mechanical analysis, can be quickly and efficiently created. The structural boundary conditions, structural mesh and the temperature results can be exported out directly to Simcenter 3D for non-linear stress analyses such as creep and fatigue calculations.
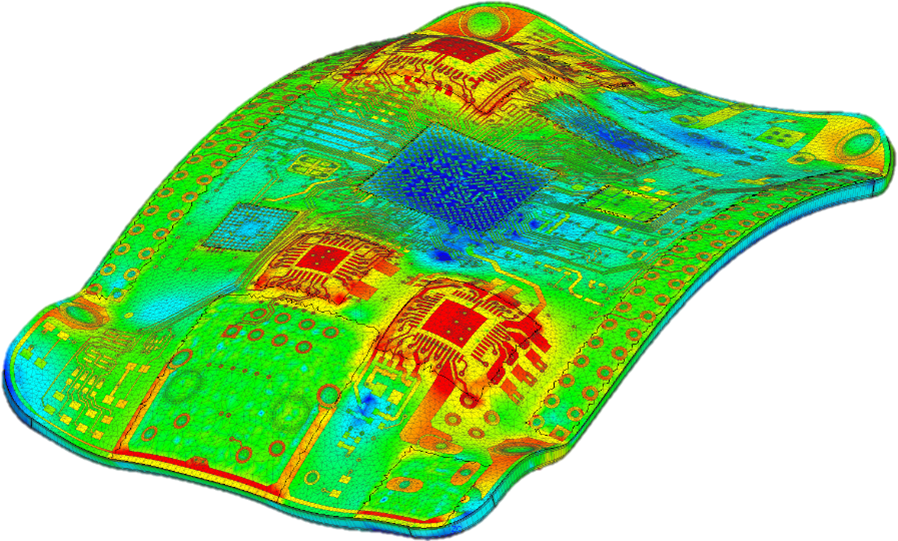
Semiconductor testing and model calibration
Besides simulations, Siemens also has specialist semiconductor measurement equipment, the Simcenter Micred range of testers. Simcenter Micred T3STER SI is used for the thermal characterization of semiconductor devices. Junction temperatures are measured directly with an electrical test method and Structure Function graphs which describe the heat flow path within the measured IC Package are obtained from the temperature measurements.
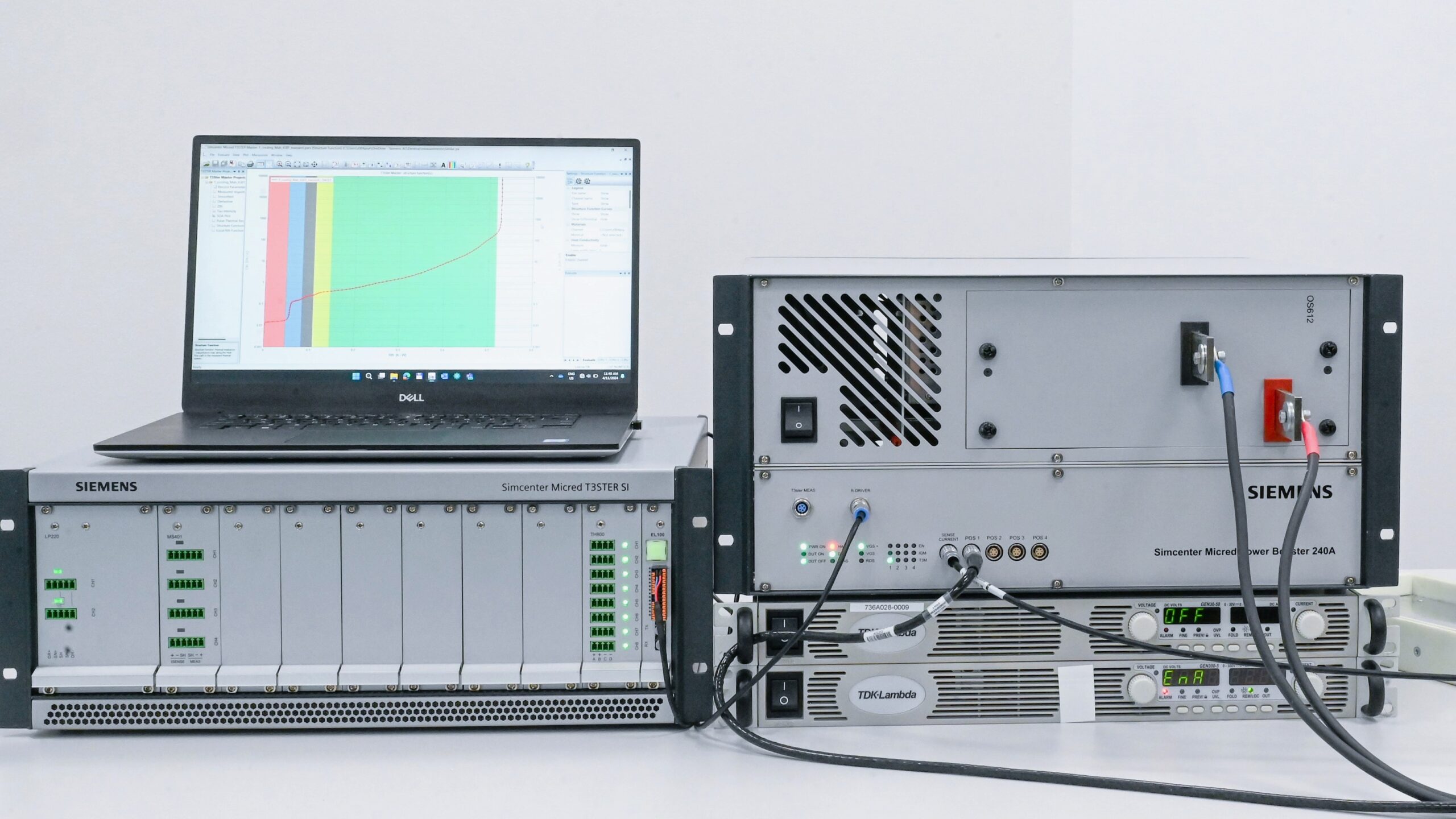
All too often, during the construction of any thermal simulation model of an IC package, there are usually some assumptions made, for example, the footprint size of the die active area, or with the material properties of the different layers found within a package. Even a small deviation of these geometric and material properties can have a significant impact on the thermal response of the package, causing significant deviations in the predicted temperature results compared to the measurements.
The Structure Function graphs from the measurements can be imported into Simcenter FLOEFD for the purposes of calibrating thermal simulation models, so as to improve their accuracy. Besides junction temperatures, the measurements also capture the transient temperature responses of the measured devices. All of these information is vital to ensure an accurate Digital Twin of the IC package.
Therefore, it is important to verify simulation models against Simcenter T3STER SI measurements. The accuracy of both thermal and structural simulations will benefit from the calibration of the IC package.
Design Space Analysis and Optimization
The next piece in the jigsaw puzzle of CAE analysis is the optimization of the cooling solutions, whether through the use of air cooled heatsinks, heat spreaders or thermal vias under the IC package etc. Siemens Multidisciplinary Design Analysis and Optimization (MDAO) tool, HEEDS, can carry out a design space exploration and optimization of the problem efficiently and provide suitable solutions for the designer. Multiple parameters such as the reduction in the total weight of the cooling solution, cost reduction along with minimizing temperatures, can be considered during optimization.
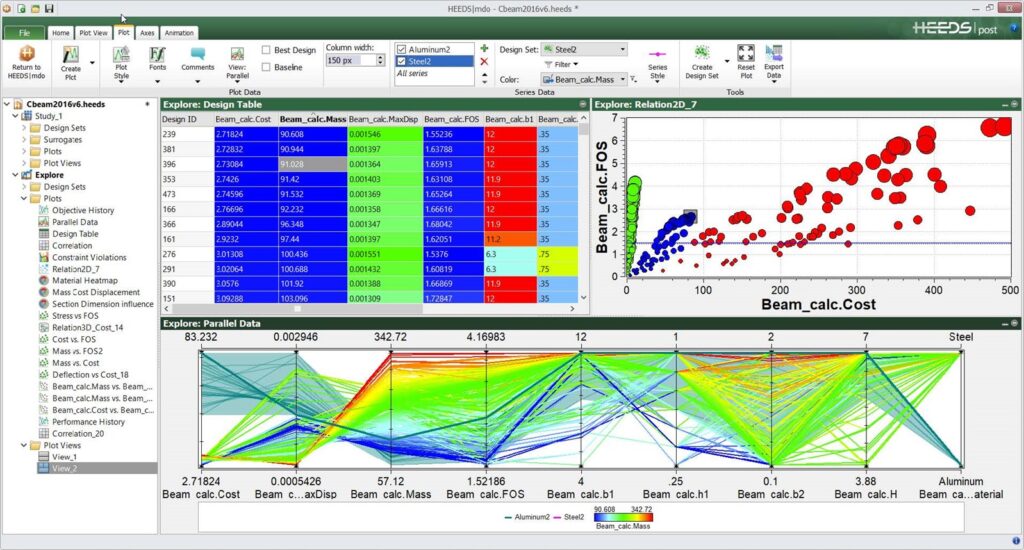
Finally, the data chain from the multi-domain simulations carried out would need to be linked. This where Siemens Simulation Process and Data Management (SPDM) tool is essential. With Teamcenter, there is full traceability and management across the different domains, simulation and test processes and results. This allows for seamless collaborations between different analysis teams.
In summary, the Siemens Xcelerator provides a comprehensive solution for simulations across all design domains, supporting users in their “shift left” paradigm, where analyses of products are moved earlier in the design cycle. This will help improve product quality, reliability, reduce costs and accelerate time to market.