Combustion simulation – A cyclist’s guide to clean air with adaptive mesh refinement
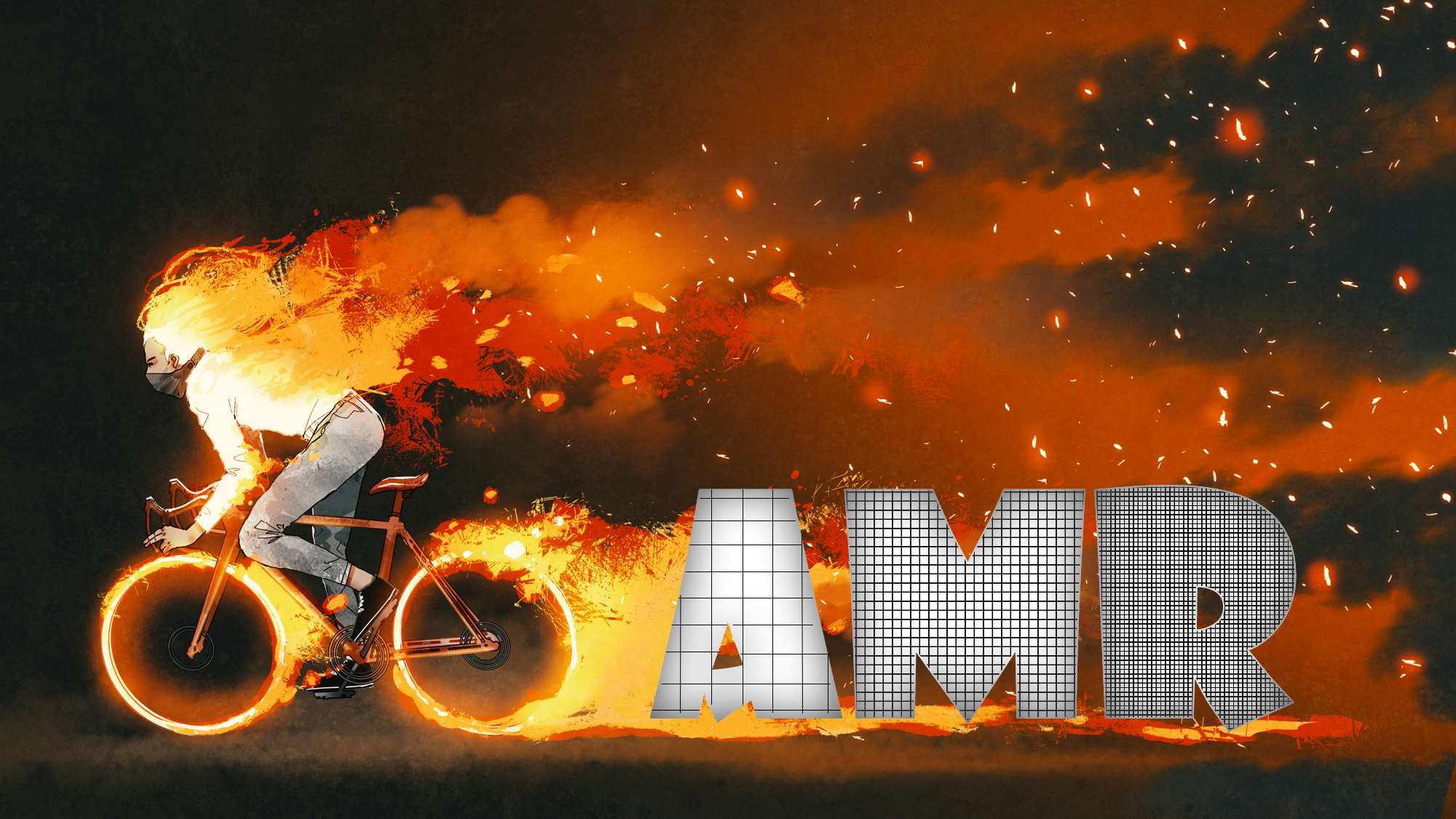
While combustion simulation is my profession, cycling is my passion. Taking my daily exercise cycling through London, last week, the eery quiet contrasts massively with what I am used to. Take a look at the lock-down difference between Oxford Circus, the famous London shopping mecca:
Cycling has become a great way to take exercise during these difficult times! Beautiful sights, no traffic and clean air! These last two are direct consequences of the lock-down we are currently undergoing in London.
Thinking about ‘clean air’ one of the emissions that is important to me as a cyclist is Nitrogen Dioxide and Nitrogen oxides (NOx). NOx has been shown to cause respiratory issues and, suffering from severe asthma, a drop in NOx means a faster and easier cycle!
I looked at ‘lock-down’ stats for the UK and motor vehicle use in the UK has dropped 40%. This is leading to almost a 40% reduction in the value of NOx concentrations in London. No wonder I am beating my best cycling time on Strava!
Keeping up these dramatic environmental improvements when the restrictions are removed is tricky! To decide where we can reduce NOx, I wanted to look at where it is produced in the UK.
Sources of NOx in the UK
In the UK one of our major sources of emissions is from power generation, where our UK power strategy is generally to use natural gas as a reliable source of energy bridging the gap before renewable can occur.It is roughly the same as that of road-transport at the moment.
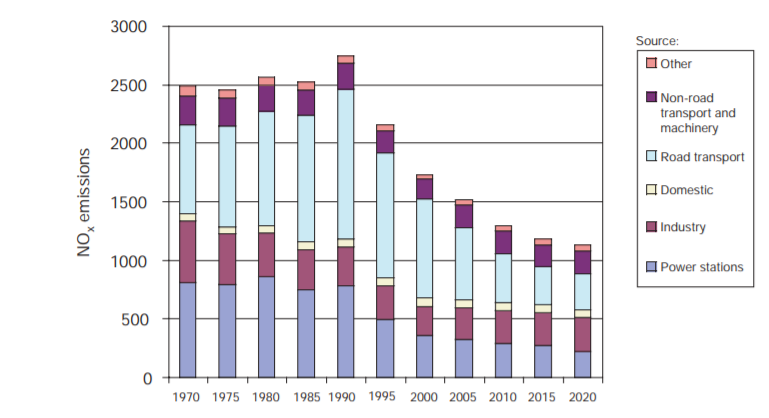
I often cycle through the gorgeous Lee Valley Park which is next to the Enfield Power Station which uses a combined gas cycle turbine. I started thinking to myself (or hoping to myself) that maybe my poor cycling times on Strava aren’t related to my fitness but are actually due to the NOx emissions!
In search of the best time I thought I could help by using Simcenter STAR-CCM+ to carry out some combustion simulation and look at how we can reduce the NOx coming from this gas turbine!
Clean air with Gas Turbine combustion simulation: what’s so tricky about it?
I started my investigation by wanting to understand why it is so tricky to get our Gas Turbine NOx values lower. So I used combustion simulation to investigate. Power generation from natural gas in the combustion chamber looks like this:
This is the definition of chaos for me! The flame constantly moving backwards and forwards with pockets detaching on and off. It’s clear why it’s so tricky! I wanted to investigate how this chaotic behavior influenced our NOx predictions.
My chemistry studies from University a long time ago tell me that thermal NOx is exponentially dependent on temperature. I knew this from the Arrhenius equations. So, I started by looking at the temperature field of this gas turbine:
Immediately I noticed hot pockets of temperature detaching from the flame. These hot pockets of gas are where the NOx is produced in great amounts since the temperature is too high. To truly make improvements to my gas turbine and understand how to get clean air I needed a solution to get this kind of detailed resolution of these hot pockets without my colleagues complaining about my cluster usage!
I also needed this detailed resolution because we measure NOx in parts per million (ppm)! Amazingly, a gas turbine can be as low as 10 ppm for NOx. To put this in context, tracking one part per million is equivalent to finding one specific granule of sugar among 273 sugar cubes.
Combustion simulation adapting for clean air in Gas Turbines – Reacting Flow model specific AMR
Early this year my colleague Ritu wrote about the ‘grand challenge problems’. She was talking about the computational hurdles she found when taking on these. I was most interested in this hurdle:
Capturing the relevant flow features of varying length scales requires refinement zones that quickly escalate the cell count.
So, when I naively started out trying to capture NOx that’s exactly the problem I encountered. The cell count was ‘escalating’ quickly whenever I tried to capture these hot pockets and resolve these low values! I tried to use volume refinement shapes but this manually intensive process quickly became frustrating since the flame was so chaotic.
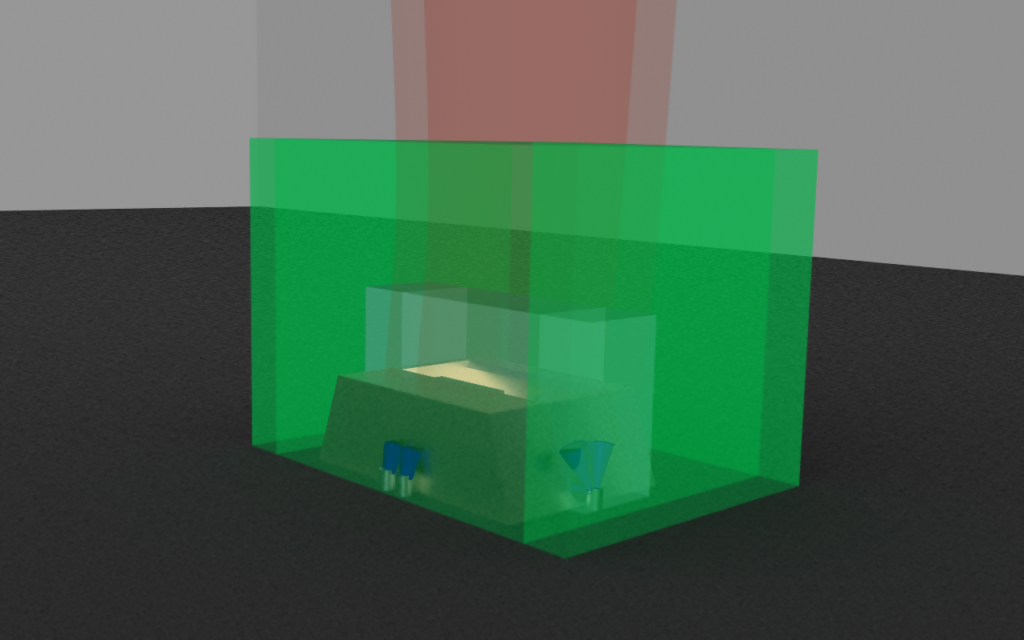
In the 2020.2 release of Simcenter STAR-CCM+ we are building on the 2020.1 capabilities of Adaptive Mesh Refinement (AMR) and including a Reacting Flow mesh adaption model. We designed this to hurdle over these computational issues for our combustion simulations.
Starting small
I first tried this out on a furnace and a simple model combustor before I moved onto my ‘grand challenge’ problem. I started out with these two smaller problems because I knew in the past that I had to run these cases with an excessive amount of mesh.
Firing up Simcenter STAR-CCM+ 2020.2 on my workstation (remotely), I loaded in my old sim files. First, I cleared the mesh refinements I had made to attempt to capture the flame shape previously. In just 5 clicks I had the new AMR model enabled and then just one click more to press the run button. The results speak for themselves:
The adaption captures the flame perfectly and it is immediately apparent the reduction in mesh and run-time. Looking at the mesh count reduction we see:
Mesh Count Reduction | |
Furnace | 5x |
Combustor | 4x |
AMR driven by the Reacting Flow model allowed me to start with a coarse mesh and then automatically and intelligently refine the cells in the region of the reacting flame front. The result is a sharp resolution of the flame front with far fewer cells, while at the same time delivering a significant speed-up.
With the 2020.2 release of Simcenter STAR-CCM+, I put my flame front refinement worries behind me and sat back to watch the adaption getting my clean air!
Clean Air, Clean Turbine!
Having tried this out on these simple test cases I wanted to try this out on my gas turbine. Comparing my fine mesh on the right-hand side with the adapted mesh, the difference in cell count is obvious! This was a big time saving for me! I then immediately went on a new cycle ride in the Lee Valley!
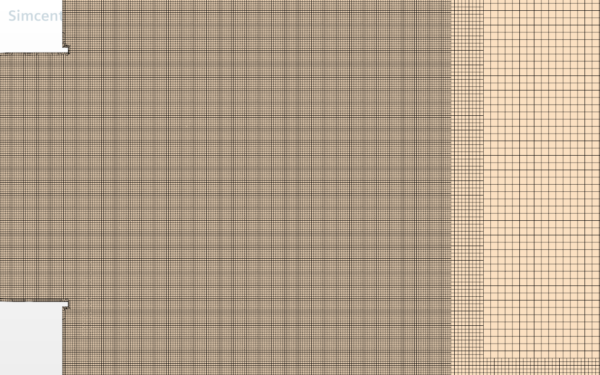
The adaptive mesh captures hot pockets of temperatures perfectly. My NOx emission results with AMR compared very favorably with experimental results.
Experiment | CFD | |
NOx (ppmv) | 5 | 13 |
I can now help to minimise NOx production in gas turbines. This will improve this ‘bridging technique’ before we move entirely to renewable energy in the UK. Using Simcenter STAR-CCM+ capabilities for design exploration we can drive this value even further down without worrying about meshing!
References:
[1] Slides, datasets and transcripts to accompany coronavirus press conferences, Prime Minister’s Office, 10 Downing Street, https://www.gov.uk/government/collections/slides-and-datasets-to-accompany-coronavirus-press-conferences
[2] Ricardo: an analysis of Covid-19 lockdown on UK local air pollution, David Carslaw https://airqualitynews.com/2020/03/31/ricardo-an-analysis-of-covid-19-lockdown-on-uk-local-air-pollution/
[3] Nitrogen Dioxide in the United Kingdom, Air Quality Expert Group, https://uk-air.defra.gov.uk/assets/documents/reports/aqeg/nd-summary.pdf
Comments
Comments are closed.