“Innovation” podcast series (Ep. #5): eVTOL Electrical System Design and Compliance
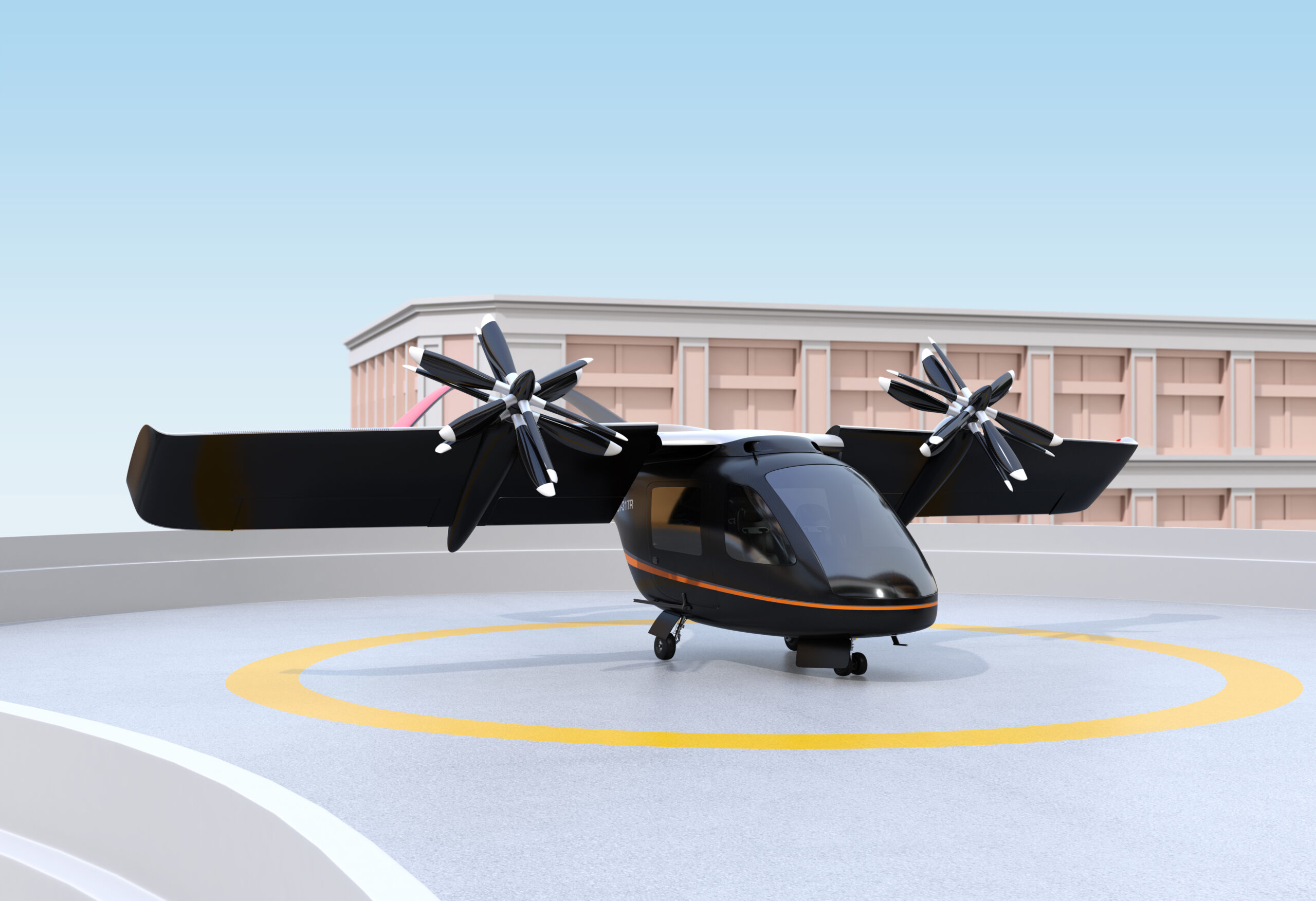
When you think about an eVTOL aircraft, there’s no engine to power a hydraulic or pneumatic system. Everything is based on the electrical system. As a result, the industry is looking for high-powered electrical solutions in an extremely lightweight design.
How do you find the perfect balance between the systems required to make an eVTOL fly safely and inefficiently? Increasingly, platform developers are taking a multi-disciplinary systems approach to platform development to optimize key performance metrics. Through a comprehensive digital twin, ideas can be developed in concert with knowledge of how a certain innovation in one discipline helps or hurts the implementation objectives of another discipline.
Teams can’t just optimize one system at the expense of the other systems, you have to find a proper balance between all of the systems through a multi-domain solutions approach.
In our final episode of the “Innovation” podcast series, we’ll explore the design and manufacture of an electrical system for today’s eVTOL aircraft. We’ll touch on the importance of power management and why electrical platform weight is critical to eVTOL design. All of this wouldn’t be possible without a highly digitalized environment so we’ll dive into the advantages of digitalization – not only when creating an electrical system, but also when it comes to compliance.
Listen to episode #5 now.
Listen to all episodes in our eVTOL innovation series:
Episode #1 – “Up, up and away – eVTOLs in the age of digital transformation”
Episode #2 – “Aerodynamic design through digitalization”
Episode #3 – “Power density and thermal management”
Episode #4 – “Structural design using composites and additive manufacturing”
Welcome to Talking Aerospace Today – a podcast for the Aerospace & Defense industry. A place that brings the promise of tomorrow’s technology to the ears of our listeners today.
eVTOLs are not only electrically powered but they need an electrical system that’s lean, lightweight, and efficient. They also have to 110 percent safe – no question about it. So, what are manufacturers doing to ensure they meet these requirements in an efficient manner?
Today, in the fifth and final episode of our “Innovation” podcast series, we’ll explore and explain the design and manufacture of an electrical system for today’s eVTOL aircraft. We’ll also touch on the importance of power management and why electrical platform weight is so critical to eVTOL design. Of course, all this wouldn’t be possible without a model-based engineering approach so we’ll dive into model-based design and the advantages of this approach when it comes to creating an electrical system for an eVTOL aircraft.
I am your host, Scott Salzwedel, and for the last time in this series, I am joined by Dale Tutt, Vice President of Aerospace & Defense at Siemens Digital Industries Software. We’ll also be joined by and Anthony Nicoli, the Aerospace & Defense Director of Integrated Electrical Systems at Siemens Digital Industries Software. Tony is the Siemens guru of all things electrical in an aircraft.
Please join us as we uncover electrical design considerations for eVTOLs, and how the digital transformation from Siemens addresses these complexities and challenges.
In this episode, you will learn:
- Dale’s experience with electrical systems. (03:00)
- What manufacturers focus on the most in the electrical system of an eVTOL (04:15)
- The challenges with electrical systems in today’s eVTOL designs. (05:03)
- How companies are addressing the power management and platform weight of electrical system design. (05:57)
- How model-based techniques and approaches help with getting certifications easier and faster. (08:35)
- The benefits of using a comprehensive digital twin. (10:09)
- How embracing the digital transformation allows teams to operate more efficiently. (12:32)
Connect with Dale:
Connect with Tony:
Connect with Scott:
Resources:
Podcast Transcript:
Scott Salzwedel: Hello, this is Talking Aerospace Today, a podcast for the Aerospace and Defense industry – a place that brings the promise of tomorrow’s technology to the ears of our listeners today. I’m your host, Scott Salzwedel. Welcome to our final episode in our five-part series: “Driving Innovation through Digital Transformation.” We are in the early stages of a huge innovation wave spreading throughout the industry. Finding the right technologies is key to success and significant profits.
Today in our final podcast, we’ll be discussing electrical system design. eVTOLs are not only electrically powered but they require an electrical system that’s lean, lightweight, and efficient, and of course, 110% safe, so very important.
Before we get started, to recap our last episode, we talked about the importance of structural design in eVTOLs and how composites are making a huge difference – a great episode. If you missed it, I urge you to take a listen. In this podcast, we’ll be explaining and exploring how to design and manufacture an electrical system for today’s eVTOL aircraft. We’ll talk about the importance of power management and weight. We’ll also talk about how a model-based approach benefits all the teams involved when it comes to creating an electrical system for an eVTOL aircraft. I’m pleased to introduce my special guest, Dale Tutt, who is Vice President of Aerospace and Defense at Siemens Digital Industries Software. Welcome, Dale. Thanks for stopping by to talk about innovation.
Dale Tutt: Hey, thanks, Scott. It’s very good to be here today and I’m looking forward to the discussion.
Scott: Dale, could you please share with our listeners how we have covered innovation in this podcast series?
Dale: This has really been a fun series. In our second episode, we talked about aerodynamic design and all the considerations that go into the design of an eVTOL or an urban air mobility vehicle. And then in episode three, we talked about power density and thermal management, some of the challenges that companies have, as they design their system on their eVTOLs, and how they manage all of the heat that’s being generated by those electrical systems. And then in episode four – the last episode – we talked about structural design and using composites and additive manufacturing, some of the considerations that companies are making as they think about how they build these aircraft more efficiently. And then today, we’re going to talk about electrical system design, it really is the “e” in the eVTOL, and there’s a lot of design considerations and I’m looking forward to the discussion.
Scott: Great, thanks, Dale. I should mention that later in this episode, we’ll be joined by Tony Nicoli, the Aerospace & Defense Director of Integrated Electrical Systems at Siemens Digital Industries Software. So pleased to have Tony on the show today. Dale, no question, wiring systems are critical to any airborne vehicle for weight, safety, even performance. What’s been your experience with electrical systems?
Dale: It’s been kind of interesting. I think as I go back to some of my earlier programs that I worked on, the electrical systems were fairly low. I was working on business jets and we might have 15 kilowatts on the electrical power on the airplane and that could drive most electrical systems and the electrical teams tended to be pretty small. And now you’re talking about megawatts and the electrical systems are dominant, there’s so much more wiring. So, it’s been quite a change, quite a growth in the last 20 years, just in electrical systems and what they mean to the aircraft. We really started to see this, back in the ‘70s, to some extent where you started seeing some of your first real fly-by-wire aircraft, such as the F-16, where they were able to take advantage of flight control computers and reduce the stability of the airplane because they had computers to help manage the airplane. As a result, they could go to smaller control surfaces, smaller tails, and save structural weight. It’s been quite a change and it’s been quite a transformation throughout the years.
Scott: Wow, very cool. When looking at the electrical system of an eVTOL aircraft, what are manufacturers focused on the most?
Dale: It’s all about the electrical systems now at this point and everything is electrical. When you start talking about an eVTOL, you don’t have an engine to power a hydraulic or pneumatic system, so you have to do everything with an electrical system. And so as a result, they’re looking for higher power electrical solutions and a very lightweight design. There’s a lot more software and it’s added a lot of complexity to the design of the eVTOLs.
Scott: Great. Thanks, Dale. It’s such an important topic we’re discussing today. At this time, I’d like to bring Tony. Tony is the Siemens guru of all things electrical in an aircraft. Thanks for being here. I’d like to start by asking what are the challenges with electrical systems in today’s eVTOL designs.
Tony Nicoli: Thanks, Scott. Heaping praise on me will get you nowhere. The two biggest challenges I see are, first, how do we achieve enough time in the air per pound of payload to make it a viable alternative for the missions we intend? And second, how do we ensure the safety of this new mode of transport? Allow me to expand on that. You know, all-electric technology is played by the limitations on electric energy storage density. Modern batteries just can’t compete with liquid chemical fuel; they differ by about a factor of 10, something like that. So, if you want to fly an eVTOL, we need to be clever about how we optimize the platform as your mission system. We’ve got to design it, all of it, to address the specific mission we are targeting.
Scott: When it comes to electrical system design, we hear a lot about power management and platform weight reduction. Can you elaborate on that?
Tony: Absolutely. The two biggest issues to address are power management and overall platform weight. These are two variables that platform designers can control and should control early in the process in their pursuit of sufficient flight time and safety reserves for eVTOL aircraft.
Scott: What are companies doing about this?
Tony: Increasingly, the most sophisticated platform developers are taking a multi-disciplinary systems approach to platform development to optimize these two key performance metrics. Mechanical and electrical systems are being developed in concert with knowledge of how innovative ideas in one discipline helps or hurts the implementation objectives of the other. Further, model-based descriptions of the functions required from both disciplines are being brought together and assessed in tandem. Configuration-controlled electromechanical digital twins allow not just designers but systems engineers to make early predictions of how platform architectural trades will impact key platform characteristics, like power, weight and other key mission parameters like flight time. And when I say early, I mean early, like during architectural definition. This kind of real-time insight was unavailable until recently. It is revolutionizing what is possible, even with today’s technology.
Scott: Dale, do you want to get in here? Is there anything you want to add at this point?
Dale: As Tony says, it’s about finding the balance between all these different systems and the structure and all the concerns. And you can’t just optimize on one system at the expense of the other systems, you have to find a good balance between all of the systems and really find balance in a multi-domain solution. As he says, it’s starting from the beginning, early in the architecture, and then being able to carry that optimized design through the rest of your systems as you design it so that you can use that information and really leverage it as you go into your certification program. A lot of challenges with this.
Scott: Tony mentioned something about a sophisticated platform, multi-disciplinary systems coming together: mechanical and electrical. So, Tony, I get the feeling you’re talking about that new announcement, the Siemens Electrical/Electronic (E/E) systems development environment, is that what you’re alluding to?
Tony: Yes, I am, Scott.
Scott: Listeners, you can just Google that. It’s a fascinating technology coming out of Siemens. But before we go any further, I have to ask about certification… that’s huge in this area. I’m sure it’s very tricky. So, can you shed some light on certification?
Tony: Sure can. Scott, ensuring safety and providing the evidence that allows us to understand that the platform will fly safely is the next biggest concern. With the prospects of thousands of additional small urban air vehicles buzzing about our cities and countryside, we need to be 130% sure that our mission systems and avionics will perform in all flight phases and under all flight conditions. We’ll also need to know that whatever multi-platform control system is employed to manage this traffic, it will work. Here again, model-based techniques are already being employed by the most advanced organizations.
Scott: Model-based techniques, model-based approaches. Dale, anything you want to shed some light on in this regard?
Dale: Yeah. I think I’ll just reiterate the importance of certification and having a good trail of information that you can audit will provide confidence when you get into certifying with the FAA and other civil certification authorities. The model-based systems and approaches, model-based techniques, really help establish that digital trail of information with these complex systems.
Scott: I would imagine having a model-based approach that allows teams to work together eliminates those silos, as they say. It allows teams to be proactive in meeting the demands of what they need to do, as well as being aware of what other teams need to do as part of the overall platform development lifecycle. It’s all about starting and knowing the electrical architecture earlier in the process, it’s that shift left approach. I’m guessing this is made possible by the Siemens comprehensive digital twin we talked about, and even the digital thread technologies. Tony, can you shed some light in this regard?
Tony: I sure can, Scott, and I’d like to discuss a few key points. First, by extending the digital thread, integrating the tools that perform certification, and connecting with the platform’s electrical and mechanical digital twin, users know how implementation changes impact regulatory compliance in nearly real-time. This allows developers to explore a much larger variety of solutions while taking into account the compliance impact. This can really help with innovating new electrical systems and designs. The story doesn’t end with a safe design. We need to be able to demonstrate its safety to the regulatory authorities. Once again, extending the digital thread, this time to reporting, enables us to accelerate the communication of the impact of our design changes to DERs and ARs. We can do this in formats and frameworks that make it easier for regulatory authorities to understand what we changed and how it ensures regulatory compliance. Finally, what’s cool about this whole thing is that we can use these model-based techniques to reduce the cognitive load on both the development team and the regulatory team, allowing them to work together more easily toward the common goal of implementing the new safe technology that will bring us the eVTOL mission solutions we seek.
Scott: This all sounds rather revolutionary… the way digitalization streamlines and optimizes many of the processes involved here. How are our customers solving some of these more typical problems when it comes to designing electrical systems for eVTOLs? I know you’ve touched on this already, but maybe you could expand a little bit more?
Tony: Well, Scott, Siemens has invested nearly 2,000 man-years of effort to create a comprehensive electrical and electronic systems development portfolio. It consumes system modeling data and requirements to enable eVTOL electrical system architecture optimization. This allows eVTOL systems engineers to choose a better architectural starting point with advanced knowledge of how it will impact platform performance characteristics.
Scott: Wow, really good stuff. Thanks, Tony. Dale, do you have anything more to add?
Dale: Yeah, as I think about the challenges that some of these companies face today, I mentioned earlier the growth of these electrical systems on so many aircraft and eVTOL aircraft is so different. In the past, you could use a lot of document-based systems. But now, today with the new tools, new solutions out there, the companies that are embracing this digital transformation are really being able to operate a lot more efficiently. So, with task automation; being able to translate data from one system to the next without doing a lot of manual processes. As a result, companies are able to move faster and they’re freeing up their teams to be more innovative, as they are able to focus on solving problems instead of managing administrative tasks around their design and making sure that everything’s in sync. How does Siemens help with this digital transformation with our Xcelerator portfolio? It’s really all of our solutions packaged together. It’s all of the tools that you can use to help you along your way with your digital transformation. And it scales the company of any size, and any program of any size. As you’re starting a new program, you’re able to then grow within this Xcelerator portfolio. As Tony talked about the comprehensive digital twin and digital threads and the ability to have this rich, robust understanding and the connectivity from engineering into manufacturing and into certification with a digital twin and digital thread, and then being able to do this in a very flexible and open ecosystem where you can incorporate the latest technology, any solution set that helps you be more competitive. And so, we’ve been very actively involved in and partnering with our customers on their digital transformations.
Scott: Well, I’m afraid that’s all the time we have for this episode. Before we sign off, I was wondering, Tony, could you cite a customer case study of any kind?
Tony: Scott, there’s a lot going on right now, but for many reasons, I cannot discuss it all here. However, I will say that we’ve had huge successes with companies such as Pilatus, KAI, Bell and Boeing. There is one case study I can talk about, and it’s about how the Boeing Saab team applied our model-based systems engineering extensively to their advanced platforms, including the T-7a. As a result, the Boeing T-7a advanced pilot training system received Aviation Week Network’s Game Changer Award. So, we’re very pleased about that.
Scott: Very nice, Tony. Thanks for sharing. I wish we had more time. But I do appreciate you being a part of the show. Thanks, Tony.
Tony: My pleasure, Scott. Thanks a lot for inviting me.
Scott: Dale, it’s time to say goodbye. Thanks for your time today.
Dale: Hey, Scott, no problem. And thanks for having me. This has been a lot of fun for me – I always enjoy talking about innovation. I’ve learned some new stuff along the way from the experts that we have had on the show. I feel bad that this series is coming to an end, but I look forward to the next one.
Scott: Me too. There’s just so much more we need to cover. Things are constantly changing in our industry. Dale, you’ve been wonderful, and thanks for being the anchor throughout all these episodes. And of course, I’d like to extend my deepest thanks to our listeners. I’m glad you tuned into this podcast. Thank you, listeners.
At the top of the show, I mentioned this is a five-part series. If you enjoyed this episode and you’d like to listen to previous episodes, please subscribe to Talking Aerospace Today on Apple iTunes, Spotify, or wherever you go to get your favorite podcast. We are planning to do more podcasts in the future, so please sign up now. That way, you won’t miss a single episode. You can also check out the links in this podcast’s description.
My name is Scott Salzwedel, and this is Siemens Talking Aerospace Today. I hope you’ll join us again for our next podcast. Until then, bye for now.
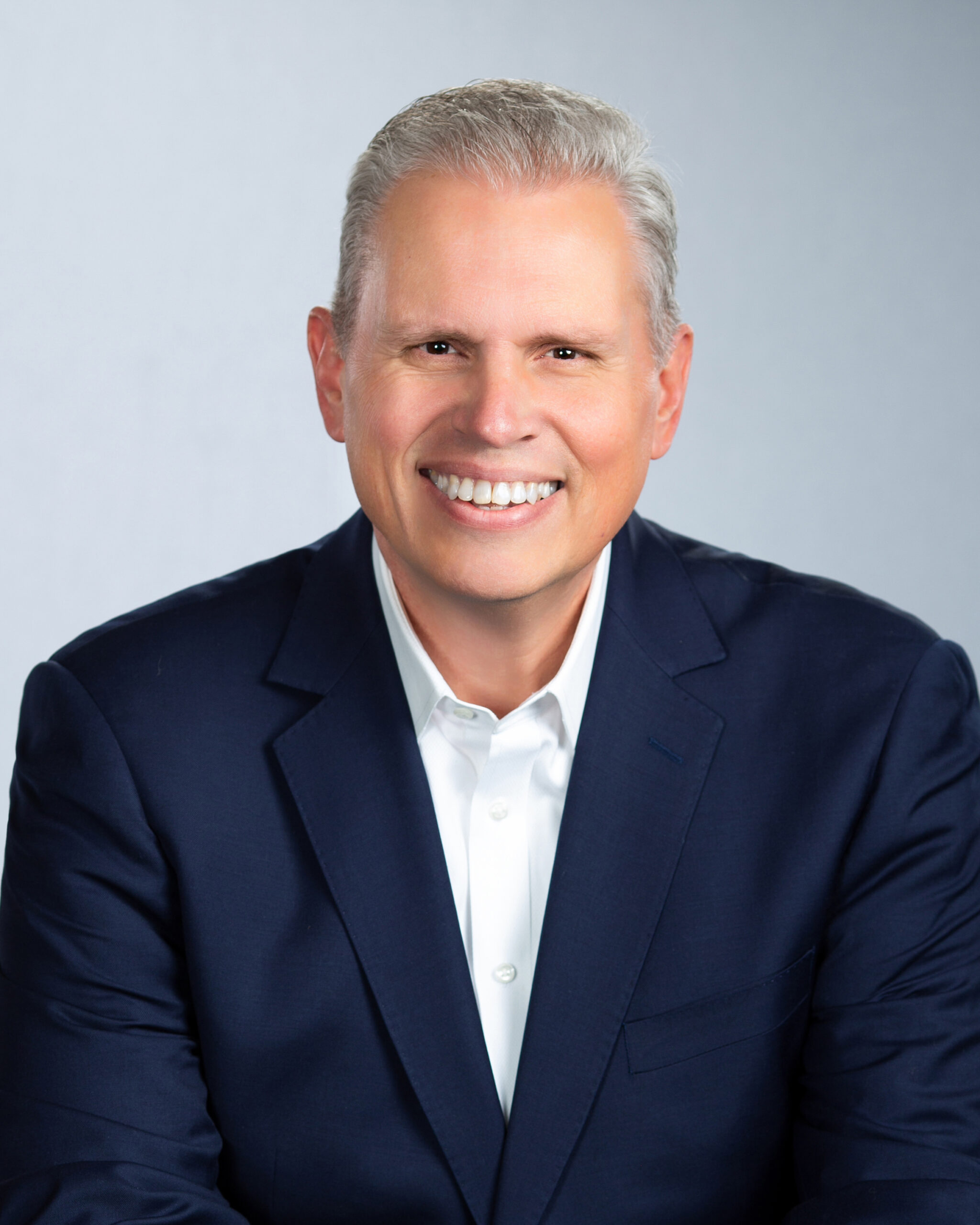
Dale Tutt – Vice President of Industry Strategy at Siemens Digital Industries Software
Dale Tutt is Vice President of Industry Strategy at Siemens Digital Industries Software. Dale leads a team of experts to develop and execute industry-specific product and marketing strategies in collaboration with the global product, sales, and business development teams. With over 5 years of experience in this role combined with extensive experience in the aerospace and defense industry, Dale has a deep understanding of the challenges and opportunities facing companies as they embark on their digital transformation journeys.
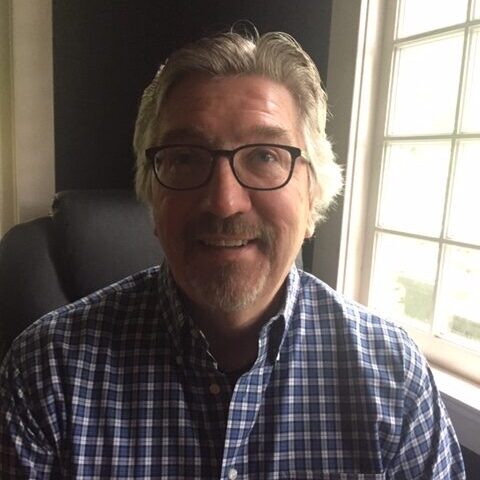
Scott Salzwedel – Host
Scott Salzwedel is senior technical writer and corporate communications writer involved in the Siemens Aerospace & Defense Industry and Siemens Capital. In addition to writer/host of Talking Aerospace Today, Scott is the writer of white papers, articles, blogs, videos and websites at Siemens.
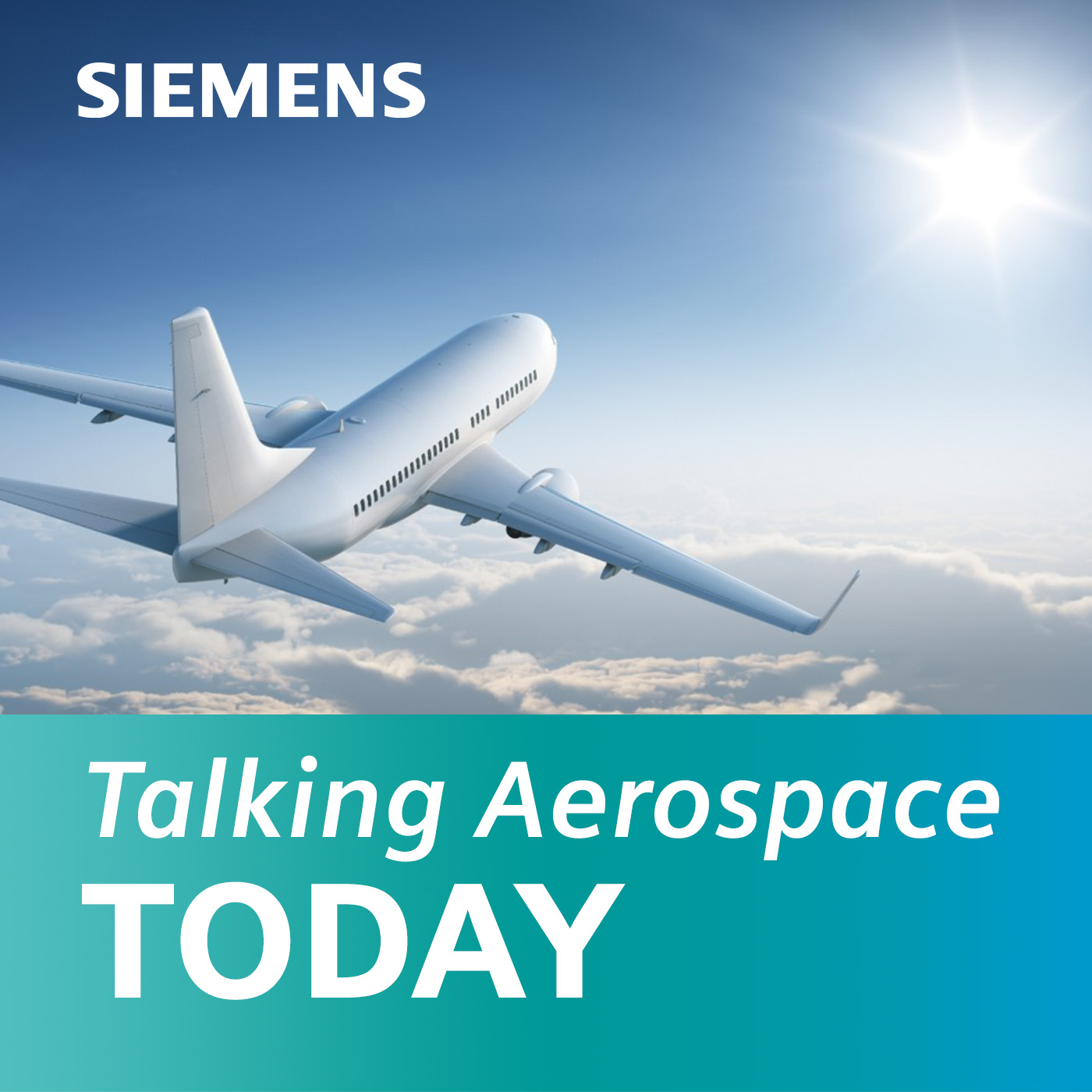
Talking Aerospace Today Podcast
The A&D Industry is at a serious inflection point. Transformation to the digital enterprise has opened up a new era in innovation and technological breakthroughs. However, complexity and compliance continue to hamper the best of efforts.
Join us as we explore how Siemens is turning complexity into a competitive advantage for many of our customers – today and well into tomorrow.