“Innovation” podcast series (Ep. #3): eVTOL Power Density and Thermal Management
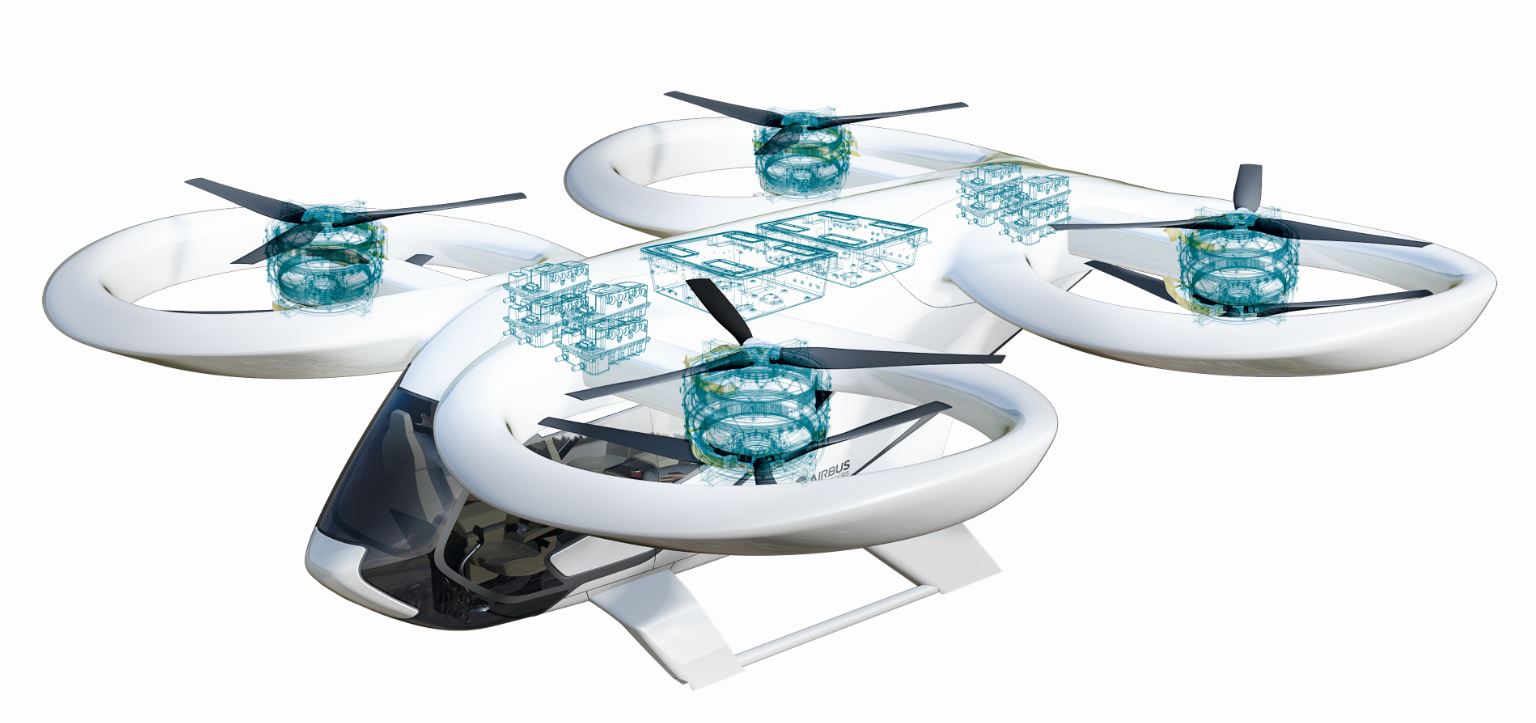
Let’s talk electrical propulsion.
More specifically, electrical propulsion as it relates to urban air mobility (UAM). Not sure if you realize this but there’s a burgeoning industry out there that will soon change our lives for the better.
With electrical propulsion, especially as it relates to UAM aircraft, considerations must be made on power density, thermal regulation, electromagnetic interference and various other factors.
Please join me for our third episode in our “Innovation” podcast series as we discuss thermal density and thermal management in eVTOL aircraft. In this podcast Dale Tutt of Siemens A&D and Thierry Olbrechts of Simcenter Aerospace Solutions with be joining me.
Electric propulsion is a great response to the need for green energy alternatives and battling climate collapse. Electric propulsion is being built into short-haul aircraft for cargo and medical supplies delivery, urban air mobility vehicles for human transport and even into supersonic air travel. …Fascinating stuff!
Listen to episode #3 now.
Listen to all episodes in our eVTOL innovation series here:
Episode #1 – “Up, up and away – eVTOLs in the age of digital transformation”
Episode #2 – “Aerodynamic design through digitalization”
Episode #4 – “Structural design using composites and additive manufacturing”
Episode #5 – “Electrical system design and compliance”
Welcome to Talking Aerospace Today – a podcast for the Aerospace & Defense industry. A place that brings the promise of tomorrow’s technology to the ears of our listeners today.
When you think about the first airplanes… they were propeller-driven. Then, the jet engine came along and transformed the nature of aviation forever.
Today, we’re ready to embark on the next frontier – electric propulsion in urban air mobility (UAM) vehicles. Electric propulsion is a great response to the need for green energy alternatives and battling climate collapse. Electric propulsion is being built into short-haul aircraft for cargo and medical supplies delivery, urban air mobility vehicles for human transport and even into supersonic air travel.
In our last episode, we had a great conversation on aerodynamic design and the associated elements that impact performance and efficiency – and how simulation delivers the much-needed and critical results.
In this third episode of a five-part series we’re calling “eVTOL Power Density and Thermal Management,” we’ll be addressing power density and thermal management of an eVTOL aircraft. You’ll learn the benefits and challenges of using electrical systems, how companies go about solving those challenges and how Siemens is contributing to the digitalization of this space through the Xcelerator portfolio.
I am your host, Scott Salzwedel, and in this episode, I am joined by two industry leaders. Dale Tutt, Vice President of Aerospace & Defense at Siemens Digital Industries Software, and Thierry Olbrechts, the Director of Simcenter Aerospace Solutions at Siemens Digital Industries Software.
Please join me for this one-of-kind discussion. Where else are you going to hear about mastering the physics of high-power density electric motors?
In this episode, you will learn:
- The innovations happening in electric propulsion. (02:54)
- The advantages and challenges of electrical systems. (04:03)
- The challenges of electrical propulsion relating to eVTOL design. (05:43)
- What needs to be considered when making electrical propulsion units viable for aviation? (10:03)
- How to manage the heat produced by electrical propulsion units. (12:28)
- How Siemens Xcelerator helps customers with good solutions. (15:50)
Connect with Dale:
Connect with Thierry:
Connect with Scott:
Resources:
Podcast Transcript:
Scott Salzwedel: Hello, this is Talking Aerospace Today, a podcast for the Aerospace and Defense industry – a place that brings the promise of tomorrow’s technology to the ears of our listeners today. I’m your host, Scott Salzwedel. Welcome to episode three of our five-part series: “Driving innovation through digital transformation.” We are in the early stages of a huge innovation wave spreading throughout the industry, finding the right technologies is key to success and significant profits.
Today in our third podcast we’ll be discussing power density and thermal management of an eVTOL aircraft. The battery is only one part of the electrical propulsion system. In addition to the battery, there’s the electrical power distribution, the electrical management system along with cables, buses and so much more.
Before we get started to recap our last episode, we talked about eVTOL aerodynamic design, how there’s so much to aerodynamics the eye cannot see. If you missed it, I urge you to take a listen. In this podcast, we’ll be discussing eVTOL power density thermal management. Whenever you’re dealing with electric propulsion thermal management, this is of paramount concern. I’m pleased to introduce my special guest Dale Tutt, who is Vice President of Aerospace and Defense at Siemens Digital Industries Software. Welcome, Dale. Thanks for stopping by to talk about innovation.
Dale Tutt: Hey, thanks, Scott. It’s so good to be here today.
Scott: Okay, so innovation, could you please share with our listeners how we plan to roll out this podcast series?
Dale: Absolutely. So, in the last episode – episode number two – we had a great conversation on aerodynamic design and some of the considerations that these eVTOL or these urban air mobility companies have to look at as they’re designing their new aircraft. In this episode, we’re going to have a great conversation around power density and thermal management and how does a company go about solving all of those challenges. Next up, we’ll be talking about structural design and using composites and additive manufacturing to really come up with the most lightweight design possible. And then finally, we’ll wrap it up with the “e” in eVTOL part, our electrical system design. So, a lot of good topics around all of the technical challenges that accompany working on these urban air mobility aircraft have and that they’re facing today.
Scott: Great, thanks Dale. I should also mention that later in this episode, we’ll be joined by Thierry Olbrechts, Director of Simcenter Aerospace Solutions at Siemens Digital Industries Software. Thierry’s experience in aircraft simulation runs deep. So, we’re pleased to have Thierry on the show today. But first Dale, what’s so innovative about eVTOL propulsion?
Dale: It definitely feels like we’re entering the next wave of propulsion in aircraft design. When you think about the first airplanes that came out, propeller-driven, and then the next propulsion system that really came up was the jet engines. And if you think about the first jets that came out, and how they just started to transform the aviation industry, in World War II, when the Me 262 came out and really changed the nature of aviation with fighter aircraft. And now there’s been all sorts of fighter aircraft developed over the years on jet engines and how it transformed the airline industry, and business jets being able to move people faster and more efficiently from one place to another. Now, the next frontier is electric propulsion. And I have to say, when I was starting as an engineer, I could have never imagined that electric propulsion could become commonplace in my lifetime. And so, it’s pretty amazing what’s going on in this arena of electric propulsion right now.
Scott: Yeah, it’s exciting stuff for sure. I’m seeing more and more of this “e” designation. What does that mean?
Dale: Well “e” is just simply, electrical. So, it’s electric vertical takeoff and landing (eVTOL) aircraft. It really has become the standard industry term moving as companies have moved from one form of vertical takeoff to another. But to get there, the “e” allows you to have much lower mechanical complexity because you’re able to do everything electrically on the airplane and you have more flexibility with some of your aircraft configurations, and the ability to put more rotors on these aircraft. The electrical components are so much easier to maintain and sometimes more reliable than their mechanical counterparts. And I think, then, the impact on this simplicity. It’s really part of the total cost of operations. When you think about total costs of operations of helicopters, which are the more traditional vertical takeoff and landing aircraft, is the maintenance that’s needed for them. But the challenge is, when you start bringing electrical together, the power density isn’t the same for batteries as for a gallon of gas. And so, you really have to change how you manage your weight and your performance, and your efficiency to help manage the battery complexity. Another challenge when everything’s electric is you get huge thermal issues. These electrical systems generate heat so you don’t have the convenient sources, the traditional sources, to reject that heat.
Scott: This is probably a good time to bring in Thierry. Hi, Thierry. Could you please help us to understand the challenges of electrical propulsion relating to eVTOL design?
Thierry Olbrechts: Hi Scott and Dale. It’s great to be here. Well, yes, the electrical propulsion units that are being developed today – and it started actually, eight years ago – are really allowing to change the configurations of the aircraft.
And one of the major things that we see is that there’s a drastic increase of installed electrical power, which is basically unseen for everything that has been flying up to now, actually. Now when you compare, for instance, look at the CityAirbus, it has actually something like eight motors of 200 kilowatts installed. And so, it basically requires 800 kilowatts to take off four to six people and to fly it. And of course, there’s another 800-kilowatts electrical motor installed for redundancy reasons. And that makes that aircraft has actually 1.6 megawatts installed electrical power, which is quite amazing. And certainly, when you compare that, for instance, to the installed electrical power of, let’s say, traditional fixed-wing aircraft, like the 787, and the F-35 JSF, which has approximately one megawatt installed power on the aircraft. I know the comparison is a little bit difficult – because in the 787 the electrical power is not used to propel the aircraft – but still, it shows what new kind of challenges are basically in front of the engineers that need to develop this. Of course, Dale already pointed to that when you develop such an electrical system, it comes with a lot of heat. And so, a lot of heat needs to be rejected during the complete mission.
But another thing that I thought of, Dale, is that when you compare the current power units on an aircraft, they are all very concentrated. So let’s say the conversion of the chemical energy into heat into mechanical energy, again into propulsion energy actually happens at one concentrated point on the wing. And with the electrical power units, certainly, when you look into, for instance, hybrid electrical power units, you will have the gas turbine, and the generator, which is located at one location in the aircraft, you will need a lot of harnesses to basically transport the energy throughout the different parts of the aircraft and basically feed the different motors, which will really be distributed around the aircraft.
And then there’s of course the increase in power density. When you want to make electrical power units viable for the aircraft industry you need to reduce the weight. That has always been the case on the structure, etc., and certainly on the electrical machines that you want to install. Now, that increase comes with a lot of engineering challenges. And, of course, when you decrease the weight, you decrease the heat capacity of that system, whether it’s at the component level, like at the battery level, the electrical power distribution centers, the inverters, the motors, etc., but it also holds for the integrated aircraft. How are you going to make sure that during that mission, whether it’s in cold or hot conditions, that the thermal balance of your integrated aircraft is right?
Next to the thermal problems, I believe there is an unseen, let’s say “challenge” related to the integration of the electrical systems. We’ll be talking in another podcast about this, but it’s clear that the electrical machines will operate at a higher voltage than what has been implemented typically in the current aircraft, but also at the higher currents. And that creates a lot of integration problems not only the heat integration problem, but also electromagnetic integration problems. There will be a lot of electromagnetic effects there will be EMI/EMC problems, maybe when you operate electrical harnesses at the higher altitudes, maybe some Corona effects will basically lower the performance of your insulation that you have put in place in the harnesses.
Scott: Could you tell us a little bit more about the aircraft electrical motor design?
Thierry: Of course… The development of aircraft electrical propulsion units is very interesting. Actually, when you look at traditional industrial motors like industrial motors for trains or mining machines, these machines typically have a power density of less than one kilowatt per kilogram. Now, when you want to make electrical propulsion units viable for aviation, the industry will need to increase the power density of these machines, whether it’s a motor or the inverters that are involved. The industry will need to increase that power density to 10 to 15 kilowatt per kilogram. So, the quest to remove the weight and to increase the power is all about finding, I would say, a good engineering balance. And that balance is very much dependent on each different aircraft and its specific mission. And the only way to do that is actually to master the physics of these high power density electric motors and inverters etc., is to master that through simulation. And of course, when you want to master that in a decent way, you need to take into account all the physics that are basically playing in such a machine. So, you have the electromagnetical physics, you have the thermal side, you have the rotor dynamics, you have the structural behavior, structural dynamics behavior, you name it. You need to be able to deal with all this physics in an integrated way.
Now, a very nice example that I want to talk about here is the Rolls-Royce electrical aircraft example, where they have already been able to implement high-power and high-power density motors in flying testbeds like the Extra 330 aircraft. So, I’m talking here about the Rolls-Royce propulsion unit of 260 D, which is actually oil-cooled, in order to protect, of course, the permanent magnets. In the newest version, that engine, that motor actually reaches already 5.8 kilowatts per kilogram. And, of course, they also develop higher power motors like the two-megawatt motor, which will be Integratable into a commuter aircraft and that’s actually a motor that reaches 10 kilowatts per kilogram.
Scott: So with all this heat, how do companies manage it? It must be nearly impossible. Just mind-boggling.
Thierry: Yes, indeed. So the aircraft industry is looking for a lot of new ways to reject the heat, actually. A way to solve this is to look into more performant ways to exchange the heat and basically reject the heat from the motors and its components. Possible ways to do that is to use dual-phase cooling cycle systems. What is clear though, is that before defining the architecture of the aircraft, one needs to go through these dynamic mission cases. And it’s very important to look at which aircraft structural architecture and which aircraft system architecture is actually the best for that specific aircraft and its mission. So, there again, the need to basically be able to create digital twins that allow us to look into the engineering physics – that allow a look into all engineering physics – whether it’s at the component level or at the integrated aircraft level. So, including, of course, all thermal, physical aspects.
Scott: Could you give our listeners a few real-world examples to help illustrate these concepts?
Thierry: Oh, yes. Well, I want to come back on Rolls-Royce Electrical because they are really at the forefront of implementing digital twin technology in the development of their aircraft motors. They have really been using the Siemens Xcelerator portfolio to the max, they did not only develop their motor in the Siemens solutions for developing the digital mock-up and the CAD models, they also have been managing all the data and all the requirements in the Siemens Xcelerator portfolio. But on the simulation side, they have been using our tools to look into the electromagnetic behavior to optimize the electromagnetic configuration of the electrical motor. Very important, as I already said is the thermal management so they have been using our fluid dynamics capabilities to look into how to implement the right systems to basically cool the motor with oil, and how do we also use the flow of the air to help to cool certain parts of the motor.
Next to that, of course, there’s also the structural integrity, the structural stiffness which is very important. And as you know, when you increase the power density, you take away a lot of structural mass, but when you reduce the structural mass, you also take away stiffness, and that might have an impact on the deformations that happen in the motor, which on itself might again have an impact on the electromagnetic behavior. So, there’s really these interactions between the different physics that need to be understood.
And that’s where Rolls-Royce Electrical has been using the Siemens tools to really create a tightly integrated digital twin coupled to the parameters of the CAD model in order to come to good solutions.
Scott: Now that’s a wonderful example, Rolls-Royce Electrical and how they’re using the Siemens Xcelerator portfolio. So, Thierry, I’m just wondering, maybe we could on a broader scale, just talk in general about the Siemens Xcelerator portfolio. How do you see that helping our customers?
Thierry: Siemens provides the most comprehensive and complete digital twin, and we can simulate all engineering physical phenomena that capture the integrated thermal balance of the aircraft. And we can do that in a very scalable way. First of all, scalable from the component level, because you need to understand the structural, thermal, electromagnetic behavior at the component level, up to the integrated aircraft level. And that’s what we call, at that level we actually are capable to create a virtual integrated aircraft model, which is very important to understand at the vehicle level, how the different systems interact with each other, whether it’s energetical, or thermal.
Secondly, scalable with respect to all the physics. So, you need to be able to look into the structures, you need to understand the thermal behavior, the energetical exchanges between the different systems. You need to understand the electromagnetic side of the motor, but also the dynamics. Within the electrical domain, for instance, you also need to understand how that motor and the different components of it will basically create electromagnetic fields in the context of electromagnetic compliance and interference. Now, with the breadth of this engineering physics comes also the need to look into the engineering physics with different methods. And that’s also where we provide a lot of methods that can help the engineer perform the task in the most efficient way. So, we have fluid dynamics capabilities. We have 1D system simulation capabilities. We have 3D CAE capabilities. And as Durrell already pointed out in the previous podcast testing is very important. You often need to bring a lot of evidence as proof of compliance to the authorities connected to these different domains.
Now, it’s also scalability in the lifecycle of the program of such an aircraft development and motor development. You need to be able to perform very early trade-off studies and that typically requires coarse models, because these coarse models basically allow you to very rapidly look into different configurations of, for instance, the cooling system of this electrical motor. But as you grow in the lifecycle of that development, you’ll need to be able to create very detailed models, very highly accurate models. And let’s say later in the development phase when you come to the verification phase, and when you maybe want to use these models in Model-in-the-Loop (MIL), Software-in-the-Loop (SIL) and Hardware-in-the-Loop (HWIL) type of verification, test benches on the integrated aircraft, you need real-time models, which are again, let’s say representing the physics of the system, but which allow you to run these models in a real-time way.
On top of that it’s not only about the digital twin, It’s also about how do you manage the processes with the different teams that you put in place? How do you manage the processes with your supply chain? And how do you manage, for instance, the processes to go through the verification and starting from the requirements that you have basically documented? Well, that requires, of course, the digital thread capabilities that we have. And for instance, verification management allows you to couple the requirements very much to, let’s say, the information that will be created around the test benches, whether it’s model in the loop, hardware in the loop type of test benches. But that verification management capability also allows you to take this data and to connect it to the simulations that you have done and basically keep the traces to the requirements.
Scott: Great! Well thanks, Thierry. Really good stuff. Dale, care to jump in here? We’re talking about the digital solutions and anything you want to add about Xcelerator, the digital twin, or digital thread at this time?
Dale: Yeah Scott, thanks. And thanks Thierry, it’s great stuff. And I think as he was saying, talking about all the different tools and solutions that we have available that you can put in your toolkit, as you build the digital twin of your program, and this can really scale to any size of the company and to all your different processes and that it really gives you that rich, robust understanding of what’s going on in a multi-physics, multi-domain way. Having this comprehensive digital twin, being able to bring different solutions in quickly in a very flexible and open ecosystem and so, with these tools, and with these approaches, and the understanding you can get, and the automation of the workflows between the different tools as you build your twin, it really helps foster innovation. As I’ve said before, when you take away these administrative tasks, you really allow your engineers, your technicians to start focusing on what they do best. That’s solving problems and coming up with new and creative solutions. So, getting on the path of digital transformation and really using that to go quickly into your design development certification is a big benefit a lot of our customers are getting out of digital transformation.
Scott: Well, you know what, guys? I’m afraid our time is up. Thierry, thank you so much for joining us today.
Thierry: Hey, Scott, nice to be here with you and Dale.
Scott: Thanks so much, Thierry. So no question, Siemens Aerospace and Defense is ahead of the curve when it comes to innovation. It’s no surprise, we’re bringing the technology of tomorrow to our customers today in a number of very real and proven ways, as you’ve just heard here. So, Dale, thanks for joining the show today.
Dale: Hey, no problem, Scott. I really enjoyed today’s topic. A lot of challenges, and it was a fun topic to talk about.
Scott: Dale, before we say goodbye could you tell our listeners what they can expect in our next episode?
Dale: Absolutely. I’m actually very excited about this next one as well. So, we’re going to be talking about the structural design of your eVTOL using composites and it’s a very up and coming topic and I can’t wait to talk about it.
Scott: Thanks Dale, I know you’d like to talk about composites. And of course, I’d like to extend my deepest thanks to our listeners. Glad you tuned into this podcast. Thank you, listeners.
At the top of the show I mentioned this is a five-part series. If you enjoyed this episode and you don’t want to miss any upcoming episode, please subscribe to Talking Aerospace Today on Apple iTunes, Spotify, or wherever you go to get your favorite podcast – that way, you won’t miss a single episode. You can also check out the links in this podcast’s description.
My name is Scott Salzwedel, and this is Siemens Talking Aerospace Today. I hope you’ll join us again for our next podcast. Until then, bye for now.
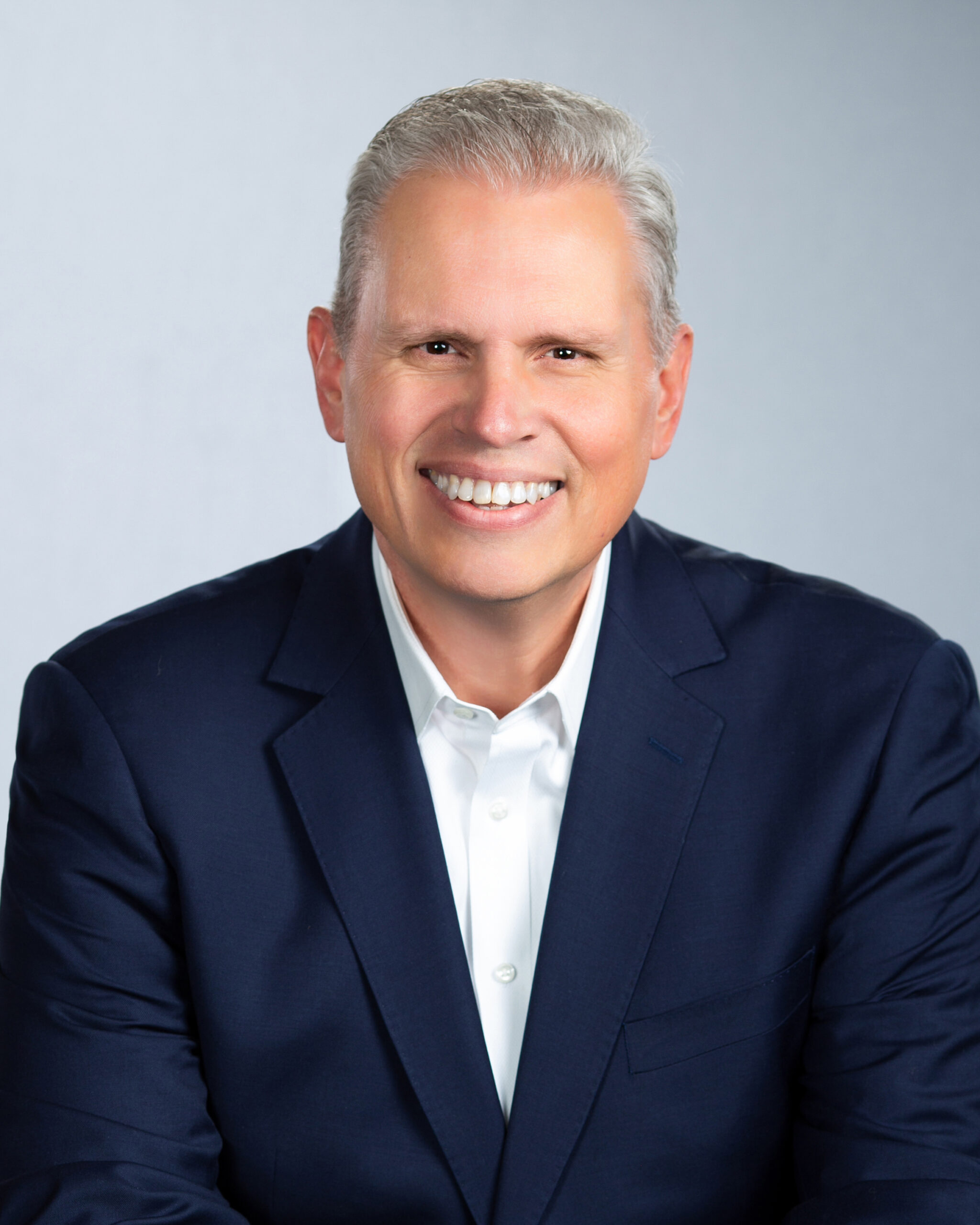
Dale Tutt – Vice President of Industry Strategy at Siemens Digital Industries Software
Dale Tutt is Vice President of Industry Strategy at Siemens Digital Industries Software. Dale leads a team of experts to develop and execute industry-specific product and marketing strategies in collaboration with the global product, sales, and business development teams. With over 5 years of experience in this role combined with extensive experience in the aerospace and defense industry, Dale has a deep understanding of the challenges and opportunities facing companies as they embark on their digital transformation journeys.
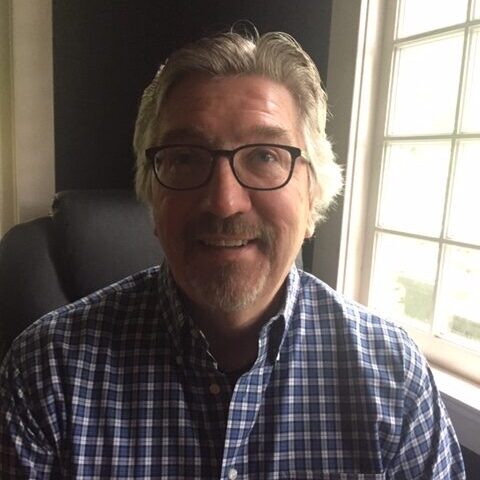
Scott Salzwedel – Host
Scott Salzwedel is senior technical writer and corporate communications writer involved in the Siemens Aerospace & Defense Industry and Siemens Capital. In addition to writer/host of Talking Aerospace Today, Scott is the writer of white papers, articles, blogs, videos and websites at Siemens.
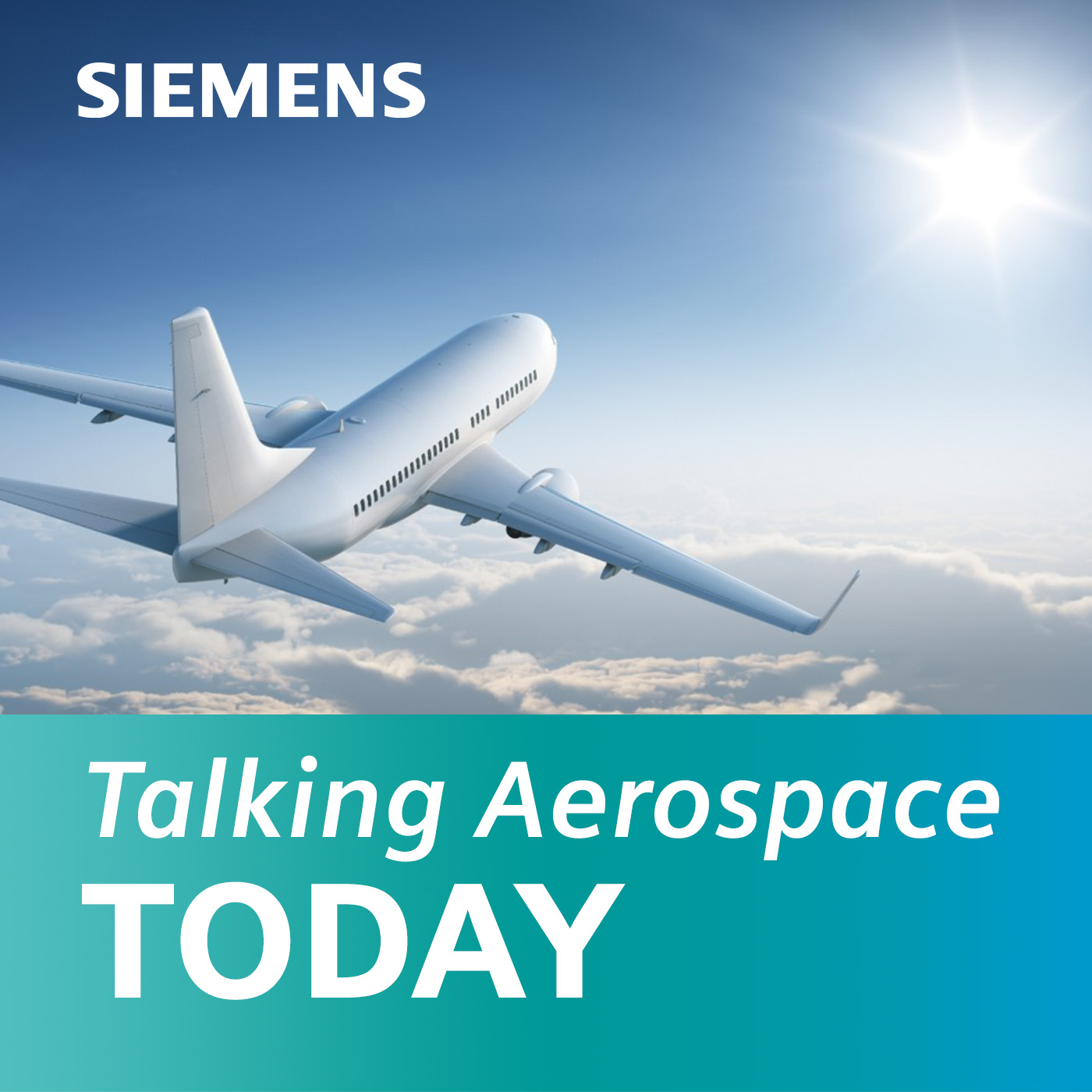
Talking Aerospace Today Podcast
The A&D Industry is at a serious inflection point. Transformation to the digital enterprise has opened up a new era in innovation and technological breakthroughs. However, complexity and compliance continue to hamper the best of efforts.
Join us as we explore how Siemens is turning complexity into a competitive advantage for many of our customers – today and well into tomorrow.