Versatile robot dresspack modeling with Kineo Flexible Cables
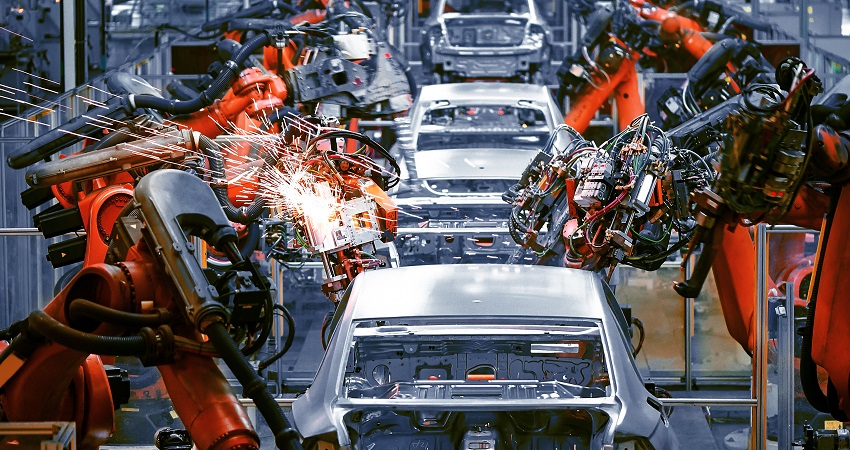
The reliable supply of energy and control data to industrial robots is essential to their efficiency. Robots are fitted with dresspacks that accommodate a variety of cables to transmit power and control, for example, pneumatic hoses, electrical cables and shielding tubes. Because damage to these cables often results in serious downtime, simulating the operational efficiency of a dresspack prior to deployment helps to safeguard productivity on the factory floor.
Kineo Flexible Cables is a software component that’s designed for integration into any software application that needs to model the deformation and configuration of compliant cables. It’s particularly well-suited to simulating the energy supply systems for industrial robots and enables the physical performance of hoses, cables and tubes to be evaluated.
In this article, we take a look at how the latest version of the software can simulate the sophisticated solutions that are available from dresspack suppliers to mitigate against cable damage.
Simulating cable attachment systems
Continuous and variable robot motion can cause repeated strain on cables through stretching, twisting or bending, resulting in deterioration and ultimate failure. To minimise damage, dresspacks offer a range of cable attachments to ensure cables have appropriate freedom to move in such a way that strain is reduced. For example, a ball-joint termination provides strain relief by allowing the orientation of the cable at its end to continually adapt to the robot’s motion.
Kineo Flexible Cables offers a comprehensive set of tools for modeling the growing range of cable attachments on the market, from ball-joint terminations and simple rotating clamps to more sophisticated attachments that not only reduce strain on the cable, but also manage an additional risk: surplus cable. Cables must be long enough to satisfy the robot’s full operational range, but over shorter operational ranges, cable slack can develop and interfere with the robot and/or its work environment. One solution to this problem is to deploy a sophisticated cable attachment system, such as the structure simulated in the video below.
The cable is attached with a retractable pulley to a free-sliding joint in a cantilever. The cantilever can also rotate freely to accommodate the motion of the robot/cable. As a result, the robot is equipped with sufficient cable to operate over its full range, while any slack cable is restricted to a safe zone, clear of the robot.
During the simulation, Kineo Flexible Cables takes account of all specified attachments and computes the path/deformation of the cable according to its material properties and by modeling any contact between the cable and the robot/environment. The software can also diagnose possible issues by reporting potential collisions and generating cable stress calculations.
Another solution to the problem of surplus cable is a cable retraction system. These devices are fitted to the robot and safely house the cable, feeding or retracting cable as required – you can see an example in the video, just above the “elbow” joint on the robot. Kineo Flexible Cables can model various retraction systems and you can learn more in our previous article on the topic.
Complementary robot simulation/control software from Kineo
Siemens Digital Industries Software also offers you complementary solutions to extend and accelerate your robot simulation and control applications:
- KineoWorks – automatically compute collision-free trajectories for industrial robots and machine tools. Available as a component with a rich GUI, software vendors, system integrators and OEMs can create custom robot simulation and control applications easily with reduced risk and time-to-market.
- KineoWorks Interact – build a rich Graphical User Interface for your software applications quickly and easily with tools for 3D visualization, user-interaction, data import/export, etc. with the minimum of coding.
- Kineo Collision Detector – perform high speed collision analysis on mesh surfaces and point cloud data in motion simulation environments such as robotics simulation.
Further information
Learn about our latest innovation for programming multi-robot work cells
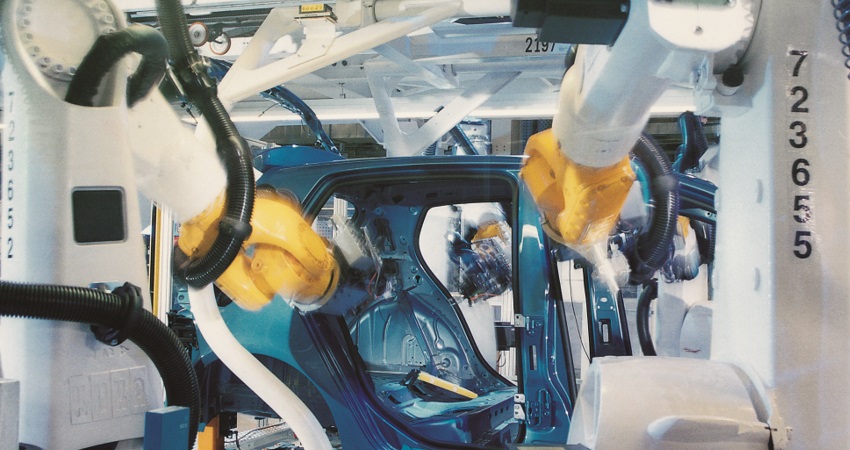