Three ways simulation lowers costs for manufacturers
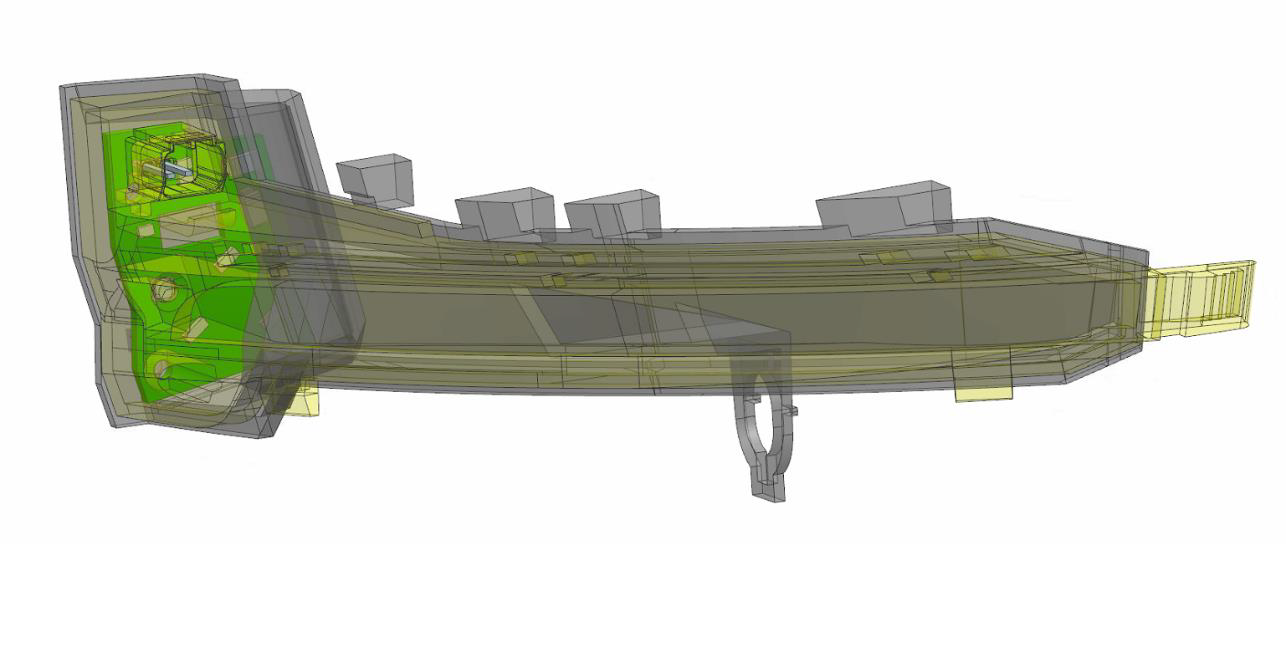
The automotive lighting manufacturing sector will reach a market share of $28 billion (CAGR 6.7%) within five years. Working with clients in this sector, Siemens Solution Partner, SimOfis, understands how technology drives advances in automotive lighting and how far the market has come since the days of oil or gas-driven headlamps of the 1880s. Now, with electric vehicles on the rise and light technology constantly evolving, competitive manufacturers are racing to stay on top while continuing to innovate, save time and reduce costs.
In the automotive lighting manufacturing process, heat emissions and component weights make a big difference. In addition, vehicle headlamps require rigorous thermal testing. Today’s top manufacturers turn to simulation software to solve these challenges. And deploying the right solution is critical.
FEKA Automotive is a Turkish automotive lighting and parts manufacturer and longtime customer of SimOfis. We, at SimOfis, helped the company deploy Simcenter™ FLOEFD™, part of the Xcelerator™ portfolio, the comprehensive and integrated portfolio of software and services from Siemens Digital Industries Software. The software was instrumental in driving successful pre-production simulations for FEKA that guarantee cost-effective, world-class headlamp manufacturing processes.
“Simcenter™ FLOEFD™ is placed into the middle of our workflow. We use it for every single automotive lighting product that we develop.”
Erol Kocabıyık, Deputy R&D Manager, FEKA Automotive
Technology-driven time and cost-savings
As a Siemens solution partner specialized in Simcenter FLOEFD, our team at SimOfis understands that the printed circuit board (PCB) geometries and the outer housing are critical components in automotive lighting that must withstand severe thermal conditions. While the lens and plastics are included in the housing, it’s the electronics, including LEDs and diodes attached to the PCB, that make testing more complicated. To achieve rapid, high-quality and cost-effective product design and thermal performance, SimOfis used the computational fluid dynamics (CFD) simulations in Simcenter FLOEFD to help the FEKA Automotive R&D team predict the behavior of fluids and adjust product specifications accordingly — before any tangible prototypes were produced.
Simcenter FLOEFD helps improve quality
Remove guesswork to achieve rapid innovation
In automotive lighting manufacturing, simulating and testing thermal performance are considered two essential parts of headlamp production. While CFD simulations can be very time-consuming, FLOEFD accelerates workflows through its CAD-embedded structure, where simulation results, model creation and CAD geometry preparation are completed within the software. When sent to thermal test cabins at the FEKA Automotive facility, the results showed FLOEFD™ simulations are incredibly close to actual test results.
Accelerate workflows to facilitate more choices
The FLOEFD CAD embedded structure also allows FEKA Automotive to expedite its iterative design process by providing numerous design options for consideration within a short period. Scanning a vast design space helps to select the best one quickly.
“With Simcenter FLOEFD, we were able to conduct way more simulations than we would with traditional CFD software. Previously, some samples predicted to be safe appeared unsafe during tests, but FLOEFD corrected these challenges and reduced costs significantly.”
Erol Kocabıyık, Deputy R&D Manager, FEKA Automotive
Optimize products for rapid development
FEKA Automotive has been a FLOEFD customer for more than four years, and the group views it as a crucial tool for lighting product development. Not only has the R&D department been enabled to develop more products each year, but time is no longer wasted during meshing, design optimization, or model creation processes. Now, displaying results, model creation and CAD geometry preparation are all completed through the same interface, comparing different designs faster and easier.
Through simulation, products are well optimized for rapid development and have better thermal performances, decreasing time to market and saves money for manufacturers. Working with FEKA Automotive, SimOfis reduced simulation times spent on model preparation, meshing and solving phases plus decreased physical prototype production while producing five times the number of simulations, in the same amount of time as its previous traditional CFD software allowed – bringing more products to market each year.
Visit the Xcelerator™ portfolio for more information about the comprehensive and integrated portfolio of software and services from Siemens Digital Industries Software.
SimOfis is a Siemens solution partner in Turkey specializing in Simcenter™ FLOEFD™ and focuses on its vast expertise in computational fluid dynamics. Salih Bilgiç, CFD Application Engineer and Çağrı Bostancı, Sales Manager at SimOfis, contributed to this blog.