How Reusing Parts Cuts Engineering Costs

How much time do you think your engineers are spending recreating standard and supplier parts? Take a guess and read this survey from CADENAS, who interviewed engineers from more than 500 companies about their part search habits. According to the study, engineers spend at least 30-minutes a day recreating standard or supplier parts. The average is closer to an hour per day. What a waste of time!
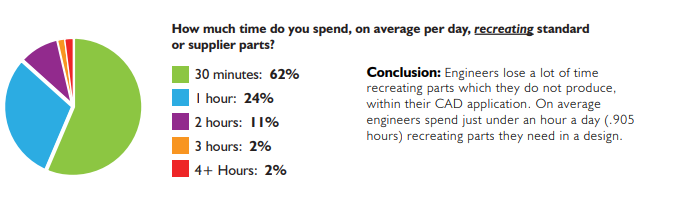
Part costs and engineering time add up quickly
Each part entered into a library like Teamcenter has engineering costs associated with it. When engineers can’t easily find parts in Teamcenter, they redraw parts that already exist, which adds costs – as much as 10x! Without a reuse process in place, parts are typically only used in one project.
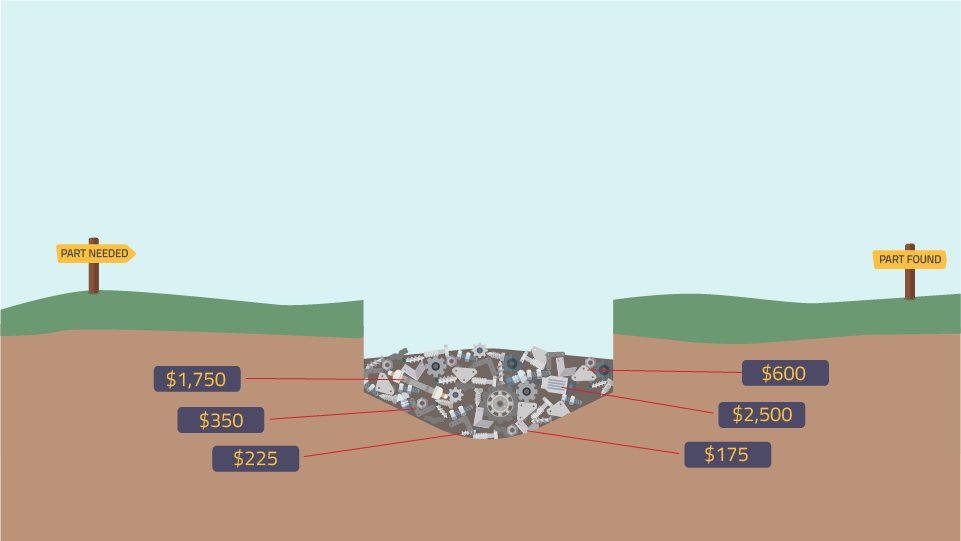
Duplicate parts are a cost multiplier
Let’s look at a real-world example to illustrate how duplicate parts get created.
Imagine that Bob is an engineer who works for you. Bob is designing a conveyer belt. He needs a bracket with specific characteristics, but he can’t find one that will work for his project in Teamcenter. So, he models one using NX.
Bob names the part, angle-plate-5.prt, and doesn’t add any attribute data, dimensions or specifications. The bracket works for his design, so he continues with his project.
A few weeks later, Bob’s cubicle neighbor, John, is working on a conveyer for a different customer. John needs a bracket for his design as well. He performs a search in Teamcenter using relevant attribute data, but he can’t find what he is looking for because no brackets in Teamcenter match his search criteria.
So, what will John do? Well, he models a similar bracket to the one Bob created! John has his special naming convention that is quite different from Bob’s. He also always inserts his initials at the beginning of his file names so that he can find them in the future.
John is your classic overachiever, so naturally, he adds some attribute data, but only fields that are relevant to his current project. He names the bracket, JW_3x4_L-Bracket_Holes-8_D-1-4.prt.
So, now interchangeable brackets exist inside Teamcenter without proper attribute information, dimensions, specifications, or consistent naming conventions. When another engineer needs a similar bracket in the future, I’ll bet it gets added a third time.
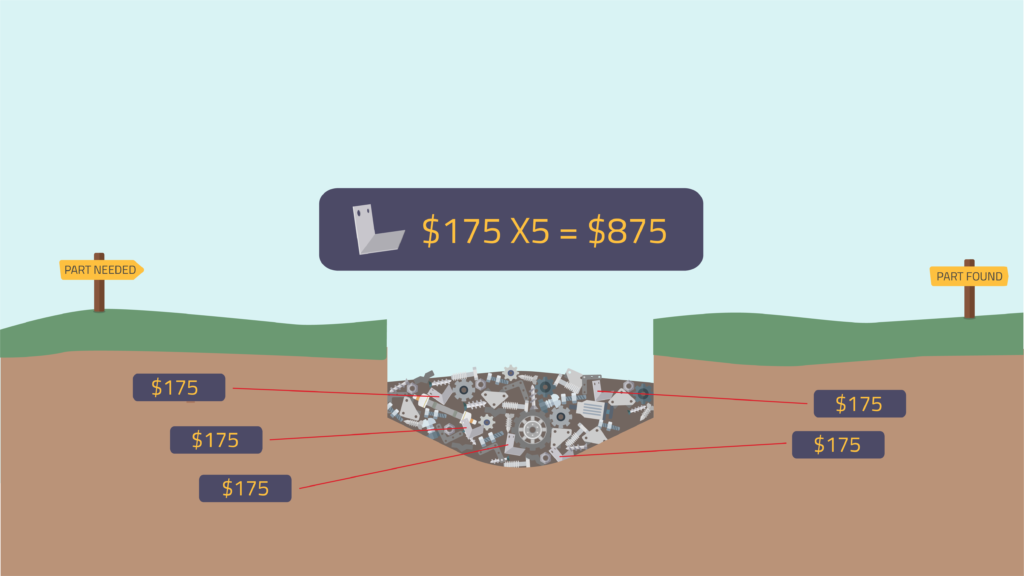
In the example image, a bracket that costs $175 multiplied five times is $875, when adding downstream processes that typically 10x the costs, the duplicate brackets cost $8,750 instead of $1,750.
If introducing a bracket costs this much, how much do complicated vendor models cost your company to recreate multiple times?
Create a part reuse strategy with CADENAS PARTsolutions and Teamcenter
By focusing on reusing parts, your company can shave off nearly 30-minutes a day of wasted work from each design engineer AND eliminate most of the redundant efforts downstream.
It is essential to learn how to reuse digital parts if you want to increase your engineering efficiency, cut costs, and increase speed to market for new designs.
To see how much time reusing parts can save your engineers, download the Engineering Reuse Time Savings Calculator from CADENAS PARTsolutions.
Joseph Lewin is the Product Marketing Manager for PARTsolutions software. His goal is to enable engineers to work more efficiently by providing resources and education about improved engineering processes.