Hidden champion of digitalization [ARTICLE]
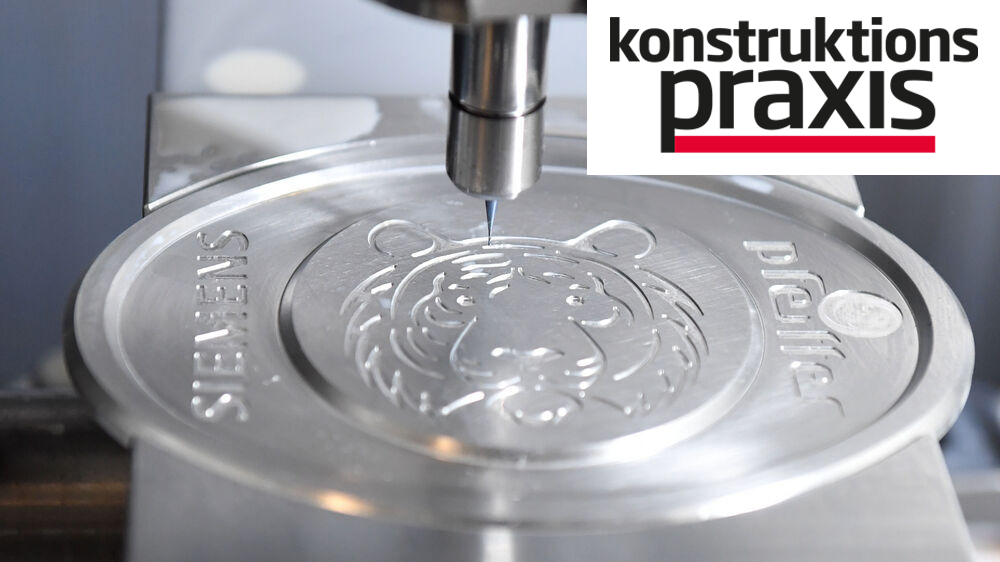
How can a small part manufacturing company compete globally? Many manufacturers are faced with this question as the future of their business depends on it.
Konstruktions Praxis, a German magazine that covers “everything design engineers need”, explained in a recent article titled: “Connectivity opens up growth opportunities” how W.A. Pfeiffer, manufacturer of high precision components, is able to grow their business and stay competitive by implementing an end-to-end CAD-CAM-CNC process chain, transforming their business into a digital machine shop.
The greatest challenge for us is that we can no longer physically expand at this facility.
Andreas Pfeiffer, CEO
A buzzing shop floor
Anyone who visits the medium-sized metalworking company in the small town of Zirndorf, west of Fürth and Nuremberg, wouldn’t suspect that they’re looking at a real “hidden champion” of digitalization. In contrast to the rather quiet environment, the family-owned company with only 25 employees and 16 CNC machines is busy machining parts and system components for a wide variety of applications such as optical systems, precision mechanics, machinery, and medical devices.
Business is going well, even if the market has become more challenging due to continuously increasing complexity of components and shorter throughput times, says Andreas Pfeiffer, owner of W. Andreas Pfeiffer – Maschinen- und Apparatebau: “The greatest challenge for us is that we can no longer physically expand at this facility.”
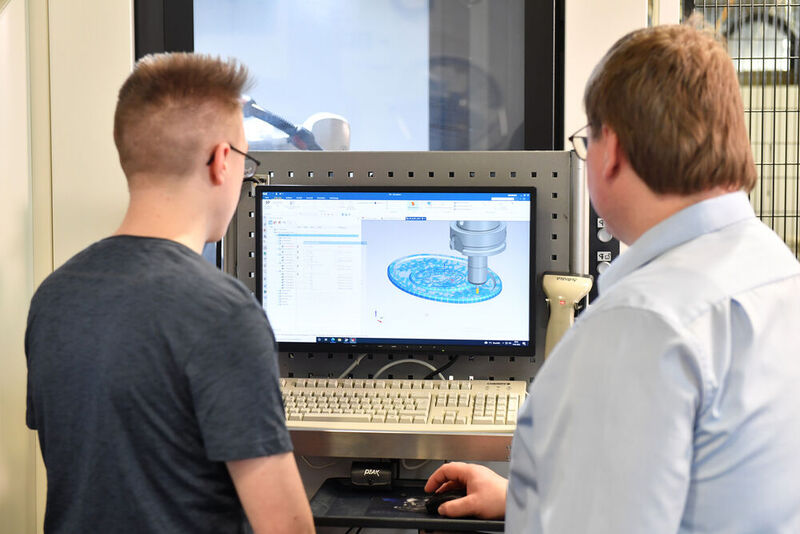
Integrated software for higher productivity
To address these challenges, Pfeiffer needed to automate and connect their entire production process. They decided to rely on Siemens solutions to transform their business as they provided them with the advanced manufacturing capabilities used by many top-tier companies.
With our comprehensive and integrated software, which includes NX CAM, Teamcenter, Opcenter APS, and Mcenter (formerly Sinumerik Integrate), this end-to-end, digital process chain has now become reality at W. Andreas Pfeiffer. From order acceptance to manufacturing to invoicing, data flows seamlessly, ensuring that all the team members have access to the correct data. The data is managed centrally, connecting the people, systems, and machines.
More automation and smart manufacturing solutions
This completely digital part manufacturing process is the result of over 20 years of innovations by this small yet forward-looking company. Mr. Pfeiffer and his team have doubled down on these activities in recent years: “We have increased our efforts to standardize our processes and data for the tools, programming templates and clamping devices. To see all these ideas come together now and to work with this digital process chain for the first time is simply terrific.”
We have increased our efforts to standardize our processes and data for the tools, programming templates and clamping devices. To see all these ideas come together now and to work with this digital process chain for the first time is simply terrific.
Andreas Pfeiffer, CEO
How the digital manufacturing process works
W.A. Pfeiffer’s typical manufacturing process begins with incoming customer orders. The order is created in the ERP system and in the Teamcenter software at the same time. The necessary materials are then ordered, and the due dates simultaneously planned using the Opcenter APS software. “All tools work together seamlessly, which makes coordination much easier,” says Andreas Pfeiffer.
The job data is then seamlessly transferred from Teamcenter to NX. The machining operations for all the CNC machines are programmed, postprocessed and simulated with NX CAM using a digital twin. The digital twin accurately represents the workpiece, fixtures, machine, cutting tools, as well as the machining process. That way, they can program in the context of the machine, enabling the engineers to create intelligent toolpaths for the most challenging components. Next, the CNC programs and tool lists are seamlessly transferred to production using Manage MyResources.
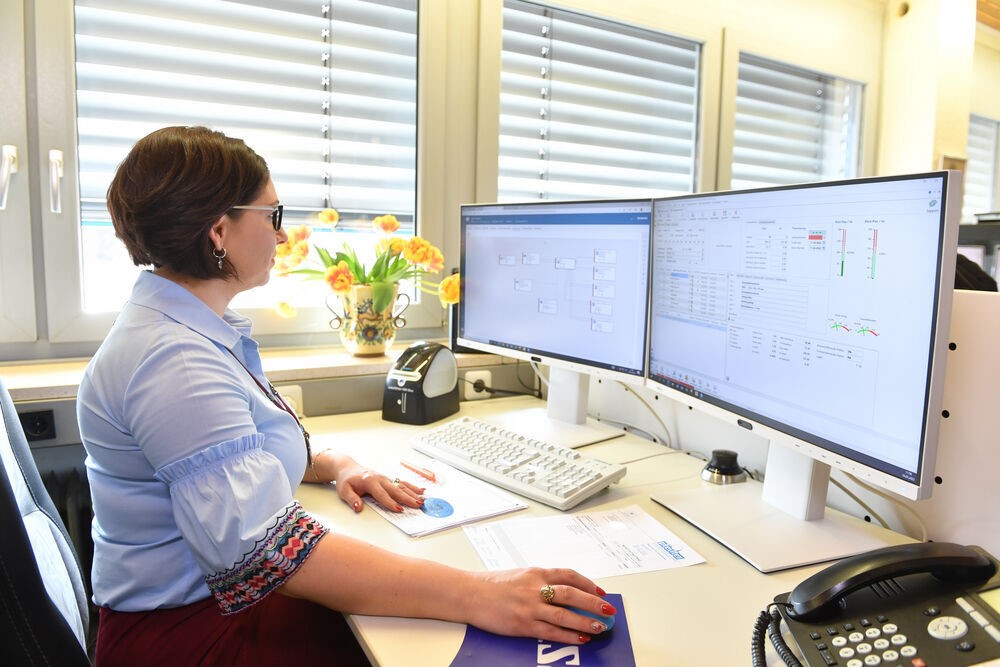
For Andreas Pfeiffer, the investment in the new software has already paid off – “Just by analyzing our processes during the implementation, we were able to improve many processes.” His co-workers have accepted these new tools as well: “We no longer have duplicate data storage; we have much better transparency across all processes. I expect that we will be able to reduce setup times by up to 50% overall.”
Read the full German article on Konstruktions Praxis or view the English pdf below: