Meeting rigid-flex pcb design challenges with Xpedition
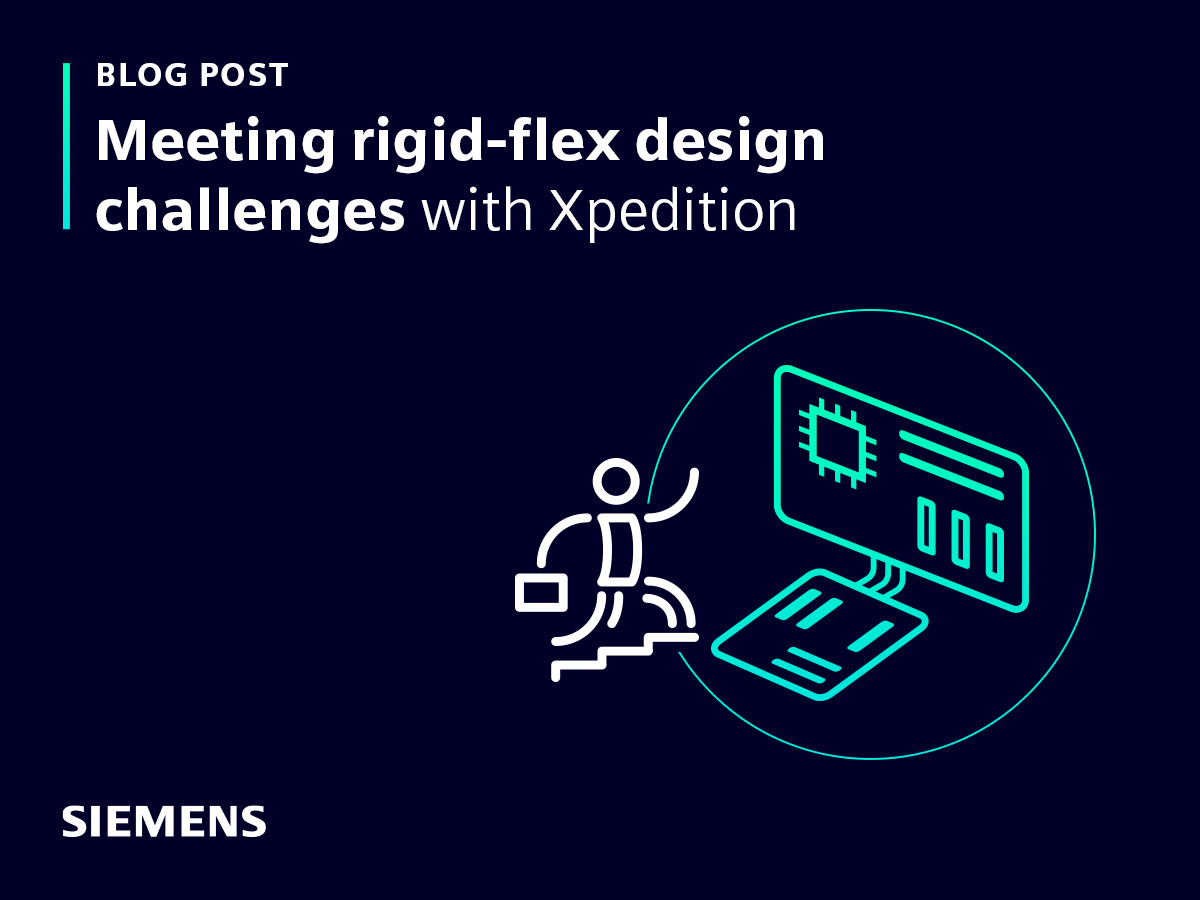
Apart from the typical challenges of PCB design, flex and rigid-flex PCB designers encounter a whole set of unique obstacles. If not handled properly, these hurdles can result in design failures, re-spins, and long-term reliability problems. Let’s take a look at some of these challenges.
Multiple board outlines, each with separate layer stack-ups:
Rigid-flex pcb designs have multiple regions, each with a different layer stack-up. These stack-ups need to be defined during the design process so that all downstream operations, like electrical and manufacturability analysis, and fabrication output, can use them. With Xpedition, creating a rigid-flex pcb design is as simple as drawing the multiple board outlines and assigning a layer stack-up to each one. Each board outline is given a name to easily identify them when they partially or completely overlap.
Special layer types, such as adhesive, cover layer, and stiffener:
A cover layer is like a protective coating that goes on top of the metal foil in a flex design. It’s super helpful because it offers better protection against wear and scratches compared to solder mask. Plus, it helps the metal foil stick to the base material, so it’s got awesome adhesion. You can use a sheet of cover layer that covers the whole design and gets embedded in the rigid stack-ups of the rigid-flex pcb design. They call this an “Embedded cover layer” because it’s all embedded into the rigid sections. In Xpedition, the cover layer is part of the layer stackup, creating an embedded cover layer.
Stiffeners are these cool pieces of rigid material that get bonded to flex regions to make them all “rigidize”. This helps you assemble components on the flex area or give you rigid mounting holes. The stiffener material can be conductive, like metal, or non-conductive, like plastic or FR4. In Xpedition, you define the stiffener as a layer in the layer stack-up, but you also draw the actual stiffener as a stiffener shape on that layer.
For the adhesive layer, you’ll need to define it in the layer stack-up. But just like stiffeners, you can draw one or more “adhesive shapes” on that adhesive layer.
Bending and folding of the assembly:
The main reason for creating a flex design is so that it can be easily bent or folded. As a designer, it’s important to determine where your design will bend, how it will bend, and what design “quirks” you can tolerate in the area affected by the bend. In Xpedition, there’s a draw object called a “bend area” that specifies the location of the bend.
The properties of the bend area determine the extent of the bend: the angle, the direction (positive or negative angle), and the sharpness of the bend (the bend radius). While the center of the bend can be represented as a line, the region on the flex board that is affected by the bend is wider. Naturally, the bend region becomes wider as the bend angles and bend radius increase.
The need to route along curving boards without causing reliability issues due to metal stress
When you’ve got a curving flex cable and a bunch of signals that need to fit in with a tight squeeze, you need a special routing algorithm that can follow the board outline’s shape and automatically insert all the required signals.
Xpedition has several ways to solve this challenge. It’s vital that all curved traces be routed with true arcs rather than with approximated segmented arcs, as was common in the past. Even cases where arcs were segmented into as many as 64 segments can still get stress fractures due to the arc not being completely round. In Xpedition, all curved traces use true arc primitives.
Plane and shape fills that conform to flex requirements
It’s generally not acceptable to have solid plane fill in bend regions in a flex design. Instead, the typical pattern is cross-hatched. However, for best reliability and to prevent metal fatigue, the cross-hatched pattern must be rotated 45 degrees off the bend line.
Note that the board strip that bends may be at any angle and the bend line itself can be angled, so the 45 degrees off the bend line can actually be any odd angle value. In Xpedition, you can set a unique hatch angle for every fill that requires it using the “Plane Classes and Parameters” dialogue.
Design Rule Checking (DRC) that understands specific flex-rigid rules
Xpedition is unique in its ability to generate and maintain these dynamically and have a DRC that reports if a tear drop fails.
Signal and Power integrity of a multi stack-up board
Most designs today require some level of signal integrity analysis as part of the design process. This is advanced enough in single stackup designs, and now in flex-rigid pcb designs, that we have boards with multiple rigid stack-ups, multiple flexible stack-ups, partial adhesive in the stack-up, and stiffeners that must be properly modelled in order to get correct analysis results.
HyperLynx, developed in collaboration with Xpedition, is a powerful tool designed to analyze flex-rigid designs. It understands how interconnects pass through various stack-up scenarios and applies appropriate modeling to ensure a functional design, even with complex stack-ups.
Manufacturability analysis
Flex circuitry is more difficult to manufacture than rigid PCBs, and the best way to ensure that designs are manufacturable is to run DFM checks throughout the layout process as well as running DFM on the manufacturing release process. Running DFM checks on PCBs with Valor NPI can reduce respins on average by 57%. For rigid/flex, it is even more critical to ensure manufacturability before sending the product model data to the fabricator. Applying DFM to PCB designs results in more time spent designing and less time fixing.
Flex fabrication output that safely conveys design intent to FAB
With a complex design that is a mix of rigid and flexible boards, each of which might have a unique layer stack-up, it’s clear that board fabricators have a challenge in figuring out what the designer wants to build. Even educated guesses are bound to lead to misunderstandings that can lead to very costly situations. Avoid the guesswork by using ODB++ and its built-in constructs as a fabrication data format to safely communicate all flex-specific information.
Xpedition helps alleviate rigid-flex pcb design challenges
Traditionally, a designer would use his/her experience to navigate around these problems and apply workarounds as their PCB design tools failed to understand what was being designed. With designs becoming more and more complex, and an increasing demand for ever-shorter design times, its obvious designers are stretched too thin. Using PCB design tools like Xpedition, Hyperlynx, and Valor NPI can set you up for success.
To dive deeper into rigid-flex pcb design, download the full white paper: Meeting flex and flex-rigid design challenges or watch this webinar: Rigid-flex design: practical tips and best practices.