3 Ways Digitalization Helps Manage Automotive Harness Design Complexity
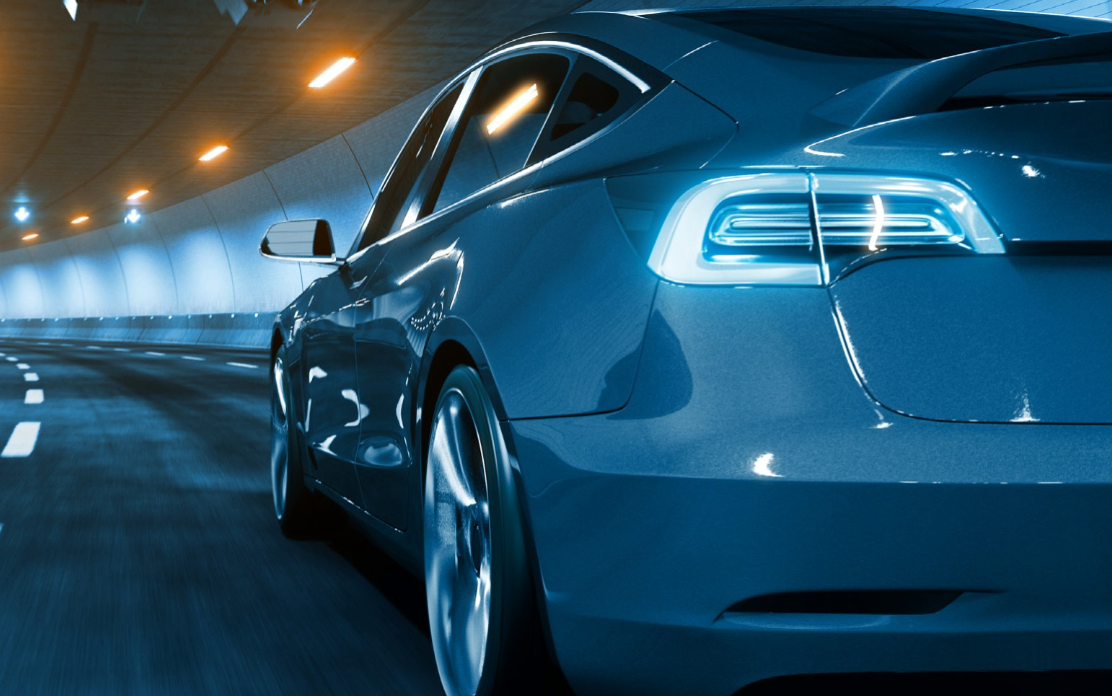
The automotive industry has been rapidly evolving with the advent of more advanced electronic systems in vehicles. From electric vehicles (EVs) to autonomous driving features, the increasing complexity of automotive designs has pushed the limits of traditional engineering methods, including automotive harness design complexity.
Automotive wire harness are the components responsible for transmitting power and information throughout the vehicle. Wire harnesses contain over 1.8 miles of cabling, weighing about 27 pounds, and there are thousands of possible configurations. Not only are they getting more complex (and heavy), they’re generating an increasing volume of data.
Managing the design and production of these incredibly complex wire harnesses is a formidable challenge, and companies are turning to digitalization for more efficient solutions. In this post, we’ll examine three ways in which digitalization helps to manage automotive harness design complexity, and how Siemens Xcelerator can streamline design, testing, and production.
1. Enhanced design accuracy and efficiency
Digital tools enable engineers to create more accurate and detailed designs while significantly reducing the time required for design iterations. Using sophisticated software, engineers can visualize the entire harness in 3D, allowing for a better understanding of the spatial relationships and constraints within the vehicle. This approach helps to minimize the number of errors that might occur due to incorrect wire length calculations or improper connector placements.
Simulation software plays a crucial role here, offering the ability to test various configurations without the need for physical prototypes. For example, simulation can predict how the harness will behave under different environmental conditions, such as heat and vibration, ensuring the design is robust before any physical model is made. This not only cuts down development time but also drastically reduces the costs associated with iterative physical testing.
2. Streamlined collaboration among teams
One of the most significant benefits of digitalization in harness design is better collaboration between different teams. As automotive design involves multiple disciplines—electrical, mechanical, safety, and production—effective communication and data sharing are crucial. Digital tools help to create a digital thread, which enables real-time updates and data sharing, ensuring all teams are on the same page.
Cloud-based platforms allow team members to access the latest designs from anywhere in the world, fostering a collaborative environment that is not limited by geographical boundaries. Changes made by one engineer are instantly available to all other members of the team, including those working on interfacing systems within the vehicle. This integration reduces the risk of data mismatches and delays, leading to a more streamlined production process.
3. Automated documentation and compliance
Compliance with industry standards and regulations is a critical aspect of automotive design. Digitalization aids in this area by automating the generation of necessary documentation for compliance and testing. Software can automatically create detailed reports and schematics of the harness designs, which are essential for both internal quality control and regulatory submissions.
Importantly, these digital tools are updated with the latest regulations and standards, ensuring that the designs comply with current requirements without requiring manual oversight. This automation significantly reduces the likelihood of compliance issues, which can cause costly delays and redesigns if discovered later in the development process.
Siemens Xcelerator: Your key to a digitalized harness business
The complexity of automotive harness design demands sophisticated solutions that can only be provided by digital technologies. By enhancing design accuracy, streamlining collaboration and automating documentation, digitalization not only simplifies the design process but also enhances the overall efficiency and reliability of automotive production.
To effectively address these challenges, many industry leaders are turning to comprehensive digital solutions like Siemens Xcelerator. This integrated portfolio of software, services and an application development platform is specifically tailored to accelerate digital transformation, allowing companies to innovate and realize the benefits of digitalization more rapidly. With Siemens Xcelerator, automotive companies can reduce time to market, enhance flexibility and ensure compliance and quality—key factors in thriving in the competitive automotive industry.
Watch this on-demand webinar to learn how you can leverage the power of Siemens Xcelerator to navigate the complexities of automotive harness design and drive your projects to successful completion.
You may also want to download our whitepaper, “Digitalizing your wire harness business,” to learn why digitalizing the wire harness business is no longer a question of whether we should, it is more a question of how fast we can do it.