Maintaining sustainability in the wiring harness industry
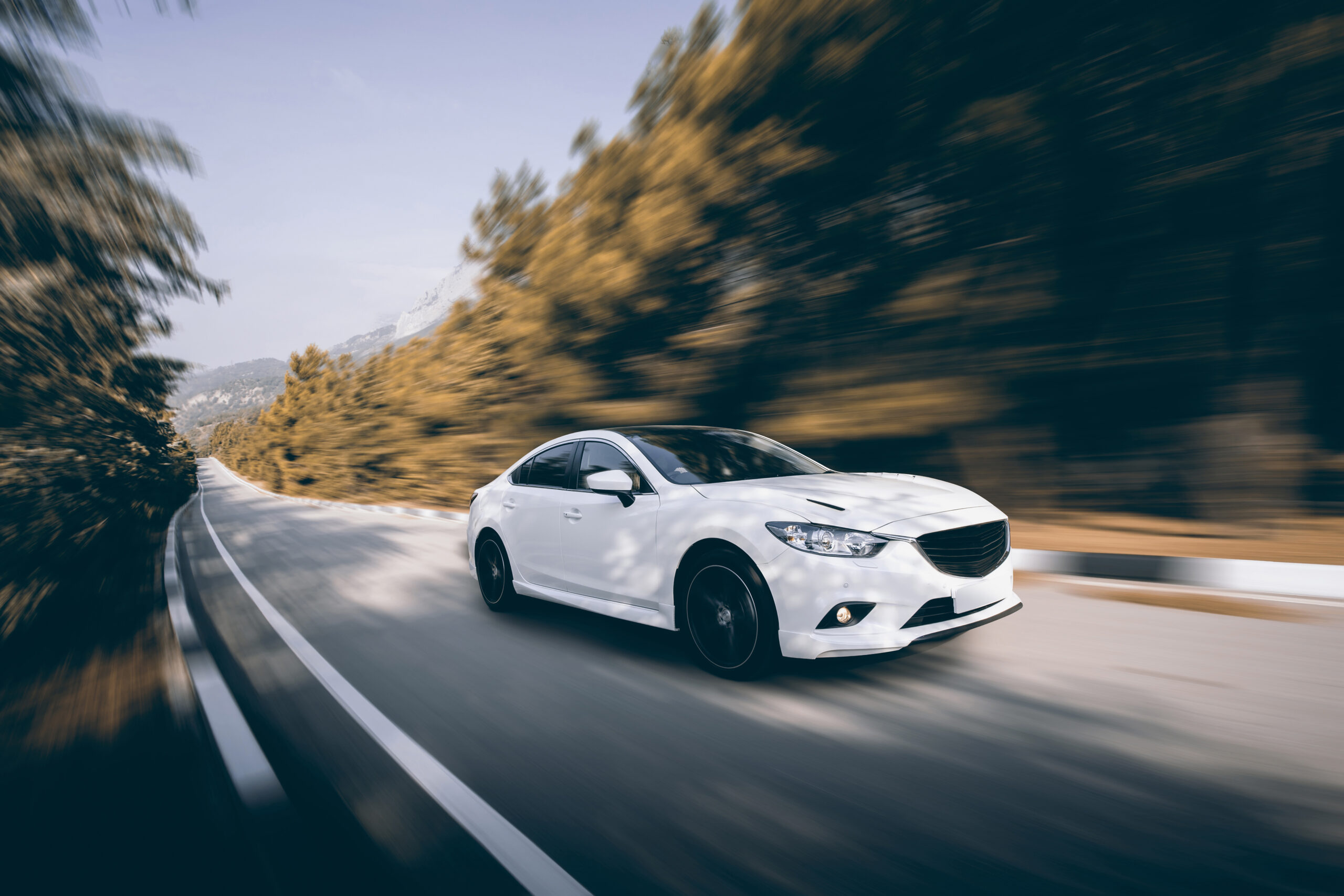
A few months ago, we posted about what sustainability challenges the automotive and heavy equipment industry face, and how the Siemens Xcelerator portfolio can enable solutions.
In our original blog post, Automotive and heavy equipment industries’ role in achieving viable sustainability, we mentioned an upcoming whitepaper on sustainability that closely looks at the importance of digital twin technology. Reliably quantifying and tracing the environmental impact that products and processes have can help make better design decisions throughout the value chain. The white paper is now available for download.
In this paper, we explore how maintaining sustainability in the wiring harness industry requires a high level of transparency. Engineers can achieve this by creating an end-to-end digitized process chain. By tracking products over the entire lifecycle, a comprehensive digital twin allows manufacturers to continuously improve their wiring harness designs and prevent faults from occurring. They can do this by adding information about the product specifications and process history. Adding product carbon footprint (PCF) information to the comprehensive digital twin can enable manufacturers to incorporate environmental impact data into product and process design to produce more sustainable products.
Specifically, manufacturers can achieve this by creating effective sustainability key performance indicators (KPIs), reducing weight, substituting materials or increasing recyclability. The white paper discusses how comprehensive digital twin technology can enable wiring harness manufacturers to create more sustainable electrical and electronic (E/E) systems. Manufacturers can use Capital software as part of the Siemens Xcelerator portfolio, the comprehensive and integrated portfolio of software, hardware and services, as part of the solution.
One example is looking at how using the generative workflow in Capital can help to design for sustainability.
Using Capital to design for sustainability
With the increase in electronics in modern-day vehicles, traditional design methods do not always meet the needs of expanded E/E system complexity. That is because conventional wire schematics creation is time-consuming and prone to errors. To move forward, automotive manufacturers and suppliers should consider a generative approach. With generative design, engineers can quickly adopt to develop new products based on meeting design constraints.
As companies face increasing pressure to get automotive products to market faster while also adhering to sustainability practices, using generative design tools is now a necessity in product development. Platform generative design tools automatically generate accurate wiring designs to allow for configurations at the platform level, providing a mechanism to optimize designs, including showing tradeoffs for weight, power consumption and more while reducing time and cost.
Designing wiring schematics requires a deep understanding of the vehicle topology and complexity, so companies are shifting away from legacy automotive design flows. Today, generative design tools are available to automatically generate accurate wiring designs for all allowable configurations at the platform level.
This platform generative flow supports the “right-first-time” design approach, as well as:
- Enables powerful automation and an intuitive user interface to streamline the design process
- Supports the development of industry-leading products that serve as a competitive differentiator
- Provides correct construction and fully optimized designs that shorten time to market and reduce costs
Learn all about generative design in our webinar, Solve automotive wiring harness complexity with a platform generative flow.
With this generative workflow, using Capital enables users to rapidly design, iterate and optimize as early as possible in the development process. This enables engineers to optimize electrical and electronic system architectures against targets such as cost, weight and network bandwidth and design them based on sustainability targets such as reduced CO2 footprint, reduced weight and increased recyclability. Designers input typology, logical connectivity, complexity and device interfaces into Capital Integrator which delivers consistent and repeatable wire connectivity based on customizable design parameters (rules). Adjusting these design parameters allows the user to generate wire connectivity as needed, which helps integrate sustainability requirements into the initial design phase.