Key challenges facing the wiring harness industry
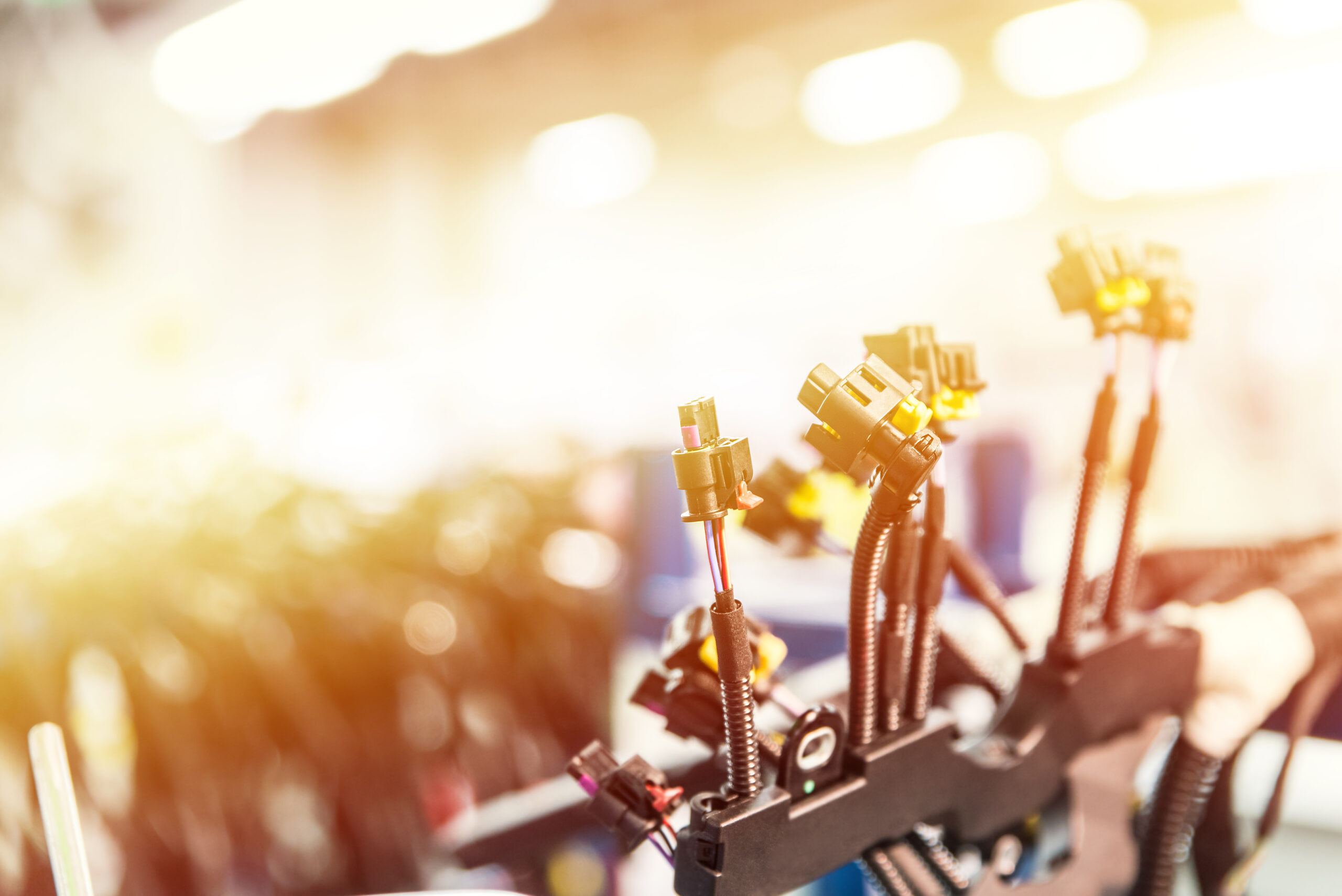
A number of trends are impacting the automotive industry, and specifically wiring harness design and manufacturing: electrification the advent of autonomous vehicles, enhanced connectivity and mobility and mass customization. New technologies, materials and architectures are emerging in vehicle design, introducing additional complexity, and new market entrants are creating intense competition for incumbent suppliers.
Although wire harness manufacturing has been around for over a century, today’s manufacturers continue to face myriad challenges:
Low margins: Historically, wire harness manufacturing has been a low-margin business. Harness manufacturers are under constant cost and price pressure from OEMs looking to reduce their own manufacturing expenses, even as material shortages resulting from supply chain disruption since the beginning of the Covid-19 pandemic are driving up the price of parts. All of this leads to lower profit margins and tighter budgets.
Stringent requirements for quality and delivery: Quality requirements are extremely high, yet delivery schedules are tight. Design changes often happen late in the design process, causing delays. Meanwhile, legislation requiring traceability and documentation puts more pressure on manufacturers to implement continuous verification and validation processes. For example, ISO 26262 requires a certain level of redundancy in wire harnesses for autonomous vehicles.
Complex processes and continuous change: The wiring systems in today’s wire harnesses are complex assemblies of multiple harnesses with vast amounts of components and an endless number of possible configurations. All these components must be managed and maintained in a database. To make matters worse, the majority — 80-85% — of a wire harness is still handmade.
Loss of tribal knowledge: When senior designers leave the company or retire, it’s a huge risk. Without a way to capture tribal knowledge comprising organizational IP and best practices that they’ve acquired during their years of hard work, there’s no efficient way to pass it along to new team members.
But fear not! Model-based workflows can unify previously fragmented domains of design and manufacturing by automating data exchange and facilitating cross-domain decisions. Tribal knowledge is captured by integrating design rules that support automation and provide consistency across the engineering process.
The three pillars of model-based harness engineering include:
- Digitization: Use digital models of the wiring harness product and the manufacturing process to create an optimized digital twin.
- Automation: Configurable rules and constraints not only help capture design guidelines, industry best practices and organizational IP, but also subsequently drive rules-based automation of the harness design and development flow.
- Data re-use: Instead of recreating or re-entering data, create data once and re-use it to the greatest extent possible by all upstream and downstream consumers.
Leveraging these three pillars, organizations can create a comprehensive “Digital Twin” in which all tasks involved in architectural, functional and physical design, as well as manufacturing engineering and after-sales service, are connected by a coherent “Digital Thread” and can use a single set of data that is accurate and consistent throughout the harness lifecycle. All stakeholders have insight into decisions made across domains, which means issues can be caught and addressed early in the design process, accelerating design while reducing rework and associated costs.
To learn more, download our brochure: Implement Siemens Capital for wire harness engineering solutions
Like what you just read? Check our our recent series of wiring harness blog posts!
- How to improve wiring harness manufacturing efficiency? Let me count the ways
- A tale of two formboards: How to improve merged formboard efficiency
- Building blocks for better wiring harness manufacturing engineering
- Fast and accurate wire harness costing.
- Six factors that impact complexity-related costs, and how to automate for success