How digitalization solves 3 challenges of traditional aerospace harness design
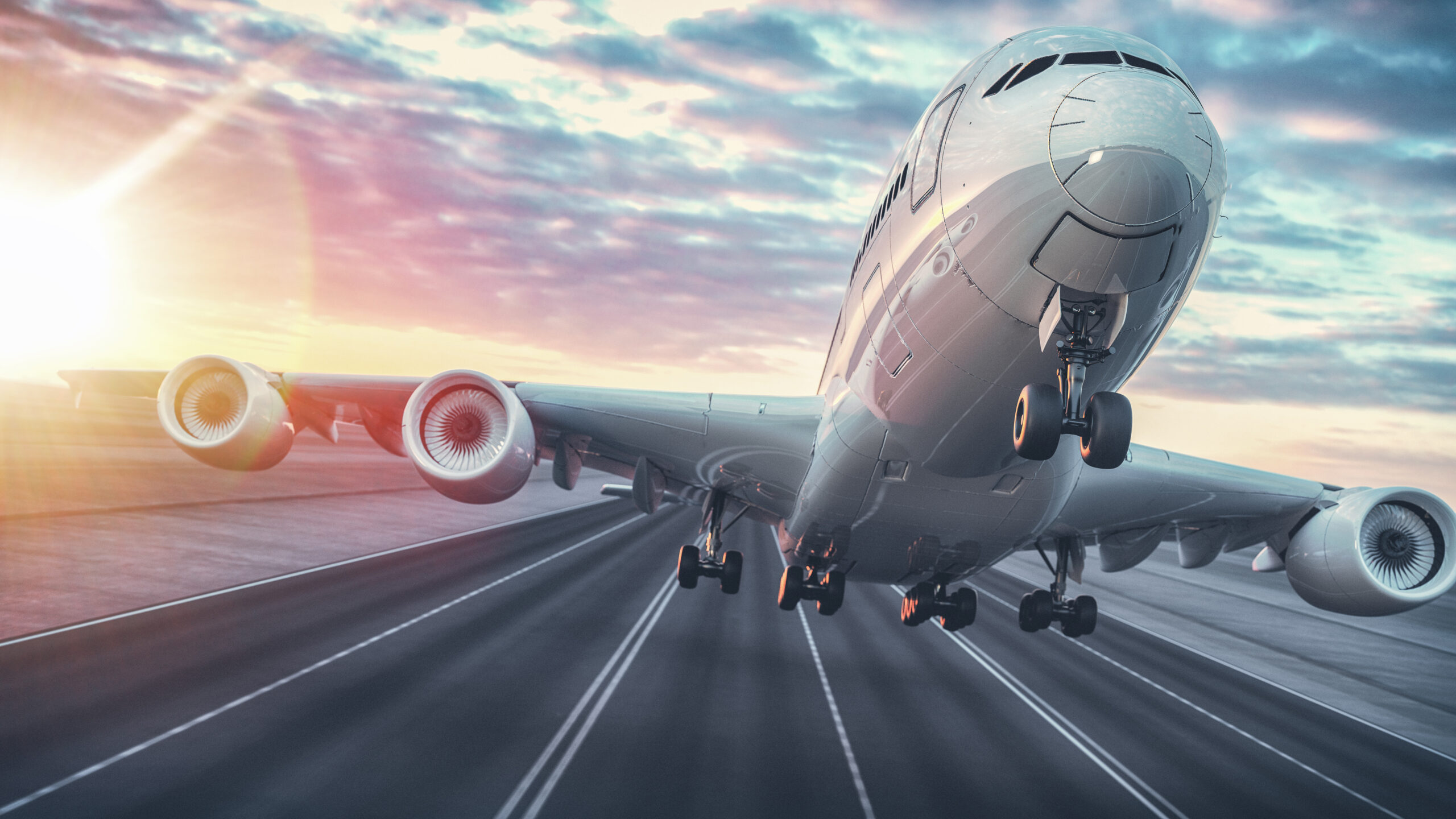
Consider the requirements for aerospace harness design for today’s advanced products. Three variables may come to mind immediately: quality, delivery and cost. These requirements are increasingly difficult to meet, given the recent trends impacting the industry.
Designers hope to improve performance with greener, lighter weight solutions. They are increasingly turning to electrical systems and integrated software solutions to add these capabilities. This in turn can satisfy the mission demands placed on today’s platforms. Meanwhile, tight budgets and timeframes along with more stringent regulations are putting the squeeze on design teams. These teams must work faster and document everything, despite limited resources.
Through digitalization, the application of digital technology to transform business processes, teams are able to visualize and validate designs before committing them to implementation. This enables them to spot and fix potential problems early. Those problems that if caught later in the process could result in delays and waste. The trend toward digitalization is building momentum. Needless to say, it’s becoming obvious that the traditional process for harness design is no longer sufficient.
Let’s examine how a “digital twin” of an aircraft wire harness enables multiple design disciplines to collaborate effectively. With this approach, there is access to critical information throughout the development lifecycle. Taking this approach, teams can deliver extremely high-quality wire harnesses for next-generation aerospace products faster, without driving up costs.
Quality isn’t an option, it’s a requirement
For today’s aerospace and defense products, quality is defined by a standard and is an absolute requirement. However, traditional harness design is characterized by error-prone manual processes. Harness bench testing can only confirm consistency between the design and the harness; it can’t be used to verify the design. Engineering errors such as incorrect component selection, sizing and wiring lengths or missing connectivity sneak through undetected. Accordingly, these must then be corrected on the assembly line.
Using a digital twin of the harness design, teams can validate the harness electronically against design rules. Therefore, they don’t need to manually transfer and transcribe information to collaborate between disciplines. Seamless data sharing ensures consistency and minimizes mistakes, allowing teams to optimize designs and ensure quality standards are achieved, before they progress too far along the development lifecycle.
On-time delivery drives revenue
Today’s fast-paced business world calls for rapid time to market – and teams that don’t deliver cost their organizations a lot of money. However, it’s a delicate balance – in their rush to go to market before competitors, they make lots of mistakes. Fixing them causes delays and puts delivery at risk, potentially resulting in financial penalties and a damaged brand reputation.
By validating designs electronically early on, teams can eliminate last-minute rework that can impact time-to-delivery as designers spend time correcting errors and calling in multiple stakeholders to check and recheck changes.
Controlling costs boosts margins
Labor, materials, services – they all drive up costs and eat into margins. Often, inefficient processes are to blame. Time-consuming design inspections and rework are expensive and invariably impact profitability.
Since designs can be validated early to minimize the number of mistakes that must be fixed late in the design and manufacturing process, costs decrease. Teams no longer have to pay for the time-consuming work of manually entering and sharing data, and less material is wasted during manufacturing because designs are correct-by-construction the first time.
How do you create a digital twin to implement digitalization?
Creating a Digital Twin requires you to combine the aircraft harness topology and wiring connections into a comprehensive digital model – and Siemens Capital makes it easy. The solution’s powerful design automation capabilities combined with its model-based wiring harness engineering workflow helps harness manufacturers cut costs, improve product quality, and boost efficiency.
Want to learn more? Download the white paper “Optimizing aircraft wire harness design” and watch our webinar. Read and hear how digitalization is transforming the traditional approach to wire harness design, and how Capital can help you create and leverage a digital twin for seamless data exchange throughout the product development lifecycle.→ Wire harness design: An underappreciated secret ingredient of your aerospace success