Navigating the complex world of resistance extraction for curvilinear shapes in IC designs
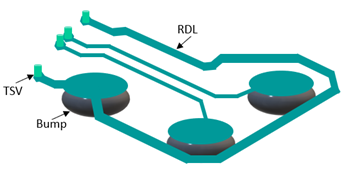
By Nada Tarek
As integrated circuit (IC) designs continue to push the boundaries of what’s possible, we’re seeing an explosion in complexity. From MEMS to 3D ICs, these advanced designs often incorporate curvilinear shapes—those that don’t conform to the typical straight-line, Manhattan-style geometries we’re used to. But while these shapes bring incredible functionality and performance enhancements, they also introduce new challenges in an area that’s crucial for IC reliability: resistance extraction.
The rise of curvilinear shapes in IC design
With the rise of IoT applications, image sensors, photonics, and MEMS, IC designs are becoming more intricate than ever. Designers are increasingly using non-Manhattan routing for interconnects, especially in 3D ICs, to achieve higher integration density and better performance. Curvilinear shapes are particularly valuable here, offering flexibility and improved functionality in tight spaces.
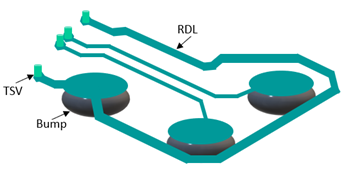
Take image sensors, for example. These devices, found in everything from smartphones to high-end cameras, rely on wide, curvilinear polygons to capture more light, thereby producing high-resolution, low-noise images. Similarly, MEMS devices often use unconventional geometries to meet the specific needs of mechanical, optical, and even biomedical applications.
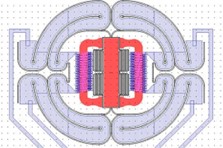
But with these innovative designs come significant challenges, particularly when it comes to accurately extracting resistance—a critical step in ensuring circuit reliability.
Why resistance extraction matters
Resistance extraction isn’t just a box to tick off during the design process—it’s a fundamental step that influences everything from timing analysis to power distribution. Accurately modeling resistance values allows designers to predict circuit behavior, ensuring that the final product performs as expected under real-world conditions.
However, as IC designs become more complex, the traditional methods for resistance extraction start to fall short. This is especially true for curvilinear shapes, where the direction and distribution of current can be anything but straightforward.
To learn more about circuit verification, including extraction, visit the Calibre Circuit Verification website.
Fracturing techniques: The key to accurate resistance extraction
To tackle the challenges posed by curvilinear shapes, advanced fracturing techniques have become essential. These methods involve breaking down complex geometries into smaller, more manageable fragments, allowing for a more detailed analysis and accurate resistance estimation. The main fracturing techniques include 1D fracturing, 2D fracturing, and more advanced methods designed to handle curvilinear shapes.
1D fracturing: The basics
1D fracturing is the most common technique, where the geometry is divided into fractures along the current direction. This approach works well for standard shapes where the current flow is uniform. But when dealing with non-standard geometries, such as those with irregular cross-sections or non-uniform current flow, 1D fracturing can introduce inaccuracies.
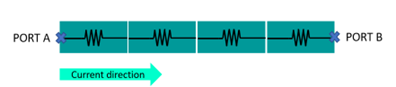
2D fracturing: Stepping up the game
For more complex shapes, like the wide metals used in CMOS image sensors or slotted conductors, 2D fracturing offers a better solution. By creating a mesh of 2D resistors, this technique provides more accurate point-to-point resistance calculations, capturing the vertical and horizontal resistance components that 1D fracturing might miss.
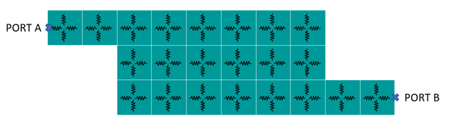
Advanced fracturing: The future of resistance extraction
When it comes to curvilinear shapes, advanced fracturing techniques take center stage. These methods align fractures with the boundaries of polygon shapes, enabling more precise resistance extraction. This approach is especially important for designs like MEMS and photonics, where the shapes are anything but standard. One of the methods that advanced fracturing lies on is fracturing in the direction of polygon, which involves breaking structure into smaller elements aligning with boundaries of polygon shape allowing more accurate resistance extraction.
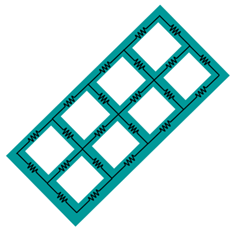
Best practices for accurate resistance extraction
As resistance extraction techniques evolve, so too must the tools we use. Next-generation extraction tools integrate various fracturing methods to handle both conventional and unconventional structures. By doing so, designers can achieve accurate resistance calculations across the entire design, ensuring reliability and performance.
However, there’s always a trade-off between accuracy and simulation runtime. More fracturing means better accuracy, but it can also lead to longer simulation times. The key is to apply advanced fracturing only where it’s needed, such as in curvilinear shapes, while using simpler methods for more standard geometries.
Ready to dive deeper?
Accurate resistance extraction is crucial for ensuring the reliability and performance of your IC designs. To explore the latest innovations in this area, check out our technical paper, “Ready for curvilinear: new innovations for resistance extraction.” Download it here.