Test engineering optimization for NPI profitability
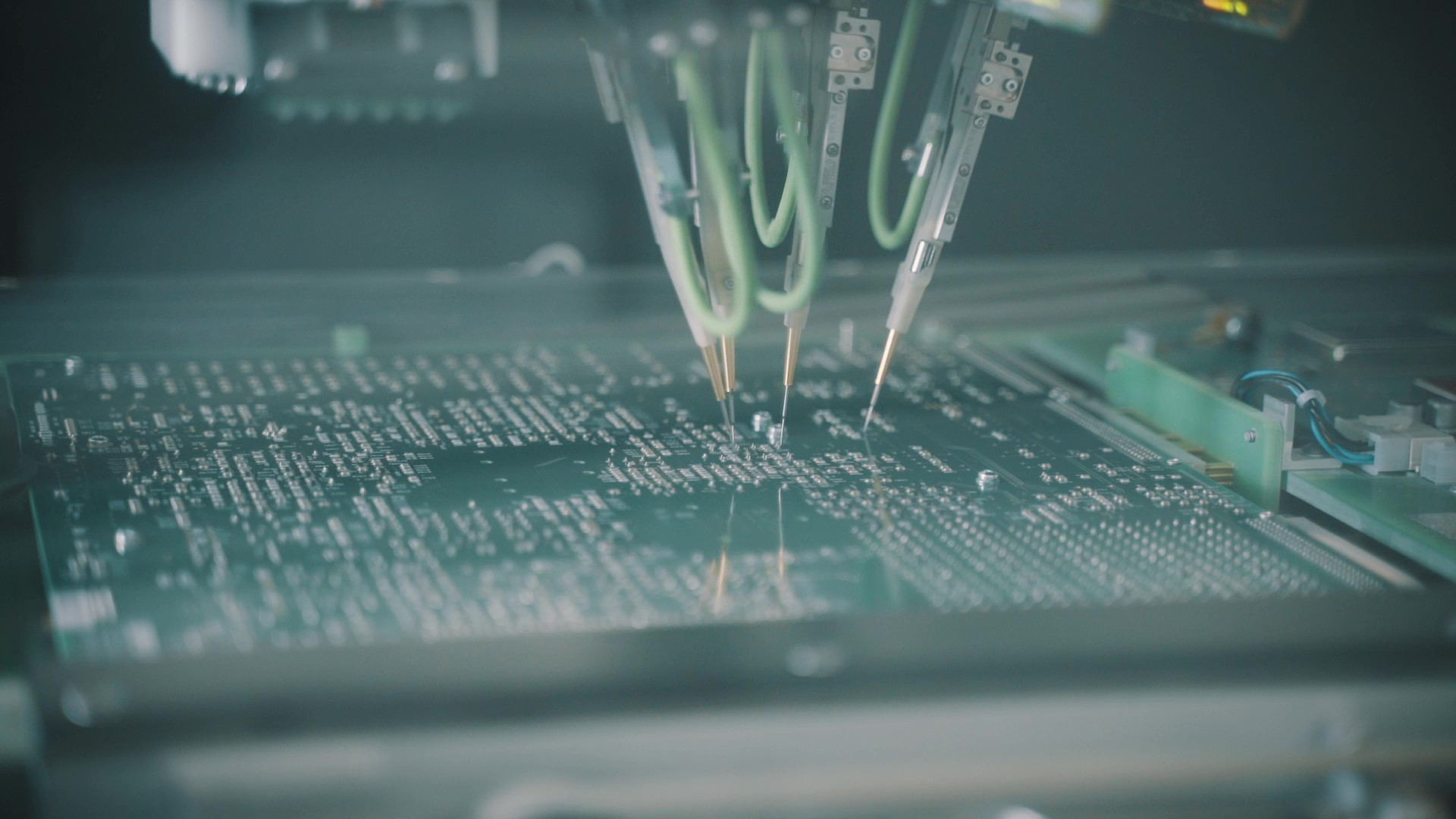
The journey from design data to PCB testing program must be quicker than ever before. New article by Mark Laing
For PCB and assembly manufacturers faced with the trend toward high-mix, low-volume production, Test Engineering has become a critical factor in maintaining the profitability as NPIs (New Product Introductions) are increasingly frequent. In order to optimize the test engineering process – while making sure that a PCB assembly is fully tested and free of defects – it has become crucial to accelerate the journey from design data to an automated, fully-debugged PCB testing program.
In recent years, test engineering has evolved from the “bed-of-nails” in-circuit technology (ICT) approach used for PCBs, to the adoption of flying probe machines, which are better suited for high-mix, low-volume production and prototype runs. While ICTs remain in use and are an efficient means of IC programming, in-line testing, and high-volume testing, the migration to flying probes continues to accelerate due to the cost of ICT fixtures and the reduction in production volumes.
The test engineering domain can be divided into two distinct disciplines:
- Product Verification – in which the product undergoes functional testing in order to ensure that it works according to its design specifications. Product verification differs widely from product to product, and is heavily customized for each project.
- Process Verification – in which the product is tested in order to ensure that it was manufactured properly. Successful process verification techniques can be reused in a wide range of manufacturing projects, and therefore, are a manufacturer’s prime target for optimization.
In an article recently published in IConnect007, Mark Laing, Siemens’ Business Development Manager and test engineering expert, presents crucial guidelines for economizing and optimizing the process verification task, such as:
- Maintaining a single data source for all machines and applications, enabling the creation of a process digital twin that serves as a “single point of truth” upon which all activities are based.
- Efficient generation of test plans, including automated placement of probes, and when required – easy, graphics-based position adjustments.
- Fully debugged test programs, whose debug information can be used to diagnose and repair boards that fail during production.