IT/OT convergence success at Siemens’ Erlangen factory
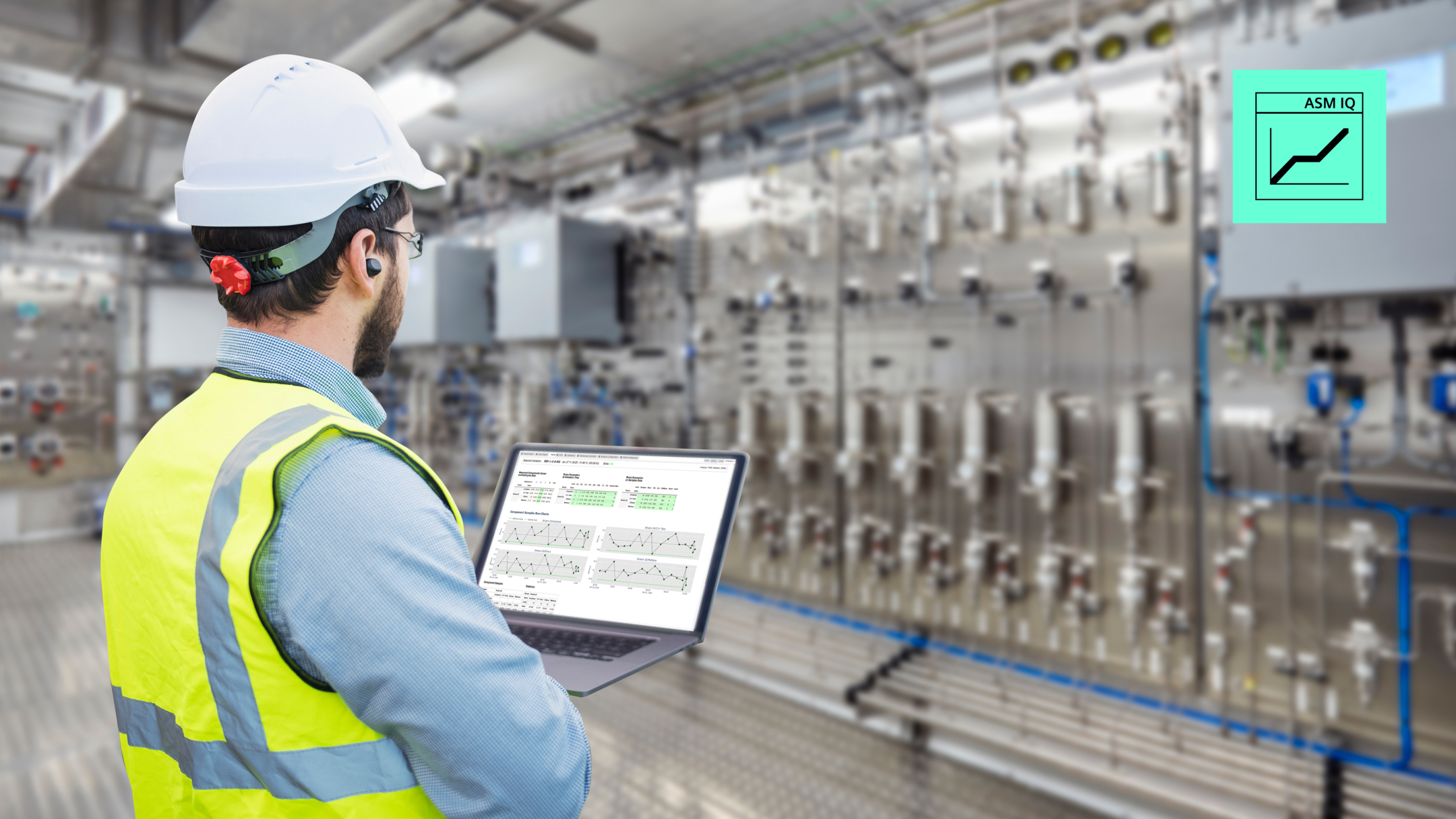
As expectations in the manufacturing industry rise, OEMs strive to cut costs, enhance production lines, and make operations more sustainable. To achieve their optimization goals, manufacturers have begun to undergo an IT/OT convergence transformation. By connecting the once separate worlds of IT and OT, factories can identify areas of improvement on the shop floor using data and deploy operational solutions to address prevalent issues in the industry.
Successfully implementing operational solutions by combining the functionalities of IT and OT is a demanding though obtainable task. Siemens recently brought IT/OT convergence to its own electronics factory in Erlangen, Germany. By digitally transforming its PCB assembly production they have been rewarded with considerable and continued benefits that are helping overcome modern manufacturing hurdles.
The challenge
Erlangen wanted to connect their plants’ systems, identify challenges on the shop floor, and deploy operational solutions to address them. To achieve this goal, the factory digitized its production processes, giving them access to digitalized data analysis.
Connecting the data together into a seamless system proved to be a great challenge. Like many factories, Erlangen has many legacy plants with a diverse pool of machinery. Every plant utilized separate interfaces all while generating different types of data in disparate file formats. Without homogenous data from the shop floors, the factory wouldn’t be able to generate insights into their production lines and systems and thus optimize its productivity.
To combat siloed data, Erlangen adopted Siemens’ Industrial Edge solution, an edge computing platform that acts as central management system for IT and OT capabilities. Using Mendix on the Industrial Edge, Erlangen was able to analyze each plant’s log files, determine their operational status, and transmit the data to its database for easy visualization on a dashboard. With the data consolidated, Erlangen could finally evaluate the state of its operations and identify ways to improve productivity across plants.
IT and OT in harmony
After overcoming the obstacles of IT/OT integration, the rewards began to materialize. Now that Erlangen had unlocked previously inaccessible shop floor data, it could rely on both employee’s experience and automated AI insights to optimize production and speed up innovation. Identifying the factory’s critical issues enabled Erlangen to acknowledge the most significant bottlenecks in their process and potentially eliminate them completely. Already, the factory has seen a 4% improvement in productivity and employee workload reductions of 60%. Additionally, Erlangen can now detect up to 60% of pseudo faults through AI.
And these aren’t the only gains the factory saw from IT/OT convergence. Now that it is capturing data, the factory can also track fluid and consumption rates as well as energy consumption. The increased transparency of their production’s environmental footprint enabled them to derive machining processes optimized for sustainability. Looking to continuously adapt, Erlangen uses its data to find new methods to enhance sustainable operations.
The manufacturing industry is moving into a renaissance of digital transformation. IT/OT convergence helps companies curtail rising costs, enhance their industrial systems, and actualize their sustainability goals. Through both manual and automated data analysis, manufacturers can make informed decisions about their plants and processes to:
- Improve productivity
- Lighten employee workloads
- Preemptively detect machine malfunctions
- Analyze downtimes and failures
- Test solutions cheaply and quickly
The Erlangen factory reaps these benefits and has no plans of slowing their IT/OT integration growth. Currently, the factory is working towards realizing a closed-loop system that can dynamically control its production processes based on up-to-date process and quality data. This way, the factory would be able to optimize its systems without expensive or time-consuming testing.
Approaching the future
The future is bright for the Erlangen factory. Leaders within the organization see its digital transformation as an intermediary step towards the industrial metaverse–a digitally expanded space that fosters greater efficiency, productivity, sustainability, and connectivity. The enhanced data collection capabilities enabled through IT/OT solutions can facilitate the creation of increasingly advanced simulation models for factories. Since platforms like Industrial Edge also enable employees to access the data quickly and easily, IT/OT convergence is a crucial step towards creating smarter factories, making operations more sustainable, and ultimately revolutionizing the manufacturing landscape.
To learn more about how Siemens Electronics Factory Erlangen, Germany combined state-of-the art production methods with the latest technologies such as digital twins, AI, and IT/OT convergence here.
Siemens Digital Industries Software helps organizations of all sizes digitally transform using software, hardware and services from the Siemens Xcelerator business platform. Siemens’ software and the comprehensive digital twin enable companies to optimize their design, engineering and manufacturing processes to turn today’s ideas into the sustainable products of the future. From chips to entire systems, from product to process, across all industries. Siemens Digital Industries Software – Accelerating transformation.