Inside machine building for the battery industry – Ep. 2 transcript
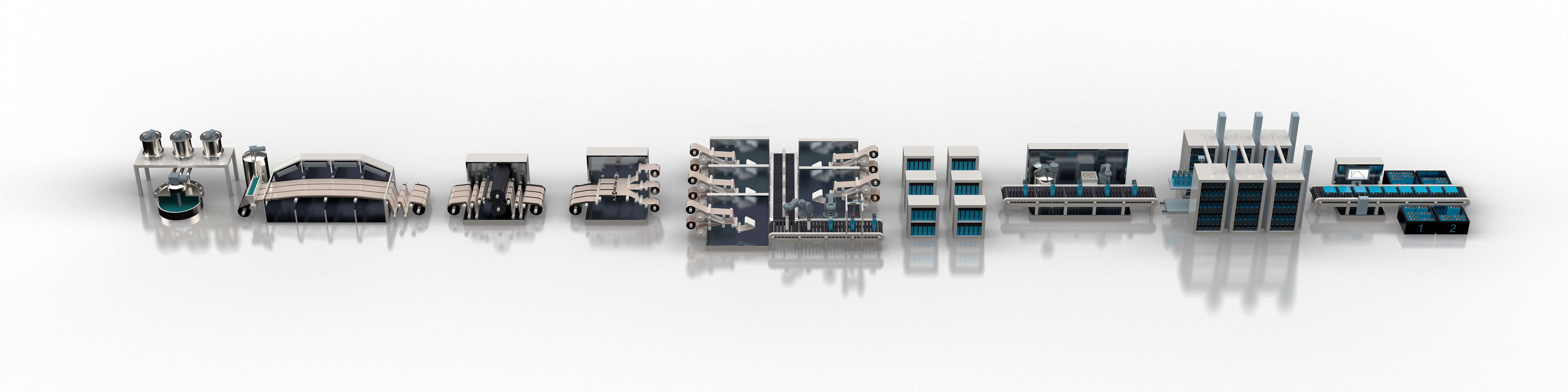
This is part 2 of Inside Machine Building for the Battery Industry. Listen to the podcast here or follow along by reading the transcript.
Chris Pennington: It’s great to get those different viewpoints. It looks like smart manufacturing will be essential to grow battery manufacturing while achieving the necessary quality requirements. Can you elaborate on some of the unique challenges battery manufacturers face in comparison to traditional or discrete manufacturers?
Rahul Garg: Puneet said earlier that the battery manufacturing process has been more like an art, like trying to bake a cake. Now, they’re trying to move away from that art process and make it into a more standard process given the high demands that exist because you cannot rely upon artisans to get the production process completed. That’s probably the biggest change and hurdle that that companies need to get through.
And Puneet, I’m sure you probably have lots of reasons why they need to be looking at that, given the fact that it’s not a standard discrete process that they can replicate effectively. They’re probably having lots of issues around the quality and other challenges that may be coming up out because of that.
Puneet Sinha: Absolutely right Rahul. So, if I can elaborate on that, battery is fundamentally very different than previous technologies of the IC (internal combustion) engine and the kind of technology that goes in IC engine vehicles. And the reason is because battery requires very strong interaction across various domains, materials, electrical electronics, chemicals, and software. All of these domains interact much more heavily in the battery world compared to IC engine where these domains either did not interact or the interaction was very weak. That was a big reason that in the world of battery, if you change a seemingly minor thing, it can have a significant impact down the line on the manufacturability of that battery or the life or the quality of the battery.
That’s why it is very critical to account for all of these domains and their interaction, both for engineering and manufacturing of batteries. Actually, in my engagement with various battery companies, we are seeing that when the production is starting, the scrap rate can be 40% or higher and that is because some of these minor changes that has happened can lead to impacts which are tough to predict. And even in a factory where the stable scrap rate can be 10 to 15%, which is very high scrap rate.
Rahul Garg: It could wipe out your entire profits, I would imagine.
Puneet Sinha: Right. If you’re looking to have cost effective manufacturing and this simple math. If you do, you will find that if you reduce the scrap rate even by just a few percentage points, you are looking at hundreds of millions of dollars’ worth of savings in manufacturing.
Even a small percentage change in scrap reduction has a huge impact on cost, hence profitability. Hence the survivability of that company for future. And that is one of the big pain points in the battery industry, which is shared not only by the new entrants but also the companies who are doing manufacturing for many, many years.
The other thing that also adds up to that, especially if you are a large enterprise who has been doing battery manufacturing for many, many years. Especially the companies that that are in China, Japan, Korea have to scale up globally. When you go into a new facility, a new plant, various changes can happen. Even subtle changes in how the dry rooms are being run can have a major impact on quality of the battery. All of these things needs to be considered very carefully and they are the ones that started impacting overall profitability.
Chris Pennington: As you said, both existing battery manufacturers and new entrants face significant challenges if they’re going to meet market demands. How can digital transformation and smart manufacturing solutions help address the challenges such as scrap rate and help machine builders and battery manufacturers? Moreover, how can digital transformation help these companies achieve their sustainability goals?
Puneet Sinha: I’m going to divide that in two parts. First, you ask why scrap rates are so high and how it can be addressed. And second was about sustainability.
For scrap rate, as I mentioned earlier, battery requires a very strong interaction between materials, electrical, electronic process, and mechanical processes. Even a minor change in chemical formulation, even microscopic defects in the materials, variability in the manufacturing process, or slight environmental changes are some of the key reasons why scrap rates can be very high.
Rahul Garg: I would imagine even the quality of the lithium that’s being used can have an impact on the manufacturing process.
Puneet Sinha: Yes. The scrap rate is very high for battery for many reasons. One of the key reasons is the quality of raw material that is utilized for battery manufacturing.
Cell manufacturing especially for UM batteries, there can be some microscopic level of defects variability in the material. Be it lithium, graphite, lithium, cobalt, or manganese, there are various steps involved in a cell manufacturing, even a small variation in them can have some significant impact and even slight changes in dry room operating conditions. The challenge with batteries is that all of these are happening at a microscopic level.
To give you an idea, when electrode sheets are coated after coating, they need to be dried. You are talking about microscopically 450 to 100 Micron thick electrodes meter width. And very long roles to and to find out if the whole electrode role is dried up correctly is a tough challenge. Even a small area that is not dried across this whole role, which has a very challenging dimensions from the manufacturing perspective as huge implications for quality.
And these are the things that you do not pick up immediately. If the area of an electrode remains wet and is not dried enough, it will have impact by the end of manufacturing process. That’s where these things are picked up. As you see, there are literally thousands of variables from the material quality, the sourcing of material, microscopic defects, and potential changes in operating conditions to where these defects are happening versus where they are picked up at the very end.
It is very tough for battery manufacturing companies to start picking up these defects when they are happening, and they have to wait till the whole process is done many times and then that increases scrapped because they have to many times scrap the whole role just because some of the areas are not coded correctly or not dried correctly for example.
The second question you asked was about sustainability. It is absolutely right that battery cell manufacturing is a very energy intensive process. To put in perspective, it takes approximately 30 to 40 units of energy consumption to create one unit of battery energy. In order for that kind of energy intensive process to happen, there is a significant impact on the carbon footprint of a given factory, especially when you’re doing battery manufacturing on a large scale.
It is very critical that battery companies have a very strong overview and executional insight into how the operations are happening when the downtimes are coming. Are the machines being utilized in a way that is amenable to minimizing the energy usage? And this is just not on the battery suppliers, but also battery.
Machine builders have a huge role to play to address that sustainability equation. The equation includes how much energy machines are consuming and how effective they are in getting a certain process done while minimizing energy consumption. All of these things start coming together to address challenges that come with sustainability, especially for the energy consumption for the battery manufacturing.
Chris Pennington: It seems we have a good understanding of what battery manufacturers need to change, but in what ways is Siemens positioned to assist battery manufacturers and machine builders in navigating the complexities of battery manufacturing?
Rahul Garg: For battery manufacturers and for the machine builders, there are a few things that we have looked at given all the issues that Puneet was talking about. All the way from a very complex process which is multi-model in terms of the various sub kinds of tasks that needs to be looking at given all but the steps that one needs to go through and given the complexities of variability that exist, one of the things that we think that can help a lot is in standardizing a across the manufacturing process with certain components that standardization process helps eliminate many of the variabilities that you can manage.
There are many variabilities that are perhaps coming in from the outside environment that you cannot control all the time, but at least let’s try and manage the variability that’s within your environment, within your 4 walls, within your control. We strongly believe that standardizing on certain set of technologies can help not only improve your process, but also help accelerate the delivery and the development of your process.
The second big thing that we think is very helpful is, as part of that whole standardization process, it can help provide a glue between the machine builders and the manufacturers. If the machine builders are using different technologies and if the manufacturer is trying to the complete a process using these different technologies, it’s just going to become harder.
Again, using this whole standardized technology background makes it easier for the manufacturer to ensure that the end deliverables are working on are more manageable. That’s why we are really big on this whole standardization process.
The other big thing that we are giving our customers is this whole concept of virtual commissioning and additional twin, which allows manufacturers and the machine builders to build a complete digital twin of your manufacturing equipment and your manufacturing process pretty much.
When this becomes again very valuable. It helps you evaluate how your manufacturing systems, manufacturing process, and your manufacturing equipment will function given all the variabilities that you may have to encounter.
These digital twins can help you really fine tune your process in a much better way before you actually start making anything. It can help you virtually evaluate, simulate, and test all of the conditions in which you will be running your manufacturing process and make sure that your manufacturing is highly optimized. Then you can take it to the next level when you actually start building so that when you start building all the variability that you could expect in that process which actually have been addressed and have been taking care of.
At least those are a couple of things that they’re working on quite extensively and trying to help the customer’s problems.
Puneet, anything to add on that?
Puneet Sinha
Rahul, those are absolutely some of the key dimensions that you have touched upon the dimension standardization and virtual commissioning. One thing that I will just also mention: battery suppliers always deal with multiple machine builders, so a battery supplier is always looking to bring machines different machines from different machine builders. And how those machines will come and work together in a seamless fashion in a given factory becomes a critical element of manufacturing success. The IT OT integration.
And that is a critical element and also a part of synchronization. That’s again from Siemens’ perspective, not only about digital twin technology and solution, but also how they connect seamlessly with our automation solutions becomes a key element and value to make that standardization happen.
Rahul Garg: I agree. The whole IT OT process is critical not only in standardizing but also in ensuring you have the ability to drive a maximum efficiency through our manufacturing process. Typically, what happens, is the OT operations are identifying the issues, but by the time you get them relayed up to your to your IT executives, it’s too late.
But as you have the tight integration, you can be responding a lot faster and quickly.
Puneet, do you have any recent examples where we have been able to show customers the value of what Siemens has to offer and how it has helped them with their manufacturing process for specifically for batteries?
Puneet Sinha: Siemens is fast becoming a preferred technology partner for the overall battery ecosystem. 8 out of top 10 battery suppliers leverage some elements of our extended portfolio. But in this session, I would like to bring a specific success story. It is from ECM, a Taiwanese company. They are one of the leading developers for one of the cathode materials, which is an LFP material. It’s a magnesium iron phosphate material. That company also develops manufacturing equipment, and they are looking to sell that equipment as a turnkey solution to other companies as well.
When they were looking at their own manufacturing line for the cathode material and developing manufacturing equipment, the time, and efforts that that was needed for them to design and modify those machines and tweak them to the production environment of different companies was a huge bottleneck for them. And when we engage with them, this is what they talk to us about. The solution they started leveraging from our side is our plan simulation portfolio.
Leveraging Siemens’ planned simulation, they created this shell tune of their complete production line, and because some of the stations in cell manufacturing work in cyclical process, while some other work in batch process, it is critical that each working station is deployed properly.
Ideal time can be significant, and it impacts the production efficiency. Leveraging our solution, ECM was able to accurately simulate output of their whole line energy consumption and they were able to reduce equipment idle time, improving the production efficiency by 15% and reducing the energy consumption by 5%.
One other thing that they are interested in is how they can bring more automation and have a fully automated factory for their own cathode production line. This is an area where starting with what they have already achieved with our planned simulation.
Now they are using that and connecting with the images and SCADA so that they start moving toward a fully automated production line, because now they can have of course, the dial tone of the line. Now they can simulate or be more predictive in their simulation, analyze abnormalities, and find the solutions in advance. That’s helping them save labor for quality controls and make necessary adjustments.
Chris Pennington: Now, thanks for sharing, Puneet. It really does show what can be achieved with digitalization. Before we close out for today, are there any final thoughts either of you would like to leave our listeners with?
Rahul Garg: Yeah. One interesting thing was some of the issues that Puneet identified to me were certainly very daunting and in an industry that is growing so rapidly that it has to scale up 14 times in the next few years. There is not much room for error, and you need to make sure that you can start working as you expand with the right company with the right partner.
Someone who’s been there and has the experience necessary to help you in that process. I do think what Siemens can bring to bear for some of these companies that are that are going in this direction of battery manufacturing can be very helpful to them. The years of experience we have, the years of technology that we have built, they can truly help them in their journey, and we can become a good partner in their pursuits.
Puneet Sinha: Fully agree with what you said, Rahul. Just expand to expand on that: what I will also say for battery industry to achieve his ambition, this 14X growth is scaling of their production capacity, ambition. It cannot be achieved just by battery suppliers alone. It requires a close collaboration between battery suppliers and their material providers. And a key element in that is machine builders. How machine builders and the battery suppliers can collaborate closely.
In terms of the kind of machines that are needed bring certain simplification in the process. Improving quality and the reduction of energy consumption and also how these two groups of companies can collaborate to bring more data-driven manufacturing. How that can be made available to operators easily so that real-time changes potentially can be made to improve production? That is a critical question for the whole battery ecosystem to achieve its ambitions and become greener.
Chris Pennington: Some great final thoughts there. Thanks very much Rahul and Puneet. It’s been a pleasure having you as our guest today. Thanks to both of you for joining me to discuss the significance of smart manufacturing in the battery industry.
I’d also like to thank our listeners for tuning in and I hope you’re able to join us in future events. Thank you and goodbye.
Siemens Digital Industries Software helps organizations of all sizes digitally transform using software, hardware and services from the Siemens Xcelerator business platform. Siemens’ software and the comprehensive digital twin enable companies to optimize their design, engineering and manufacturing processes to turn today’s ideas into the sustainable products of the future. From chips to entire systems, from product to process, across all industries. Siemens Digital Industries Software – Accelerating transformation.
Comments
Leave a Reply
You must be logged in to post a comment.
This thought brings an interesting and nuanced view to the conversation. Solar