Why simulation is the future of manufacturing
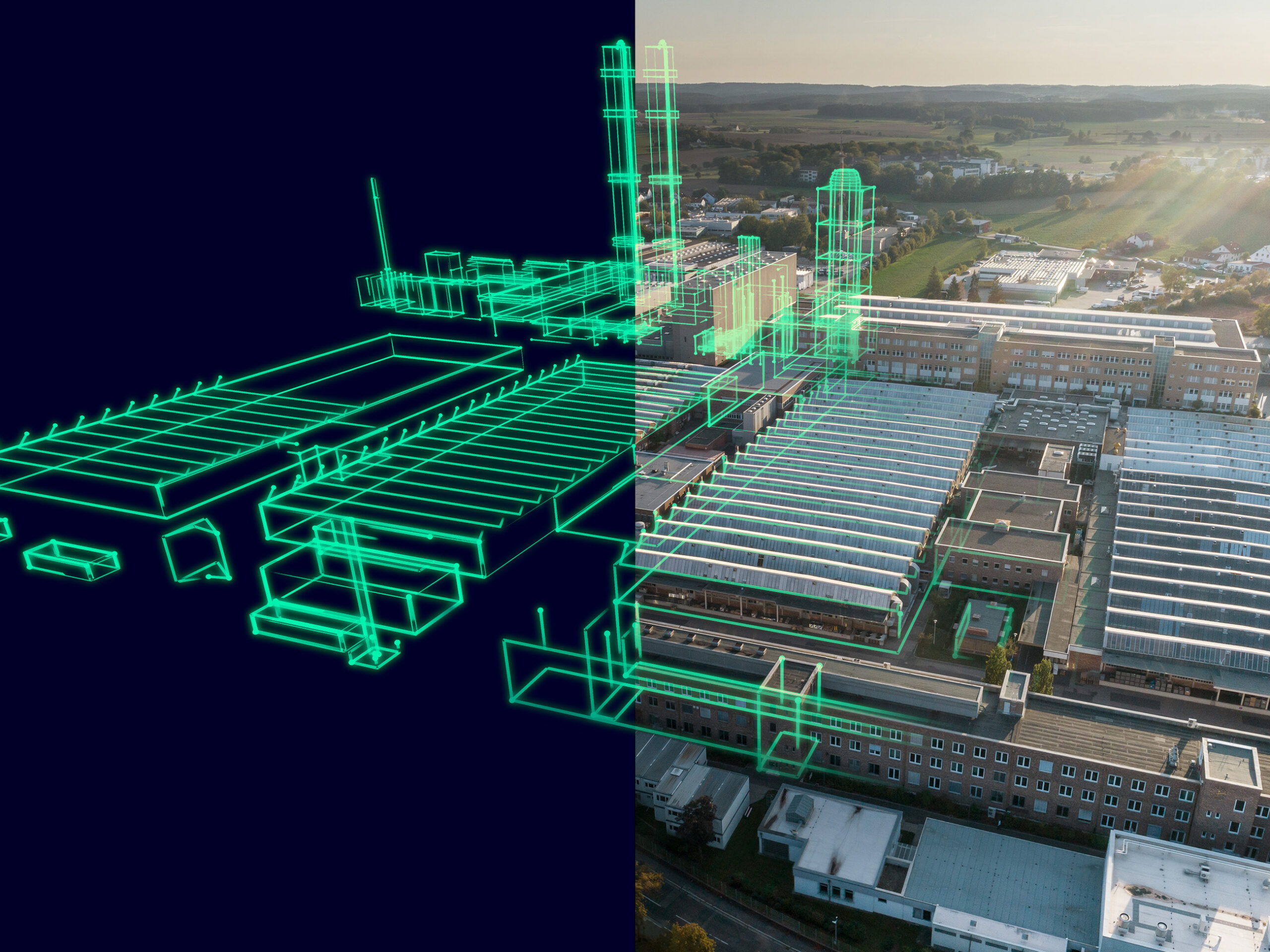
Updating old processes is a formidable task for OEMs. With the high baseline costs of operating manufacturing facilities, attempting to modernize plants may seem like an unnecessary expense in the short run. Modernization is potentially time-consuming and increases both monetary and environmental costs. However, refusing to update industrial systems can leave manufacturers in a predicament. Due to labor shortages, potential supply chain disruptions and increasingly strict environmental regulations, modernization may be mandatory to keep up with surging operational expenses. While upgrading outdated systems can initially seem intimidating, investing in simulation technology made for industrial systems is the key to tackling today’s manufacturing challenges head on.
Simulation for industrial systems
But what is simulation for industrial systems? Simply put, it is leveraging simulation technology to improve every aspect of the production process, from product prototyping to production lines. Using data gathered within their own facilities, manufacturers can create a comprehensive digital twin of their entire plant to identify what systems could be improved. An accurate and comprehensive digital twin will help manufacturers gain a better understanding of both product and production behavior, leading to more optimized production lines, more efficient production systems and increased sustainability.
Recreating a plant virtually allows manufacturers and machine builders to optimize their machines and their systems before committing to expensive redesigns in the real world. Using simulation technology, they can perform design reviews with their customers and flesh out the full capabilities of the physical systems.
Additionally, simulation technology would help manufacturers and machine builders side-step expensive and time-consuming reworks of their facilities. Leveraging the digital twin eliminates much of the extra time and costs accrued by shipping physical prototype machines as well as potentially expensive modifications if machines don’t meet customer expectations.
Improving sustainability with simulation software
Along with productivity, simulation software boosts sustainability. With the rising cost of energy and the continuing climate crisis, reducing energy consumption becomes critical. Being able to simulate an entire production line’s energy consumption before the production process has even started can help machine builders and manufacturers identify potential areas of environmental improvement. This has a significant positive impact on both the planet and plant operations
With the digital twin, manufacturers, machine builders and their customers can easily optimize the functionality and components of their machines while reducing prototype waste, since unused prototypes will inevitably become scrap. Moreover, shipping them increases carbon dioxide emissions due to reliance on fossil fuels for most modes of transportation.
Getting started with simulation
Despite the benefits, preparing plants for simulation technology can be difficult. Machines produce several types of data that are necessary to capture to create an accurate and data-rich digital twin. Plant data is often siloed and unorganized, and older machines with limited data collection abilities may have an even harder time consolidating data for simulation technology. The first step of the process begins once manufacturers and machine builders acknowledge that implementing simulations for industrial systems is an ongoing task.
OEMs need to start small and expand as their processes grow. For some, the best way to start their simulation journey is on the mechanical side. Examining aspects like kinematics, collision detection, or even machine function will help build an understanding of how to optimize the entire system. However, this is only one piece of the puzzle.
Not all production facilities are built the same. Some plants would gain more from considering automation as a practical starting point. Either way, whether a company is building their digital twin to address throughput or behavior models, the only way to make the most of simulation technology is by bringing both methods together.
Simulation software has the ability to unlock a manufacturing plant’s true potential. Continued and active optimization through digital transformation and the digital twin can help reduce surging operational costs while improving energy efficiency. To learn more about simulation software in factories listen to our most recent podcast “Exploring simulation for industrial systems” here.
Siemens Digital Industries Software helps organizations of all sizes digitally transform using software, hardware and services from the Siemens Xcelerator business platform. Siemens’ software and the comprehensive digital twin enable companies to optimize their design, engineering and manufacturing processes to turn today’s ideas into the sustainable products of the future. From chips to entire systems, from product to process, across all industries. Siemens Digital Industries Software – Accelerating transformation.